Overview
Forging grade materials are essential in various industries, from automotive to aerospace, due to their remarkable strength, durability, and performance under extreme conditions. This guide dives deep into the world of forging grade materials, exploring their types, compositions, properties, and specific metal powder models. We will also look at their applications, specifications, suppliers, and pricing. By the end of this article, you’ll have a detailed understanding of forging grade materials and how to choose the best one for your needs.
What is Forging Grade Material?
Forging grade materials are metals and alloys specifically designed to withstand the intense pressures and high temperatures involved in the forging process. These materials are known for their superior mechanical properties, such as toughness, fatigue strength, and resistance to wear and corrosion.
Why Are Forging Grade Materials Important?
- Strength and Durability: Forged materials exhibit enhanced mechanical properties compared to cast or machined parts.
- Versatility: They can be used in a wide range of applications, including automotive, aerospace, industrial machinery, and more.
- Quality: Forging eliminates internal voids and gas pockets, resulting in a more homogeneous material structure.
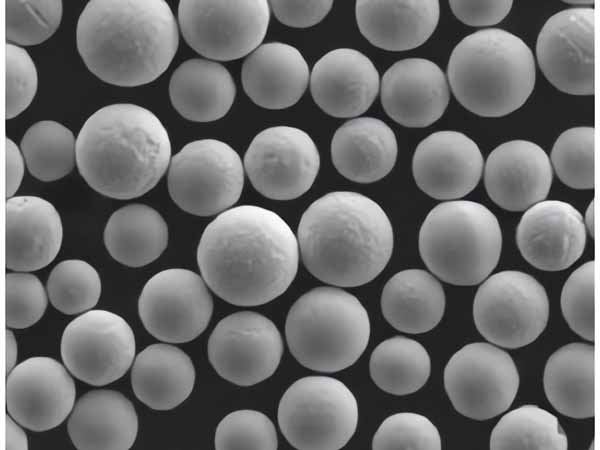
Types of Forging Grade Materials
1. Carbon Steel
Carbon steel is widely used in forging due to its excellent mechanical properties and cost-effectiveness. It’s classified into three categories based on carbon content: low, medium, and high carbon steel.
2. Alloy Steel
Alloy steels contain additional alloying elements like chromium, nickel, and molybdenum, enhancing their mechanical properties. They are known for their improved toughness, wear resistance, and strength.
3. Stainless Steel
Stainless steels are known for their corrosion resistance, making them ideal for applications exposed to harsh environments. Common grades include 304, 316, and 410.
4. Tool Steel
Tool steels are designed for high hardness and wear resistance, making them suitable for cutting and forming tools. Popular grades include D2, H13, and A2.
5. Aluminum Alloys
Aluminum alloys are valued for their lightweight and high strength-to-weight ratio. Commonly used grades in forging include 2024, 6061, and 7075.
6. Titanium Alloys
Titanium alloys are known for their exceptional strength, lightweight, and corrosion resistance, making them ideal for aerospace and medical applications.
Composition of Forging Grade Materials
Understanding the composition of forging grade materials helps in selecting the right material for specific applications. Below is a table summarizing the compositions of various forging grade materials:
Material | Composition | Properties |
---|---|---|
Carbon Steel | Iron, Carbon (0.2-2.1%) | High strength, good ductility, cost-effective |
Alloy Steel | Iron, Carbon, Chromium, Nickel, Molybdenum | Enhanced toughness, wear resistance, improved strength |
Stainless Steel | Iron, Carbon, Chromium (10.5-30%), Nickel | Excellent corrosion resistance, good strength, durability |
Tool Steel | Iron, Carbon, Manganese, Chromium, Tungsten | High hardness, wear resistance, ideal for cutting tools |
Aluminum Alloys | Aluminum, Copper, Magnesium, Silicon, Zinc | Lightweight, high strength-to-weight ratio, good corrosion resistance |
Titanium Alloys | Titanium, Aluminum, Vanadium | Exceptional strength, lightweight, excellent corrosion resistance |
Characteristics of Forging Grade Materials
Each forging grade material has unique characteristics that make it suitable for specific applications. Let’s delve into these characteristics:
Carbon Steel
- Strength: High tensile strength and good impact resistance.
- Ductility: Excellent formability, making it easy to work with.
- Cost: Economical, making it a popular choice for many applications.
Alloy Steel
- Toughness: Enhanced toughness due to the presence of alloying elements.
- Wear Resistance: Superior resistance to wear and abrasion.
- Strength: Higher strength compared to carbon steel.
Stainless Steel
- Corrosion Resistance: Excellent resistance to rust and corrosion.
