Directed Energy Deposition (DED) is an advanced manufacturing technique that has revolutionized the field of metal additive manufacturing. It involves the focused application of energy to deposit materials, typically metals, layer by layer to create complex structures. This comprehensive guide delves into every aspect of DED, from its basic principles to the intricate details of metal powders used in the process. Let’s embark on this journey to understand the fascinating world of DED.
Overview of Directed Energy Deposition (DED)
Directed Energy Deposition (DED) is a form of additive manufacturing that uses a focused energy source, such as a laser, electron beam, or plasma arc, to melt and deposit material, typically in the form of metal powders or wires, onto a substrate. This process allows for precise control over the deposition, enabling the creation of complex geometries and the repair of high-value components.
Key Features of DED:
- High precision and control
- Ability to work with a variety of metals
- Suitable for both creating new parts and repairing existing ones
- Utilizes metal powders or wires as feedstock
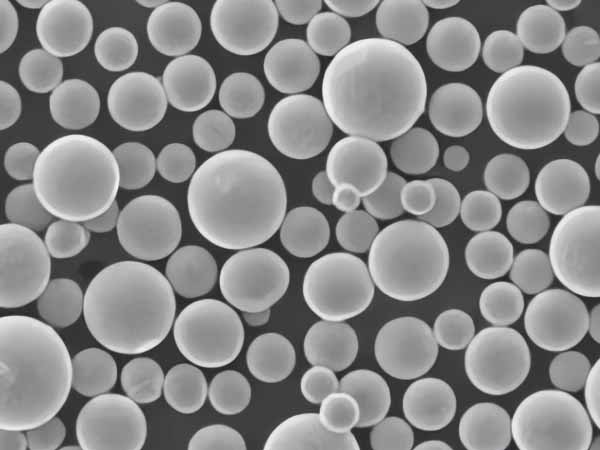
Types and Composition of Metal Powders for DED
Choosing the right metal powder is crucial for the success of the DED process. Here, we list and describe some of the most commonly used metal powders in DED:
Metal Powder | Composition | Properties | Characteristics |
---|---|---|---|
Ti-6Al-4V | Titanium alloy with 6% Aluminum, 4% Vanadium | High strength-to-weight ratio, corrosion resistance | Widely used in aerospace and biomedical applications |
316L Stainless Steel | Iron alloy with Chromium, Nickel, Molybdenum | Excellent corrosion resistance, good mechanical properties | Common in medical, food processing, and marine industries |
Inconel 718 | Nickel-based superalloy with Chromium, Iron, Molybdenum | High temperature resistance, good tensile strength | Used in jet engines and high-temperature applications |
AlSi10Mg | Aluminum alloy with Silicon and Magnesium | Lightweight, good thermal conductivity | Popular in automotive and aerospace sectors |
Hastelloy X | Nickel-chromium-iron-molybdenum alloy | High strength at elevated temperatures, oxidation resistance | Suitable for gas turbine engines |
Cobalt-Chrome | Cobalt alloy with Chromium | High wear and corrosion resistance, biocompatibility | Ideal for medical implants and dental prosthetics |
Maraging Steel | Low-carbon martensitic steel with Nickel, Cobalt, Molybdenum | Ultra-high strength, toughness | Used in tooling and high-strength applications |
Copper | Pure Copper | Excellent electrical and thermal conductivity | Utilized in electrical and heat exchanger components |
Tungsten Carbide | Tungsten and Carbon | Extremely hard, wear-resistant | Employed in cutting tools and abrasive surfaces |
Tool Steel (H13) | Iron alloy with Chromium, Molybdenum, Vanadium | High hardness, good thermal fatigue resistance | Suitable for die-casting and extrusion tools |
Applications of Directed Energy Deposition (DED)
The versatility of DED makes it suitable for a wide range of applications across various industries. Here’s a look at some of the primary uses:
Application Area | Examples | Benefits |
---|---|---|
Aerospace | Turbine blades, structural components | Lightweight, strong, resistant to high temperatures |
Medical | Implants, prosthetics, dental devices | Customization, biocompatibility |
Automotive | Engine components, lightweight parts | Improved fuel efficiency, reduced emissions |
Tooling | Molds, dies, cutting tools | Enhanced durability, reduced lead time |
Energy | Gas turbine components, heat exchangers | High temperature resistance, improved efficiency |
Defense | Armored vehicle parts, weapon components | Enhanced strength, customized designs |
Research | Prototyping, material development | Rapid iteration, ability to test new materials |
Repair and Maintenance | Restoration of high-value components | Cost-effective, reduces downtime |
Oil and Gas | Drill bits, pipeline components | Wear resistance, high strength |
Construction | Structural elements, cladding | Customized designs, high durability |
Specifications, Sizes, Grades, and Standards
Understanding the specifications, sizes, grades, and standards of metal powders used in DED is essential for selecting the right material for a given application.
