Introduction: What is Fewer Satellite Particles Powder?
In the realm of metal powders, particularly those used in additive manufacturing, precision casting, and other high-performance applications, the purity and particle size distribution of the powder are critical. One such innovation that has emerged is the fewer satellite particles powder. This term refers to metal powders that have been processed to reduce or eliminate the small, unwanted particles—known as satellites—that cling to larger particles. These satellite particles can lead to a host of issues, from poor flowability to inconsistent layer deposition in 3D printing processes.
But why should you care about fewer satellite particles powder? Well, think about it like this: if you were baking a cake, you’d want all your ingredients finely sifted and measured, right? Imagine if there were lumps or clumps in your flour—your cake wouldn’t come out smooth and uniform. The same principle applies here. Fewer satellite particles mean better control over the manufacturing process, leading to higher quality and more reliable end products.
This article will delve deep into the world of fewer satellite particles powder, exploring its composition, characteristics, specific metal powder models, applications, advantages, and limitations. We’ll also compare different powders and provide you with comprehensive tables to help you understand this topic fully. So, let’s get started!
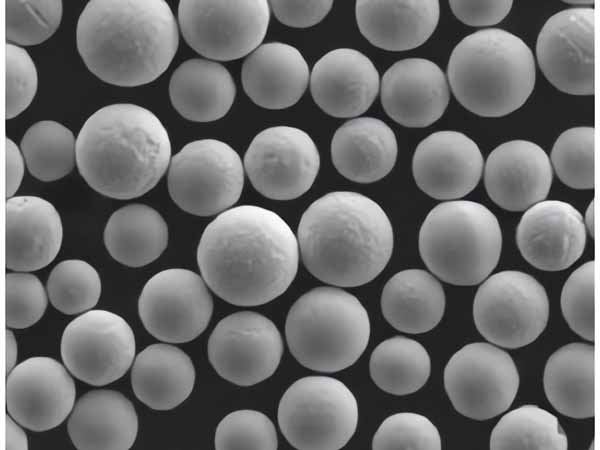
Composition of Fewer Satellite Particles Powder
Fewer satellite particles powder isn’t just any metal powder; it’s engineered with precision. These powders are typically made from metals like titanium, aluminum, copper, and various alloys, each chosen for specific applications in industries such as aerospace, automotive, medical, and electronics.
The composition of fewer satellite particles powder is carefully controlled during manufacturing. Advanced techniques like gas atomization or plasma atomization are employed to ensure the powder’s high purity and minimize the formation of satellites. The process usually involves the rapid cooling of molten metal, which forms spherical particles. During this process, fine control over the atomization parameters helps reduce the likelihood of satellite formation.
Below is a table summarizing the typical composition of fewer satellite particles powder for different metal types.
Metal Type | Composition | Purity Level | Primary Use |
---|---|---|---|
Titanium (Ti) | Ti (90-99%), Alloying Elements (Al, V, etc.) | ≥99.5% | Aerospace, Medical Implants |
Aluminum (Al) | Al (85-99%), Silicon, Magnesium | ≥99% | Automotive, Electronics |
Copper (Cu) | Cu (90-99%), Zinc, Tin | ≥99.9% | Electronics, Conductive Parts |
Nickel Alloys | Ni (70-90%), Chromium, Molybdenum, Iron | ≥99% | Aerospace, High-Temperature Applications |
Stainless Steel | Iron (70-80%), Chromium, Nickel, Manganese | ≥98% | Medical Devices, Industrial Components |
Cobalt-Chrome | Co (60-70%), Chromium, Molybdenum | ≥99% | Dental, Medical Implants, High-Wear Parts |
Characteristics of Fewer Satellite Particles Powder
The defining characteristic of fewer satellite particles powder is its high level of spherical particle uniformity and low satellite particle content. These characteristics directly translate into better performance in various applications. Let’s break down the key characteristics:
- Particle Size Distribution: A narrow particle size distribution is critical in fewer satellite particles powder. This ensures consistency in layer deposition during additive manufacturing and uniformity in sintering processes.
