Overview of Helium Plasma
Helium plasma, often referred to as the fourth state of matter, is a powerful tool in various high-tech industries, including semiconductors, medical devices, and surface treatments. Its unique properties, such as high energy density, low thermal conductivity, and the ability to create controlled environments for chemical reactions, make it indispensable in advanced manufacturing processes.
This article will delve into the intricate details of helium plasma, exploring its composition, characteristics, applications, and the specific metal powders that interact with it. We’ll compare different models of metal powders, discuss the pros and cons of using helium plasma in various applications, and provide a comprehensive FAQ section to address common queries.
Composition of Helium Plasma
Helium plasma is created by ionizing helium gas, which means adding enough energy to remove electrons from helium atoms. This ionization process results in a hot, electrically conductive gas where the charged particles (ions and electrons) are free to move. The composition of helium plasma is relatively simple, involving mainly helium ions, free electrons, and neutral helium atoms.
Table: Composition of Helium Plasma
Component | Description |
---|---|
Helium Ions (He⁺) | Positively charged helium atoms, essential for the plasma’s conductivity and reactivity. |
Free Electrons | Electrons that have been stripped from helium atoms, contributing to the plasma’s charge. |
Neutral Helium Atoms | Non-ionized helium atoms, which can absorb or release energy during plasma interactions. |
Helium plasma is prized for its stability and purity, as helium is an inert gas, meaning it does not readily react with other substances. This makes it ideal for applications where contamination must be minimized.
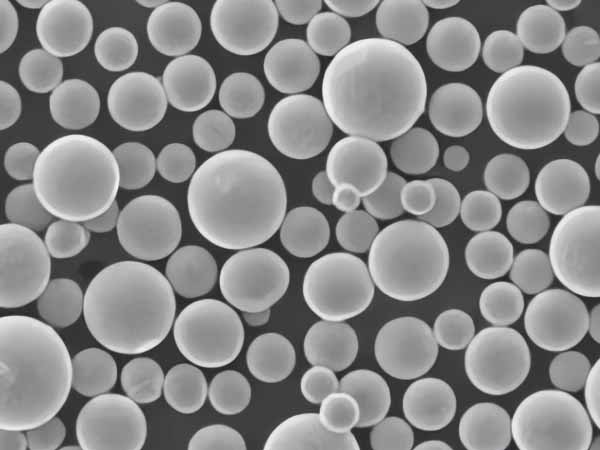
Characteristics of Helium Plasma
Understanding the characteristics of helium plasma is crucial for harnessing its potential in various applications. Below, we highlight some of the key characteristics:
1. High Energy Density
Helium plasma can reach temperatures of up to 20,000°C, making it incredibly effective for cutting, welding, and other high-energy processes. The high energy density allows for precise and efficient operations.
2. Low Thermal Conductivity
Unlike other plasmas, helium plasma has a low thermal conductivity, which helps concentrate heat in a specific area without affecting surrounding materials. This is particularly beneficial in processes requiring high precision.
3. Stability and Purity
Helium’s inert nature ensures that the plasma remains stable and pure, with minimal risk of contamination. This is essential in industries like semiconductors, where even a small amount of contamination can lead to defects.
Table: Key Characteristics of Helium Plasma
Characteristic | Description |
---|---|
Energy Density | High, allowing for precise cutting, welding, and other processes. |
Thermal Conductivity | Low, ensuring minimal impact on surrounding materials. |
Stability | Highly stable due to helium’s inert nature, minimizing contamination risks. |
Purity | High purity, critical for applications in sensitive industries. |
These characteristics make helium plasma a versatile tool across a range of industries, from aerospace to medical devices.
Applications of Helium Plasma
Helium plasma finds application in several cutting-edge fields due to its unique properties. Below are some of the primary uses:
1. Semiconductor Manufacturing
In semiconductor manufacturing, helium plasma is used in processes like dry etching and plasma-enhanced chemical vapor deposition (PECVD). Its high purity and stability are vital for creating precise and defect-free components.
2. Medical Device Sterilization
Helium plasma is employed in the sterilization of medical devices. Its ability to kill bacteria and viruses without damaging sensitive equipment makes it invaluable in the healthcare industry.
3. Surface Treatment
Helium plasma is used to modify the surfaces of materials to improve their adhesion properties, corrosion resistance, or other characteristics. This is particularly important in industries like automotive and aerospace.
