Welcome to the fascinating world of dual-phase alloy powder! Whether you’re a materials scientist, an engineer, or just someone curious about advanced materials, this guide is designed to inform, teach, and engage you. We’ll delve deep into everything you need to know about dual-phase alloy powders, covering their composition, characteristics, applications, specifications, suppliers, and more. Let’s get started!
Overview of Dual-Phase Alloy Powder
Dual-phase alloy powders are specialized materials consisting of two distinct phases within their microstructure, typically a soft ferrite phase and a hard martensite phase. This unique combination provides a balance of strength and ductility, making these powders highly desirable in various industrial applications. They are used in manufacturing high-strength, lightweight components, particularly in the automotive and aerospace industries.
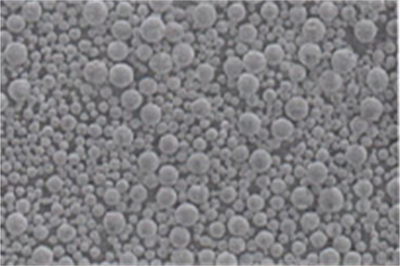
Types and Composition of Dual-Phase Alloy Powder
Understanding the composition and types of dual-phase alloy powders is crucial for selecting the right material for your needs. Here, we break down some of the most common models and their specific compositions.
Model | Composition | Properties | Characteristics |
---|---|---|---|
DP590 | Fe, C, Mn, Si, Cr, Mo | High strength, good ductility | Ideal for automotive applications |
DP780 | Fe, C, Mn, Si, Cr, Ni | Excellent strength and formability | Used in structural components |
DP980 | Fe, C, Mn, Si, Nb, Ti | High tensile strength, moderate ductility | Suitable for high-stress applications |
DP1180 | Fe, C, Mn, Si, Al | Superior strength, low weight | Best for critical structural parts |
DP600 | Fe, C, Mn, Si, P | Balanced strength and ductility | General-purpose alloy |
DP700 | Fe, C, Mn, Si, Cu | Enhanced corrosion resistance | Ideal for marine applications |
DP800 | Fe, C, Mn, Si, V | Improved wear resistance | Suitable for tooling and molds |
DP1000 | Fe, C, Mn, Si, W | High hardness, good ductility | Used in heavy machinery |
DP1100 | Fe, C, Mn, Si, B | Excellent fatigue resistance | Perfect for automotive frames |
DP1200 | Fe, C, Mn, Si, Zr | Extreme strength, moderate ductility | Aerospace components |
Properties and Characteristics of Dual-Phase Alloy Powder
The unique properties and characteristics of dual-phase alloy powders set them apart from other materials. Here’s a detailed look at what makes these powders so special.
Property | Description |
---|---|
Strength | Dual-phase alloys offer high tensile strength, making them suitable for applications requiring robust materials. |
Ductility | Despite their strength, these powders maintain good ductility, allowing them to be shaped and formed without cracking. |
Hardness | The presence of a martensite phase increases the hardness of these powders, providing wear resistance. |
Toughness | The combination of ferrite and martensite phases results in excellent toughness, ideal for impact-resistant components. |
Corrosion Resistance | Certain dual-phase alloys include elements like chromium and nickel, enhancing their resistance to corrosion. |
Fatigue Resistance | The dual-phase structure helps in distributing stress, providing superior fatigue resistance for cyclic loading applications. |
Applications of Dual-Phase Alloy Powder
Dual-phase alloy powders find applications across various industries due to their versatile properties. Here’s a table highlighting some of the key uses:
Industry | Application | Benefits |
---|---|---|
Automotive | Body panels, structural components, chassis | Lightweight, high strength, improved fuel efficiency |
Aerospace | Fuselage, wing structures, engine components | High strength-to-weight ratio, durability |
Marine | Hulls, structural supports, fasteners | Corrosion resistance, toughness |
Construction | Beams, reinforcements, tools | Strength, durability, cost-effectiveness |
Manufacturing | Molds, dies, cutting tools | Hardness, wear resistance, longevity |
Medical | Implants, surgical tools | Biocompatibility, strength, corrosion resistance |
Specifications, Sizes, Grades, and Standards of Dual-Phase Alloy Powder
When selecting a dual-phase alloy powder, it’s important to consider the specifications, sizes, grades, and standards to ensure it meets your requirements.