- Flowability: The powder’s ability to flow smoothly is paramount for processes like 3D printing. Fewer satellite particles improve flowability, reducing the chances of clogging and ensuring even distribution of material.
- Packing Density: The absence of satellite particles leads to a higher packing density, which is crucial for applications requiring dense, solid structures, like in aerospace components.
- Purity: High purity levels are maintained, with minimal contamination from unwanted elements or oxides. This is especially important in medical and aerospace applications where material integrity is critical.
- Surface Finish: The end products manufactured using fewer satellite particles powder often have superior surface finishes, reducing the need for post-processing.
Here’s a summary table of these characteristics:
Characteristic | Description |
---|---|
Particle Size Distribution | Narrow, consistent particle size range |
Flowability | High, with reduced risk of clogging in additive manufacturing processes |
Packing Density | Higher packing density due to uniform particle shape and size |
Purity | High purity with minimal contamination, crucial for sensitive applications |
Surface Finish | Superior surface finish on final products, reducing the need for extensive post-processing |
Advantages of Fewer Satellite Particles Powder
Why should one opt for fewer satellite particles powder over conventional metal powders? Let’s explore the advantages:
- Improved Print Quality: In additive manufacturing, the consistency of the powder directly impacts the quality of the final product. Fewer satellite particles mean fewer defects and better overall print quality.
- Enhanced Flowability: As mentioned earlier, powders with fewer satellites flow better, which is essential in high-precision manufacturing processes like 3D printing. This leads to fewer interruptions and more reliable production cycles.
- Higher Density in Parts: The higher packing density of these powders translates to parts with fewer voids and higher structural integrity. This is particularly important in applications where mechanical strength and durability are paramount.
- Reduced Waste: Better flowability and consistent layer deposition mean that less material is wasted during the manufacturing process. This not only saves costs but also aligns with sustainable manufacturing practices.
- Better Surface Finish: The smoother, more uniform layers deposited using fewer satellite particles powder result in better surface finishes, reducing the need for additional finishing processes like sanding or polishing.
- Lower Defect Rate: The reduced presence of satellites means fewer potential sites for defect formation, which is crucial for applications where reliability is critical, such as in aerospace or medical devices.
- Cost Efficiency: While the initial cost of fewer satellite particles powder might be higher, the reduction in waste, post-processing, and defect rates can lead to overall cost savings.
- Enhanced Mechanical Properties: The final products often exhibit better mechanical properties such as tensile strength, hardness, and fatigue resistance due to the uniformity and purity of the powder.
Disadvantages of Fewer Satellite Particles Powder
However, it’s essential to balance the advantages with a clear understanding of the limitations:
- Higher Initial Cost: The advanced manufacturing processes required to produce fewer satellite particles powder often result in a higher initial cost compared to conventional powders.
- Limited Availability: Not all metal types or alloys are available in fewer satellite particles powder form, which can limit the range of applications.
- Processing Complexity: The techniques used to achieve fewer satellite particles can be complex and require specialized equipment and expertise.
- Sensitivity to Handling: Due to the fine nature of these powders, they can be more sensitive to handling and environmental conditions, potentially leading to oxidation or contamination if not stored properly.
Here’s a comparison table summarizing the pros and cons:
Advantages | Disadvantages |
---|---|
Improved print quality | Higher initial cost |
Enhanced flowability | Limited availability in certain metals and alloys |
Higher density in parts | Processing complexity |
Reduced waste | Sensitivity to handling and storage conditions |
Better surface finish | |
Lower defect rate | |
Cost efficiency in the long term | |
Enhanced mechanical properties |
-
CM247LC Powder | Nickel Alloy Powder
-
0# Pure Nickel powder
-
NiCoCrAlY alloys powders
-
Rene 142 alloy-Rene Powder
-
Haynes 25 Haynes Powder
-
Best Hastelloy C-22 Powder-High temperature alloy Powder for 3D Printing
-
Best Hastelloy C-276 Powder-High temperature alloy Powder for 3D Printing
-
Best Hastelloy N Powder-High temperature alloy Powder for 3D Printing
-
Best Hastelloy B Powder丨High temperature alloy Powder for 3D Printing
Specific Metal Powder Models with Fewer Satellite Particles
When it comes to fewer satellite particles powder, various metal powders are available on the market, each tailored for specific applications. Below are ten examples of metal powders that have been engineered to minimize satellite content, along with their detailed descriptions.