- Strength: Good mechanical properties, maintaining strength at high temperatures.
- Aesthetic Appeal: Attractive finish, making it suitable for decorative applications.
Tool Steel
- Hardness: High hardness and wear resistance, ideal for cutting tools.
- Heat Resistance: Can withstand high temperatures without losing hardness.
- Durability: Long-lasting performance in demanding applications.
Aluminum Alloys
- Lightweight: Low density, making it ideal for weight-sensitive applications.
- Strength-to-Weight Ratio: High strength relative to its weight.
- Corrosion Resistance: Good resistance to corrosion in various environments.
Titanium Alloys
- Strength: Exceptional strength, even at high temperatures.
- Lightweight: Lower density compared to steel and other metals.
- Corrosion Resistance: Excellent resistance to corrosion, particularly in marine environments.
Specific Metal Powder Models for Forging
Metal powders are essential in the production of forging grade materials, offering precision and consistency. Here are ten specific metal powder models used in forging:
1. 316L Stainless Steel Powder
- Composition: Iron, Chromium, Nickel, Molybdenum
- Properties: Excellent corrosion resistance, good mechanical properties
- Applications: Medical implants, marine environments
2. 17-4 PH Stainless Steel Powder
- Composition: Iron, Chromium, Nickel, Copper
- Properties: High strength, corrosion resistance, good mechanical properties
- Applications: Aerospace, chemical processing
3. H13 Tool Steel Powder
- Composition: Iron, Carbon, Chromium, Molybdenum, Vanadium
- Properties: High hardness, excellent toughness, good heat resistance
- Applications: Die casting, extrusion tools
4. 6061 Aluminum Alloy Powder
- Composition: Aluminum, Magnesium, Silicon
- Properties: High strength-to-weight ratio, good corrosion resistance
- Applications: Aerospace, automotive parts
5. 7075 Aluminum Alloy Powder
- Composition: Aluminum, Zinc, Magnesium, Copper
- Properties: Very high strength, good fatigue resistance
- Applications: Aircraft structures, high-stress components
6. Ti-6Al-4V Titanium Alloy Powder
- Composition: Titanium, Aluminum, Vanadium
- Properties: High strength, lightweight, excellent corrosion resistance
- Applications: Aerospace, biomedical implants
7. M2 High-Speed Steel Powder
- Composition: Iron, Carbon, Tungsten, Molybdenum, Vanadium, Chromium
- Properties: High hardness, excellent wear resistance, good toughness
- Applications: Cutting tools, drill bits
8. 4140 Alloy Steel Powder
- Composition: Iron, Carbon, Chromium, Molybdenum
- Properties: High toughness, good wear resistance, high fatigue strength
- Applications: Automotive parts, heavy machinery
9. 2024 Aluminum Alloy Powder
- Composition: Aluminum, Copper, Magnesium, Manganese
- Properties: High strength, good fatigue resistance, lightweight
- Applications: Aircraft structures, military applications
10. A2 Tool Steel Powder
- Composition: Iron, Carbon, Chromium, Molybdenum, Vanadium
- Properties: High hardness, good wear resistance, air-hardening
- Applications: Die casting, plastic molds
Applications of Forging Grade Materials
Forging grade materials are used across various industries due to their excellent mechanical properties and durability. Here are some common applications:
Industry | Application |
---|---|
Automotive | Crankshafts, connecting rods, gears, suspension components |
Aerospace | Aircraft frames, engine components, landing gear |
Industrial Machinery | Heavy-duty machinery parts, hydraulic systems, mining equipment |
Medical | Surgical instruments, implants, prosthetics |
Construction | Structural components, fasteners, reinforcement bars |
Oil & Gas | Drill bits, valves, fittings, pipelines |
Marine | Shipbuilding components, marine fasteners, propeller shafts |
Defense | Military vehicles, weapon components, armor plating |
Specifications, Sizes, Grades, and Standards
The specifications and standards for forging grade materials vary based on the industry and application. Here’s a detailed table summarizing these details:
Material | Specifications | Sizes | Grades | Standards |
---|---|---|---|---|
