Overview of Electrode Inert Gas Atomisers
When it comes to producing high-quality metal powders, few techniques stand out as much as Electrode Inert Gas Atomisation (EIGA). This process, which involves the use of inert gases like argon, nitrogen, or helium, allows for the creation of metal powders with precise characteristics tailored for various industrial applications. But what exactly are these atomisers, and how do they work? More importantly, why should you care?
Whether you’re a material scientist, an engineer, or someone dipping their toes into the world of metallurgy, this guide will walk you through everything you need to know about Electrode Inert Gas Atomisers, from their fundamental principles to the specific metal powders they produce.
What Are Electrode Inert Gas Atomisers?
Electrode Inert Gas Atomisers are specialized devices used to produce metal powders through the atomisation process. This involves the melting of a metal or alloy using an electric arc, followed by the disintegration of the molten material into fine droplets by a high-pressure inert gas. The droplets then solidify into powder particles, which can be collected and used for various applications, including 3D printing, additive manufacturing, and metal injection molding.
How Do They Work?
In an EIGA system, the metal electrode serves as the source of material. The electrode is heated and melted by an electric arc in a chamber filled with an inert gas, which prevents oxidation. The high-pressure inert gas stream breaks the molten metal into tiny droplets. These droplets rapidly cool and solidify into fine powder particles, which are then collected for further use.
The process might sound simple on paper, but it’s the nuances that make EIGA a preferred method for high-quality metal powder production. For instance, the use of inert gas minimizes contamination, ensuring the purity of the metal powder. Additionally, the size and distribution of the powder particles can be controlled by adjusting parameters like gas pressure, electrode material, and arc intensity.
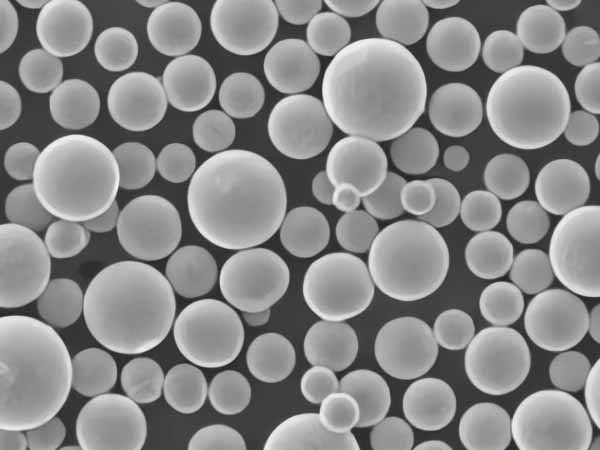
Types of Metal Powders Produced by Electrode Inert Gas Atomisers
One of the significant advantages of Electrode Inert Gas Atomisers is their versatility in producing a wide range of metal powders. Here’s a breakdown of some specific models and their characteristics:
Metal Powder Model | Composition | Characteristics | Applications |
---|---|---|---|
Ti-6Al-4V | Titanium, 6% Aluminium, 4% Vanadium | High strength, low density, excellent corrosion resistance | Aerospace components, biomedical implants |
Inconel 718 | Nickel-based superalloy | High-temperature resistance, excellent mechanical properties | Turbine blades, rocket engines, 3D printing |
316L Stainless Steel | Chromium, Nickel, Molybdenum | Corrosion resistance, good weldability, and machinability | Medical instruments, food processing equipment, additive manufacturing |
AlSi10Mg | Aluminium, 10% Silicon, Magnesium | Lightweight, good thermal conductivity, excellent castability | Automotive parts, aerospace, heat exchangers |
CuCrZr | Copper, Chromium, Zirconium | High electrical and thermal conductivity, excellent strength at elevated temperatures | Electrical components, heat sinks |
H13 Tool Steel | Chromium, Molybdenum, Vanadium | High toughness, resistance to thermal fatigue, and wear resistance | Molds, dies, tooling for plastic injection |
NiCrMo Alloy | Nickel, Chromium, Molybdenum | Outstanding resistance to oxidation and corrosion, high strength at elevated temperatures | Chemical processing equipment, marine engineering |
CoCrMo Alloy | Cobalt, Chromium, Molybdenum | Biocompatible, wear-resistant, high strength | Orthopedic implants, dental prosthetics |
7075 Aluminium Alloy | Aluminium, Zinc, Magnesium | High strength-to-weight ratio, good fatigue resistance | Aircraft structures, sports equipment |
Maraging Steel | Iron, Nickel, Cobalt, Molybdenum | Ultra-high strength, good toughness, excellent machinability | Aerospace, tooling, high-performance sports equipment |
Composition of Electrode Inert Gas Atomisers
The composition of the metal powders produced by EIGA depends on the electrode material and the inert gas used during atomisation. Let’s explore the specifics:
Element | Common Electrode Materials | Role in Metal Powder |
---|---|---|
Titanium (Ti) | Ti-6Al-4V | Provides high strength, low density, and excellent corrosion resistance |
Nickel (Ni) | Inconel 718, NiCrMo Alloy | Contributes to high-temperature resistance and excellent mechanical properties |
Aluminium (Al) | AlSi10Mg, 7075 Aluminium | Offers lightweight properties and good thermal conductivity |
Chromium (Cr) | 316L Stainless Steel, CoCrMo Alloy | Enhances corrosion resistance and mechanical strength |
Cobalt (Co) | CoCrMo Alloy, Maraging Steel | Adds to the wear resistance and biocompatibility in medical applications |
Molybdenum (Mo) | 316L Stainless Steel, H13 Tool Steel | Increases strength, hardness, and resistance to corrosion |
Vanadium (V) | Ti-6Al-4V | Improves the strength-to-weight ratio and contributes to overall durability |
Zinc (Zn) | 7075 Aluminium Alloy | Enhances strength, particularly in alloys used in high-stress applications |
Copper (Cu) | CuCrZr | Offers high electrical and thermal conductivity, essential for electronics and heat management |
Zirconium (Zr) | CuCrZr | Contributes to high-temperature strength and stability, particularly in copper alloys |
Characteristics of Electrode Inert Gas Atomisers
The characteristics of the metal powders produced by EIGA are crucial for their performance in various applications. These characteristics include:
- Particle Size Distribution: EIGA allows for precise control over particle size, typically ranging from 5 to 150 microns. This is critical for applications like additive manufacturing, where consistency in particle size ensures smooth printing and optimal mechanical properties.