- Argon-Atomized Titanium Powder (Ti64)
- Description: This titanium alloy powder is atomized using argon gas to ensure a highly spherical shape with minimal satellites. It’s commonly used in aerospace and medical applications for its excellent strength-to-weight ratio and biocompatibility.
- Applications: Aerospace components, medical implants, high-performance automotive parts.
- Plasma-Spheroidized Aluminum Alloy Powder (AlSi10Mg)
- Description: Plasma spheroidization is used to produce this aluminum alloy powder, known for its high flowability and reduced satellite content. It is ideal for lightweight structures requiring good thermal properties.
- Applications: Automotive parts, heat exchangers, lightweight structural components.
- Gas-Atomized Stainless Steel Powder (316L)
- Description: A high-purity stainless steel powder with a low satellite content, produced via gas atomization. It offers excellent corrosion resistance and is used in a variety of industrial and medical applications.
- Applications: Medical devices, surgical instruments, industrial components.
- Nickel-Based Superalloy Powder (Inconel 718)
- Description: This nickel-based superalloy powder is atomized to achieve a spherical shape with fewer satellites, enhancing its high-temperature performance. It’s widely used in aerospace and energy applications.
- Applications: Turbine blades, rocket engines, high-temperature industrial components.
- Copper Powder (CuSn10)
- Description: A copper alloy powder with reduced satellite content, known for its excellent electrical conductivity and formability. It’s particularly suitable for electrical and thermal applications.
- Applications: Electrical connectors, heat sinks, conductive parts.
- Cobalt-Chrome Alloy Powder (CoCrMo)
- Description: This cobalt-chrome-molybdenum alloy powder is refined to minimize satellites, providing superior wear resistance and biocompatibility. It’s a go-to material for medical and dental implants.
- Applications: Dental crowns, orthopedic implants, high-wear components.
- Tungsten Carbide Powder (WC-Co)
- Description: A tungsten carbide powder with a cobalt binder, engineered to have fewer satellites, making it ideal for applications requiring extreme hardness and wear resistance.
- Applications: Cutting tools, mining equipment, wear-resistant coatings.
- Maraging Steel Powder (18Ni300)
- Description: This high-strength steel powder is processed to reduce satellite particles, ensuring high performance in applications requiring toughness and machinability.
- Applications: Tooling, molds, high-strength structural components.
- Aluminum-Bronze Powder (CuAl10Fe5Ni5)
- Description: An aluminum-bronze alloy powder with enhanced flowability and fewer satellites, offering excellent corrosion resistance and strength.
- Applications: Marine components, bearings, wear-resistant parts.
- Iron-Chromium-Aluminum Powder (FeCrAl)
- Description: A high-temperature resistant alloy powder with minimized satellite particles, ideal for applications requiring oxidation resistance at elevated temperatures.
- Applications: Heating elements, automotive exhaust components, high-temperature industrial parts.
Applications of Fewer Satellite Particles Powder
Fewer satellite particles powder is a game-changer across multiple industries, thanks to its unique characteristics and advantages. Let’s explore the various applications where these powders make a significant impact.
