Overview of Electrode Induction Melting Inert Gas Atomisation (EIGA)
Electrode Induction Melting Inert Gas Atomisation, or EIGA, is a state-of-the-art process for producing high-quality metal powders used in various industries, including aerospace, automotive, and medical applications. This process combines two major technologies: electrode induction melting and inert gas atomisation, resulting in fine, uniform metal powders with excellent properties.
The EIGA process involves melting a metal electrode using induction heating and then atomizing the molten metal with an inert gas, such as argon or nitrogen, to produce fine powder particles. This method is particularly effective for producing powders of reactive metals and alloys, such as titanium, aluminum, and their various blends, without contamination from the surrounding environment.
Benefits of EIGA:
- Purity: The inert gas environment minimizes contamination.
- Uniformity: Produces consistent particle sizes.
- Versatility: Suitable for a wide range of metals and alloys.
- Efficiency: High yield with minimal waste.
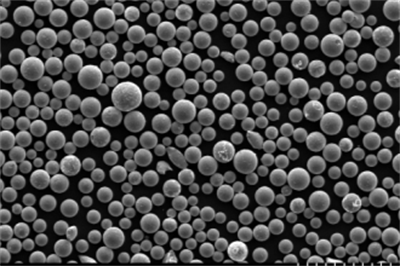
Types and Compositions of EIGA Metal Powders
Understanding the types and compositions of metal powders produced by EIGA is crucial for selecting the right material for specific applications. Here’s a detailed table presenting various types of metal powders, their compositions, and their unique properties.
Metal Powder Model | Composition | Properties | Applications |
---|---|---|---|
Ti-6Al-4V | 90% Titanium, 6% Aluminum, 4% Vanadium | High strength, lightweight, corrosion-resistant | Aerospace, biomedical implants |
Inconel 718 | Nickel, Chromium, Iron, Niobium, Molybdenum | High-temperature strength, oxidation resistance | Gas turbines, jet engines |
316L Stainless Steel | Iron, Chromium, Nickel, Molybdenum | Corrosion resistance, good weldability | Medical devices, marine applications |
AlSi10Mg | Aluminum, Silicon, Magnesium | High strength-to-weight ratio, good casting properties | Automotive, aerospace components |
CoCrMo | Cobalt, Chromium, Molybdenum | High wear resistance, biocompatibility | Dental and orthopedic implants |
Ti-15Mo | 85% Titanium, 15% Molybdenum | High corrosion resistance, excellent biocompatibility | Biomedical implants |
Maraging Steel | Nickel, Cobalt, Molybdenum, Titanium | Ultra-high strength, good ductility | Aerospace, tooling, high-stress components |
NiTi (Nitinol) | Nickel, Titanium | Shape memory, superelasticity | Medical devices, actuators, sensors |
CuCrZr | Copper, Chromium, Zirconium | High electrical conductivity, good thermal properties | Electrical contacts, heat exchangers |
Hastelloy X | Nickel, Chromium, Iron, Molybdenum | Excellent oxidation resistance, high-temperature strength | Chemical processing, gas turbines |
Characteristics of Electrode Induction Melting Inert Gas Atomisation
The EIGA process boasts several key characteristics that make it a preferred method for metal powder production:
1. High Purity:
The use of an inert gas environment significantly reduces the risk of contamination from oxygen, nitrogen, or other atmospheric gases. This ensures that the powders produced are of the highest purity, which is essential for critical applications like aerospace and medical devices.
2. Uniform Particle Size Distribution:
EIGA produces powders with a narrow particle size distribution. This uniformity is crucial for consistent performance in applications such as additive manufacturing and powder metallurgy.
3. Versatility:
EIGA is capable of processing a wide range of metals and alloys, including those that are reactive or have high melting points. This versatility makes it an ideal choice for producing powders of materials that are difficult to process using other methods.
4. Efficiency and Yield:
The process is highly efficient, with a high yield of usable powder and minimal waste. This efficiency translates to cost savings and more sustainable production practices.
Applications of EIGA Metal Powders
EIGA-produced metal powders find applications across various high-tech industries. Here’s a detailed table showing the primary uses for each type of metal powder.
