Overview of FeCoNiCr Powder
FeCoNiCr powder is a type of high-entropy alloy (HEA) powder, known for its extraordinary mechanical properties, thermal stability, and corrosion resistance. As its name suggests, it is primarily composed of iron (Fe), cobalt (Co), nickel (Ni), and chromium (Cr). These powders are becoming increasingly relevant in industries such as aerospace, automotive, energy, and biomedical applications due to their unique combination of properties, such as high strength-to-weight ratios, improved wear resistance, and excellent performance in extreme environments.
High-entropy alloys, including FeCoNiCr, break away from the traditional alloying principle, which is usually based on a single primary element with small additions of others. Instead, HEAs are formed by mixing equal or near-equal amounts of multiple elements. This results in complex alloy structures that exhibit exceptional material properties, making FeCoNiCr alloys stand out.
Whether you’re new to this or a seasoned materials scientist, this guide is going to break everything down for you. By the end of it, you’ll not only understand what makes FeCoNiCr powder so special, but also how it’s used across various industries, what models exist, and what advantages or limitations to expect.
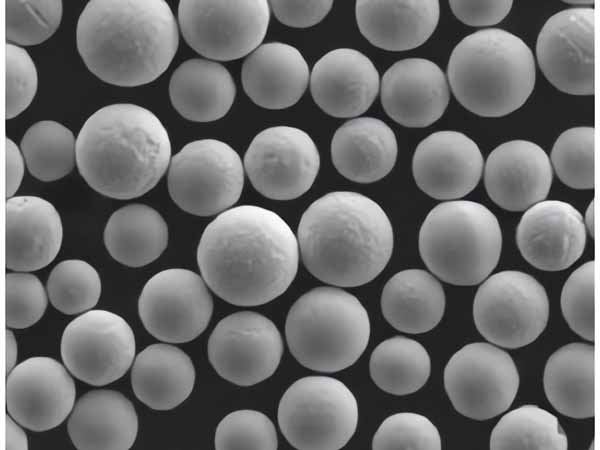
Composition of FeCoNiCr Powder
The composition of FeCoNiCr powder is its defining feature. Each element contributes unique properties, making the alloy more than just the sum of its parts.
Element | Percentage (%) | Contribution to Alloy |
---|---|---|
Iron (Fe) | 20-25 | Improves strength and durability. |
Cobalt (Co) | 20-25 | Provides magnetic properties and wear resistance. |
Nickel (Ni) | 20-25 | Enhances corrosion resistance and toughness. |
Chromium (Cr) | 20-25 | Adds oxidation resistance and hardness. |
The roughly equal proportions of these elements lead to a balanced, stable microstructure that results in the exceptional characteristics seen in FeCoNiCr powders. This even distribution of the atoms within the material matrix prevents large clusters or segregations, leading to more uniform and predictable behavior under stress.
Characteristics of FeCoNiCr Powder
The defining characteristics of FeCoNiCr powder include its ability to perform in harsh conditions, which makes it suitable for a wide variety of applications.
Key Characteristics
- High Strength: The combination of Fe, Co, Ni, and Cr creates a robust material with high tensile strength and yield strength.
- Corrosion Resistance: Chromium and nickel make this alloy highly resistant to corrosive environments, allowing it to outperform many traditional materials in demanding situations.
- Oxidation Resistance: With chromium in the mix, FeCoNiCr alloys exhibit excellent oxidation resistance, allowing them to withstand high temperatures without degrading.
- Thermal Stability: The powder retains its mechanical properties even at elevated temperatures, making it suitable for use in extreme environments like gas turbines and rocket engines.
- Wear Resistance: The presence of cobalt enhances wear resistance, which is crucial in industries where material degradation can lead to system failure.
Applications of FeCoNiCr Powder
FeCoNiCr powder’s unique properties make it invaluable across multiple sectors. Whether it’s the aerospace industry seeking materials that can endure extreme temperatures or the medical field looking for biocompatible alloys, FeCoNiCr fits the bill.