Industry | Applications | Benefits |
---|---|---|
Aerospace | Turbine blades, structural components, rocket engines | High strength-to-weight ratio, high-temperature performance |
Medical | Implants, surgical instruments, dental crowns | Biocompatibility, high precision, superior surface finish |
Automotive | Lightweight structural components, heat exchangers, exhaust systems | Reduced weight, better thermal properties, enhanced durability |
Electronics | Conductive parts, heat sinks, connectors | Excellent electrical conductivity, formability, thermal management |
Energy | High-temperature industrial components, turbine blades, heating elements | Oxidation resistance, high-temperature durability |
Industrial Manufacturing | Tooling, molds, cutting tools | Wear resistance, high strength, cost efficiency |
Marine | Bearings, corrosion-resistant components, propellers | High corrosion resistance, durability in harsh environments |
Mining | Wear-resistant coatings, cutting tools | Extreme hardness, long service life, reduced maintenance costs |
Defense | High-strength structural components, lightweight armor | Enhanced durability, high strength, and impact resistance |
Specifications, Sizes, Grades, and Standards
When choosing fewer satellite particles powder, it’s essential to consider the specific specifications, sizes, grades, and standards that match your application needs. The table below provides a comprehensive overview.
Metal Type | Particle Size (µm) | Grade | Standard | Purity (%) |
---|---|---|---|---|
Titanium (Ti64) | 15-45, 45-90 | Grade 5 | ASTM F136, AMS 4998 | ≥99.5 |
Aluminum (AlSi10Mg) | 20-63, 63-150 | AlSi10Mg | ISO 3522, AMS 4289 | ≥99 |
Stainless Steel (316L) | 10-45, 45-105 | 316L | ASTM A276, AMS 5648 | ≥99 |
Nickel Alloys (Inconel 718) | 15-45, 45-90 | Inconel 718 | ASTM B637, AMS 5662 | ≥99 |
Copper (CuSn10) | 10-45, 45-75 | CuSn10 | ASTM B505, ISO 1338 | ≥99.9 |
Cobalt-Chrome (CoCrMo) | 15-45, 45-90 | CoCrMo | ASTM F75, ISO 5832-4 | ≥99 |
Tungsten Carbide (WC-Co) | 0.5-15, 15-45 | WC-Co | ISO 5286, ASTM B777 | ≥99 |
Maraging Steel (18Ni300) | 15-45, 45-90 | 18Ni300 | AMS 6521, ASTM A538 | ≥99 |
Aluminum-Bronze (CuAl10Fe5Ni5) | 15-45, 45-90 | CuAl10Fe5Ni5 | ASTM B148, AMS 4640 | ≥98 |
Iron-Chromium-Aluminum (FeCrAl) | 15-45, 45-90 | FeCrAl | ASTM A213, ISO 11954 | ≥99 |
Suppliers and Pricing Details
Finding the right supplier for fewer satellite particles powder is crucial for ensuring quality and consistency in your manufacturing processes. Below is a list of reputable suppliers along with indicative pricing details.
Supplier | Metal Types Offered | Typical Price (per kg) | Location | Lead Time |
---|---|---|---|---|
Advanced Powders & Coatings (AP&C) | Titanium, Aluminum, Stainless Steel | $100 – $500 | Canada | 4-6 weeks |
LPW Technology | Nickel Alloys, Stainless Steel, Cobalt-Chrome | $150 – $600 | UK | 3-5 weeks |
Carpenter Additive | Titanium, Aluminum, Maraging Steel | $200 – $700 | USA | 4-8 weeks |
Sandvik Osprey | Aluminum, Copper, Tungsten Carbide | $120 – $550 | Sweden | 5-7 weeks |
Praxair Surface Technologies | Inconel, Cobalt-Chrome, Stainless Steel | $180 – $650 | USA | 6-8 weeks |
Höganäs AB | Iron-Chromium-Aluminum, Aluminum-Bronze | $90 – $400 | Sweden | 3-6 weeks |
Erasteel | Maraging Steel, Stainless Steel, Nickel Alloys | $140 – $600 | France | 4-6 weeks |
Arcam AB (GE Additive) | Titanium, Aluminum | $220 – $750 | Sweden | 5-8 weeks |
H.C. Starck | Tungsten Carbide, Nickel Alloys | $150 – $700 | Germany | 6-10 weeks |
APMI International | Specialty Alloys, Stainless Steel, Cobalt-Chrome | $180 – $600 | USA | 4-8 weeks |
