Overview of Diffusion Alloy Powder
Diffusion alloy powder is a specialized material used extensively in various industries, from automotive to aerospace, due to its unique properties and capabilities. This powder consists of base metal particles coated with one or more alloying elements. The process involves heating the mixture to a temperature where the coating diffuses into the base particles, creating a homogenous material with enhanced properties.
Key Details:
- Composition: Base metal coated with alloying elements.
- Properties: Enhanced hardness, wear resistance, and corrosion resistance.
- Applications: Automotive parts, aerospace components, industrial machinery.
- Advantages: Improved material performance, cost-effective production, versatile applications.
Types of Diffusion Alloy Powder
Let’s delve into some specific models of diffusion alloy powders, each with its unique composition and properties:
Model | Base Metal | Alloying Elements | Key Properties |
---|---|---|---|
Model A | Iron | Chromium, Nickel | High corrosion resistance, improved hardness |
Model B | Copper | Zinc, Tin | Enhanced conductivity, moderate wear resistance |
Model C | Aluminum | Silicon, Magnesium | Lightweight, excellent strength-to-weight ratio |
Model D | Titanium | Aluminum, Vanadium | High strength, excellent corrosion resistance |
Model E | Nickel | Chromium, Molybdenum | Superior heat resistance, corrosion resistant |
Model F | Stainless Steel | Chromium, Nickel | High durability, excellent wear resistance |
Model G | Cobalt | Chromium, Tungsten | High wear resistance, good thermal stability |
Model H | Magnesium | Zinc, Manganese | Lightweight, high strength |
Model I | Tungsten | Nickel, Iron | High density, excellent wear resistance |
Model J | Zinc | Aluminum, Copper | Good corrosion resistance, low melting point |
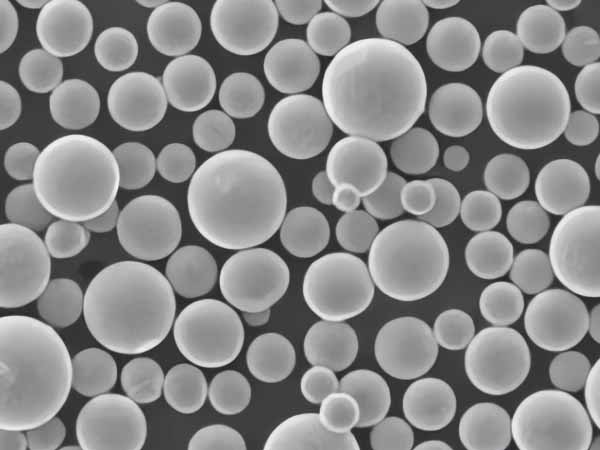
Composition of Diffusion Alloy Powder
The composition of diffusion alloy powder is critical in determining its properties and suitability for various applications. Here’s a detailed look at the typical compositions:
Model | Base Metal | Alloying Elements | Composition Ratio (%) |
---|---|---|---|
Model A | Iron | Chromium (15%), Nickel (5%) | Fe: 80%, Cr: 15%, Ni: 5% |
Model B | Copper | Zinc (10%), Tin (5%) | Cu: 85%, Zn: 10%, Sn: 5% |
Model C | Aluminum | Silicon (8%), Magnesium (4%) | Al: 88%, Si: 8%, Mg: 4% |
Model D | Titanium | Aluminum (6%), Vanadium (4%) | Ti: 90%, Al: 6%, V: 4% |
Model E | Nickel | Chromium (12%), Molybdenum (8%) | Ni: 80%, Cr: 12%, Mo: 8% |
Model F | Stainless Steel | Chromium (18%), Nickel (8%) | SS: 74%, Cr: 18%, Ni: 8% |
Model G | Cobalt | Chromium (10%), Tungsten (5%) | Co: 85%, Cr: 10%, W: 5% |
Model H | Magnesium | Zinc (5%), Manganese (2%) | Mg: 93%, Zn: 5%, Mn: 2% |
Model I | Tungsten | Nickel (8%), Iron (4%) | W: 88%, Ni: 8%, Fe: 4% |
Model J | Zinc | Aluminum (4%), Copper (2%) | Zn: 94%, Al: 4%, Cu: 2% |
Characteristics of Diffusion Alloy Powder
Diffusion alloy powders are known for their distinct characteristics which make them suitable for various industrial applications. Let’s break down these characteristics:
Characteristic | Description |
---|---|
Hardness | Enhanced due to the diffusion of alloying elements, making the material more resistant to deformation. |
Wear Resistance | High, especially in models with chromium or tungsten, reducing material degradation over time. |
Corrosion Resistance | Improved, particularly in nickel-based and stainless steel powders, protecting against rust and decay. |
Thermal Stability | Excellent in powders containing elements like tungsten or molybdenum, retaining properties at high temperatures. |
Strength-to-Weight Ratio | High in aluminum and titanium-based powders, ideal for lightweight yet strong applications. |
Electrical Conductivity | Enhanced in copper-based powders, suitable for electrical and electronic applications. |
Applications of Diffusion Alloy Powder
Diffusion alloy powders are utilized across a wide range of industries due to their versatile properties. Here are some of the primary applications:
Industry | Applications |
---|---|
Automotive | Engine components, gears, brake discs, and exhaust systems. |
Aerospace | Aircraft engine parts, structural components, and landing gear. |
Industrial Machinery | Cutting tools, bearings, and pumps. |
Electronics | Conductive pastes, connectors, and circuit boards. |
Medical Devices | Implants, surgical instruments, and diagnostic equipment. |
Energy | Turbine blades, fuel cells, and solar panels. |
Specifications, Sizes, Grades, and Standards
When selecting diffusion alloy powders, it’s essential to consider the specifications, sizes, grades, and standards to ensure they meet the application requirements.
