If you’re diving into the world of metal powders, particularly CuSnTi powder, you’re in for an exciting and highly technical journey. Whether you’re a material scientist, an engineer working on industrial components, or someone just curious about the properties and applications of metal powders, this guide will have you covered.
In this article, we’ll discuss everything from the composition of CuSnTi powder to its properties, specific models, and applications in various industries. We’ll also provide a detailed comparison of available powder models, their specifications, suppliers, pricing, and more.
So, let’s embark on this technical adventure and dig into the fascinating world of CuSnTi powder!
Overview of CuSnTi Powder
CuSnTi powder is an alloyed powder made of copper (Cu), tin (Sn), and titanium (Ti), each of which adds distinct properties to the mix. Known for its durability, corrosion resistance, and specific mechanical advantages, CuSnTi powder is widely used in industries like aerospace, automotive, electronics, and additive manufacturing (AM).
This alloyed powder’s unique combination of strength, conductivity, and flexibility makes it ideal for both structural and functional components. In the following sections, we’ll break down the specific characteristics, models, and uses of this versatile powder.
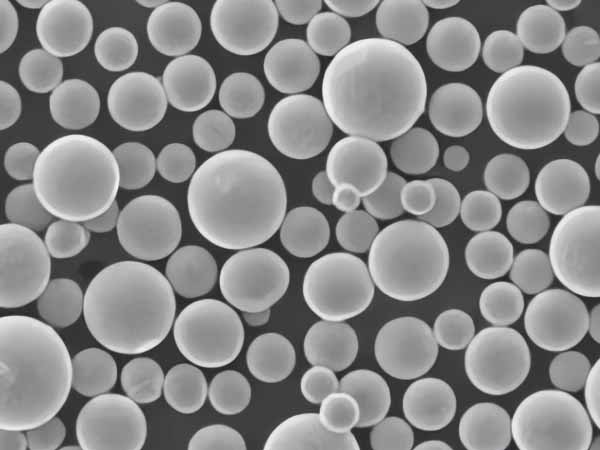
Composition of CuSnTi Powder
When we talk about CuSnTi powder, the composition plays a crucial role in determining its properties. The specific ratios of copper, tin, and titanium dictate how the powder will perform in various applications. Typically, copper makes up the majority, while tin and titanium are added to tweak the material’s properties.
Metal | Composition (Weight %) | Effect on Properties |
---|---|---|
Copper (Cu) | 80-90% | Provides high thermal and electrical conductivity, corrosion resistance |
Tin (Sn) | 5-10% | Improves wear resistance, lubricity, and hardness |
Titanium (Ti) | 2-5% | Enhances strength, corrosion resistance, and fatigue resistance |
The balance between these elements allows CuSnTi powder to stand out among other metal powders by offering both mechanical strength and excellent corrosion resistance.
Characteristics of CuSnTi Powder
Understanding the core characteristics of CuSnTi powder is essential when choosing the right material for your needs. Let’s break down these characteristics:
1. Corrosion Resistance
Thanks to the high copper content, CuSnTi powder exhibits excellent resistance to corrosion in harsh environments. Titanium enhances this property even further, allowing the alloy to withstand exposure to chemicals, seawater, and acidic environments.
2. Mechanical Strength
With the addition of titanium, CuSnTi powder is stronger than pure copper while retaining sufficient ductility. This makes it ideal for mechanical components where both strength and flexibility are needed.
3. Electrical and Thermal Conductivity
While adding tin and titanium reduces conductivity slightly compared to pure copper, CuSnTi still offers excellent electrical and thermal conductivity—a property that’s crucial for electronics and heat-dissipating applications.
4. Wear Resistance
Tin significantly boosts the wear resistance of CuSnTi powder. This makes it a great choice for parts subject to friction or sliding contact, such as bushings, bearings, and gears.
Specific Models of CuSnTi Powder
Now let’s dive into the specific models of CuSnTi powder available on the market. Each of these models has unique compositions and is tailored for specific applications.
