Overview of CuAl10 Powder
If you’ve found yourself diving into the world of metallurgy, you’ve probably come across CuAl10 powder. But what exactly is it? Why is it such a sought-after material in various industries, from aerospace to automotive? Well, CuAl10 powder, or Copper-Aluminum Alloy (Cu-Al Alloy), is a bronze alloy consisting of 90% copper and 10% aluminum, often used in the form of powder. It’s prized for its unique properties, including excellent corrosion resistance, strength, and versatility, making it an ideal candidate for numerous applications.
Let’s take a deeper look into what makes CuAl10 powder so special and explore its characteristics, uses, types, and the various models you can find on the market.
Composition of CuAl10 Powder
Understanding the composition of CuAl10 powder is key to grasping its overall performance. This alloy consists primarily of copper (Cu) and aluminum (Al), but other trace elements can also play a role in fine-tuning its properties.
Element | Percentage Composition |
---|---|
Copper (Cu) | 90% |
Aluminum (Al) | 10% |
Iron (Fe) | 0.5% (max) |
Manganese (Mn) | 0.5% (max) |
Silicon (Si) | Trace amounts |
Lead (Pb) | Trace amounts |
The high copper content ensures excellent electrical and thermal conductivity, while aluminum imparts strength and corrosion resistance. Trace elements such as iron and manganese can help to increase the alloy’s overall hardness.
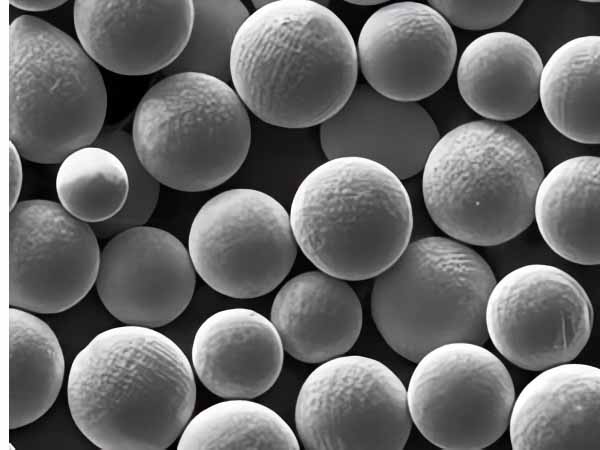
Characteristics of CuAl10 Powder
Now, you may be wondering: What makes CuAl10 powder such a go-to material? Below are the standout characteristics that make this alloy a favorite in various industrial applications.
Key Characteristics:
- High Strength-to-Weight Ratio: CuAl10 offers exceptional mechanical strength compared to its relatively lightweight structure. This makes it ideal for applications where weight matters, like in aerospace components.
- Excellent Corrosion Resistance: Thanks to the presence of aluminum, CuAl10 powder resists corrosion, particularly in marine environments. Whether you’re dealing with seawater, chlorides, or other corrosive agents, this alloy holds its own.
- High Wear Resistance: CuAl10 is known for its durability. It handles wear and tear better than many other copper-based alloys.
- Good Thermal and Electrical Conductivity: Copper is a great conductor of heat and electricity, and this property remains in CuAl10, making it useful in electrical applications.
- Ease of Casting: CuAl10 is easy to cast, which makes it a favorite for 3D printing and other metal powder bed fusion techniques.
These attributes are crucial in making the CuAl10 powder an all-purpose alloy that delivers high performance in demanding conditions.
Types of CuAl10 Powder Models
There are various forms and models of CuAl10 powder, each tailored for different applications and needs. Depending on the manufacturing process or required application, slight variations in composition and particle size can impact performance. Let’s dive into 10 popular models:
1. CuAl10F Powder
A finely milled version with high flowability, perfect for additive manufacturing and metal injection molding (MIM). Its smooth, spherical particles ensure even distribution during the printing process.
2. CuAl10P Powder
This powder is specialized for powder metallurgy (PM). With its tailored particle size distribution, it’s great for sintering applications that demand tight tolerances and high precision.
3. CuAl10-GH
This is a gas-atomized CuAl10 powder that’s ideal for laser-based manufacturing techniques such as Selective Laser Melting (SLM) or Direct Metal Laser Sintering (DMLS). It boasts superior purity and flowability.
4. CuAl10-R Powder
Designed specifically for thermal spraying applications, CuAl10-R offers enhanced wear resistance when used as a coating material. This model performs well under high-stress environments and high temperatures.
