Overview
The Divergent Adaptive Production System (DAPS) is a groundbreaking approach in the manufacturing sector, leveraging advanced technologies to optimize production processes. This system adapts to varying production requirements, enhancing efficiency, flexibility, and sustainability. By integrating innovative methodologies and cutting-edge materials, DAPS offers a transformative solution for modern manufacturing challenges.
What is a Divergent Adaptive Production System (DAPS)?
DAPS is designed to respond dynamically to changes in production demands, materials, and market conditions. Unlike traditional rigid production systems, DAPS is built on flexibility and adaptability, allowing manufacturers to quickly pivot and meet diverse needs. This system utilizes a combination of digital technologies, such as AI, IoT, and big data analytics, to monitor and adjust processes in real-time, ensuring optimal performance and minimal waste.
Key Features of DAPS:
- Adaptability: Easily adjusts to changes in production requirements and materials.
- Efficiency: Optimizes resource use and minimizes waste through real-time adjustments.
- Sustainability: Incorporates eco-friendly practices and materials, reducing environmental impact.
- Scalability: Suitable for small-scale and large-scale production needs.
- Integration: Seamlessly integrates with existing manufacturing systems and processes.
Metal Powders in DAPS
Metal powders play a crucial role in DAPS, especially in additive manufacturing and 3D printing applications. These powders must meet specific criteria regarding composition, particle size, and properties to ensure quality and consistency in the final products.
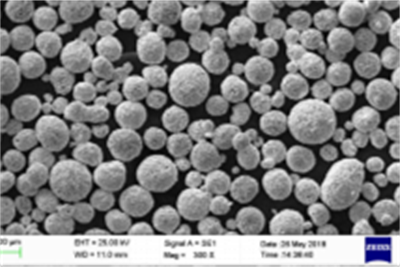
Types of Metal Powders Used in DAPS
Type | Composition | Properties | Applications |
---|---|---|---|
Titanium Alloy | Ti-6Al-4V | High strength, corrosion resistance | Aerospace, medical implants |
Stainless Steel | 316L, 17-4 PH | Corrosion resistance, durability | Automotive, industrial equipment |
Aluminum Alloy | AlSi10Mg | Lightweight, good mechanical properties | Aerospace, automotive, consumer goods |
Nickel Alloy | Inconel 718, 625 | High temperature resistance | Turbine blades, aerospace |
Cobalt-Chrome | CoCr | Wear resistance, biocompatibility | Medical implants, dental prosthetics |
Copper Alloy | CuCrZr | High conductivity | Electrical components, heat exchangers |
Tool Steel | H13, M2 | Hardness, wear resistance | Molds, dies, cutting tools |
Tungsten | W | High density, high melting point | Aerospace, defense, electrical contacts |
Bronze | Cu-Sn alloys | Low friction, good wear properties | Bearings, bushings, sculptures |
Magnesium Alloy | AZ91D, WE43 | Lightweight, good strength-to-weight | Automotive, aerospace, electronics |
Applications of Metal Powders in DAPS
Application | Description |
---|---|
Aerospace | Manufacturing of lightweight, high-strength components for aircraft and spacecraft |
Automotive | Production of durable, lightweight parts to improve fuel efficiency and performance |
Medical Implants | Creation of biocompatible implants and prosthetics |
Industrial Equipment | Fabrication of robust machinery and tools for various industrial applications |
Consumer Goods | Development of customized and durable consumer products |
Electrical Components | Production of high-conductivity parts for electronic devices |
Defense | Manufacturing of high-density components for military applications |
Heat Exchangers | Creation of efficient thermal management systems |
Sculptures and Art | Crafting of intricate and durable artistic pieces |
Cutting Tools | Production of high-hardness, wear-resistant tools |
Specifications of Metal Powders for DAPS
Type | Particle Size (µm) | Purity (%) | Density (g/cm³) | Standards |
---|---|---|---|---|
Titanium Alloy | 15-45 | >99.5 | 4.43 | ASTM F2924, AMS 4998 |
Stainless Steel | 10-50 | >99.5 | 7.8 | ASTM A240, ASTM F138 |
Aluminum Alloy | 20-60 | >99.8 | 2.7 | ASTM B209, ISO 3522 |
Nickel Alloy | 15-45 | >99.5 | 8.44 | ASTM B637, AMS 5662 |
Cobalt-Chrome | 10-50 | >99.5 | 8.3 | ASTM F75, ISO 5832-4 |
Copper Alloy | 15-60 | >99.9 | 8.96 | ASTM B152, EN 1652 |
Tool Steel | 20-50 | >99.5 | 7.8 | ASTM A681, ISO 4957 |
Tungsten | 10-45 | >99.9 | 19.3 | ASTM B777, MIL-T-21014 |
Bronze | 20-80 | >99.8 | 8.8 | ASTM B584, EN 1982 |
Magnesium Alloy | 20-60 | >99.9 | 1.74 | ASTM B93, AMS 4377 |
Suppliers and Pricing Details
Supplier | Metal Powder Types | Price Range (per kg) | Location | Contact Information |
---|---|---|---|---|
Höganäs AB | Titanium, Stainless Steel | $200 – $400 | Sweden | website |
GKN Hoeganaes | Aluminum, Nickel, Cobalt-Chrome | $150 – $350 | USA | website |
LPW Technology | Tool Steel, Tungsten | $250 – $500 | UK | website |
Arcam AB | Titanium, Aluminum | $180 – $380 | Sweden | website |
Carpenter Powder | Nickel, Cobalt-Chrome | $220 – $450 | USA | website |
AP&C | Stainless Steel, Aluminum | $170 – $330 | Canada | website |
TLS Technik | Copper, Bronze | $140 – $300 | Germany | website |