- Sphericity: The inert gas atomisation process tends to produce spherical particles, which are preferred in powder metallurgy due to their flowability and packing density.
- Purity: The use of an inert gas environment minimizes contamination, resulting in powders with high purity levels, essential for aerospace and biomedical applications.
- Morphology: EIGA powders exhibit uniform morphology, which is vital for consistent performance in end-use applications.
- Density: The density of the powders can be tailored through process parameters, influencing the final product’s mechanical properties.
Applications of Metal Powders from Electrode Inert Gas Atomisers
Metal powders produced via EIGA find applications across numerous industries, thanks to their unique properties. Here’s a look at some of the primary applications:
Industry | Specific Uses | Benefits of EIGA Powders |
---|---|---|
Aerospace | Turbine blades, structural components | High strength-to-weight ratio, excellent thermal resistance |
Biomedical | Implants, prosthetics, dental applications | Biocompatibility, corrosion resistance, tailored mechanical properties |
Automotive | Engine parts, lightweight components | Reduced weight, improved fuel efficiency, and enhanced performance |
Electronics | Conductive inks, connectors, heat sinks | High electrical and thermal conductivity, precise control over particle size |
Additive Manufacturing | 3D printing, prototyping, custom parts | High sphericity, consistent particle size, and tailored material properties |
Tooling | Molds, dies, cutting tools | High wear resistance, toughness, and thermal fatigue resistance |
Energy | Battery components, fuel cells | Improved energy density, tailored electrochemical properties |
Chemical Processing | Corrosion-resistant equipment | Enhanced resistance to corrosive environments, high-temperature stability |
Marine Engineering | Propulsion systems, structural components | Resistance to seawater corrosion, high strength at low temperatures |
Sports Equipment | Lightweight, high-performance gear | High strength-to-weight ratio, excellent durability |
Specifications, Sizes, Grades, and Standards of Metal Powders from Electrode Inert Gas Atomisers
Understanding the specifications, sizes, and standards of metal powders is crucial for selecting the right material for your application. Here’s a detailed table:
Metal Powder | Typical Particle Size (Microns) | Grade | Standards | Size Range |
---|---|---|---|---|
Ti-6Al-4V | 15-45 | Grade 23 | ASTM F2924, ISO 5832-3 | 10-150 |
Inconel 718 | 10-50 | AMS 5662 | ASTM B637, ASTM F3055 | 5-100 |
316L Stainless Steel | 20-60 | UNS S31603 | ASTM A240, ASTM B476 | 10-120 |
AlSi10Mg | 15-50 | AA 319.0 | ASTM B917 | 10-100 |
CuCrZr | 20-45 | C17400 | ASTM B193, ASTM B570 | 5-80 |
H13 Tool Steel | 10-40 | H13 | ASTM A681 | 5-75 |
NiCrMo Alloy | 10-50 | Alloy 80 | ASTM B333 | 10-100 |
CoCrMo Alloy | 15-60 | ASTM F75 | ASTM F75, ISO 5832-12 | 15-90 |
7075 Aluminium Alloy | 20-50 | 7075-T6 | ASTM B211 | 10-100 |
Maraging Steel | 15-45 | Maraging 250 | AMS 6514, ASTM A564 | 10-80 |
Suppliers and Pricing Details for Electrode Inert Gas Atomisers
Choosing a supplier for metal powders can be as crucial as selecting the right material. Here’s a table with some notable suppliers and a rough estimate of pricing for different types of metal powders. Pricing can vary based on quantity, purity, and specific requirements.