Table: Applications of Helium Plasma
Application | Description |
---|---|
Semiconductor Manufacturing | Used in dry etching and PECVD for creating precise components with minimal defects. |
Medical Device Sterilization | Effective in sterilizing sensitive medical equipment without causing damage. |
Surface Treatment | Employed to enhance adhesion, corrosion resistance, and other surface properties in various materials. |
The versatility of helium plasma in these applications highlights its significance in modern technological advancements.
Specific Metal Powder Models for Helium Plasma
When it comes to using helium plasma in processes like additive manufacturing (3D printing), selecting the right metal powder is crucial. Different metal powders react uniquely with helium plasma, influencing the quality and properties of the final product. Below, we discuss ten specific metal powder models that are commonly used with helium plasma.
1. Titanium Alloy Powder (Ti-6Al-4V)
Description: Ti-6Al-4V is a widely used titanium alloy powder known for its high strength, lightweight, and excellent corrosion resistance. When used with helium plasma, it produces components with superior mechanical properties, making it ideal for aerospace applications.
2. Inconel 718 Powder
Description: Inconel 718 is a nickel-based superalloy powder that offers exceptional resistance to high temperatures and corrosion. Helium plasma enhances its strength and durability, making it suitable for turbine engines and other high-performance applications.
3. Stainless Steel Powder (316L)
Description: 316L stainless steel powder is known for its corrosion resistance and biocompatibility. When processed with helium plasma, it is often used in medical implants and surgical instruments due to its enhanced surface finish and strength.
4. Aluminum Alloy Powder (AlSi10Mg)
Description: AlSi10Mg is an aluminum alloy powder that offers good strength-to-weight ratio and excellent thermal properties. Helium plasma processing improves its surface finish, making it ideal for automotive and aerospace components.
5. Copper Powder (Cu-Cr-Zr)
Description: Copper powder, specifically Cu-Cr-Zr, is known for its excellent electrical conductivity and thermal properties. Helium plasma processing helps in creating components with superior electrical performance, often used in electronics and electrical systems.
6. Cobalt-Chromium Alloy Powder
Description: Cobalt-chromium alloy powder is highly resistant to wear and corrosion. Helium plasma processing enhances its hardness, making it ideal for dental implants and other medical applications.
7. Maraging Steel Powder (18Ni300)
Description: Maraging steel powder is known for its high strength and toughness. Helium plasma processing can significantly improve its mechanical properties, making it suitable for tooling and aerospace components.
8. Tungsten Carbide Powder (WC-Co)
Description: Tungsten carbide powder, often combined with cobalt, is used for its extreme hardness and wear resistance. Helium plasma processing is used to create cutting tools and wear-resistant coatings.
9. Nickel Alloy Powder (NiCr)
Description: Nickel alloy powder, particularly NiCr, is known for its high-temperature resistance and corrosion properties. Helium plasma processing enhances these characteristics, making it suitable for turbine blades and other high-temperature applications.
10. Tantalum Powder (Ta)
Description: Tantalum powder is highly corrosion-resistant and biocompatible. Helium plasma processing is used to create medical implants and electronic components due to its enhanced surface properties.
Table: Specific Metal Powder Models for Helium Plasma
Metal Powder Model | Description | Key Applications |
---|---|---|
Ti-6Al-4V | High strength, lightweight, excellent corrosion resistance. | Aerospace, medical implants |
Inconel 718 | Nickel-based superalloy with high-temperature and corrosion resistance. | Turbine engines, high-performance components |
316L Stainless Steel | Corrosion-resistant and biocompatible, with enhanced surface finish. | Medical implants, surgical instruments |
AlSi10Mg | Good strength-to-weight ratio, excellent thermal properties. | Automotive, aerospace |
Cu-Cr-Zr | Excellent electrical conductivity and thermal properties. | Electronics, electrical systems |
Cobalt-Chromium Alloy | High wear and corrosion resistance, with enhanced hardness. | Dental implants, medical devices |
18Ni300 Maraging Steel | High strength and toughness, with improved mechanical properties. | Tooling, aerospace |
WC-Co | Extreme hardness and wear resistance, used in cutting tools. | Cutting tools, wear-resistant coatings |
NiCr | High-temperature and corrosion resistance, with enhanced characteristics. | Turbine blades, high-temperature components |
Tantalum (Ta) | Highly corrosion-resistant and biocompatible, with enhanced surface properties. | Medical implants, electronics |
These metal powders, when processed with helium plasma, offer enhanced performance in various critical applications, ranging from aerospace to medical devices.
