Overview of Ti45Al8Nb Powder
Ti45Al8Nb is an intermetallic titanium aluminide alloy powder used in powder bed fusion additive manufacturing processes like selective laser melting (SLM) and electron beam melting (EBM).
Some key details about Ti45Al8Nb powder include:
- Contains 45% titanium, 8% niobium, and balance aluminum with trace impurities.
- Has low density, high strength-to-weight ratio, and can withstand high temperatures.
- Used to 3D print lightweight, high-performance components for aerospace, automotive, and other applications.
- Provides good corrosion resistance, weldability, and oxidation resistance up to 700°C.
- More ductile than other high Al titanium aluminide alloys due to niobium additions.
- Powder production methods include gas atomization, plasma rotating electrode process (PREP), and plasma atomization.
Equipment Used for Processing Ti45Al8Nb Powder
Type | Key Characteristics |
---|---|
Gas atomizers | Inert gas rapidly cools melted alloy into powder. Lower cost, suitable for high volumes. |
Plasma atomizers | Plasma energy atomizes molten material into fine, spherical powder. Higher cost. |
Sieving machines | Classify powder into narrow size distributions important for AM. |
Mixers | Blend powders evenly. Reduce segregation. |
Powder recyclers | Remove contamination from reused powder and refresh its flowability. |
Applications of Ti45Al8Nb Components
Category | Uses |
---|---|
Aerospace | Turbine blades, exhaust components, airframe parts. Reduces weight. |
Automotive | Turbocharger wheels, valves, drivetrain parts. Enables performance gains. |
Industrial | Turbomachinery, pumps, tooling. Offers high strength and corrosion resistance. |
Biomedical | Implants, prosthetics. Biocompatible with high strength-to-weight. |
The lightweight, performance properties of 3D printed Ti45Al8Nb make it suitable for demanding applications across industries.
Ti45Al8Nb Powder Specifications
Parameter | Typical Value |
---|---|
Particle size | 15-45 μm |
Morphology | Spherical |
Composition | Ti-45Al-8Nb |
Apparent density | 2.7-3.2 g/cc |
Tap density | 4.0-4.5 g/cc |
Flow rate | 15-25 s/50g |
Residual oxygen | <0.15 wt% |
Powder properties like particle size distribution, morphology, and flowability are critical for high quality 3D printing.
Suppliers of Ti45Al8Nb Powder
Supplier | Key Details | Price per kg |
---|---|---|
Supplier 1 | Wide size distributions. Good spherical morphology. | $100-150 |
Supplier 2 | Research scale batches. Custom alloy development. | $250-500 |
Supplier 3 | High purity, medical/aerospace quality. | $500-1000 |
Prices depend on purity, quality, distribution, quantities ordered, and other factors. Small R&D batches tend to cost more.
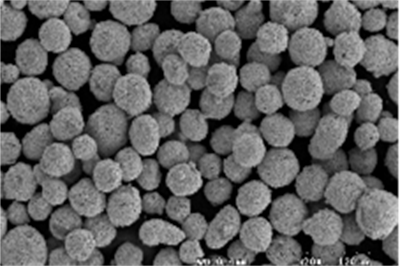
How to Choose a Ti45Al8Nb Powder Supplier
When selecting a Ti45Al8Nb powder supplier, consider the following:
- Quality systems – Supplier should have ISO 9001 or AS9100 certification to ensure reliable quality powder.
- Technical expertise – Look for deep metallurgical knowledge and experience with titanium aluminide alloys.
- AM process experience – Preferred suppliers understand powder requirements for 3D printing applications.
- Consistency – The supplier should reliably produce powder to the same specifications in each batch.
- Sampling – Ask for samples to conduct own quality testing before purchasing batches.
- Lead time – Supplier should deliver powders within reasonable timeframes to avoid delays.
- Recycling – Some suppliers offer cost-effective powder recycling services.
- Price – Compare pricing from several suppliers for your desired material, quality, quantity, etc.
Select a highly qualified Ti45Al8Nb powder supplier focused on AM industry needs to produce quality components.
How to Optimize Ti45Al8Nb Powder for AM Processing
To achieve high density prints with good mechanical properties from Ti45Al8Nb powder, follow these AM process optimization guidelines:
- Use spherical powder with controlled size distribution, typically 15-45 μm. This packs well and spreads evenly.