Industry | Application | Why FeCoNiCr? |
---|---|---|
Aerospace | Turbine blades, engine components | High-temperature stability, corrosion resistance. |
Automotive | Exhaust systems, high-performance parts | Wear and corrosion resistance, thermal stability. |
Biomedical | Implants, surgical tools | Biocompatibility, strength, and corrosion resistance. |
Energy | Power generation, nuclear reactors | Exceptional thermal stability, durability. |
Manufacturing | Cutting tools, molds | Wear resistance, hardness. |
In these sectors, FeCoNiCr powder often serves as a superior alternative to traditional alloys like stainless steel, titanium, and Inconel.
Models of FeCoNiCr Powder
There are various models of FeCoNiCr powder, each with slight variations in composition and intended use. Below are ten specific models with unique characteristics tailored to different applications.
Model | Composition | Key Features | Applications |
---|---|---|---|
FeCoNiCrAl | Fe, Co, Ni, Cr, Al | Enhanced oxidation resistance due to aluminum. | Aerospace, turbine blades. |
FeCoNiCrMn | Fe, Co, Ni, Cr, Mn | Improved mechanical properties, better ductility. | Automotive parts, wear-resistant tools. |
FeCoNiCrMo | Fe, Co, Ni, Cr, Mo | Increased corrosion resistance from molybdenum. | Marine engineering, offshore applications. |
FeCoNiCrTi | Fe, Co, Ni, Cr, Ti | Superior high-temperature performance. | Power generation, heat exchangers. |
FeCoNiCrV | Fe, Co, Ni, Cr, V | Higher strength and hardness due to vanadium. | High-strength applications, cutting tools. |
FeCoNiCrNb | Fe, Co, Ni, Cr, Nb | Enhanced wear resistance and toughness. | Aerospace, high-wear environments. |
FeCoNiCrW | Fe, Co, Ni, Cr, W | Improved creep resistance, better high-temp stability. | High-pressure systems, aerospace. |
FeCoNiCrSi | Fe, Co, Ni, Cr, Si | Silicon adds oxidation resistance, low-density. | Lightweight components, electronics. |
FeCoNiCrZr | Fe, Co, Ni, Cr, Zr | Zirconium improves toughness and thermal stability. | Nuclear reactors, high-stress environments. |
FeCoNiCrCu | Fe, Co, Ni, Cr, Cu | Copper enhances electrical conductivity. | Electrical components, connectors. |
These models vary slightly in their alloying elements, which change the performance characteristics depending on the specific needs of an application. For example, adding aluminum (Al) to the mix creates better oxidation resistance, which is crucial for high-temperature environments like turbines.
Specifications and Standards for FeCoNiCr Powder
When selecting FeCoNiCr powder for industrial applications, it’s important to understand the specifications and standards. Here’s a breakdown of commonly used sizes, grades, and relevant standards:
Specification | Details |
---|---|
Powder Size | 1-100 microns |
Purity | ≥ 99% |
Standards | ASTM B212, AMS 5718, ISO 22068 |
Grades | Industrial Grade, Medical Grade, Aerospace Grade |
Density | 7.8 g/cm³ |
Powder size is critical in applications like additive manufacturing, where smaller particles often lead to higher surface quality. Similarly, purity and standards ensure the material performs consistently under different working conditions.
Advantages of FeCoNiCr Powder
Compared to conventional materials, FeCoNiCr powder offers several compelling advantages:
Why FeCoNiCr Stands Out:
- Higher Temperature Resistance: Compared to stainless steel or even Inconel, FeCoNiCr alloys withstand higher operating temperatures without losing strength.
- Improved Wear and Tear Resistance: Materials that see a lot of mechanical stress, like cutting tools, benefit from the superior wear resistance of FeCoNiCr.
- Corrosion Resistance: Especially in marine or industrial chemical environments, the alloy’s resistance to oxidation and corrosion surpasses traditional materials.
- Magnetic Properties: The cobalt content lends magnetic properties to FeCoNiCr alloys, useful in certain electrical and magnetic applications.
- Versatility: With the ability to fine-tune the alloy’s properties by tweaking the elemental composition, FeCoNiCr can be adapted for specific tasks, making it more versatile than alloys like titanium or brass.
Limitations of FeCoNiCr Powder
As excellent as FeCoNiCr powder is, it’s not without its limitations. Here are a few areas where it may not always be the ideal solution:
Drawbacks to Consider:
- Cost: The raw materials involved, particularly cobalt and nickel, are more expensive compared to common metals like iron or aluminum, making FeCoNiCr alloys more costly to produce.
