Electrode powders refer to specialty metal, alloy and composite powders used as feedstock materials in the manufacturing of welding electrodes and thermal spray consumables. Powder characteristics play a critical role in determining metallurgical, mechanical and processing performance of coatings, fills and interfaces during welding, surfacing, cladding, PTA and related high temperature processes.
Types of Electrode Powders
Key powder categories used in electrodes include:
Type | Description | Common Constituents |
---|---|---|
Base powders | Provides bulk of deposited weld metal composition | Iron, nickel, cobalt, copper alloys |
Matrix powders | Binder holding components together | Iron, nickel, cobalt, copper alloys with boron, silicon additives |
Alloying powders | Added to achieve target chemistry | Manganese, chromium, molybdenum, vanadium, niobium |
Flux powders | Promotes arc stability and wetting | Rutile, silicates, fluorides, oxides |
Composite powders | Reinforces deposit or imparts functionality | Hard phases like tungsten carbide, surface modulus agents |
Particle size distribution, shape, flow characteristics, layering tendency and reconstitution behavior during melting all significantly impact processing quality and consistency.
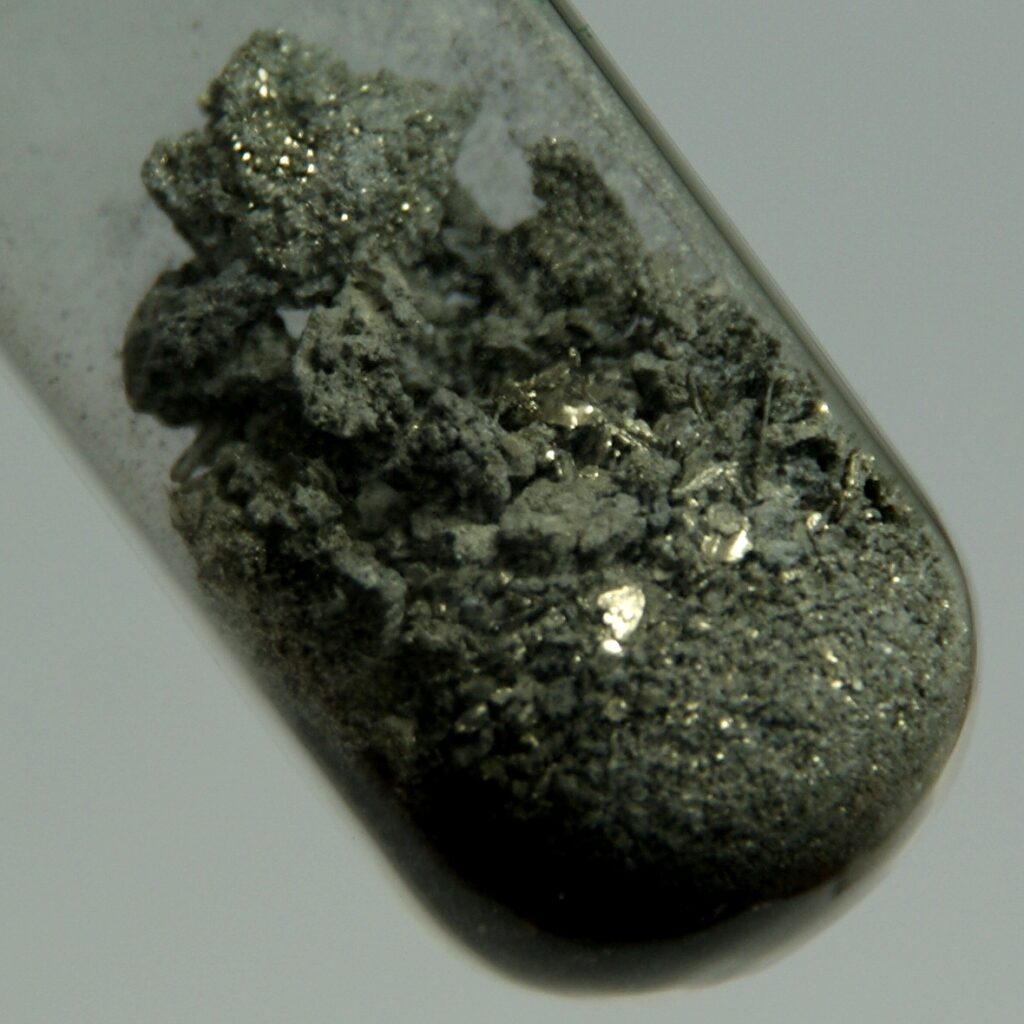
Electrode Powder Composition
Electrode powders contain complex compositions tailored to develop desired properties and performance in the molten and finished state.