- Minimize satellite particles which can cause defects. Sieve powder to improve size distribution.
- Apply plasma spheroidization if powder particles are too irregular or porous after atomization.
- Ensure good powder flowability – refresh powder with mixers/recyclers if flow rate drops.
- Set hot bed temperature above 80°C to reduce thermal stresses in the alloy during printing.
- Use higher laser powers >400 W to properly melt the powder. Optimize parameters to limit porosity.
- Print with 30-50 μm layers for good resolution and density. Thinner layers may cause balling.
- Minimize support structures – Ti45Al8Nb can bridge small gaps without supports.
- Conduct print trials to dial in ideal settings for the specific printer and powder batch.
Work with powder and part suppliers to identify optimal powder characteristics and process parameters. Test samples before a full production run.
How to Post-Process 3D Printed Ti45Al8Nb Components
Common post-processing techniques for as-printed Ti45Al8Nb components include:
- Support removal – Carefully remove support structures, if any, using wire EDM or cutting.
- Stress relieving – Heat to 600-800°C for 1-3 hours to relieve residual stresses from the build.
- Machining – CNC milling, turning, drilling to improve dimensional accuracy and surface finish. Use rigid setups suitable for hard alloys.
- Grinding – Automated or manual grinding with rigid fixturing yields precision tolerances.
- Polishing – Can achieve excellent surface finishes and removes any adhered powder.
- Coatings – Apply functional coatings for hardness, wear resistance, corrosion protection, etc.
- Hot isostatic pressing (HIP) – Further densifies internal structure and improves fatigue performance.
Work with experienced operators familiar with titanium alloys to avoid damaging the components during post-processing.
Design Principles for 3D Printing Ti45Al8Nb
When designing components to be 3D printed from Ti45Al8Nb powder, consider the following design guidelines:
- Avoid overhangs exceeding 45° to prevent support requirements.
- Include small fillets and radii in corners to reduce stress concentrations.
- Design wall thicknesses greater than 1 mm to prevent failures or deformations.
- Account for 40-50% reduction in strength along layer plane compared to vertical direction.
- Position and orient parts to minimize supports and ensure uniform heating and cooling.
- Design enclosed internal channels with vent holes rather than completely sealed volumes.
- Allow 0.5-1 mm of stock material for post-processing removal to achieve final dimensions.
- Consolidate assemblies into fewer parts to reduce weight, processing steps, and costs.
Work collaboratively with AM process engineers to design parts optimized for additive manufacturing from the outset.
Qualifying 3D Printed Ti45Al8Nb Components
To gain confidence in 3D printed Ti45Al8Nb parts for end-use applications, conduct the following qualifications:
- Visual – Inspect for defects like cracking, porosity, surface finish flaws.
- Microscopy – Use optical or electron microscopy to characterize microstructure and internal voids.
- Density – Measure density distribution and compare to wrought material properties.
- Mechanical testing – Conduct tension, compression, and hardness tests per ASTM standards.
- Non-destructive – Use techniques like x-ray or ultrasonic inspection to detect internal defects.
- Dimensional – Confirm critical dimensions meet specified tolerances.
- Lifetime testing – Test parts through extended cycles and usage conditions.
- Process validation – Print test geometries and coupon samples that represent production components.
Work with accredited labs and consultants with metallurgy and AM experience when qualifying high value or critical components.
Installing and Integrating 3D Printed Ti45Al8Nb Parts
When preparing 3D printed Ti45Al8Nb components for integration into assemblies and end-use systems:
- Thoroughly clean surfaces – remove any powder residue, oxidation, or contamination.
- Apply protective coatings if needed – anodizing improves corrosion and wear resistance.
- Use thermal management – control temperatures during joining to avoid cracking.
- Account for lower ductility – avoid or minimize impact loads which could cause fractures.
- Allow for thermal expansion differences when joining to other materials.
- Select suitable joining methods – bolting, adhesive bonding, brazing, and welding can work.
- Validate functionality – test components under actual loading and operating environments.
- Inspect for defects – use NDT methods like x-ray, penetrant testing to identify any subsurface flaws.
Consult closely with design and manufacturing engineers throughout the integration process to avoid any issues.