-
NiCoCrAlY alloys powders
-
Rene 142 alloy-Rene Powder
-
Haynes 25 Haynes Powder
-
Best Hastelloy C-22 Powder-High temperature alloy Powder for 3D Printing
-
Best Hastelloy C-276 Powder-High temperature alloy Powder for 3D Printing
-
Best Hastelloy N Powder-High temperature alloy Powder for 3D Printing
-
Best Hastelloy B Powder丨High temperature alloy Powder for 3D Printing
-
FGH95 Ni-base Alloy Powder | Nickel Alloy Powder
-
CMSX-4 Nickel Alloy Powder | Nickel Alloy Powder
Specifications, Sizes, and Grades of Metal Powders
Different metal powders come in various specifications, sizes, and grades, depending on the intended application and the requirements of the helium plasma process. Below, we provide a detailed breakdown:
Table: Specifications, Sizes, and Grades of Metal Powders
Metal Powder | Particle Size Range (µm) | Purity (%) | Grade | Typical Applications |
---|---|---|---|---|
Ti-6Al-4V | 15-45 | 99.5 | ASTM F136 | Aerospace, medical implants |
Inconel 718 | 15-53 | 99.0 | AMS 5662 | Turbine engines, high-temperature parts |
316L Stainless Steel | 10-45 | 99.9 | ASTM F138 | Medical implants, surgical instruments |
AlSi10Mg | 20-63 | 99.8 | ISO 8062-3 | Automotive, aerospace components |
Cu-Cr-Zr | 15-45 | 99.9 | ASTM B506 | Electrical components, connectors |
Cobalt-Chromium Alloy | 10-50 | 99.5 | ASTM F1537 | Dental implants, medical devices |
18Ni300 Maraging Steel | 20-53 | 99.0 | AMS 6521 | Tooling, high-strength components |
WC-Co | 10-45 | 99.9 | ISO 6508-1 | Cutting tools, wear-resistant coatings |
NiCr | 15-45 | 99.0 | AMS 5395 | Turbine blades, heat exchangers |
Tantalum (Ta) | 10-50 | 99.95 | ASTM F560 | Medical devices, electronics |
The particle size, purity, and grade of each metal powder play a crucial role in determining its suitability for specific applications. Helium plasma processes often require powders with high purity and specific particle size distributions to ensure optimal performance.
Advantages and Limitations of Helium Plasma
Helium plasma, while versatile and powerful, comes with its own set of advantages and limitations. Understanding these can help in making informed decisions about its use in various applications.
Advantages of Helium Plasma
- Precision and Control: Helium plasma allows for high precision in cutting, welding, and surface treatments, making it ideal for industries where accuracy is critical.
- Minimal Contamination: Due to helium’s inert nature, the risk of contamination is significantly reduced, which is essential in semiconductor manufacturing and medical applications.
- High Energy Efficiency: Helium plasma processes are energy-efficient, providing high output with lower energy consumption compared to other methods.
- Versatility: Helium plasma can be used with a wide range of materials, from metals to ceramics, enhancing its utility across various industries.
Limitations of Helium Plasma
- Cost: Helium is more expensive compared to other gases like argon, which can increase the overall cost of helium plasma processes.
- Availability: The availability of helium is limited, and its supply can be inconsistent, leading to potential disruptions in industrial processes.
- Complexity of Equipment: The equipment required to generate and maintain helium plasma is often complex and expensive, necessitating specialized knowledge and maintenance.
- Limited Penetration: Helium plasma may have limited penetration depth in certain materials, requiring multiple passes or additional processes to achieve the desired results.
Table: Advantages and Limitations of Helium Plasma
Aspect | Advantages | Limitations |
---|---|---|
Precision | High precision in cutting, welding, and surface treatments. | Limited penetration in some materials. |
Contamination | Minimal risk of contamination, ideal for sensitive industries. | High cost compared to other gases. |
Energy Efficiency | Energy-efficient, with high output and lower energy consumption. | Complex and expensive equipment required. |
Versatility | Can be used with a wide range of materials, enhancing its applicability. | Availability issues due to limited supply of helium. |
Understanding these pros and cons can help industries decide whether helium plasma is the right choice for their specific needs.