Element | Key Functions |
---|---|
Iron | Base constituent in carbon steels and low alloys |
Nickel | Added for corrosion resistance, tensile strength |
Chromium | Primary alloying element for stainless steels, resistance to wear, heat and corrosion |
Molybdenum | Solid solution strengthener, supports high temperature hardness |
Manganese, Vanadium, Niobium, Titanium | Important microalloying elements to form carbides/nitrides for strengthening |
Silicon, Boron | Deoxidizers critical for sound welds |
Carbon | Fundamental constituent of steel composition that impacts strength, hardness and weldability |
Copper | Improves corrosion resistance in several alloy families |
Role of Alloying Elements
- Form beneficial precipitates to reinforce grain boundaries
- Develop multiple microstructural phases for improved mechanical properties
- Increase hardenability for better through-thickness properties
- Enable tempering resistance at high operating temperatures
- Resist damage through corrosive species like chlorides and sulfides
Advanced electrodes leverage complex metallurgical mechanisms like eutectic reactions to generate exceptional in-service performance.
Electrode Powder Properties
Property | Typical Values | Measurement Methods |
---|---|---|
Particle shape | Irregular, dendritic, crushed | Microscopy, SEM imaging |
Particle size distribution | 10 to 150 microns | Laser diffraction, sieving |
Apparent density | 2 to 6 g/cc | Hall flowmeter |
Tap density | 4 to 8 g/cc | ASTM B527 |
Flow rate | 20 to 50 s/50g | Hall flowmeter |
Loss on ignition | 1 to 10% | Thermogravimetric analysis |
Residual carbon | 0.1% max | Combustion infrared detection |
Residual oxygen | 1% max | Inert gas fusion analysis |
Spherical gas atomized electrode powders offer better flow and packing but reduced mechanical anchoring compared to irregular shapes. Specifications tailored for deposition process – wire vs. coating vs. thermal spray.
Electrode Powder Applications
Electrode powders serve critical functions across joining, surfacing and additive manufacturing processes:
Application | Details | Common Powders Used |
---|---|---|
Shielded metal arc welding (SMAW) | Manual stick electrodes | Rutile, cellulose, iron powder, ferroalloys |
Gas metal arc welding (GMAW) | Continous solid/metal cored wire feeds | Carbon steel, stainless steel, nickel alloys |
Flux cored arc welding (FCAW) | Tubular consumables with flux core | Alloyed steel, chromium, nickel, manganese |
Submerged arc welding (SAW) | Automated wire process with granular flux | Silicon, manganese, chromium, nickel |
Electroslag welding | Vertical up passes with flux pool | Chromium, nickel, copper, Vernon |
Plasma transferred arc (PTA) | Powder fed into plasma plume | Tungsten carbides, chrome carbides, niobium carbides |
Thermal Sprays
Specialized electrode-type powders for coating deposition via combustion, electric arc and plasma spray methods.
Thus electrode powders find usage across manual, automatic, high deposition and surface engineering welding and thermal spray processes in industrial environments.
