Metal powders have revolutionized industries by providing innovative solutions for manufacturing and production. From aerospace to automotive, metal powders are the backbone of high-performance applications. In this article, we will delve deep into the world of high performance metal powders, exploring their types, properties, applications, and much more.
Overview of High Performance Metal Powders
High performance metal powders are finely divided metals that exhibit superior characteristics such as high strength, excellent thermal stability, and exceptional wear resistance. These powders are essential in various cutting-edge applications, including additive manufacturing, powder metallurgy, and surface coating technologies.
Key Details:
- Types: Multiple alloys and pure metals
- Applications: Aerospace, automotive, medical devices, electronics
- Properties: High strength, thermal stability, wear resistance
Types of High Performance Metal Powders
There are several types of high performance metal powders, each tailored to specific applications. Let’s take a closer look at some of the most popular ones:
Type | Description |
---|---|
Titanium Alloy Powders | Known for their high strength-to-weight ratio and excellent corrosion resistance. Ideal for aerospace and medical applications. |
Aluminum Alloy Powders | Lightweight with good strength and thermal conductivity. Used extensively in automotive and aerospace industries. |
Nickel-Based Superalloy Powders | Exhibit exceptional heat resistance and mechanical strength. Crucial for turbine engines and high-temperature applications. |
Stainless Steel Powders | Offer excellent corrosion resistance and mechanical properties. Widely used in food processing, medical devices, and automotive sectors. |
Cobalt-Chrome Alloy Powders | Known for their high wear resistance and strength at elevated temperatures. Commonly used in dental and orthopedic implants. |
Copper Alloy Powders | Provide excellent electrical and thermal conductivity. Used in electrical components and heat exchangers. |
Tungsten Carbide Powders | Extremely hard and wear-resistant. Essential for cutting tools and wear-resistant applications. |
Iron-Based Alloy Powders | Versatile and cost-effective with good mechanical properties. Used in various industrial applications, including automotive components. |
Inconel Powders | A family of nickel-chromium-based superalloys known for their oxidation and corrosion resistance. Used in extreme environments such as turbine blades and nuclear reactors. |
Magnesium Alloy Powders | Lightweight with good strength. Used in aerospace and automotive applications for weight reduction. |
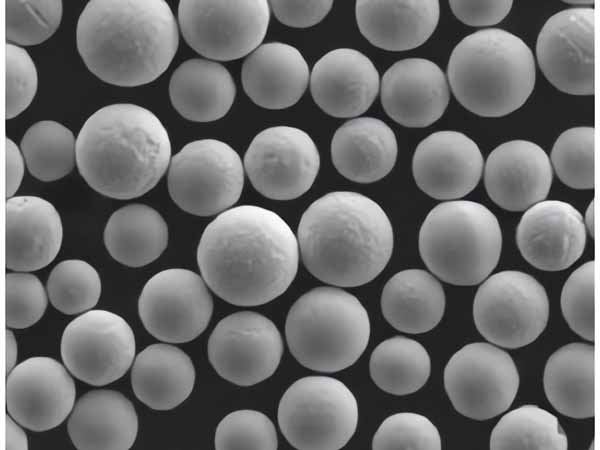
Composition of High Performance Metal Powders
The composition of metal powders greatly influences their properties and suitability for specific applications. Here’s a detailed look at the composition of some high performance metal powders:
Type | Composition |
---|---|
Titanium Alloy Powders | Primarily titanium with varying amounts of aluminum and vanadium |
Aluminum Alloy Powders | Aluminum mixed with elements like silicon, magnesium, copper, and zinc |
Nickel-Based Superalloy Powders | Nickel, chromium, cobalt, and additional elements such as molybdenum, aluminum, and titanium |
Stainless Steel Powders | Iron, chromium, nickel, and sometimes molybdenum |
Cobalt-Chrome Alloy Powders | Cobalt, chromium, and molybdenum |
Copper Alloy Powders | Copper with additions of zinc, tin, and sometimes lead |
Tungsten Carbide Powders | Tungsten and carbon, often with a cobalt binder |
Iron-Based Alloy Powders | Iron with carbon, chromium, nickel, and other alloying elements |
Inconel Powders | Nickel, chromium, iron, and additional elements such as molybdenum and niobium |
Magnesium Alloy Powders | Magnesium with aluminum, zinc, and manganese |
Characteristics of High Performance Metal Powders
Understanding the characteristics of metal powders is crucial for selecting the right material for your application. Here are some key characteristics of high performance metal powders:
Characteristic | Description |