Model | Particle Size (μm) | Grade | Standards |
---|---|---|---|
Model A | 10-50 | Premium | ASTM B214, ISO 4497 |
Model B | 20-60 | Industrial | ASTM B212, ISO 3923 |
Model C | 5-45 | High Purity | ASTM B330, ISO 3507 |
Model D | 15-55 | Aerospace | ASTM B348, ISO 5832 |
Model E | 10-40 | High Temperature | ASTM B394, ISO 6486 |
Model F | 25-75 | Corrosion Resistant | ASTM B366, ISO 683 |
Model G | 30-90 | Wear Resistant | ASTM B333, ISO 5831 |
Model H | 5-35 | Lightweight | ASTM B403, ISO 4497 |
Model I | 20-70 | High Density | ASTM B701, ISO 4498 |
Model J | 15-65 | Low Melting Point | ASTM B669, ISO 13314 |
Suppliers and Pricing Details
Finding reliable suppliers and understanding the pricing of diffusion alloy powders is crucial for industrial procurement.
Supplier | Location | Product Range | Price (per kg) |
---|---|---|---|
Supplier A | USA | Models A, B, C | $50 – $150 |
Supplier B | Germany | Models D, E, F | €70 – €200 |
Supplier C | China | Models G, H, I | ¥400 – ¥1200 |
Supplier D | Japan | Models A, C, E, G | ¥6000 – ¥18000 |
Supplier E | India | Models B, D, F, H | ₹3000 – ₹9000 |
Comparing Pros and Cons of Diffusion Alloy Powder
Understanding the advantages and limitations of diffusion alloy powders can help in making an informed decision.
Characteristic | Advantages | Limitations |
---|---|---|
Hardness | Enhanced hardness improves durability and lifespan of components. | May require specialized equipment for processing. |
Wear Resistance | High wear resistance reduces maintenance costs and downtime. | Can be expensive depending on the alloying elements used. |
Corrosion Resistance | Superior corrosion resistance extends the usability in harsh environments. | Potential for higher initial cost. |
Thermal Stability | Maintains performance at elevated temperatures, suitable for high-temperature applications. | Limited to specific high-temperature environments. |
Strength-to-Weight Ratio | Ideal for applications where weight is a critical factor, such as aerospace and automotive. | Lightweight materials may have lower overall strength. |
Electrical Conductivity | Essential for electronic applications, ensuring reliable performance. | Limited to certain base metals like copper. |
In-Depth Look at Specific Metal Powder Models
Let’s take a closer look at some specific metal powder models, highlighting their unique features and applications:
Model A: Iron-Chromium-Nickel Powder
This model is particularly known for its high corrosion resistance and improved hardness. It’s extensively used in the automotive and industrial machinery sectors, where durability and longevity are paramount.
Model B: Copper-Zinc-Tin Powder
Model B offers enhanced conductivity and moderate wear resistance, making it a preferred choice for electrical and electronic applications. It’s also used in the manufacturing of connectors and conductive pastes.
Model C: Aluminum-Silicon-Magnesium Powder
Lightweight yet strong, Model C is ideal for aerospace applications. Its excellent strength-to-weight ratio makes it suitable for structural components and engine parts.
Model D: Titanium-Aluminum-Vanadium Powder
With high strength and excellent corrosion resistance, Model D is perfect for medical devices and aerospace applications. It’s often used in implants and aircraft engine parts.
Model E: Nickel-Chromium-Molybdenum Powder
Model E is known for its superior heat resistance and corrosion resistance. It’s commonly used in high-temperature environments, such as turbine blades and fuel cells.
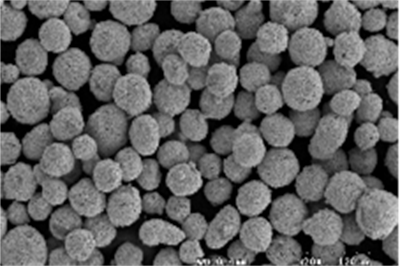
FAQs
Question | Answer |
---|---|
What is diffusion alloy powder? | Diffusion alloy powder is a material consisting of base metal particles coated with alloying elements. |
How is diffusion alloy powder made? | It’s made by heating a mixture of base metal and alloying elements to a temperature where diffusion occurs. |
What are the benefits of using diffusion alloy powder? | Enhanced properties like hardness, wear resistance, and corrosion resistance. |
Which industries use diffusion alloy powder? | Automotive, aerospace, industrial machinery, electronics, medical devices, and energy sectors. |
How do I choose the right diffusion alloy powder? | Consider the application’s specific requirements, such as hardness, wear resistance, and thermal stability. |
Can diffusion alloy powder be customized? | Yes, the composition can be tailored to meet specific application needs. |
What are the common alloying elements used? | Chromium, nickel, silicon, magnesium, aluminum, and molybdenum are commonly used alloying elements. |
Is diffusion alloy powder expensive? | The cost varies depending on the base metal and alloying elements used. |
Where can I buy diffusion alloy powder? | Various suppliers globally, including those in the USA, Germany, China, Japan, and India. |
Are there any limitations to using diffusion alloy powder? | Potential higher initial cost and the need for specialized processing equipment. |
Conclusion
Diffusion alloy powder represents a significant advancement in material science, offering a versatile solution for enhancing the properties of base metals. From improving hardness and wear resistance to providing excellent corrosion resistance, these powders are indispensable in a range of industries. By understanding the various models, compositions, and applications, businesses can make informed decisions to leverage the benefits of diffusion alloy powders effectively. Whether you’re in the automotive, aerospace, or electronics sector, the right diffusion alloy powder can elevate the performance and durability of your products.