Gas turbines are at the heart of numerous industrial applications, from power generation to aerospace. One critical aspect of gas turbine technology is the materials used in their construction. Among these, gas turbine engineering powders play a vital role in manufacturing components that can withstand extreme conditions such as high temperatures and pressures. This article will delve deep into the world of gas turbine engineering powder, providing an overview, detailed descriptions of specific metal powder models, and insights into their applications, compositions, and characteristics.
Overview of Gas Turbine Engineering Powder
Gas turbine engineering powders are specialized materials designed for the production of high-performance turbine components. These powders, often made from superalloys and other advanced materials, are engineered to meet the rigorous demands of gas turbines. The manufacturing of these powders involves a variety of processes, including atomization, reduction, and alloying, to ensure they meet specific industry standards and performance requirements.
Key Points:
- Purpose: Used in the production of gas turbine components like blades, vanes, and combustion chambers.
- Materials: Primarily superalloys (Nickel-based, Cobalt-based), stainless steel, titanium alloys, and ceramics.
- Processes: Atomization, reduction, sintering, hot isostatic pressing (HIP), and additive manufacturing.
- Applications: Power generation, aerospace, marine propulsion, and oil & gas industries.
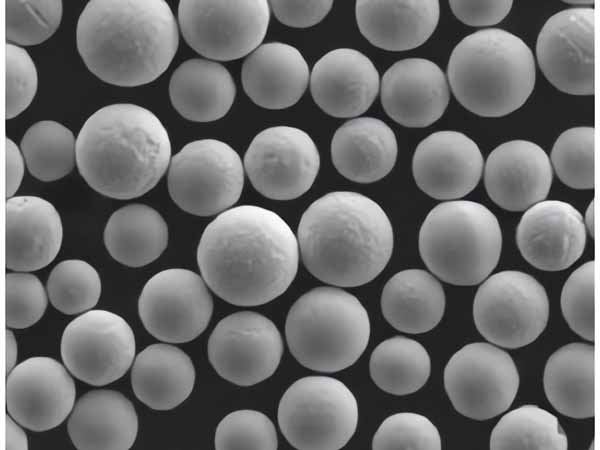
Types, Composition, and Properties of Gas Turbine Engineering Powders
Powder Model | Material Composition | Properties | Applications | Notable Characteristics |
---|---|---|---|---|
IN718 | Nickel-Chromium alloy with Iron, Niobium, Molybdenum | High tensile strength, good weldability | Turbine blades, discs | Excellent creep resistance |
Rene 88DT | Nickel-based superalloy with Cobalt, Chromium, Tungsten | High fatigue resistance, superior strength at high temperatures | High-pressure turbine discs | Optimal for high-stress environments |
CMSX-4 | Nickel-based single-crystal alloy with Rhenium, Tantalum | Outstanding creep strength, high melting point | Turbine blades, vanes | Exceptional for high-temperature applications |
Hastelloy X | Nickel-Chromium-Molybdenum alloy | Good oxidation resistance, high-temperature strength | Combustion chambers | Excellent for corrosive environments |
CoCrMo | Cobalt-Chromium-Molybdenum alloy | High wear resistance, biocompatibility | Gas turbine bearings | Ideal for components requiring high wear resistance |
Ti-6Al-4V | Titanium alloy with Aluminum, Vanadium | High strength-to-weight ratio, excellent corrosion resistance | Low-pressure turbine blades, casings | Lightweight and strong |
Haynes 282 | Nickel-based superalloy with Chromium, Molybdenum | Excellent thermal stability, good weldability | Turbine discs, cases | Ideal for long-life components |
Mar-M247 | Nickel-based superalloy with Cobalt, Chromium, Aluminum | High creep strength, corrosion resistance | Turbine blades, vanes | Used in extreme environments |
Inconel 625 | Nickel-Chromium-Molybdenum alloy | Excellent fatigue resistance, oxidation resistance | Exhaust systems, turbine seals | Performs well in extreme heat |
Stellite 6B | Cobalt-Chromium alloy with Tungsten | High hardness, wear resistance | Valve seats, bearings | Superior wear and galling resistance |
Composition of Gas Turbine Engineering Powder
The composition of gas turbine engineering powders is meticulously engineered to meet the specific demands of turbine components. The materials used in these powders often include superalloys, which are primarily based on Nickel, Cobalt, or Iron. These alloys are chosen for their ability to maintain mechanical strength at high temperatures, resist oxidation and corrosion, and provide overall durability under extreme conditions.