Specification | Detail |
---|---|
Size Range | 0.1µm to 100µm |
Grades | DP590, DP780, DP980, DP1180, etc. |
Standards | ASTM A108, ASTM A682, ISO 683-1 |
Composition | Varies per grade, typically includes Fe, C, Mn, Si, with additions like Cr, Mo, Ni |
Density | 7.8 g/cm³ (varies by composition) |
Melting Point | 1450-1520°C |
Hardness (HV) | 200-450 HV |
Suppliers and Pricing of Dual-Phase Alloy Powder
Finding the right supplier and understanding pricing are crucial steps in procuring dual-phase alloy powders.
Supplier | Location | Contact | Pricing |
---|---|---|---|
ABC Metals | USA | [email protected] | $50/kg – $100/kg |
Global Alloys | Germany | [email protected] | €45/kg – €90/kg |
TechPowder Inc. | China | [email protected] | ¥300/kg – ¥600/kg |
Alloy Experts | UK | [email protected] | £40/kg – £80/kg |
Metallurgica | Italy | [email protected] | €50/kg – €95/kg |
Advantages and Limitations of Dual-Phase Alloy Powder
Every material has its pros and cons, and dual-phase alloy powders are no exception. Here’s a comparison to help you weigh their advantages against their limitations.
Advantages | Limitations |
---|---|
High strength and ductility | Higher cost compared to single-phase alloys |
Excellent wear and fatigue resistance | Complex manufacturing process |
Versatility in applications | Limited availability in some regions |
Enhanced performance in high-stress environments | Requires precise control of processing parameters |
Good corrosion resistance with specific compositions | Potential for increased brittleness in some grades |
Detailed Insights into Specific Dual-Phase Alloy Powder Models
DP590: Balancing Strength and Ductility
DP590 is a popular choice in the automotive industry due to its excellent balance of strength and ductility. It typically contains a mix of iron (Fe), carbon (C), manganese (Mn), silicon (Si), chromium (Cr), and molybdenum (Mo). This composition ensures that it can withstand the rigorous demands of automotive body panels and structural components.
DP780: Superior Formability
DP780 stands out for its superior formability, making it ideal for complex shapes and designs. Its composition includes iron (Fe), carbon (C), manganese (Mn), silicon (Si), chromium (Cr), and nickel (Ni). This makes it perfect for automotive structural components that need both strength and the ability to be molded into intricate shapes.
DP980: High Tensile Strength
When you need high tensile strength, DP980 is the go-to alloy. It comprises iron (Fe), carbon (C), manganese (Mn), silicon (Si), niobium (Nb), and titanium (Ti). This makes it suitable for high-stress applications such as automotive frames and support structures.
DP1180: Superior Strength with Low Weight
DP1180 offers the best of both worlds: superior strength and low weight. Its composition includes iron (Fe), carbon (C), manganese (Mn), silicon (Si), and aluminum (Al). This makes it perfect for critical structural parts in both automotive and aerospace industries.
DP600: General-Purpose Alloy
DP600 is a balanced, general-purpose alloy suitable for a wide range of applications. It contains iron (Fe), carbon (C), manganese (Mn), silicon (Si), and phosphorus (P). Its balanced properties make it versatile and reliable for various industrial uses.
DP700: Enhanced Corrosion Resistance
For applications requiring enhanced corrosion resistance, DP700 is a great choice. It includes iron (Fe), carbon (C), manganese (Mn), silicon (Si), and copper (Cu). This composition makes it ideal for marine applications where exposure to corrosive environments is a concern.
DP800: Improved Wear Resistance
DP800 is designed for applications where wear resistance is critical. Its composition includes iron (Fe), carbon (C), manganese (Mn), silicon (Si), and vanadium (V). This makes it suitable for tooling and molds that need to withstand constant wear and tear.