Metal Powder | Available Sizes | Grades | Standards |
---|---|---|---|
Ti-6Al-4V | 15-45 µm, 45-105 µm | Grade 5, Grade 23 | ASTM F2924, AMS 4999 |
316L Stainless Steel | 15-45 µm, 45-105 µm | AISI 316L | ASTM A276, UNS S31603 |
Inconel 718 | 15-45 µm, 45-105 µm | UNS N07718 | AMS 5662, ASTM B637 |
AlSi10Mg | 15-45 µm, 45-105 µm | EN AC-43000 | ISO 3522 |
Hastelloy X | 15-45 µm, 45-105 µm | UNS N06002 | ASTM B435, AMS 5536 |
Cobalt-Chrome | 15-45 µm, 45-105 µm | CoCrMo, F75 | ASTM F75, ISO 5832-4 |
Maraging Steel | 15-45 µm, 45-105 µm | 18Ni(300), MDN 250 | AMS 6514, ASTM A538 |
Copper | 15-45 µm, 45-105 µm | C11000, C18150 | ASTM B170, ASTM B152 |
Tungsten Carbide | 1-20 µm, 10-50 µm | WC-Co, WC-Ni | ISO 4499-5 |
Tool Steel (H13) | 15-45 µm, 45-105 µm | H13 | ASTM A681, DIN 1.2344 |
Suppliers and Pricing Details
Choosing the right supplier is crucial for obtaining high-quality metal powders at competitive prices. Here’s a list of some reputable suppliers along with pricing details:
Supplier | Metal Powder | Price (per kg) | Notes |
---|---|---|---|
Carpenter Technology | Ti-6Al-4V | $150 – $200 | High-quality aerospace-grade powders |
Sandvik Osprey | 316L Stainless Steel | $50 – $80 | Wide range of stainless steel powders |
Höganäs AB | Inconel 718 | $120 – $180 | Premium superalloy powders |
EOS GmbH | AlSi10Mg | $70 – $100 | Excellent consistency and quality |
Praxair Surface Technologies | Hastelloy X | $200 – $250 | High-performance nickel alloys |
Arcam AB | Cobalt-Chrome | $100 – $150 | Medical-grade powders |
LPW Technology | Maraging Steel | $90 – $130 | Specialty high-strength steels |
GKN Additive | Copper | $40 – $60 | High conductivity powders |
Kennametal | Tungsten Carbide | $300 – $400 | Extremely hard and durable powders |
Böhler Edelstahl | Tool Steel (H13) | $70 – $110 | Superior quality for tooling applications |
Pros and Cons of Directed Energy Deposition (DED)
Every manufacturing technique comes with its set of advantages and limitations. Here’s a comparison to help understand DED better:
Advantages | Disadvantages |
---|---|
High precision and control over material deposition | Initial setup cost can be high |
Capable of producing complex geometries | Requires skilled operators |
Suitable for repairing high-value components | Limited to certain types of materials |
Reduces material wastage compared to subtractive methods | Surface finish may require post-processing |
Flexibility in material choices, including metal powders and wires | Deposition rate can be slower compared to other methods |
Characteristics of Directed Energy Deposition (DED)
The DED process is characterized by several unique attributes that set it apart from other additive manufacturing techniques:
- Energy Source: DED utilizes a concentrated energy source such as a laser, electron beam, or plasma arc to melt and deposit materials.
- Feedstock: The process can use either metal powders or wires, providing flexibility in material selection.