-
CM247LC Powder | Nickel Alloy Powder
-
0# Pure Nickel powder
-
NiCoCrAlY alloys powders
-
Rene 142 alloy-Rene Powder
-
Haynes 25 Haynes Powder
-
Best Hastelloy C-22 Powder-High temperature alloy Powder for 3D Printing
-
Best Hastelloy C-276 Powder-High temperature alloy Powder for 3D Printing
-
Best Hastelloy N Powder-High temperature alloy Powder for 3D Printing
-
Best Hastelloy B Powder丨High temperature alloy Powder for 3D Printing
Electrode Powder Size Specifications
Size Class | Typical Range | Applications |
---|---|---|
Extra fine | 10-38 microns | High alloy steels, duplex/super alloys |
Fine | 38-75 microns | Automated GMAW wires, SAW fluxes |
Medium | 75-150 microns | Manual SMAW sticks, FCAW |
Coarse | 150-300 microns | High deposition submerged arc |
International Electrotechnical Commission standard IEC 60544 governs dimensional tolerances, size analysis methodology and sieve sizes.
Beyond chemistry, particle size distribution is critical for arc stability, metallurgical microstructure, deposit efficiency, speed, surface finish and performance.
Classification of Electrode Powders
Several classification systems covering composition, intended use and relevant standards help identify suitable powders:
Standard | Basis |
---|---|
AWS A5.0 | Alloy families and electrode type – mild steel, low alloy steel, stainless steel, surfacing, etc |
ASME SFA-5.0 | Welding wire specifications grouping alloys into similar base types |
ISO 14172 | Chemical composition ranges for steel and nickel filler metals |
ISO 17632 | Specifying wire dimensions, shielding, current types and positions |
ISO 13916 | Acceptance inspection levels for metallic filler material |
CEN EN 758 | Defining requirements for flux coated arc welding sticks |
CEN EN 760 | Specification for flux cored wire types |
These classifications help align electrode development, testing and application to produce repeatable, high quality welds meeting application needs.
Cost Breakdown of Electrode Powders
Powder Grade | Price Range | Key Drivers |
---|---|---|
Carbon and low alloy steels | $3-6 per lb | Bulk commodity pricing, stable costs |
Stainless steels | $6-12 per lb | Price volatility for nickel/chromium |
High strength low alloys | $15-25 per lb | Source of alloying additions like cobalt |
Tool steels, superalloys | $30-60 per lb | Feedstock method, tight chemistry requirements |
Carbides, composites | $50-150 per lb | Base powder synthesis route, low demand |
- Requires high purity precursor materials
- Costs rise for fine controlled powders
- Special use-case niche alloys more expensive
- Requires extensive R&D and testing
- Economies of scale from bulk production
Recommendations
Work closely with powder producers during alloy development to balance performance and budget based on application criticality.
Grades of Electrode Powder
Description | Typical Applications | Examples |
---|---|---|
Commodity plain carbon and low alloy steels | Structural fabrication, infrastructure, transport | AISI/SAE 1018, 4140 compositions |
Common austenitic stainless steels | Tanks, process vessels, marine hardware | 304L, 316L grades |
Low temperature service steels | Cryogenic storage, liquefied gas containment | 9% nickel steels meeting AWS A5.11 |
Solid wire for high speed joining | Automotive assembly, appliances | ER70S-6, ER308LSi |
Metal cored wires for high deposition | Structural steel fabrication, bridges | AWS classifications like EM12K |
Hardfacing alloys | Wear resistant overlays | Chromium carbides like Stoody D Dur 600 |
Corrosion resistant alloys | Chemical processing equipment | Nickel and cobalt alloys per AWS A5.14 |
High strength steels | Aerospace, pressure vessels, turbines | Custom nickel and cobalt superalloys |
The spectrum runs from high volume commodity filler wires for carbon steel to specialized grades for demanding environments. Custom formulations address unique requirements.