Key Components:
- Nickel (Ni): Nickel-based superalloys are the most common due to their excellent high-temperature strength and oxidation resistance. These alloys often contain Chromium (Cr), Molybdenum (Mo), Aluminum (Al), and Titanium (Ti) as additional elements to enhance performance.
- Cobalt (Co): Cobalt-based superalloys are used where high wear resistance is needed, such as in turbine blades and vanes. These alloys are known for their ability to retain strength at elevated temperatures.
- Iron (Fe): Although less common, Iron-based superalloys are used in some applications where cost and manufacturability are more critical than extreme temperature performance.
- Ceramics: In some cases, ceramic powders are used for specific turbine components that require extreme temperature resistance without the need for significant mechanical strength, such as thermal barrier coatings.
Common Elements in Gas Turbine Engineering Powders and Their Functions
Element | Function | Common Applications | Notable Alloys |
---|---|---|---|
Nickel (Ni) | Provides high-temperature strength, oxidation resistance | Turbine blades, discs | IN718, CMSX-4, Mar-M247 |
Chromium (Cr) | Enhances corrosion resistance, oxidation resistance | Combustion chambers, turbine vanes | Inconel 625, Hastelloy X |
Cobalt (Co) | Increases wear resistance, provides strength at high temperatures | Bearings, valve seats | CoCrMo, Stellite 6B |
Molybdenum (Mo) | Improves creep strength, corrosion resistance | High-temperature turbine components | Haynes 282, Hastelloy X |
Aluminum (Al) | Adds oxidation resistance, forms protective oxide layer | Turbine blades, casings | IN718, Ti-6Al-4V |
Titanium (Ti) | Provides high strength-to-weight ratio, enhances corrosion resistance | Low-pressure turbine components | Ti-6Al-4V |
-
CM247LC Powder | Nickel Alloy Powder
-
0# Pure Nickel powder
-
NiCoCrAlY alloys powders
-
Rene 142 alloy-Rene Powder
-
Haynes 25 Haynes Powder
-
Best Hastelloy C-22 Powder-High temperature alloy Powder for 3D Printing
-
Best Hastelloy C-276 Powder-High temperature alloy Powder for 3D Printing
-
Best Hastelloy N Powder-High temperature alloy Powder for 3D Printing
-
Best Hastelloy B Powder丨High temperature alloy Powder for 3D Printing
Characteristics of Gas Turbine Engineering Powder
Gas turbine engineering powders possess a range of characteristics that make them suitable for manufacturing high-performance turbine components. These characteristics are critical in determining the suitability of a particular powder for a given application.
Key Characteristics:
- Particle Size Distribution:
- A critical factor affecting the powder’s flowability and packing density, influencing the final component’s mechanical properties.
- Morphology:
- The shape and surface texture of the powder particles can impact the sintering process and the resulting microstructure of the manufactured component.
- Purity:
- High purity levels are essential to avoid contamination that can lead to premature failure of the component.
- Density:
- The bulk and tap density of the powder affect how it behaves during processing, particularly in additive manufacturing and hot isostatic pressing (HIP).
- Oxidation Resistance:
- Powders are often designed to resist oxidation during processing and in the final component to ensure long-term performance at high temperatures.
Key Characteristics of Gas Turbine Engineering Powders
Characteristic | Description | Impact on Application |
---|---|---|
Particle Size Distribution | Range and distribution of particle sizes | Affects flowability, packing density, and mechanical properties |
Morphology | Shape and surface texture of particles | Influences sintering, final microstructure |
Purity | Level of contaminants present | Affects overall performance and durability |
Density | Bulk and tap density of powder | Influences processing behavior and component integrity |
Oxidation Resistance | Ability to resist oxidation | Critical for high-temperature performance |
Advantages of Gas Turbine Engineering Powder
The use of gas turbine engineering powders offers numerous advantages, particularly when compared to traditional manufacturing methods or other materials. These advantages make them indispensable in the production of turbine components.
Key Advantages:
- Enhanced Material Properties:
- Gas turbine powders are specifically engineered to provide superior high-temperature strength, corrosion resistance, and oxidation resistance compared to bulk materials.
- Flexibility in Manufacturing:
- Powders can be used in various manufacturing processes, including additive manufacturing, powder metallurgy, and HIP, allowing for complex geometries and optimized component designs.
- Cost-Effectiveness:
- Although the initial cost of powders may be higher, the ability to produce near-net-shape components reduces material waste and machining time, leading to overall cost savings.