Supplier | Metal Powder Types | Pricing (per kg) | Website | Contact Information |
---|---|---|---|---|
Advanced Powders & Coatings | Ti-6Al-4V, Inconel 718, 316L Stainless Steel | $300-$600 | apcinc.com | [email protected] |
Arcam EBM | AlSi10Mg, 7075 Aluminium Alloy | $250-$550 | arcam.com | [email protected] |
LPW Technology | CuCrZr, H13 Tool Steel | $400-$700 | lpwtechnology.com | [email protected] |
Saint-Gobain | NiCrMo Alloy, CoCrMo Alloy | $350-$650 | saint-gobain.com | [email protected] |
Carpenter Technology | Maraging Steel, Inconel 718 | $500-$800 | cartech.com | [email protected] |
Note: Prices are approximate and can vary based on the order volume and specific requirements. It’s always best to contact suppliers directly for the most accurate and up-to-date pricing.
Pros and Cons of Electrode Inert Gas Atomisers
Understanding the strengths and limitations of Electrode Inert Gas Atomisers is essential for evaluating their suitability for different applications. Here’s a detailed comparison:
Aspect | Pros | Cons |
---|---|---|
Purity | Produces high-purity metal powders due to inert gas environment | High-purity requirement may result in higher costs and complexity |
Particle Size Control | Excellent control over particle size and distribution | Fine-tuning the process to achieve specific particle sizes can be challenging |
Material Versatility | Capable of producing a wide range of metal powders, including high-performance alloys | Some metals may be challenging to process or require specialized equipment |
Particle Shape | Typically produces spherical particles, which are ideal for many applications | Non-spherical particles may occasionally be produced, affecting flowability |
Cost | Provides high-quality powder with minimal contamination | Can be more expensive compared to other atomisation methods |
Environmental Impact | Inert gas reduces contamination and waste | Inert gas usage can be costly and requires careful handling |
Advantages of Electrode Inert Gas Atomisers
- High Purity: The inert gas environment significantly reduces the risk of contamination, ensuring high purity of the final metal powders.
- Versatility: Capable of processing a wide variety of metals and alloys, making it suitable for many industrial applications.
- Spherical Particles: Produces spherical powder particles, which are desirable for applications requiring good flowability and packing density.
- Control Over Particle Size: Provides precise control over the particle size distribution, crucial for advanced manufacturing processes.
Limitations of Electrode Inert Gas Atomisers
- Cost: The initial setup and operational costs can be higher compared to other powder production methods.
- Complexity: Requires specialized equipment and expertise, which can be a barrier for smaller operations.
- Gas Consumption: The consumption of inert gases can be significant, adding to operational expenses and environmental considerations.
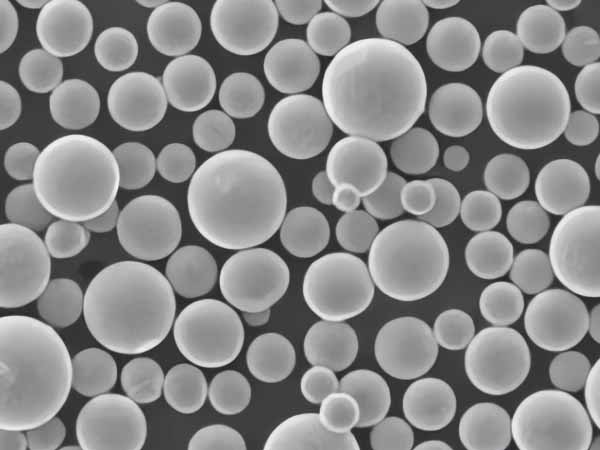
FAQ
Here are some common questions and answers about Electrode Inert Gas Atomisers:
Question | Answer |
---|---|
What metals can be atomised using EIGA? | EIGA can atomise a wide range of metals including titanium, nickel-based alloys, stainless steel, and aluminium alloys. |
How does EIGA compare to other atomisation methods? | EIGA generally offers higher purity and better control over particle size compared to methods like water atomisation. However, it can be more costly. |
What are the typical applications of EIGA powders? | EIGA powders are used in aerospace, biomedical, automotive, electronics, and many other industries where high-quality metal powders are required. |
Can EIGA be used for producing metal powders for 3D printing? | Yes, EIGA is well-suited for producing metal powders used in additive manufacturing and 3D printing due to its ability to produce uniform and spherical particles. |
What are the safety considerations when using EIGA? | Proper handling and management of inert gases are crucial to ensure safety. Additionally, equipment must be maintained and operated according to safety standards. |
Conclusion
Electrode Inert Gas Atomisers represent a sophisticated and versatile technology for producing high-quality metal powders. With their ability to control particle size, maintain purity, and produce spherical particles, EIGA systems are invaluable in many advanced manufacturing processes. However, the higher costs and complexity associated with this technology must be considered.
Whether you’re involved in aerospace, biomedical applications, or any industry that requires high-performance metal powders, understanding the capabilities and limitations of EIGA can help you make informed decisions about your material choices.
For those looking to dive deeper into the world of metal powders and atomisation techniques, exploring various suppliers and understanding the specific needs of your applications will be crucial. With the right knowledge and resources, you can leverage the benefits of EIGA to drive innovation and excellence in your field.