Gas atomized powder is a versatile material with applications across many industries. This article provides a thorough overview of gas atomized powder, including its composition, properties, production methods, applications, suppliers, and more.
What is Gas Atomized Powder?
Gas atomized powder, also known as gas atomization powder, is a metal powder produced through a process called gas atomization. In gas atomization, molten metal is broken up into fine droplets and rapidly solidified with cold, high-pressure gas streams. This produces a consistent, spherical metal powder optimal for industrial applications.
The gas atomization process allows precise control over powder characteristics like particle size distribution, shape, purity, and internal structure. Compared to other metal powder production methods, gas atomized powders have more uniform particle sizes, higher densities, lower contamination, and better flowability.
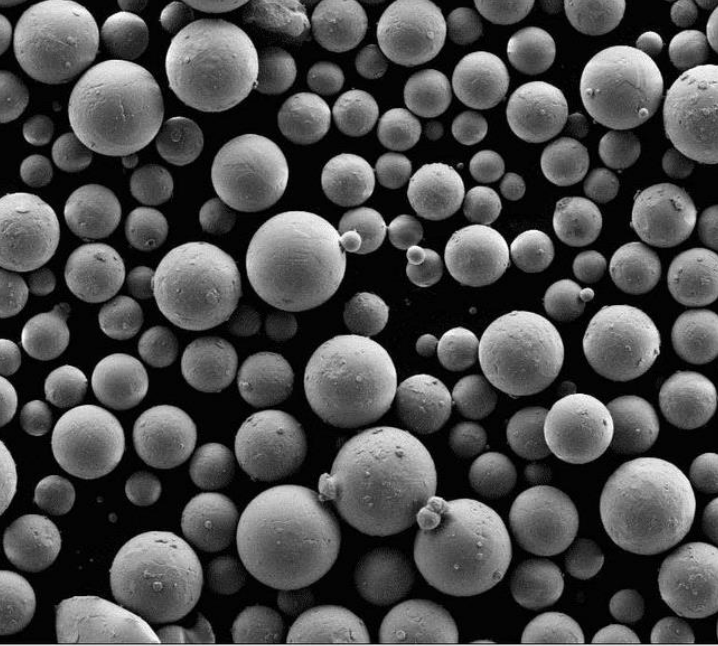
Gas Atomized Powder Composition
Gas atomized powders can be produced from various metals and alloys including:
- Stainless steel
- Tool steel
- Cobalt alloys
- Copper alloys
- Aluminum alloys
- Titanium alloys
- Nickel alloys
- Special alloys
The most commonly gas atomized materials are stainless steels, carbon steels, and nickel-based superalloys.
The composition can be customized to achieve specific material properties by carefully controlling the ratios of metals in the liquid alloy. Common alloying elements include chromium, nickel, molybdenum, manganese, and silicon.
Material | Typical Composition |
---|---|
Stainless Steel | Iron, Chromium, Nickel |
Tool Steel | Iron, Carbon, Chromium, Tungsten, Molybdenum |
Cobalt Alloy | Cobalt, Chromium, Tungsten |
Copper Alloy | Copper, Zinc |
Aluminum Alloy | Aluminum, Magnesium, Silicon |
Titanium Alloy | Titanium, Aluminum, Vanadium |
Nickel Alloy | Nickel, Chromium, Iron |
Gas Atomized Powder Properties
Gas atomized powders have many unique properties that make them suitable for specialty applications:
Particle Shape: Spherical and semi-spherical shape allows excellent metallurgical bonding and material performance. The consistent morphology enables precise additive manufacturing.
Particle Size: Typically 10 to 150 microns. Narrow distribution ensures homogeneous properties and quality. Smaller sizes have better flow and packing density.
Internal Structure: Rapid cooling rate creates finer uniform grain structure leading to outstanding properties. Some materials have fully amorphous structures.
Composition: No contamination from oxidation or atmosphere exposure during production. Alloying additions are fully dissolved.
Density: Up to 98% of theoretical density allows full utilization of superior alloy properties.
Surface Area: Higher surface area increases chemical activity for applications like catalysis.
In summary, gas atomized powders have clean chemistry, spherical morphology, narrow size distribution, high purity, lack of satellites, controlled internal structure, and adjustable alloy compositions.
Property | Description | Significance |
---|---|---|
Particle Shape | Spherical | Excellent flowability, packing density, metallurgical bonding |
Particle Size | 10 – 150 μm typical | Controls application method, density, properties |
Particle Size Distribution | Narrow | Consistent, homogeneous quality and performance |
Internal Structure | Fine grain, uniform, amorphous possible | Outstanding mechanical properties and performance |
Composition | No contamination or oxidation | Utilizes full benefit of alloying additions |
Density | Up to 98% theoretical | Maximizes strength and functionality |
Surface Area | Relatively high | Improves chemical reactivity |
Gas Atomized Powder Production
Gas atomized powder production involves melting, atomization, cooling/solidification, and sieving:
Melting: The raw materials are carefully weighted and loaded into a vacuum induction melting furnace. They are melted under inert atmosphere into a homogeneous liquid alloy.