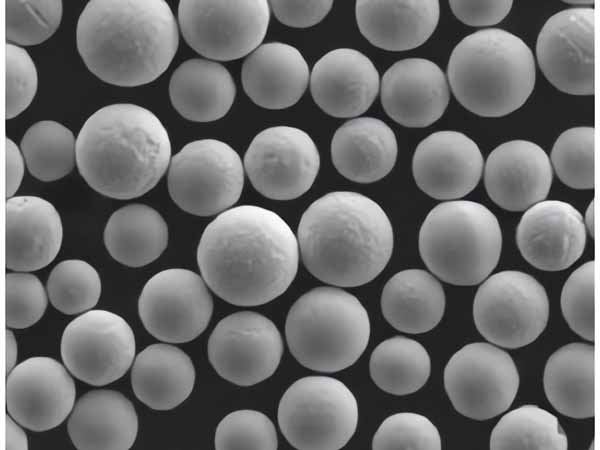
Supplier and Pricing Details
Selecting the right supplier and understanding the pricing details are crucial steps in integrating helium plasma processes into your operations. Below, we provide information on some leading suppliers and the typical pricing for metal powders used with helium plasma.
Table: Suppliers and Pricing Details
Supplier | Metal Powder | Pricing (per kg) | Additional Services | Location |
---|---|---|---|---|
Carpenter Technology | Ti-6Al-4V | $350 – $450 | Custom alloy development, technical support | United States |
Höganäs AB | 316L Stainless Steel | $150 – $250 | Powder customization, global distribution | Sweden |
Sandvik Materials | Inconel 718 | $400 – $500 | Metal powder consulting, supply chain management | United States, Sweden |
Arcam AB | AlSi10Mg | $200 – $300 | Additive manufacturing solutions, powder reuse programs | Sweden |
HC Starck | Tantalum (Ta) | $600 – $800 | High-purity materials, R&D collaboration | Germany |
Praxair Surface Technologies | NiCr | $300 – $400 | Surface coating solutions, technical expertise | United States |
GKN Additive | Cobalt-Chromium Alloy | $250 – $350 | Additive manufacturing services, material certification | United Kingdom |
ATI Specialty Materials | Maraging Steel 18Ni300 | $350 – $450 | High-performance materials, industry-specific solutions | United States |
Kennametal | Tungsten Carbide (WC-Co) | $500 – $700 | Wear-resistant solutions, tooling services | United States |
Oerlikon Metco | Cu-Cr-Zr | $250 – $350 | Advanced material processing, R&D support | Switzerland |
Pricing can vary based on factors such as order quantity, customization requirements, and additional services provided by the supplier.
FAQs
Question | Answer |
---|---|
What is helium plasma used for? | Helium plasma is used in semiconductor manufacturing, medical device sterilization, surface treatments, and additive manufacturing, among other applications. |
Why is helium plasma preferred over other types of plasma? | Helium plasma is preferred for its stability, high energy density, and minimal risk of contamination, making it ideal for sensitive and high-precision applications. |
What are the challenges of using helium plasma? | The main challenges include the high cost of helium, limited availability, and the complexity of the required equipment. |
Can helium plasma be used with all metals? | Helium plasma is compatible with a wide range of metals, but the effectiveness can vary depending on the specific metal and the desired outcome. |
How does helium plasma improve the quality of metal components? | Helium plasma enhances the surface finish, increases strength, and improves the overall durability of metal components, making them suitable for demanding applications. |
What safety precautions are needed when working with helium plasma? | Proper ventilation, protective clothing, and specialized equipment are essential to ensure safety when working with helium plasma. |
Is helium plasma environmentally friendly? | Helium plasma processes are relatively environmentally friendly, as they produce minimal waste and do not involve harmful chemicals. |
What industries benefit most from helium plasma technology? | Industries such as aerospace, medical devices, automotive, and electronics benefit significantly from the use of helium plasma technology. |
Can helium plasma be used in 3D printing? | Yes, helium plasma is used in additive manufacturing to produce high-quality metal parts with improved mechanical properties and surface finish. |
What are the alternatives to helium plasma? | Alternatives include argon plasma, nitrogen plasma, and laser-based processes, each with its own advantages and limitations depending on the application. |