Model | Composition (Cu/Sn/Ti) | Key Features | Applications |
---|---|---|---|
CuSnTi-8010 | Cu (80%), Sn (10%), Ti (2%) | High strength, good electrical conductivity | Automotive components |
CuSnTi-7512 | Cu (75%), Sn (12%), Ti (3%) | Excellent wear resistance, moderate conductivity | Bearings, bushings |
CuSnTi-8530 | Cu (85%), Sn (5%), Ti (3%) | Superior corrosion resistance, high fatigue strength | Aerospace components |
CuSnTi-9021 | Cu (90%), Sn (5%), Ti (5%) | Highest electrical conductivity, moderate strength | Electronics, connectors |
CuSnTi-8015 | Cu (80%), Sn (15%), Ti (5%) | Enhanced wear and corrosion resistance | Marine applications |
CuSnTi-8032 | Cu (80%), Sn (10%), Ti (10%) | High strength, superior fatigue resistance | High-stress components |
CuSnTi-8535 | Cu (85%), Sn (10%), Ti (5%) | Balanced strength and ductility | Structural components |
CuSnTi-7525 | Cu (75%), Sn (15%), Ti (10%) | High wear and fatigue resistance | Gears, high-wear surfaces |
CuSnTi-9010 | Cu (90%), Sn (5%), Ti (5%) | Superior thermal conductivity | Heat exchangers, coolers |
CuSnTi-8022 | Cu (80%), Sn (10%), Ti (10%) | High strength and thermal stability | Additive manufacturing |
Each model has been designed to maximize specific properties like strength, conductivity, or corrosion resistance, depending on the industry needs.
Applications of CuSnTi Powder
CuSnTi powder finds its way into numerous industries due to its versatile properties. Let’s explore some of the key applications across different sectors.
Industry | Key Applications | Why CuSnTi Powder? |
---|---|---|
Aerospace | Aircraft structural components | High strength, fatigue resistance |
Automotive | Bushings, bearings, gears | Wear resistance, mechanical strength |
Electronics | Connectors, heat sinks | Electrical conductivity, thermal management |
Marine | Propeller shafts, pumps | Corrosion resistance in seawater environments |
Additive Manufacturing | 3D printing of parts | Powder’s flexibility in custom component creation |
Industrial Machinery | Gears, sliding components | Wear resistance and lubrication properties |
Energy | Heat exchangers, power connectors | High thermal and electrical conductivity |
CuSnTi’s combination of strength, durability, and conductivity makes it ideal for environments where components are subject to mechanical stress, electrical currents, or chemical exposure.
Specifications and Standards of CuSnTi Powder
When selecting CuSnTi powder for any project, knowing the specifications and standards is crucial. Different industries have varying requirements regarding particle size, purity, and consistency.
Specification | CuSnTi Powder Models | Particle Size Range | Standards |
---|---|---|---|
CuSnTi-8010 | 10–50 microns | ASTM B-212 | |
CuSnTi-7512 | 20–45 microns | ISO 4288 | |
CuSnTi-8530 | 15–55 microns | AMS 4676 | |
CuSnTi-9021 | 10–60 microns | MIL-STD-3015 | |
CuSnTi-8015 | 12–50 microns | ASTM B-213 | |
CuSnTi-8032 | 15–45 microns | EN 10204 | |
CuSnTi-8535 | 18–52 microns | ASTM B-962 | |
CuSnTi-7525 | 15–50 microns | ISO 9001:2015 |
These standards ensure that the powder you purchase meets stringent quality and performance criteria, providing consistency across different manufacturing processes.
Suppliers and Pricing for CuSnTi Powder
Finding the right supplier for CuSnTi powder is key to ensuring quality and affordability. Below is a comparative look at some of the leading suppliers.