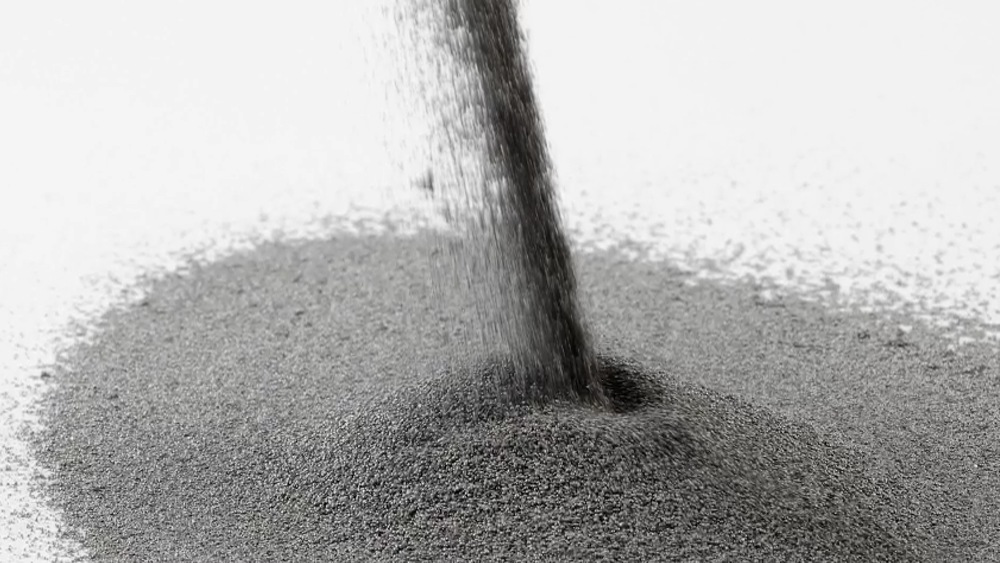
FAQs
How are welding electrodes manufactured?
Electrodes consist of a metal rod or wire onto which electrode powders are deposited creating the coating surrounding a solid or flux core:
- Electrode powder compositions tailored to develop target properties
- Powders blended, conditioned and adhered to rod
- Extrusion or compaction to consolidate coating
- Final drying and quality checks before use
Flux ingredients promote arc stability while alloying elements enrich deposited weld chemistry as the coating melts and transfers material to the joint during welding.
What are the different thermal spray powders?
Various thermal spray techniques for protective coatings, wear and corrosion resistance utilize electrode-type feedstock powders with specialized characteristics:
- Combustion powder – iron, nickel, cobalt alloys with high purity
- Wire arc spray – more coarse steel and stainless wires
- Plasma spray – extremely fine, spherical and smooth powders
- High Velocity Oxy Fuel (HVOF) – optimized for higher velocities
- Cold spray – ductile, annealed and work hardened metals
The deposition mechanism influences optimal powder attributes like particle size distribution, shape and microstructure.
How to choose the right electrode?
Factors guiding electrode selection include:
- Service conditions – temperature, corrosion, impact
- Base metal standard and composition
- Mechanical performance required – hardness, cracking, ductility
- Cryogenic or high temperature use
- Material thickness and joint preparation
- Welding process – stick, MIG, submerged arc
- Required structural integrity specs – stress rupture, creep
Work with manufacturers to match consumable performance to operating requirements through powder composition, standard classifications and supporting qualification data.
What is the porosity limit for electrode coatings?
Porosity in the electrode coating caused by gas entrapment during manufacturing leads to process inconsistencies and defects in the finished weld. Coating density requirements as per AWS, ASME and ISO standards:
- Minimum 95% theoretical density
- Less than 1% visual porosity at 10X magnification
- Maximum 5% porosity by image analysis
Achieved through optimized powder blends, steel strip surface preparation, extrusion parameters and rigorous quality control checks.
How are electrode fumes formed?
Arc welding vaporizes alloying elements in the molten droplet leading to fume formation mechanisms:
- Oxide formation – reaction with atmospheric oxygen
- Nucleation of supersaturated metal vapors upon cooling
- Condensation of gaseous species into fine particulates
Fume rate and composition depends on electrode coating, base metal, process parameters and presence of contaminants. Proper extraction and PPE is essential.
Conclusion
The composition, powder characteristics, homogenization and layering of specialty metal alloys, fluxes and composites enables tailored metallurgical structures with localized enchantment and designed weld interfaces. Maintaining strict controls from raw material to finished product is essential to achieve repeatable welds that resist cracking, wear, fatigue and corrosion across an extensive range of industrial applications and operating environments. Further advancements in novel alloys, smart wires, sensors and automation will continue expanding the scope and capabilities of next generation welding processes enabled by ever more sophisticated electrode formulations.