Advantages and Limitations Compared
When deciding between fewer satellite particles powder and conventional metal powders, it’s essential to weigh the advantages and limitations of each. Here’s a direct comparison:
Factor | Fewer Satellite Particles Powder | Conventional Metal Powders |
---|---|---|
Flowability | Superior flowability, reducing clogging and defects | May suffer from poor flowability due to satellites |
Surface Finish | Produces smoother surfaces, reducing post-processing needs | May require extensive post-processing |
Packing Density | Higher packing density, leading to denser parts | Lower packing density, more voids |
Defect Rate | Lower defect rate, higher reliability | Higher defect rate, more potential for inconsistencies |
Cost | Higher initial cost, but long-term savings | Lower initial cost, potential for higher waste |
Mechanical Properties | Enhanced properties like strength and hardness | May have inconsistent mechanical properties |
Availability | Limited to specific metals and alloys | Widely available across various metals and alloys |
Processing Complexity | Requires advanced processing techniques | Simpler processing, more widely accessible |
Suitability for High-Precision Applications | Ideal for high-precision, high-performance applications | May not be suitable for ultra-high-precision needs |
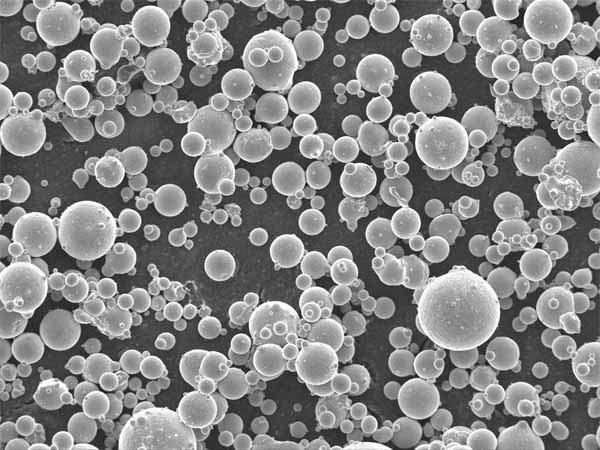
FAQ
Question | Answer |
---|---|
What is the main advantage of fewer satellite particles powder? | The main advantage is its superior flowability and reduced defect rates in additive manufacturing. |
How does fewer satellite particles powder improve surface finish? | The uniform particle size and shape reduce irregularities, leading to smoother layers and better surface finish. |
Is fewer satellite particles powder more expensive? | Yes, it typically costs more initially, but can lead to long-term savings through reduced waste and defects. |
Which industries benefit most from fewer satellite particles powder? | Aerospace, medical, automotive, and electronics industries see the most significant benefits. |
Can fewer satellite particles powder be used in any 3D printer? | It depends on the printer’s capabilities, but most high-end industrial 3D printers are compatible. |
What metals are available in fewer satellite particles powder? | Commonly available metals include titanium, aluminum, stainless steel, nickel alloys, and more. |
Are there any downsides to using fewer satellite particles powder? | The primary downside is the higher initial cost and the complexity of production. |
How are fewer satellite particles achieved? | Advanced atomization techniques like gas or plasma atomization are used to minimize satellite formation. |
Conclusion
Fewer satellite particles powder represents a significant advancement in the field of metal powders, particularly for high-precision, high-performance applications. With its superior flowability, reduced defect rates, and enhanced mechanical properties, it offers compelling benefits for industries like aerospace, medical, automotive, and electronics. While the initial cost might be higher, the long-term savings, coupled with the potential for higher-quality end products, make it a worthwhile investment.
As the demand for precision and reliability in manufacturing continues to grow, the adoption of fewer satellite particles powder is likely to expand. Whether you’re involved in 3D printing, precision casting, or any other form of advanced manufacturing, understanding and utilizing this innovative material can give you a competitive edge.