Metal Powder Model | Applications |
---|---|
Ti-6Al-4V | Aerospace components, orthopedic implants, 3D printing |
Inconel 718 | Jet engines, gas turbines, high-temperature fasteners |
316L Stainless Steel | Medical instruments, marine components, food processing equipment |
AlSi10Mg | Lightweight automotive parts, aerospace structures |
CoCrMo | Dental implants, orthopedic prosthetics, cutting tools |
Ti-15Mo | Surgical implants, dental devices, chemical processing equipment |
Maraging Steel | High-strength tooling, aerospace structural components |
NiTi (Nitinol) | Stents, guidewires, actuators, sensors |
CuCrZr | Electrical conductors, heat sinks, welding electrodes |
Hastelloy X | Chemical reactors, gas turbine components, industrial furnaces |
Specifications and Standards of EIGA Metal Powders
Ensuring the quality and consistency of metal powders is paramount, which is why specific standards and specifications are adhered to in the production process. Here is a detailed table showing the specifications, sizes, grades, and standards for various EIGA metal powders.
Metal Powder Model | Specifications | Sizes (µm) | Grades | Standards |
---|---|---|---|---|
Ti-6Al-4V | ASTM F2924, ISO 5832-3 | 15-45, 45-105 | Grade 5 | ASTM, ISO |
Inconel 718 | AMS 5662, ASTM B637 | 15-45, 45-105 | UNS N07718 | AMS, ASTM |
316L Stainless Steel | ASTM F138, ISO 5832-1 | 15-45, 45-105 | Grade 316L | ASTM, ISO |
AlSi10Mg | EN AC-43000, ASTM B918 | 15-45, 45-105 | Grade 10Mg | EN, ASTM |
CoCrMo | ASTM F75, ISO 5832-4 | 15-45, 45-105 | Grade Co28 | ASTM, ISO |
Ti-15Mo | ASTM F2066, ISO 5832-10 | 15-45, 45-105 | Grade Ti15 | ASTM, ISO |
Maraging Steel | AMS 6514, ASTM A538 | 15-45, 45-105 | Grade 300 | AMS, ASTM |
NiTi (Nitinol) | ASTM F2063, ISO 5832-7 | 15-45, 45-105 | Grade Ni50 | ASTM, ISO |
CuCrZr | EN 12163, ASTM B224 | 15-45, 45-105 | Grade CuCr | EN, ASTM |
Hastelloy X | ASTM B435, AMS 5536 | 15-45, 45-105 | UNS N06002 | ASTM, AMS |
Suppliers and Pricing Details for EIGA Metal Powders
The market for EIGA-produced metal powders is highly competitive, with numerous suppliers offering a range of products. Here’s a table summarizing some of the key suppliers and their pricing details.
Supplier | Metal Powder Model | Price (per kg) | Region | Contact Details |
---|---|---|---|---|
AP&C | Ti-6Al-4V | $300 | North America | [email protected] |
GKN Hoeganaes | Inconel 718 | $250 | Europe | [email protected] |
Carpenter Additive | 316L Stainless Steel | $150 | Global | [email protected] |
Höganäs | AlSi10Mg | $100 | Global | [email protected] |
Sandvik Osprey | CoCrMo | $350 | Europe | [email protected] |
Arcam EBM | Ti-15Mo | $400 | Global | [email protected] |
AMETEK Specialty | Maraging Steel | $200 | North America | [email protected] |
ATI Specialty Alloys | NiTi (Nitinol) | $500 | Global | [email protected] |
AMG Advanced Metallurgical | CuCrZr | $120 | Europe | [email protected] |
VSMPO-AVISMA | Hastelloy X | $300 | Russia | [email protected] |
Advantages and Limitations of EIGA Metal Powders
Every manufacturing process has its strengths and weaknesses. Here’s a comparison of the advantages and limitations of the EIGA process:
Advantages:
- High Purity:
- Minimal contamination.
- Essential for high-performance applications.
- Uniformity:
- Consistent particle sizes.
- Better performance in applications.
- Versatility:
- Wide range of metals and alloys.