---|---|
Strength | High tensile and yield strength, essential for load-bearing applications |
Thermal Stability | Ability to maintain properties at high temperatures |
Corrosion Resistance | Resistance to oxidation and degradation in harsh environments |
Wear Resistance | Ability to withstand surface wear and abrasion |
Density | Varies depending on the metal, affecting weight and material usage |
Electrical Conductivity | Crucial for applications involving electrical components |
Thermal Conductivity | Important for heat dissipation in thermal management applications |
Ductility | Ability to deform under tensile stress without fracturing |
Hardness | Resistance to deformation and scratching |
Machinability | Ease of being machined or formed into the desired shape without compromising properties |
Applications of High Performance Metal Powders
High performance metal powders are used in a wide range of applications due to their superior properties. Here are some common applications:
Application | Description |
---|---|
Aerospace | Used in the manufacturing of lightweight, high-strength components such as turbine blades and airframes |
Automotive | Essential for producing lightweight, durable parts such as engine components and structural elements |
Medical Devices | Used in orthopedic implants, dental applications, and surgical instruments due to biocompatibility |
Electronics | Applied in the production of conductive components, heat sinks, and thermal management systems |
Additive Manufacturing | 3D printing of complex geometries with tailored properties for various industries |
Powder Metallurgy | Producing parts with precise dimensions and excellent mechanical properties |
Surface Coatings | Enhancing surface properties such as wear resistance, corrosion resistance, and thermal stability |
Energy Sector | Manufacturing of components for power generation, including turbines and nuclear reactors |
Tooling and Cutting | Producing cutting tools and dies that require high hardness and wear resistance |
Marine Industry | Used in components that require corrosion resistance in marine environments |
Specifications, Sizes, and Grades
Metal powders come in various specifications, sizes, and grades to meet specific requirements. Here’s an overview:
Specification | Description |
---|---|
Particle Size | Ranges from a few microns to hundreds of microns, affecting flowability and packing density |
Purity | High purity levels are essential for consistent performance, typically >99% |
Shape | Spherical, irregular, and angular shapes, influencing packing density and flow characteristics |
Density | Apparent density and tap density, affecting the amount of powder needed for a given volume |
Flow Rate | Important for powder handling and processing |
Oxygen Content | Low oxygen content is crucial for preventing oxidation and maintaining material properties |
Standards | Compliance with industry standards such as ASTM, ISO, and AMS ensures quality and reliability |
Grades | Different grades available based on alloy composition and intended application |
Surface Area | Affects reactivity and sintering behavior, usually measured in m²/g |
Microstructure | Control over grain size and phase distribution to achieve desired mechanical properties |
Suppliers and Pricing Details
Several suppliers offer high performance metal powders, each providing different grades and specifications. Here’s a look at some key suppliers and their pricing details:
Supplier | Description | Pricing (per kg) |
---|---|---|
Höganäs AB | Leading supplier of high-quality metal powders for various applications | $50 – $200 |
Carpenter Technology | Specializes in advanced alloy powders for demanding applications | $100 – $500 |
Sandvik Osprey | Offers a wide range of metal powders with excellent properties | $80 – $300 |
Praxair Surface Technologies | Provides metal powders for additive manufacturing and coating applications | $70 – $250 |
GKN Additive | Supplies metal powders specifically for 3D printing and powder metallurgy | $90 – $350 |
HC Starck Solutions | Produces high-performance refractory metal powders | $150 – $600 |
