Manufacturing Process of CuSnZn Powder
Understanding how CuSnZn powder is produced can provide valuable insights into its properties and applications. The manufacturing process generally involves several key stages:
1. Alloy Production
The first step in producing CuSnZn powder is alloy production. This is typically done using one of two methods: melting or powder metallurgy. In the melting process, the components are melted together in a furnace, allowing for a homogeneous mixture. In powder metallurgy, the alloy components are mixed in powder form and then sintered to achieve the desired properties.
2. Atomization
Once the alloy is produced, the next step is atomization. In this process, molten metal is rapidly cooled and fragmented into fine particles. There are several atomization techniques, including:
- Water Atomization: The molten metal is sprayed into a water jet, rapidly cooling and solidifying the particles.
- Gas Atomization: Similar to water atomization but uses gas to cool the molten metal, resulting in finer and more spherical particles.
3. Milling and Sizing
After atomization, the metal powder may undergo milling to achieve the desired particle size distribution. This can involve processes like:
- Ball Milling: The powder is placed in a rotating drum with balls that grind the particles to a finer size.
- Jet Milling: High-velocity air is used to collide particles against each other, reducing their size without contamination.
4. Sintering and Compaction
To create a usable form of CuSnZn powder for specific applications, the powder may be compacted into shapes and then sintered. Sintering involves heating the compacted powder below its melting point, allowing the particles to fuse together, resulting in a solid mass with enhanced mechanical properties.
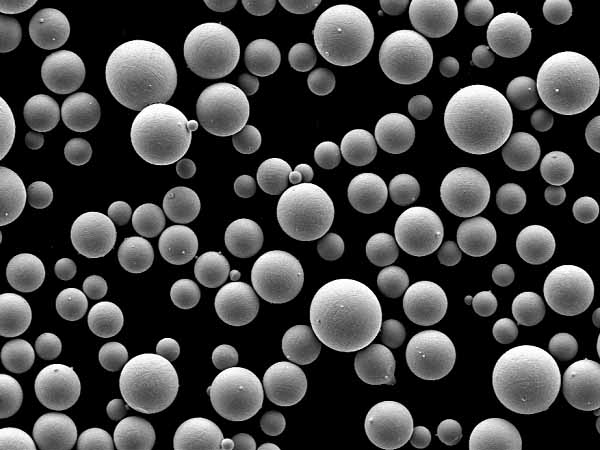
Properties of CuSnZn Powder
Let’s delve deeper into the essential properties of CuSnZn powder, emphasizing how these characteristics affect its performance in various applications.
Property | Description | Impact on Applications |
---|---|---|
Corrosion Resistance | Highly resistant to oxidation and rust due to zinc content. | Ideal for marine and outdoor applications. |
Wear Resistance | Exhibits low wear rates under friction. | Perfect for bearings, bushings, and other moving parts. |
Thermal Conductivity | High thermal conductivity due to copper. | Excellent for heat dissipation in electronic components. |
Electrical Conductivity | Excellent conductor, close to pure copper levels. | Used in electrical connectors and circuit components. |
Strength-to-Weight Ratio | Good mechanical strength relative to weight. | Suitable for lightweight applications needing durability. |
Tensile Strength | Generally ranges from 300 to 600 MPa depending on alloy. | Ensures reliability in structural applications. |
These properties make CuSnZn powder suitable for a wide array of applications, especially where durability and resistance to environmental factors are crucial.
Comparative Analysis of CuSnZn Powder Models
Let’s take a closer look at the various CuSnZn models by comparing them based on key characteristics, advantages, and disadvantages. This can help in selecting the right model for specific applications.
Model | Composition | Hardness | Ductility | Applications | Advantages | Disadvantages |
---|---|---|---|---|---|---|
CuSn10Zn2 | 10% Sn, 2% Zn | 80 HV | Moderate | Bearings, bushings | Good wear resistance, affordable | Limited high-temperature performance |
CuSn12Zn3 | 12% Sn, 3% Zn | 90 HV | Low | Heavy-duty bearings | High toughness, excellent corrosion resistance | More expensive than CuSn10Zn2 |
CuSn8Zn5 | 8% Sn, 5% Zn | 85 HV | High | Electrical connectors | Balanced properties, good machinability | Moderate wear resistance |
CuSn6Zn3 | 6% Sn, 3% Zn | 75 HV | High | Automotive components | Excellent ductility | Lower strength compared to others |
CuSn5Zn5Pb5 | 5% Sn, 5% Zn, 5% Pb | 80 HV | Very High | Gears, bushings | Excellent machinability, self-lubricating | Environmental concerns with lead |
CuSn10ZnPb | 10% Sn, 5% Zn, 5% Pb | 85 HV | High | Low-maintenance machinery | Good wear resistance | Lead-related regulations |
CuSnZnNi | Nickel added | 90 HV | Moderate | Harsh environment applications | Enhanced corrosion resistance | Higher cost due to nickel |
CuSnZnP | Phosphor added | 95 HV | Low | Aerospace components | Excellent wear and temperature resistance | Higher cost and complexity |
CuSnZnSi | Silicon added | 92 HV | Low | Marine applications | High corrosion resistance | Limited machinability |
CuSnZnPbO | Oxide-free variant | 88 HV | Moderate | Electrical applications | Maintains conductivity | Requires specific processing |
Applications Breakdown: Detailed Use Cases
To provide a better understanding of where CuSnZn powder is used, let’s explore its applications in greater detail, along with the specific benefits it brings to each case.