Supplier | CuSnTi Models Available | Pricing (Per kg) | Region |
---|---|---|---|
MetalPowderCo | CuSnTi-8010, CuSnTi-7512 | $45–$60 | North America |
GlobalAlloys | CuSnTi-8530, CuSnTi-9010 | $40–$55 | Europe |
PowderMetals Ltd | CuSnTi-8015, CuSnTi-8032 | $50–$65 | Asia-Pacific |
AlloyMasters | CuSnTi-8535, CuSnTi-7525 | $38–$52 | North America |
Industrial Powders Co | CuSnTi-9021, CuSnTi-8010 | $42–$57 | Europe |
Pricing varies depending on the model and supplier region, with additional factors such as shipping and bulk discounts coming into play. North America and Europe typically dominate the supply chain for high-quality CuSnTi powders.
Advantages of CuSnTi Powder
So why should you choose CuSnTi powder over other metal powders? Let’s look at some of the top advantages:
1. Enhanced Strength and Durability
Compared to pure copper, CuSnTioffers higher mechanical strength. This makes it suitable for applications where the material will be under mechanical stress or impact.
2. Excellent Corrosion Resistance
The addition of tin and titanium gives CuSnTi powder superior resistance to corrosion, especially in harsh environments like marine or industrial applications.
3. High Wear Resistance
With its ability to withstand wear and tear, CuSnTi is perfect for parts that will experience friction, such as bearings, gears, and bushings.
4. Electrical and Thermal Conductivity
While it may not match the conductivity of pure copper, CuSnTi powder still offers excellent electrical and thermal properties, making it a strong contender for electronics and cooling systems.
Limitations of CuSnTi Powder
While CuSnTi powder is excellent in many applications, it’s not without its downsides:
1. Higher Cost
Due to the inclusion of both tin and titanium, CuSnTi powder tends to be more expensive than simpler copper alloys.
2. Slightly Lower Conductivity
Compared to pure copper, the conductivity of CuSnTi powder is somewhat reduced, which could be a drawback in certain electronic applications.
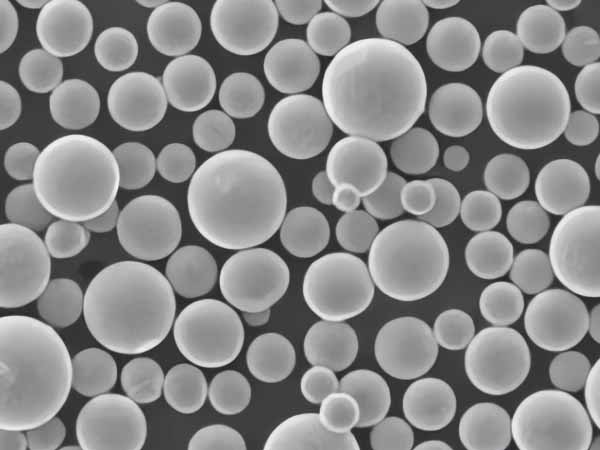
FAQs
Question | Answer |
---|---|
What is CuSnTi powder used for? | It’s used in industries such as aerospace, automotive, and electronics due to its strength, corrosion resistance, and conductivity. |
What is the composition of CuSnTi powder? | CuSnTi is typically composed of 80-90% copper, 5-10% tin, and 2-5% titanium. |
How does CuSnTi powder compare to pure copper? | CuSnTi offers better strength and wear resistance but slightly reduced conductivity compared to pure copper. |
Is CuSnTi powder suitable for 3D printing? | Yes, it’s used in additive manufacturing due to its flexibility and mechanical properties. |
Which industries commonly use CuSnTi powder? | Aerospace, automotive, electronics, marine, and industrial machinery are some of the main industries. |
How much does CuSnTi powder cost? | Pricing ranges from $40 to $65 per kg depending on the supplier and model. |
Conclusion
Whether you’re an engineer seeking high-performance materials for structural components, or you’re working on a cutting-edge electronics project, CuSnTi powder offers a combination of strength, wear resistance, and electrical conductivity that’s hard to match. With various models tailored for different needs, you can find the right composition and specification for your application.
So, the next time you’re selecting a metal powder, consider CuSnTi for its versatile properties and wide range of applications. It’s more than just a powder—it’s the building block of high-performance industrial solutions!