- Machinability: While the hardness and wear resistance are advantages in many respects, they can make FeCoNiCr harder to machine or process compared to softer materials like aluminum alloys.
- Complex Manufacturing: The processes required to produce high-quality FeCoNiCr powders can be more complex, requiring specialized equipment and techniques like gas atomization or plasma spheroidization.
Suppliers and Pricing Details for FeCoNiCr Powder
When it comes to sourcing FeCoNiCr powders, several suppliers provide this material with varying pricing depending on grade and quantity.
Supplier | Price Range | Details |
---|---|---|
American Elements | $250 – $600 per kg | Offers a wide range of alloy compositions and customizable sizes. |
Metal Powder Supplier | $400 – $700 per kg | Specializes in high-purity powder for additive manufacturing. |
Advanced Alloy Solutions | $350 – $800 per kg | Provides various HEA powders including FeCoNiCr with specific grades for aerospace. |
Sigma-Aldrich | $500 – $900 per kg | Known for ultra-high purity powders for research and development purposes. |
Pricing for FeCoNiCr powder can vary significantly based on the desired purity, powder size, and the specific alloying elements involved. Higher purity powders designed for medical or aerospace use tend to be more expensive than those for general industrial applications.
Comparison: FeCoNiCr Powder vs. Traditional Alloys
Let’s take a quick look at how FeCoNiCr stacks up against some more traditional alloys like stainless steel or titanium:
Feature | FeCoNiCr Powder | Stainless Steel | Titanium |
---|---|---|---|
Temperature Resistance | Higher, stable at extreme temps | Moderate, weakens at very high temps | Excellent, but weaker at ultra-high temps |
Corrosion Resistance | Superior, even in harsh environments | Good, but susceptible to chloride attack | Excellent, but more costly |
Strength-to-Weight Ratio | High | Moderate | High |
Cost | Higher | Lower | High |
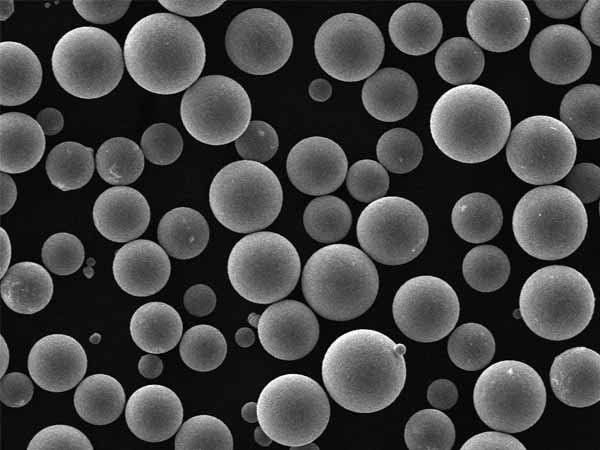
FAQ
Question | Answer |
---|---|
What is FeCoNiCr powder used for? | FeCoNiCr powder is used in high-performance applications such as aerospace components, automotive parts, medical implants, and power generation. |
Is FeCoNiCr expensive? | Yes, compared to traditional materials like stainless steel, FeCoNiCr powder is more expensive due to its complex manufacturing process and raw material costs. |
What industries benefit the most from FeCoNiCr? | Aerospace, automotive, energy, and biomedical sectors benefit significantly from FeCoNiCr due to its superior mechanical properties. |
How does FeCoNiCr compare to stainless steel? | FeCoNiCr offers higher temperature resistance and better corrosion resistance but is more expensive than stainless steel. |
Can FeCoNiCr be used in additive manufacturing? | Yes, FeCoNiCr powder is frequently used in additive manufacturing due to its fine particle size and excellent mechanical properties. |
Conclusion
FeCoNiCr powder represents the cutting edge of material science in high-entropy alloys. Its balance of high strength, corrosion resistance, and thermal stability make it an ideal choice for demanding industrial applications. Although it can be costly and more challenging to process than traditional alloys, its performance in extreme environments makes the investment worthwhile.
If you’re working in industries where reliability under stress is critical, FeCoNiCr could be your go-to material. Whether you’re an engineer, a manufacturer, or just curious about advanced alloys, understanding FeCoNiCr powder opens up new possibilities for innovation.