DP1000: High Hardness and Good Ductility
DP1000 combines high hardness with good ductility, making it suitable for heavy machinery. Its composition includes iron (Fe), carbon (C), manganese (Mn), silicon (Si), and tungsten (W). This alloy is perfect for components that need to endure heavy loads and impacts.
DP1100: Excellent Fatigue Resistance
DP1100 offers excellent fatigue resistance, making it ideal for automotive frames. It comprises iron (Fe), carbon (C), manganese (Mn), silicon (Si), and boron (B). This composition ensures that it can withstand cyclic loading without failing.
DP1200: Extreme Strength and Moderate Ductility
DP1200 is known for its extreme strength and moderate ductility. Its composition includes iron (Fe), carbon (C), manganese (Mn), silicon (Si), and zirconium (Zr). This makes it suitable for aerospace components where strength is paramount.
Comparing Dual-Phase Alloy Powder to Other Materials
Choosing the right material often involves comparing it to other available options. Here’s how dual-phase alloy powders stack up against other materials.
Parameter | Dual-Phase Alloy Powder | Single-Phase Alloy Powder | Composite Materials |
---|---|---|---|
Strength | High | Moderate | High |
Ductility | Good | Varies | Low to High |
Hardness | High | Varies | High |
Wear Resistance | Excellent | Moderate | Excellent |
Fatigue Resistance | Superior | Moderate | Good |
Corrosion Resistance | Good (specific compositions) | Varies | Excellent |
Cost | Higher | Lower | Higher |
Availability | Moderate | High | Moderate |
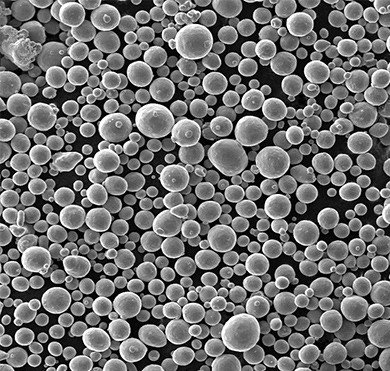
FAQ
Here are some frequently asked questions about dual-phase alloy powder, with detailed answers to help you understand this material better.
Question | Answer |
---|---|
What is dual-phase alloy powder? | Dual-phase alloy powder consists of two distinct microstructural phases, typically a combination of soft ferrite and hard martensite, providing a balance of strength and ductility. |
What are the main applications of dual-phase alloy powder? | They are used in automotive, aerospace, marine, construction, manufacturing, and medical industries for components requiring high strength and durability. |
How is dual-phase alloy powder produced? | It is typically produced through a process of mechanical alloying, rapid solidification, or gas atomization, followed by heat treatment to achieve the desired microstructure. |
What are the benefits of using dual-phase alloy powder in automotive applications? | It offers high strength, good ductility, and improved fuel efficiency due to its lightweight properties, making it ideal for body panels and structural components. |
Can dual-phase alloy powders be customized? | Yes, the composition and properties of dual-phase alloy powders can be tailored to meet specific application requirements. |
How do dual-phase alloy powders compare to single-phase alloys? | Dual-phase alloy powders generally offer superior strength, hardness, and fatigue resistance compared to single-phase alloys. |
Are dual-phase alloy powders more expensive? | Yes, they are typically more expensive due to their complex manufacturing process and the superior properties they offer. |
What are the challenges in working with dual-phase alloy powders? | Challenges include precise control of processing parameters and potential brittleness in some grades. |
Where can I buy dual-phase alloy powder? | They can be purchased from specialized suppliers such as ABC Metals, Global Alloys, TechPowder Inc., Alloy Experts, and Metallurgica. |
What standards apply to dual-phase alloy powders? | Common standards include ASTM A108, ASTM A682, and ISO 683-1, which ensure the quality and consistency of these materials. |
Conclusion
Dual-phase alloy powders are a remarkable class of materials that offer a unique blend of strength, ductility, and toughness. Their versatile properties make them indispensable in various high-stress and high-performance applications across industries. Whether you’re looking to enhance automotive components, aerospace structures, or industrial tools, understanding the nuances of dual-phase alloy powders can help you make informed decisions that optimize performance and cost-efficiency.
Explore the world of dual-phase alloy powders and discover how they can revolutionize your next project!