- Suitable for reactive materials.
- Efficiency:
- High yield.
- Cost-effective production.
Limitations:
- Cost:
- Expensive initial setup.
- High operational costs due to inert gas usage.
- Complexity:
- Requires sophisticated equipment.
- Skilled operators needed.
- Material Limitations:
- Not suitable for very low melting point metals.
- Certain alloys might be challenging to process.
Comparing EIGA Metal Powders
When choosing between different metal powders, it’s important to compare their properties and applications. Here’s a detailed comparison of various EIGA metal powders:
Metal Powder Model | Advantages | Limitations |
---|---|---|
Ti-6Al-4V | High strength-to-weight ratio, corrosion-resistant | Expensive, challenging to process |
Inconel 718 | High-temperature strength, oxidation resistance | High cost, difficult to machine |
316L Stainless Steel | Corrosion-resistant, biocompatible | Lower strength compared to other alloys |
AlSi10Mg | Lightweight, good casting properties | Lower strength than other aluminum alloys |
CoCrMo | High wear resistance, biocompatibility | High cost, difficult to machine |
Ti-15Mo | Excellent biocompatibility, corrosion-resistant | Expensive, limited availability |
Maraging Steel | Ultra-high strength, good ductility | Expensive, requires heat treatment |
NiTi (Nitinol) | Shape memory, superelasticity | High cost, difficult to process |
CuCrZr | High electrical and thermal conductivity | Lower strength compared to other alloys |
Hastelloy X | Excellent oxidation resistance, high-temperature strength | Expensive, limited machinability |
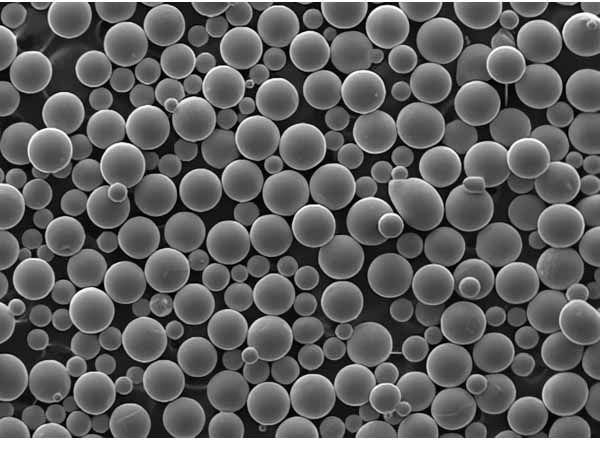
FAQ
To address common questions about EIGA, here’s a detailed FAQ section:
Question | Answer |
---|---|
What is EIGA? | EIGA stands for Electrode Induction Melting Inert Gas Atomisation, a process for producing high-quality metal powders. |
Which metals can be processed using EIGA? | EIGA can process a wide range of metals and alloys, including titanium, aluminum, stainless steel, and superalloys. |
What are the benefits of EIGA? | High purity, uniform particle size, versatility, and efficiency. |
What industries use EIGA metal powders? | Aerospace, automotive, medical, dental, and electronics industries. |
How does EIGA ensure high purity? | By using an inert gas environment, which minimizes contamination from atmospheric gases. |
Why is uniform particle size important? | It ensures consistent performance in applications such as additive manufacturing and powder metallurgy. |
What are the limitations of EIGA? | High initial setup and operational costs, complexity, and material limitations for certain alloys. |
Can EIGA produce powders for additive manufacturing? | Yes, EIGA-produced powders are widely used in additive manufacturing due to their high quality and consistency. |
How does EIGA compare to other powder production methods? | EIGA offers higher purity and better control over particle size but at a higher cost and complexity. |
Where can I buy EIGA metal powders? | Various suppliers such as AP&C, GKN Hoeganaes, and Carpenter Additive offer EIGA metal powders. |
In conclusion, Electrode Induction Melting Inert Gas Atomisation (EIGA) is a cutting-edge process that plays a crucial role in producing high-quality metal powders for various advanced applications. By understanding the types, compositions, and applications of EIGA metal powders, as well as their advantages and limitations, one can make informed decisions about their use in different industries.