- Customization:
- The composition of powders can be tailored to meet specific application requirements, allowing for the development of materials with unique properties.
- Improved Performance:
- Components made from these powders often exhibit improved performance characteristics, such as higher creep resistance, longer fatigue life, and better thermal stability.
Advantages of Gas Turbine Engineering Powders Compared to Traditional Materials
Advantage | Description | Comparison with Traditional Materials |
---|---|---|
Enhanced Material Properties | Superior high-temperature strength, corrosion resistance | Traditional materials often lack the same level of performance under extreme conditions |
Flexibility in Manufacturing | Supports advanced processes like additive manufacturing | Traditional methods may be limited in terms of design complexity |
Cost-Effectiveness | Reduces material waste, machining time | Bulk materials often require extensive machining, leading to higher costs |
Customization | Tailored compositions for specific applications | Traditional materials are less adaptable to unique application needs |
Improved Performance | Better creep resistance, fatigue life, thermal stability | Traditional materials may degrade faster under similar conditions |
Applications of Gas Turbine Engineering Powder
Gas turbine engineering powders are used in a wide range of applications across various industries. Their unique properties make them ideal for manufacturing components that must withstand extreme conditions.
Primary Applications:
- Aerospace:
- Used in the production of turbine blades, vanes, and combustion chambers for aircraft engines, where high strength and resistance to thermal fatigue are critical.
- Power Generation:
- Essential for manufacturing components of industrial gas turbines used in power plants, particularly in high-temperature areas like the hot section of the turbine.
- Marine Propulsion:
- Utilized in the construction of gas turbines for naval vessels, providing reliable performance in harsh marine environments.
- Oil & Gas:
- Employed in turbines used for oil and gas extraction and processing, where resistance to corrosion and oxidation is essential.
- Additive Manufacturing:
- Increasingly used in 3D printing of complex turbine components, allowing for greater design flexibility and rapid prototyping.
Applications of Gas Turbine Engineering Powders
Industry | Component | Powder Model Used | Key Requirements |
---|---|---|---|
Aerospace | Turbine Blades | IN718, Rene 88DT | High-temperature strength, fatigue resistance |
Power Generation | Combustion Chambers | Hastelloy X, Inconel 625 | Oxidation resistance, thermal stability |
Marine Propulsion | Turbine Blades, Vanes | Mar-M247, CMSX-4 | Corrosion resistance, creep strength |
Oil & Gas | Bearings, Seals | CoCrMo, Stellite 6B | Wear resistance, high hardness |
Additive Manufacturing | Complex Turbine Components | Ti-6Al-4V, Haynes 282 | Design flexibility, rapid prototyping |
Specifications, Sizes, Grades, and Standards of Gas Turbine Engineering Powder
Understanding the specifications, sizes, grades, and standards of gas turbine engineering powders is crucial for ensuring that the right material is chosen for a specific application. These parameters are defined by industry standards and are critical for the performance and reliability of the final components.
Specifications:
- Particle Size Distribution:
- Common ranges: 15-45 µm, 45-106 µm, depending on the application and manufacturing process.
- Purity:
- Typically >99.9% for critical applications to avoid contamination and ensure material integrity.
- Density:
- Bulk density and tap density are often specified to ensure proper packing and processing behavior.
- Morphology:
- Spherical particles are preferred for additive manufacturing, while irregular shapes may be used in other processes.
Specifications and Standards for Gas Turbine Engineering Powders
Specification | Description | Typical Range/Standard |
---|---|---|
Particle Size Distribution | Size range of powder particles | 15-45 µm, 45-106 µm |
Purity | Level of material purity | >99.9% |
Density | Bulk and tap density | Varies by material |
Morphology | Shape and texture of particles | Spherical, irregular |
Standards | Industry standards for material properties | ASTM B214, ISO 4499-1 |
Suppliers and Pricing Details for Gas Turbine Engineering Powder
Several suppliers specialize in providing high-quality gas turbine engineering powders, each offering a range of products tailored to specific applications. Pricing can vary based on the material, particle size distribution, and the volume of purchase.