Usage and Maintenance of Printed Ti45Al8Nb Parts
To achieve optimal in-service performance from 3D printed Ti45Al8Nb components:
- Operate within recommended temperature ranges – typically up to 700°C for prolonged use.
- Avoid excessive vibrations – can lead to fatigue failures in as-printed microstructure.
- Protect against corrosion – anodize or apply coatings if used in harsh environments.
- Periodically inspect for cracks, wear, corrosion damage, or other degradation.
- Clean surfaces – prevent buildup of contaminants or films which may impede performance.
- Confirm critical dimensions remain within tolerances – check for any distortions over time.
- Re-apply surface coatings as needed – electroplating, anodizing, etc. may wear with use.
- Watch for oxidation above 500°C – may adversely affect properties.
Develop detailed maintenance plans and schedules for critical printed components, especially in demanding applications.
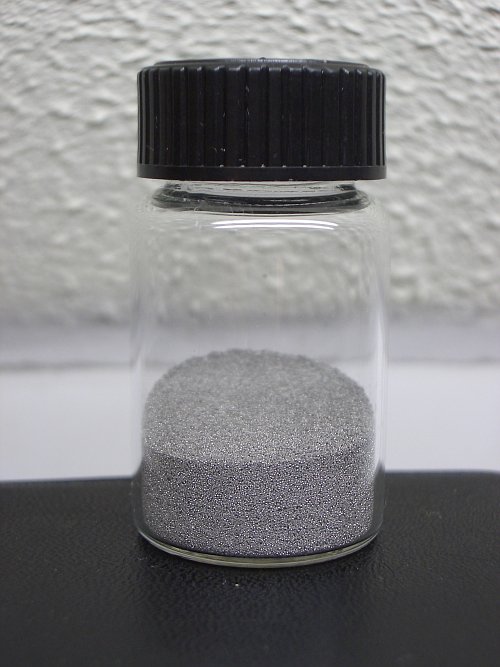
Pros and Cons of 3D Printing With Ti45Al8Nb
There are both advantages and limitations of 3D printing components from Ti45Al8Nb powder compared to conventional titanium fabrication approaches:
Advantages
- Components can be topological optimized with complex geometries.
- Consolidates assemblies into single printed parts.
- Reduces buy-to-fly ratios and material waste.
- Lowers costs for small to medium production volumes.
- Allows lightweight designs with similar strength to denser alloys.
- Shortens development timelines for new designs.
Disadvantages
- Material properties depend heavily on AM process parameters.
- Post-processing like HIP often required to achieve material specs.
- Size limitations based on build chamber dimensions.
- Higher per-part cost compared to casting or forging at high volumes.
- Anisotropic properties due to layer-based printing.
- Supply chain for high performance powder can be restrictive.
Assess the benefits and limitations relative to production needs when determining suitability of AM with Ti45Al8Nb versus conventional manufacturing methods.
FAQ
Q: What particle size powder is recommended for AM?
A: 15-45 μm is typical, with a tightly controlled distribution. Too fine or wide distributions can negatively impact density.
Q: What are some alternatives to Ti45Al8Nb for high temperature use?
A: Other titanium aluminides like Ti48Al2Cr2Nb or nickel superalloys like Inconel 718 can also work depending on requirements.
Q: Does Ti45Al8Nb require hot isostatic pressing (HIP) after printing?
A: HIP can help eliminate internal voids and further improve properties. But well-optimized AM processes can potentially avoid the need for HIP.
Q: What types of post-processing are recommended for Ti45Al8Nb?
A: Stress relieving, machining, grinding, polishing, and coating are common. Apply any needed integration steps like fastening.
Q: Is Ti45Al8Nb suitable for biomedical implants?
A: Yes, it provides an excellent combination of high strength, low stiffness, and biocompatibility needed for implants.
Q: What precautions are needed when handling titanium aluminide powders?
A: Use protective equipment to avoid breathing fine powders. Avoid ignition risks by managing dust levels since the alloys are flammable.
Q: Does recycled Ti45Al8Nb powder perform the same as virgin powder?
A: With proper recycling protocols, refreshed recycled powder can yield comparable performance to new powder in many applications.
Q: Can you weld 3D printed Ti45Al8Nb parts?
A: Yes, friction stir welding has been demonstrated for these alloys. Laser welding is also possible but can alter local material properties.