5. CuAl10-S Powder
Used primarily in marine industries for applications like propeller production, this powder features excellent anti-corrosive properties. Its particle shape is usually more irregular to ensure better bonding in molten stages.
6. CuAl10-AR
This abrasion-resistant variant is perfect for components that undergo continuous wear, such as valves, bearings, and gears in high-friction environments. The CuAl10-AR model is specifically designed to provide a balance between strength and resistance to abrasive conditions.
7. CuAl10-SF Powder
This powder is engineered for soldering and brazing applications. The CuAl10-SF model has a lower melting point compared to other variants, allowing for easier bonding in precision electronics or plumbing systems.
8. CuAl10-H Powder
The high-strength CuAl10-H is ideal for structural components in industries like automotive and aerospace. With its increased hardness and tensile strength, this model is used in applications where parts are subjected to heavy loads and stress.
9. CuAl10-MN Powder
Designed to handle extreme marine conditions, CuAl10-MN offers enhanced corrosion resistance even in saltwater environments. This makes it a go-to material for shipbuilding, offshore structures, and underwater equipment.
10. CuAl10-EX Powder
This is an experimental variant with additional trace elements like silicon and manganese, which provide improved casting fluidity and malleability. CuAl10-EX is currently being explored for advanced 3D printing techniques where intricate designs and high performance are needed.
Applications of CuAl10 Powder
CuAl10 powder’s versatility means it finds use across a wide range of industries. Below are some common applications where this alloy powder shines.
Application | Industry | Description |
---|---|---|
Aerospace components | Aerospace | Lightweight, high-strength materials for structural parts and brackets. |
Propellers and marine parts | Marine | Ideal for ship propellers, underwater fittings, and offshore platforms. |
Gears and bushings | Automotive | Excellent wear resistance and strength, used in transmission systems. |
Electrical contacts | Electrical | Good conductivity and corrosion resistance for contacts, switches, and relays. |
Bearings and valves | Industrial Machinery | High wear and corrosion resistance in mechanical parts under stress. |
Thermal spraying coatings | Engineering | Applied in thermal spraying to protect surfaces from wear and corrosion. |
3D Printing & Additive Manufacturing | Manufacturing | Used for creating complex, custom parts with high precision. |
Artistic and architectural | Art and Architecture | Used in sculptures, medals, and decorative pieces for its bronze-like appearance. |
Each application capitalizes on specific properties of CuAl10, whether it’s corrosion resistance for marine parts or conductivity for electrical systems.
Advantages of CuAl10 Powder
Why should you choose CuAl10 powder over other metal powders? Let’s break it down.
Strength:
CuAl10 provides high tensile strength, making it a great choice for heavy-duty applications where parts need to withstand significant forces.
Corrosion Resistance:
With its aluminum content, CuAl10 offers excellent protection against oxidation and corrosion, even in environments where exposure to chemicals, moisture, or saltwater is constant.
Cost-Effectiveness:
Compared to other bronze alloys, CuAl10 offers better performance at a lower cost, making it a smart option for industries seeking to optimize their material expenses.
Versatility:
From additive manufacturing to casting, CuAl10 can be used in a wide variety of production methods. Whether you need powder for laser sintering, injection molding, or soldering, this alloy delivers.
Specifications and Grades of CuAl10 Powder
Depending on the manufacturer and application, CuAl10 powder can come in different grades and sizes. Here’s a typical overview of the specifications:
Specification | Value |
---|---|
Particle Size | 15-45 µm, 45-105 µm, 105-180 µm |
Purity | 99.5% (minimum) |
Apparent Density | 2.5 – 3.2 g/cm³ |
Flowability | 22 – 35 sec/50g (depending on model) |
Melting Point | 1035 – 1050°C |
Hardness | 90 – 150 HB |
Ultimate Tensile Strength | 450 – 600 MPa |
Grades are typically defined by the particle size distribution and intended application. For example, finer powders (15-45 µm) are often preferred for laser sintering or 3D printing, while coarser powders (105-180 µm) might be used in casting applications.
-
CM247LC Powder | Nickel Alloy Powder
-
0# Pure Nickel powder
-
NiCoCrAlY alloys powders
-
Rene 142 alloy-Rene Powder
-
Haynes 25 Haynes Powder
-
Best Hastelloy C-22 Powder-High temperature alloy Powder for 3D Printing
-
Best Hastelloy C-276 Powder-High temperature alloy Powder for 3D Printing
-
Best Hastelloy N Powder-High temperature alloy Powder for 3D Printing
-
Best Hastelloy B Powder丨High temperature alloy Powder for 3D Printing
Suppliers and Pricing for CuAl10 Powder
Prices for CuAl10 powder can vary depending on factors such as particle size, purity, and volume purchased. Below is an overview of typical suppliers and price ranges.