Sandvik | Tool Steel, Nickel | $230 – $460 | Sweden | website |
Tekna | Titanium, Stainless Steel | $200 – $400 | Canada | website |
Erasteel | Tungsten, Tool Steel | $240 – $470 | France | website |
Advantages and Disadvantages of Metal Powders in DAPS
Metal Powder Type | Advantages | Disadvantages |
---|---|---|
Titanium Alloy | High strength-to-weight ratio, corrosion resistance | High cost, challenging to process |
Stainless Steel | Excellent corrosion resistance, durability | Higher density, more difficult to machine |
Aluminum Alloy | Lightweight, good thermal conductivity | Lower strength compared to some alloys |
Nickel Alloy | High temperature resistance, good mechanical properties | Expensive, limited availability |
Cobalt-Chrome | Biocompatibility, wear resistance | High cost, challenging to process |
Copper Alloy | High electrical and thermal conductivity | High density, susceptibility to oxidation |
Tool Steel | High hardness, wear resistance | Higher cost, more difficult to machine |
Tungsten | High density, high melting point | Very high cost, challenging to process |
Bronze | Good wear properties, low friction | Lower strength compared to some metals |
Magnesium Alloy | Lightweight, good strength-to-weight ratio | Flammability, lower corrosion resistance |
Characteristics of Divergent Adaptive Production System (DAPS)
Adaptability
One of the standout features of DAPS is its adaptability. Imagine a factory floor that’s more like a living organism than a static assembly line. It can adjust its operations in response to real-time data, much like how a chameleon changes its color to blend into different environments. This flexibility means that whether you’re producing aerospace components one day or automotive parts the next, DAPS can seamlessly switch gears.
Efficiency
Efficiency is the name of the game with DAPS. Traditional manufacturing systems can be wasteful, often running at full tilt even when it’s not necessary. DAPS, on the other hand, is like a smart thermostat for your production line, optimizing energy use and material consumption based on current needs. This not only reduces costs but also minimizes environmental impact, making it a win-win.
Scalability
Scalability is another feather in DAPS’s cap. Whether you’re a startup with a small production run or an established manufacturer with large-scale operations, DAPS can scale up or down accordingly. It’s like having a manufacturing system with a volume knob, allowing you to dial up or down the production output without sacrificing efficiency or quality.
Composition of Divergent Adaptive Production System (DAPS)
The composition of DAPS involves a blend of advanced technologies and materials, each playing a crucial role in its overall functionality. Here’s a breakdown of the key components:
Technologies Integrated in DAPS
Technology | Function |
---|---|
Artificial Intelligence (AI) | Real-time decision making and process optimization |
Internet of Things (IoT) | Connecting machines and devices for seamless communication |
Big Data Analytics | Analyzing large sets of data to improve production efficiency |
Additive Manufacturing | Creating complex parts with precision and minimal waste |
Robotics | Automating repetitive tasks and enhancing precision |
Augmented Reality (AR) | Assisting with maintenance and training through immersive visuals |
Key Materials in DAPS
Material | Properties | Role in DAPS |
---|---|---|
Metal Powders | Various compositions and properties | Used in additive manufacturing processes |
Composite Materials | Lightweight, high strength | Structural components, reducing weight |
Smart Materials | Respond to environmental changes | Adaptive components in machinery |
Nanomaterials | Enhanced mechanical and electrical properties | Improving material performance |
High-Performance Polymers | Durability, flexibility | Insulation, protective casings |
Advantages of Divergent Adaptive Production System (DAPS)
Flexibility in Production
Imagine you’re a chef who can whip up any dish at a moment’s notice, regardless of the ingredients on hand. That’s the level of flexibility DAPS offers in production. It can adapt to different materials, designs, and production volumes without significant downtime or reconfiguration. This is particularly beneficial for industries that need to respond quickly to market changes or customized orders.
Cost Efficiency
DAPS is like a financial advisor who helps you make the most out of every dollar. By optimizing resource use and reducing waste, it significantly cuts down production costs. Additionally, the system’s ability to predict maintenance needs and prevent breakdowns can save a fortune in repair costs and lost production time.
Enhanced Product Quality
Quality is king in manufacturing, and DAPS reigns supreme in this domain. By continuously monitoring and adjusting the production process, it ensures that each product meets the highest quality standards. It’s like having a meticulous quality control inspector on duty 24/7, catching potential issues before they become problems.