- Layer-by-Layer Deposition: Material is deposited layer by layer, allowing for the creation of complex geometries.
- Real-Time Monitoring: Advanced DED systems incorporate sensors and monitoring equipment to ensure precision and quality.
- Multi-Material Capability: DED can be used to create multi-material components, enhancing functionality and performance.
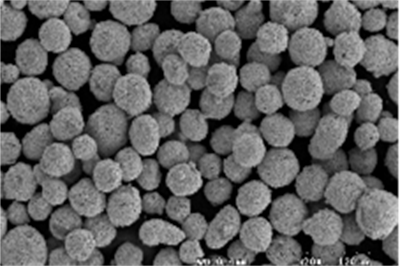
FAQs
What is Directed Energy Deposition (DED)?
Q: What is Directed Energy Deposition (DED)?
A: Directed Energy Deposition (DED) is an additive manufacturing process that uses a focused energy source, such as a laser, electron beam, or plasma arc, to melt and deposit material, typically metals, layer by layer to create complex structures.
How does DED differ from other additive manufacturing processes?
Q: How does DED differ from other additive manufacturing processes?
A: DED differs from other additive manufacturing processes by using a concentrated energy source to directly melt and deposit materials, allowing for precise control and the ability to repair high-value components. It can also use both metal powders and wires as feedstock.
What are the common applications of DED?
Q: What are the common applications of DED?
A: Common applications of DED include aerospace components, medical implants, automotive parts, tooling, energy sector components, defense equipment, research prototypes, and repair and maintenance of high-value parts.
What materials can be used in the DED process?
Q: What materials can be used in the DED process?
A: Materials commonly used in the DED process include titanium alloys (e.g., Ti-6Al-4V), stainless steels (e.g., 316L), nickel-based superalloys (e.g., Inconel 718), aluminum alloys (e.g., AlSi10Mg), cobalt-chrome, maraging steel, copper, tungsten carbide, and tool steels (e.g., H13).
What are the benefits of using DED?
Q: What are the benefits of using DED?
A: Benefits of using DED include high precision and control over material deposition, the ability to produce complex geometries, suitability for repairing high-value components, reduced material wastage, flexibility in material choices, and the ability to create multi-material components.
Are there any limitations to the DED process?
Q: Are there any limitations to the DED process?
A: Limitations of the DED process include high initial setup costs, the need for skilled operators, limitations on material types, potential need for post-processing to achieve desired surface finishes, and slower deposition rates compared to other methods.
How do I choose the right metal powder for DED?
Q: How do I choose the right metal powder for DED?
A: Choosing the right metal powder for DED involves considering factors such as the material’s composition, properties, characteristics, application requirements, and compatibility with the DED system. Consulting with suppliers and understanding the specific needs of your project can help in making an informed decision.
Who are the leading suppliers of metal powders for DED?
Q: Who are the leading suppliers of metal powders for DED?
A: Leading suppliers of metal powders for DED include Carpenter Technology, Sandvik Osprey, Höganäs AB, EOS GmbH, Praxair Surface Technologies, Arcam AB, LPW Technology, GKN Additive, Kennametal, and Böhler Edelstahl.
What factors affect the cost of metal powders for DED?
Q: What factors affect the cost of metal powders for DED?
A: Factors affecting the cost of metal powders for DED include the type of material, purity, particle size distribution, manufacturing process, supplier, and market demand. High-performance alloys and specialized powders tend to be more expensive.
Can DED be used for multi-material manufacturing?
Q: Can DED be used for multi-material manufacturing?
A: Yes, DED can be used for multi-material manufacturing, allowing the creation of components with varying properties and enhanced functionality. This capability is particularly useful in applications requiring gradient materials or parts with different performance characteristics.
Conclusion
Directed Energy Deposition (DED) is a powerful and versatile additive manufacturing technique that offers numerous benefits for creating and repairing complex metal parts. By understanding the types of metal powders available, their properties, and the applications of DED, manufacturers can make informed decisions to optimize their production processes. Whether you’re involved in aerospace, medical, automotive, or any other industry, DED has the potential to revolutionize the way you approach manufacturing and repair. Embrace the future of manufacturing with DED and unlock new possibilities for innovation and efficiency.