Carbon Steel | ASTM A105, AISI 1018 | Custom sizes available | 1018, 1045, 1095 | ASTM, SAE, AISI |
Alloy Steel | ASTM A182, AISI 4140 | Custom sizes available | 4140, 4340, 8620 | ASTM, SAE, AISI |
Stainless Steel | ASTM A182, AISI 316L | Custom sizes available | 304, 316, 410 | ASTM, SAE, AISI |
Tool Steel | ASTM A681, AISI H13 | Custom sizes available | H13, D2, A2 | ASTM, SAE, AISI |
Aluminum Alloys | ASTM B211, AA 6061 | Custom sizes available | 2024, 6061, 7075 | ASTM, SAE, AA |
Titanium Alloys | ASTM B348, Ti-6Al-4V | Custom sizes available | Grade 5, Grade 9 | ASTM, SAE, AMS |
Suppliers and Pricing Details
The suppliers and pricing of forging grade materials can vary significantly. Here’s a table highlighting some of the key suppliers and their pricing details:
Supplier | Material | Pricing (per kg) | Notes |
---|---|---|---|
Metals Depot | Carbon Steel, Alloy Steel | $1.50 – $5.00 | Bulk discounts available |
Online Metals | Stainless Steel, Tool Steel | $3.00 – $8.00 | Custom cutting services offered |
McMaster-Carr | Aluminum Alloys, Tool Steel | $2.00 – $10.00 | Wide range of sizes and grades |
Titanium Industries | Titanium Alloys | $20.00 – $40.00 | Specialized in aerospace materials |
Industrial Metal Supply | Carbon Steel, Stainless Steel | $1.80 – $7.00 | Fast shipping options available |
Comparing Pros and Cons of Forging Grade Materials
When selecting forging grade materials, it’s crucial to weigh the pros and cons. Here’s a comparative table:
Material | Advantages | Limitations |
---|---|---|
Carbon Steel | High strength, cost-effective, versatile | Prone to rust, lower corrosion resistance |
Alloy Steel | Improved toughness, wear resistance, higher strength | More expensive than carbon steel, requires heat treatment |
Stainless Steel | Excellent corrosion resistance, durable, good aesthetic appeal | Higher cost, can be difficult to machine |
Tool Steel | High hardness, wear resistance, ideal for cutting tools | Brittle, requires precise heat treatment |
Aluminum Alloys | Lightweight, good strength-to-weight ratio, corrosion resistance | Lower strength compared to steel, more expensive |
Titanium Alloys | Exceptional strength, lightweight, excellent corrosion resistance | Very expensive, difficult to machine |
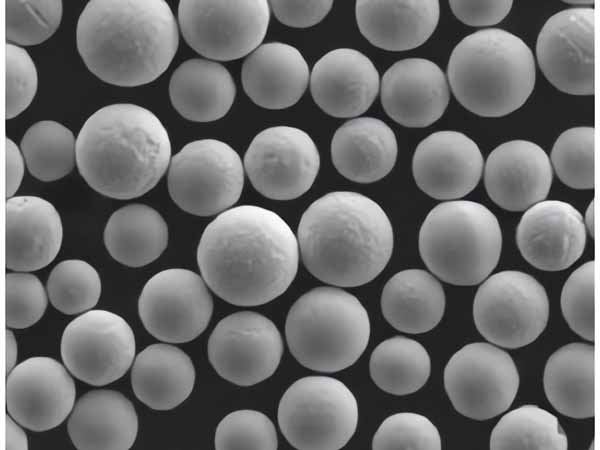
FAQs
Question | Answer |
---|---|
What are forging grade materials? | Metals and alloys designed for the forging process, known for their superior mechanical properties. |
Why are alloy steels used in forging? | They offer enhanced toughness, wear resistance, and strength due to the addition of alloying elements. |
What is the best material for aerospace applications? | Titanium alloys, due to their high strength, lightweight, and excellent corrosion resistance. |
How does stainless steel resist corrosion? | The presence of chromium forms a passive layer of chromium oxide on the surface, preventing rust. |
Are aluminum alloys suitable for high-stress applications? | Yes, especially grades like 7075, which have very high strength and good fatigue resistance. |
What is tool steel used for? | Used for making cutting and forming tools due to its high hardness and wear resistance. |
How are metal powders used in forging? | They offer precision and consistency in producing forging grade materials. |
What are the main applications of forging grade materials? | Automotive, aerospace, industrial machinery, medical, construction, oil & gas, marine, and defense. |
How does carbon content affect steel properties? | Higher carbon content increases strength and hardness but reduces ductility. |
What standards apply to forging grade materials? | Common standards include ASTM, SAE, AISI, AMS, and AA, ensuring consistency and quality in materials. |
Conclusion
Choosing the right forging grade material is crucial for ensuring the durability, strength, and performance of your products. By understanding the types, compositions, properties, and specific metal powder models, you can make an informed decision tailored to your specific needs. Whether you’re in the automotive, aerospace, or medical field, selecting the appropriate forging material can significantly impact the success and longevity of your applications.