Atomization: The liquid alloy is poured in a thin stream into the atomization tower where high velocity gas jets break it into fine droplets. Various gas nozzle designs control powder sizes and shapes. Nitrogen, argon or helium gas is used depending on the material.
Cooling and Solidification: The droplets rapidly solidify into powder form as they fall though the cooling chamber, with fine microstructures developing from the rapid temperature drop.
Sieving and Classification: Finally, the powder is collected and sieved into different size classifications as per application requirements. It may also undergo further annealing or Hot Isostatic Pressing.
The entire gas atomization process happens in closed, controlled atmospheres to prevent contamination of reactive alloys. Operational parameters like gas pressure, flow rates and alloy superheat can be optimized to produce powders with desired characteristics.
The high productivity of gas atomization lines allows cost-effective production of powder even for exotic, expensive alloys. Automated batch-to-batch repeatability ensures consistent powder quality. Overall, gas atomized powder has the most precisely controlled production process among all metal powder types.
Gas Atomized Powder Industry Applications
Some major industrial applications of gas atomized metal powder include:
Additive Manufacturing
- Selective Laser Melting (SLM)
- Direct Metal Laser Sintering (DMLS)
- Binder Jetting
- Electron Beam Melting (EBM)
Metal Injection Molding
Hot Isostatic Pressing
Thermal Spraying
Brazing and Soldering
Catalysts
The unique properties of gas atomized powder enable emerging technologies and cutting-edge applications across sectors:
Industry | Applications | Benefits |
---|---|---|
Aerospace | Turbine blades, airfoils, jet engine components, space vehicles | High strength, heat resistance, weldability |
Medical | Orthopedic implants, prosthetics, surgical tools | Biocompatibility, corrosion resistance |
Automotive | Connecting rods, drive shafts, gears, fasteners | Wear resistance, fatigue strength |
Electronics | Shielding, contacts, leadframes, sensors | Electrical conductivity, thermal properties |
Oil & Gas | Downhole tools, valves, pipelines | High toughness, corrosion resistance |
Energy | Generators, batteries, solar cells, nuclear reactors | Advanced alloys, microstructures |
In particular, gas atomized powders have seen massive adoption in metal additive manufacturing across industries due to their spherical morphology, excellent flowability, and precise size control.
Gas Atomized Powder Suppliers
Some leading global suppliers of gas atomized metal powder include:
- Sandvik Osprey
- Carpenter Additive
- Praxair
- Hoganas
- LPW Technology
- Erasteel
- PyroGenesis Canada
- Kennametal Stellite
These companies offer various standard grades as well as custom gas atomized powders tailored to client requirements:
Supplier | Materials Available | Typical Sizes | Common Applications |
---|---|---|---|
Sandvik Osprey | Stainless steels, tool steels, nickel superalloys | 15-150 μm | Additive manufacturing, MIM |
Carpenter Additive | Stainless steels, cobalt and nickel superalloys | 10-106 μm | Aerospace components, medical implants |
Praxair | Titanium, nickel, stainless steel | 10-150 μm | Thermal spray coatings |
Hoganas | Stainless steels, tool steels | 15-45 μm | Metal injection molding |
LPW Technology | Titanium alloys, nickel alloys | 15-45 μm | Precision investment casting |
Erasteel | Tool steels, stainless steels | 10-250 μm | Additive manufacturing |
PyroGenesis | Titanium alloys, refractory metals, superalloys | 45-150 μm | Aerospace applications |
Kennametal Stellite | Cobalt alloys, nickel alloys | 45-150 μm | Wear resistant coatings |
Buying gas atomized powder starts by selecting a supplier that makes the required material in suitable specifications. It is critical to obtain a product datasheet confirming composition, size range, shape and production method before purchasing.
Gas Atomized Powder Cost Analysis
Like most specialty metallic materials, gas atomized powder pricing has significant variability based on factors like:
- Alloy composition – More exotic or custom alloys can cost over $500/kg
- Material type – Superalloys are far more expensive than stainless steels
- Powder morphology – Spherical powders made via gas atomization have a premium over irregular powders
- Particle size – Finer sizes below 45 microns attract higher pricing
- Order quantity – Small lab trial orders may cost 5X more per kg
- Testing and certification – Extensive QA testing and powder certification adds cost
- Buyer location – Global supply chain logistics impact final delivered pricing
Indicative price ranges for common gas atomized alloy groups are:
Material Group | Typical Price Range |
---|---|
Stainless Steels | $50 – $150 per kg |
Tool Steels | $50 – $100 per kg |
Cobalt Alloys | $100 – $250 per kg |
Nickel Alloys | $100 – $500 per kg |
Titanium Alloys | $200 – $600 per kg |
Refractory Alloys | $500 – $2000 per kg |
Spherical gas atomized powder suitable for additive manufacturing sees significant pricing premiums across all alloy types due to stringent size distribution and purity requirements.
Cost Saving Opportunities:
- Order economical 10 kg packs instead of 500g lab samples
- Share trial material with industry peers to split costs
- Purchase irregular powder instead of spherical if possible
- Use powder recycling systems to reuse oversize/undersize fractions
- Inquire about toll processing to convert raw materials into powder
Understanding application requirements and powder characteristics is necessary to identify the optimal balance of material properties and pricing.