Application | Details | Benefits |
---|---|---|
Bearings | Used in industrial machinery and automotive applications. | Offers low friction, long lifespan under load. |
Electrical Connectors | Utilized in circuit boards and electronic devices. | Ensures high conductivity and reliability. |
Marine Components | Components like pumps, valves, and shafts. | Excellent resistance to saltwater corrosion. |
Aerospace Parts | Critical components in aircraft engines and frames. | High strength-to-weight ratio ensures safety. |
Gears | Precision gears in automotive and machinery. | Low wear rates increase operational efficiency. |
Worm Gears | Used in drive mechanisms. | Good self-lubricating properties reduce maintenance. |
Heat Sinks | Effective in dissipating heat in electronic devices. | Maintains performance in high-temperature applications. |
Pipelines | Connections and fittings in chemical processing plants. | Corrosion resistance ensures longevity. |
Automotive Fasteners | Used in bolts and screws. | High tensile strength keeps components secure. |
Industrial Pumps | Components that handle corrosive fluids. | Durability in harsh environments prevents leaks. |
Market Trends and Future Outlook
As industries continue to evolve, the demand for high-performance materials like CuSnZn powder is only expected to grow. Here are some key trends:
- Increased Use in Renewable Energy: The shift towards renewable energy sources, such as wind and solar, requires materials that can withstand harsh environmental conditions, creating opportunities for CuSnZn applications.
- Growing Aerospace Sector: With the aerospace industry expanding, there is a rising need for lightweight yet strong materials, making CuSnZn a favorable choice for various components.
- Environmental Regulations: Stricter regulations on lead use may push the market towards lead-free variants of CuSnZn powder, leading to increased research and development in these areas.
Challenges in the CuSnZn Powder Market
Despite the bright outlook, there are challenges to consider:
- Cost Fluctuations: The prices of raw materials can fluctuate, impacting the overall cost of CuSnZn powder production.
- Competition from Alternative Materials: Other materials, such as advanced polymers and aluminum alloys, could pose competition for CuSnZn powders in certain applications.
- Recycling Concerns: While CuSnZn powder is recyclable, the processes involved can be complex and costly, affecting its sustainability appeal.
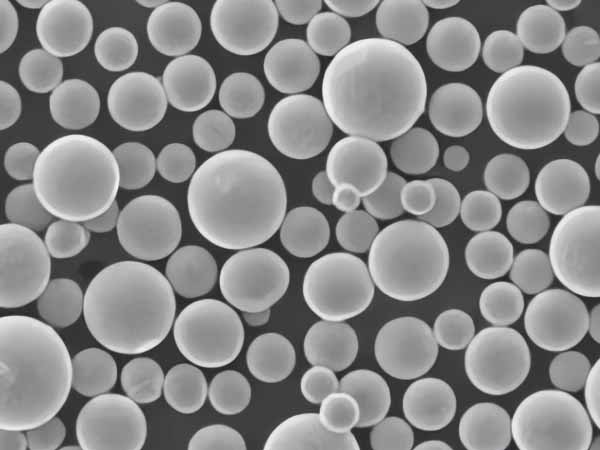
Conclusion
CuSnZn powder is more than just a material; it represents a balance of performance, durability, and versatility that is unmatched in many applications. From bearings that endure extreme wear to electrical connectors that must operate flawlessly under stress, this powder’s properties make it indispensable in a variety of industries.
As we continue to innovate and demand higher performance from materials, CuSnZn powder is well-positioned to meet these needs. Whether you’re an engineer selecting materials for a project or a manufacturer exploring new applications, understanding the intricacies of CuSnZn powder will give you the edge you need.
FAQ
If you have further questions or concerns about CuSnZn powder, here’s an expanded FAQ that might help.
Question | Answer |
---|---|
Is CuSnZn powder safe to use? | Yes, CuSnZn powders are generally safe, but lead variants should be handled with care due to toxicity. |
What is the lifespan of products made from CuSnZn? | Lifespan varies based on application but generally offers a long service life due to its durability. |
Can CuSnZn powder be 3D printed? | Yes, it can be used in selective laser sintering (SLS) and other 3D printing methods. |
What factors affect the price of CuSnZn powder? | Market demand, purity, and supplier pricing strategies can all influence costs. |
Are there any environmental concerns with CuSnZn powder? | Lead-containing alloys have environmental concerns; however, lead-free variants are becoming more popular. |
This expansion further deepens the exploration of CuSnZn powder, ensuring that it’s both informative and engaging for readers. The combination of detailed analyses, comparisons, and FAQs creates a comprehensive resource on the topic.