Suppliers and Pricing for Gas Turbine Engineering Powders
Supplier | Powder Model | Pricing (Per kg) | Available Sizes | Contact Information |
---|---|---|---|---|
Carpenter Technology | IN718, Rene 88DT | $300 – $500 | 15-45 µm, 45-106 µm | www.carpentertechnology.com |
Praxair Surface Technologies | CMSX-4, Hastelloy X | $250 – $450 | 20-63 µm | www.praxairsurfacetechnologies.com |
ATI Metals | CoCrMo, Ti-6Al-4V | $200 – $400 | 10-53 µm, 45-106 µm | www.atimetals.com |
Sandvik Osprey | Haynes 282, Mar-M247 | $280 – $480 | 15-45 µm, 20-63 µm | www.materials.sandvik |
Höganäs AB | Inconel 625, Stellite 6B | $220 – $420 | 10-53 µm | www.hoganas.com |
Comparison of Gas Turbine Engineering Powders: Pros and Cons
When choosing the right gas turbine engineering powder, it’s essential to weigh the advantages and limitations of each option. Different powders offer varying benefits in terms of strength, corrosion resistance, ease of manufacturing, and cost.
Comparing Pros and Cons of Common Gas Turbine Engineering Powders
Powder Model | Advantages | Limitations | Best For |
---|---|---|---|
IN718 | High strength, good weldability | Expensive, complex processing | Turbine blades, discs |
Rene 88DT | Excellent fatigue resistance | Difficult to machine | High-stress turbine discs |
CMSX-4 | Superior high-temperature performance | Costly, limited availability | High-temperature turbine blades |
Hastelloy X | Good oxidation resistance | Lower strength compared to other superalloys | Combustion chambers |
CoCrMo | High wear resistance | Not as strong at high temperatures | Bearings, valve seats |
Ti-6Al-4V | Lightweight, corrosion-resistant | Lower high-temperature strength | Low-pressure turbine components |
Haynes 282 | Excellent thermal stability | Expensive, difficult to weld | Long-life turbine components |
Mar-M247 | High creep strength, corrosion-resistant | Brittle at lower temperatures | Extreme environment turbine blades |
Inconel 625 | Great oxidation resistance | Moderate creep resistance | Exhaust systems, turbine seals |
Stellite 6B | Superior wear resistance | Heavy, expensive | High-wear components like valve seats |
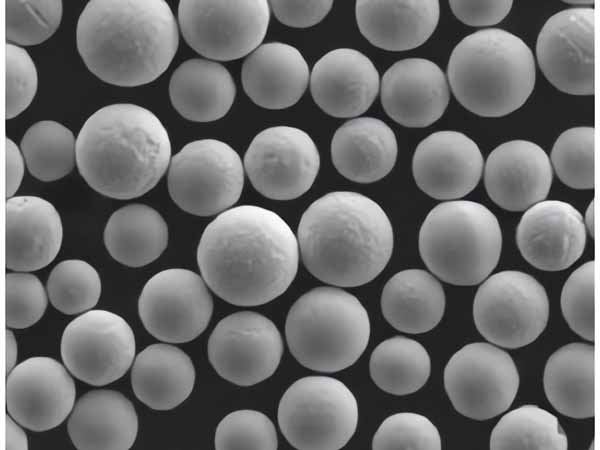
FAQ
Question | Answer |
---|---|
What are gas turbine engineering powders? | These are specialized materials used in the production of turbine components, designed to withstand extreme temperatures and pressures. |
Why are Nickel-based superalloys commonly used in gas turbines? | Nickel-based superalloys offer exceptional high-temperature strength and resistance to oxidation and corrosion, making them ideal for turbine applications. |
How is gas turbine powder manufactured? | Common methods include atomization, reduction, and alloying, with powders often being processed further using sintering, HIP, or additive manufacturing. |
What factors should be considered when selecting a gas turbine powder? | Key factors include the material’s high-temperature performance, oxidation resistance, particle size distribution, and cost. |
Can gas turbine powders be used in additive manufacturing? | Yes, many gas turbine powders are designed for use in additive manufacturing, allowing for the production of complex, high-performance components. |
How does particle size distribution affect the powder’s performance? | The size and distribution of powder particles influence flowability, packing density, and the mechanical properties of the final component. |
Are gas turbine engineering powders expensive? | These powders can be costly due to their specialized nature, but they offer cost savings through reduced waste and improved performance in critical applications. |
Which industries commonly use gas turbine engineering powders? | Industries such as aerospace, power generation, marine propulsion, and oil & gas rely heavily on these powders for manufacturing high-performance turbine components. |
Conclusion
Gas turbine engineering powders are a cornerstone of modern turbine technology, enabling the production of components that can endure the extreme environments of gas turbines. With a variety of options available, from Nickel-based superalloys to advanced ceramics, these powders offer the flexibility and performance needed across numerous industries. By understanding their composition, characteristics, and applications, engineers and manufacturers can make informed decisions to optimize their turbine components for maximum efficiency and durability.