Supplier | Price Range (per kg) | Available Grades |
---|---|---|
Höganäs | $30 – $50 | Fine to medium grades for 3D printing and MIM |
Sandvik Osprey | $25 – $40 | Coarse grades for casting and thermal spraying |
AMETEK Specialty Metals | $35 – $55 | High-purity grades for electrical applications |
GKN Additive | $28 – $48 | Fine powders for additive manufacturing |
Praxair | $30 – $45 | Medium grades for thermal spray applications |
When buying CuAl10 powder, be sure to consider not just the price, but the specific requirements of your project. A finer powder may be more expensive, but it will provide better surface quality in additive manufacturing processes.
CuAl10 Powder: Pros and Cons
To make the decision easier, let’s compare the pros and cons of using CuAl10 powder.
Pros | Cons |
---|---|
Excellent corrosion resistance | Lower conductivity compared to pure copper |
High strength-to-weight ratio | Can be more expensive than other metal powders |
Versatile for different manufacturing methods | Slightly lower ductility than some other alloys |
Durable and wear-resistant | Limited availability in certain regions |
Cost-effective for high-performance uses | May require specialized equipment for processing |
Overall, the advantages of CuAl10 far outweigh its limitations, particularly for industries that need a strong, corrosion-resistant material.
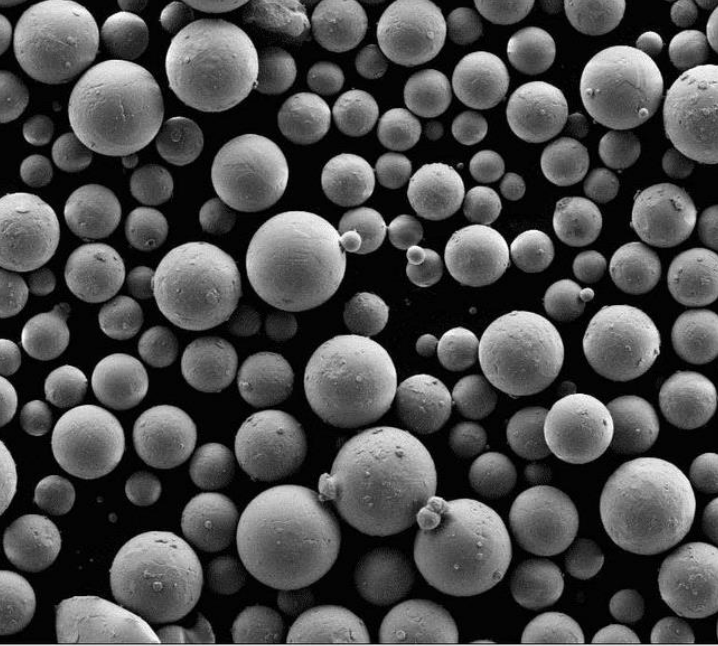
FAQ
To wrap things up, let’s tackle some frequently asked questions about CuAl10 powder.
Question | Answer |
---|---|
What industries use CuAl10 powder? | CuAl10 is used in aerospace, automotive, marine, electrical, and industrial machinery sectors. |
Can CuAl10 powder be 3D printed? | Yes, CuAl10 powder is compatible with 3D printing processes like Selective Laser Melting (SLM). |
What is the main benefit of CuAl10 powder? | Its excellent corrosion resistance combined with high strength makes it ideal for harsh environments. |
Is CuAl10 powder expensive? | It’s cost-effective compared to other high-performance alloys, though prices vary depending on purity and size. |
How is CuAl10 powder made? | It’s typically produced through gas atomization, ensuring consistent particle size and shape. |
Conclusion
In the grand scheme of metal powders, CuAl10 stands out for its balanced performance and cost-efficiency. Its combination of strength, corrosion resistance, and versatility makes it a top contender in industries that require materials capable of handling demanding environments. Whether you’re working in aerospace or marine engineering, CuAl10 powder offers an excellent solution that doesn’t compromise on quality.
When choosing your CuAl10 powder, remember to factor in the specific demands of your project—particle size, purity, and application type all play a crucial role in ensuring you get the right product for the job.