Sustainability
In today’s eco-conscious world, sustainability isn’t just a buzzword; it’s a necessity. DAPS embraces this by incorporating eco-friendly practices and materials into its processes. It’s like having a green thumb in the manufacturing world, nurturing sustainable growth and reducing the carbon footprint.
Challenges and Limitations of Divergent Adaptive Production System (DAPS)
High Initial Costs
Implementing DAPS can be akin to buying a luxury car. The initial investment can be substantial, covering advanced machinery, software, and training. However, like a high-end vehicle, the long-term benefits and cost savings often justify the upfront expense.
Complexity
DAPS is a sophisticated system, and with sophistication comes complexity. Managing and maintaining such an advanced setup requires specialized knowledge and skills. It’s like piloting an advanced aircraft; you need to be well-trained and experienced to navigate it effectively.
Integration with Existing Systems
Integrating DAPS with existing production systems can be a bit like fitting a square peg into a round hole. Compatibility issues may arise, requiring significant modifications or upgrades to current systems. This process can be time-consuming and costly, but once completed, the benefits often outweigh the initial hurdles.
Comparison: DAPS vs. Traditional Manufacturing Systems
Parameter | DAPS | Traditional Manufacturing |
---|---|---|
Flexibility | High – Can adapt to various production needs | Low – Rigid and specific to certain products |
Efficiency | Optimized – Reduces waste and resource use | Moderate – Higher waste and resource consumption |
Scalability | High – Easily scalable up or down | Low – Fixed capacity |
Initial Cost | High – Significant upfront investment | Lower – Less expensive initial setup |
Maintenance | Predictive and preventive | Reactive and often unplanned |
Quality Control | Continuous and real-time | Periodic and post-production |
Sustainability | High – Eco-friendly practices integrated | Moderate – Traditional methods |
Adaptability | High – Responds to market changes quickly | Low – Slow to adapt |
Real-World Examples of DAPS in Action
Aerospace Industry
In the aerospace sector, DAPS has revolutionized the production of lightweight, high-strength components. For instance, companies like Boeing and Airbus have integrated DAPS to manufacture critical parts such as turbine blades and airframe components. This system’s ability to produce complex geometries with minimal waste has significantly reduced production costs and improved overall efficiency.
Automotive Industry
The automotive industry benefits greatly from DAPS, particularly in the production of custom and performance parts. Companies like Tesla and BMW use DAPS to manufacture components with precise specifications, enhancing vehicle performance and reducing weight. The flexibility of DAPS allows these companies to quickly adapt to new designs and materials, keeping them ahead of the competition.
Medical Field
In the medical field, DAPS is used to produce customized implants and prosthetics. Companies such as Stryker and Zimmer Biomet have adopted DAPS to create patient-specific implants that offer better fit and function. The biocompatibility of the materials used, combined with the precision of additive manufacturing, results in higher success rates and improved patient outcomes.
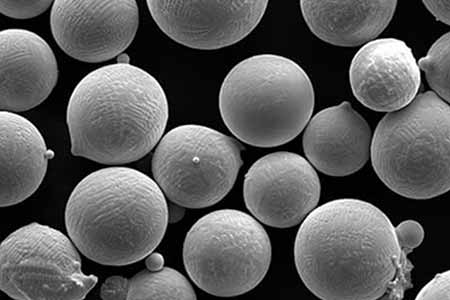
FAQ
Question | Answer |
---|---|
What is DAPS? | DAPS stands for Divergent Adaptive Production System, a flexible and efficient manufacturing approach. |
How does DAPS improve production efficiency? | By using real-time data to optimize resource use and minimize waste. |
What industries can benefit from DAPS? | Aerospace, automotive, medical, industrial equipment, and more. |
What are the initial costs of implementing DAPS? | The initial investment can be high, covering advanced machinery, software, and training. |
How does DAPS enhance product quality? | Through continuous monitoring and adjustments during the production process. |
Is DAPS sustainable? | Yes, it incorporates eco-friendly practices and materials to reduce environmental impact. |
What are the key technologies used in DAPS? | AI, IoT, big data analytics, additive manufacturing, robotics, and augmented reality. |
How does DAPS compare to traditional manufacturing? | DAPS offers higher flexibility, efficiency, scalability, and sustainability compared to traditional methods. |
Can DAPS be integrated with existing systems? | Yes, but it may require significant modifications or upgrades to current systems. |
What are the challenges of implementing DAPS? | High initial costs, complexity, and integration with existing systems. |
Conclusion
The Divergent Adaptive Production System (DAPS) represents a significant leap forward in manufacturing technology. By combining adaptability, efficiency, and sustainability, DAPS offers a versatile solution for a wide range of industries. While the initial costs and complexity may pose challenges, the long-term benefits of improved product quality, cost savings, and environmental impact make DAPS a worthwhile investment. As technology continues to advance, DAPS will likely play an increasingly critical role in shaping the future of manufacturing.