Gas Atomized Powder: Pros vs Cons
Advantages of Gas Atomized Powder:
- Excellent sphericity and flowability
- Narrow particle size distribution
- High purity with no contamination
- Controlled dense internal structure
- Suitable for additive manufacturing
- Customizable alloys and properties
- Consistent batch-to-batch quality
- Cost-effective production of novel alloys
Limitations of Gas Atomized Powder:
- Relatively high pricing
- Limited sizes below 10 microns
- May still require thermal post processing
- Lower packing density than irregular powder
- Handling fine reactive powders requires care
- Limited suppliers for specialty alloys
- Exotic compositions difficult to atomize
Gas atomization is the premier powder production technology despite its operational complexity and specialty equipment requirements. The process refinement over decades results in exceptional quality and capabilities unattainable via other methods.
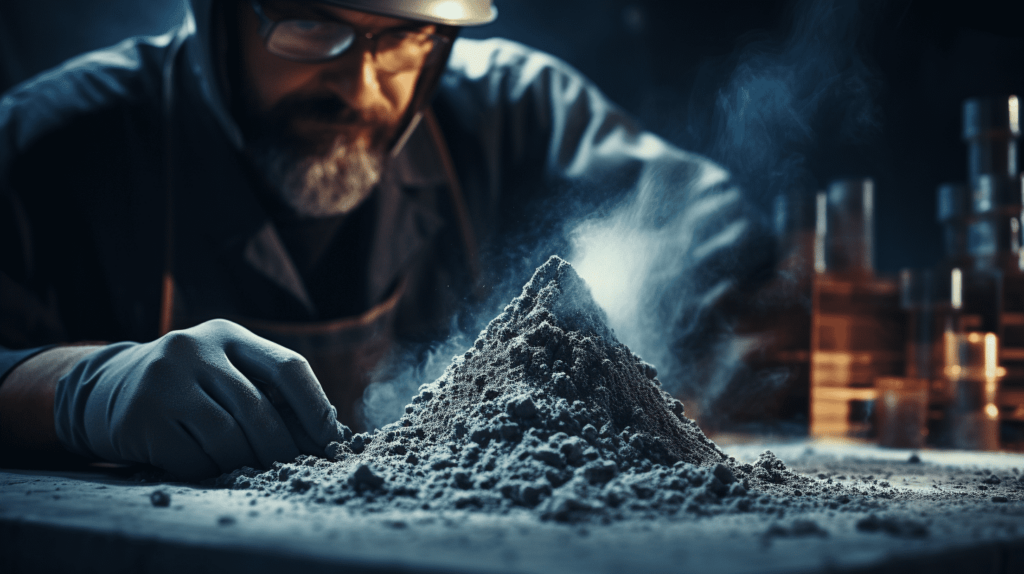
FAQ
Q: How is gas atomized powder made?
A: Gas atomized powder is made by melting the raw materials into an alloy which is then broken into fine droplets by high velocity inert gas jets. The droplets rapidly solidify into powder.
Q: What particle shapes are produced in gas atomization?
A: Gas atomization typically produces highly spherical or rounded semi-spherical powder particles with very smooth surfaces.
Q: What particle sizes can be achieved with gas atomized powder?
A: Conventional gas atomized powders range from around 10 microns to 150 microns. Specialized atomization can produce sizes below 5 microns.
Q: Which materials can be gas atomized into powder?
A: Most commercial alloys like stainless steels, tool steels, superalloys, titanium alloys and refractory alloys can be gas atomized with the right process controls.
Q: Is gas atomized powder reusable?
A: Yes, unused gas atomized powder can usually be recovered, sieved and reused. However, contamination must be avoided in handling and storage.
Q: Is gas atomized powder cheaper than virgin alloy materials?
A: No, gas atomized powder is far more expensive due to specialized production. Raw alloy material costs account for only 30% of powder value – processing adds substantial cost.
Q: What are the main applications of gas atomized powder?
A: The major applications are additive manufacturing, metal injection molding, thermal spraying, and powder metallurgy pressing. The spherical morphology also improves sintering, alloy development and porous structures.
Q: How should gas atomized powder be safely handled?
A: Gas atomized powders may be flammable or sensitizing. Care should be taken during transportation, storage and handling to control exposure. Water atomized powders are less hazardous alternatives.
Q: What is the shelf life of gas atomized powder?
A: If properly stored in sealed containers under inert atmosphere, gas atomized powder can last several years without degradation. Improper storage causing oxidation or moisture exposure will negatively impact powder properties and performance.
Conclusion
With unparalleled quality and unique material properties, gas atomized powder offers new potential for designing cutting-edge components across every industry. As additive manufacturing and alloy development continues rapidly advancing, so will novel uses for this special form of material. However, tangible commercial impact relies on powder manufacturers engaging early with end users to deploy their expertise. Through collaboration, gas atomized powder can transcend its reputation as an exotic, expensive material and take center stage enabling emerging technologies to transform how the world is made.