Kennametal | Known for their tungsten carbide powders and advanced materials | $200 – $800 |
Arcam AB (GE Additive) | Offers a variety of metal powders for additive manufacturing | $100 – $400 |
EOS GmbH | Specializes in metal powders for industrial 3D printing | $120 – $450 |
AMETEK Specialty Metal Products | Provides high-purity metal powders for critical applications | $130 – $500 |
Comparison of High Performance Metal Powders
To help you choose the right metal powder, here’s a comparison based on various parameters:
Type | Strength | Thermal Stability | Corrosion Resistance | Wear Resistance | Density | Cost |
---|---|---|---|---|---|---|
Titanium Alloy Powders | High | Excellent | Very High | Moderate | Low | High |
Aluminum Alloy Powders | Moderate | Moderate | High | Moderate | Very Low | Moderate |
Nickel-Based Superalloy Powders | Very High | Exceptional | High | High | High | Very High |
Stainless Steel Powders | High | High | Very High | Moderate | High | Moderate |
Cobalt-Chrome Alloy Powders | Very High | High | High | Very High | High | High |
Copper Alloy Powders | Low | Low | Low | Low | High | Low |
Tungsten Carbide Powders | Very High | High | Moderate | Exceptional | Very High | Very High |
Iron-Based Alloy Powders | Moderate | Moderate | Moderate | Moderate | High | Low |
Inconel Powders | Very High | Exceptional | Very High | High | High | Very High |
Magnesium Alloy Powders | Moderate | Low | Moderate | Low | Very Low | Low |
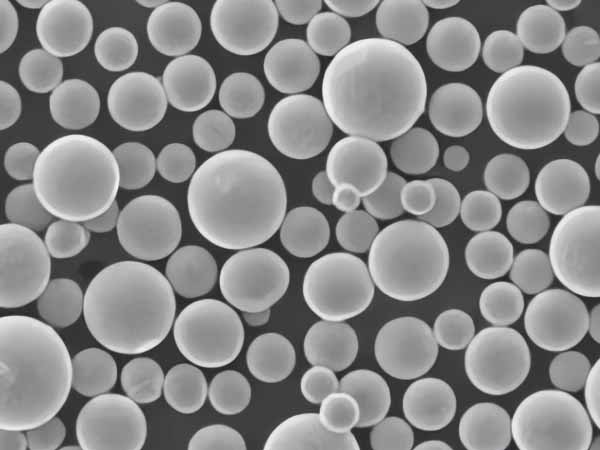
FAQ
Q: What are high performance metal powders?
A: High performance metal powders are finely divided metals known for their superior characteristics, such as high strength, thermal stability, and wear resistance. They are used in various advanced applications, including aerospace, automotive, and medical devices.
Q: What are the common applications of high performance metal powders?
A: Common applications include aerospace components, automotive parts, medical implants, electronics, additive manufacturing, powder metallurgy, surface coatings, energy sector components, tooling, and marine industry parts.
Q: How do the compositions of different metal powders affect their properties?
A: The composition of metal powders influences their mechanical and physical properties. For example, titanium alloy powders offer a high strength-to-weight ratio, while nickel-based superalloy powders provide exceptional heat resistance. The specific alloying elements and their proportions determine the final properties of the powders.
Q: What factors should I consider when selecting a metal powder?
A: Consider factors such as strength, thermal stability, corrosion resistance, wear resistance, density, cost, and the specific application requirements. The choice of metal powder should align with the performance criteria needed for your application.
Q: How are high performance metal powders manufactured?
A: High performance metal powders are typically produced through methods such as gas atomization, water atomization, plasma atomization, and mechanical alloying. These processes ensure the powders have the desired particle size, shape, and purity.
Q: What are the advantages of using metal powders in additive manufacturing?
A: Metal powders in additive manufacturing enable the production of complex geometries, customized parts, and lightweight structures. They offer design flexibility, reduced material waste, and the ability to tailor properties to specific applications.
Q: How do I ensure the quality of metal powders?
A: Ensure the quality of metal powders by sourcing from reputable suppliers, verifying compliance with industry standards, and conducting thorough testing for particle size, purity, density, and other relevant parameters.
Q: What are some challenges associated with using high performance metal powders?
A: Challenges include handling and storage to prevent oxidation, controlling particle size distribution, ensuring consistent quality, and managing costs. Proper equipment and protocols are essential to address these challenges effectively.
Q: Can high performance metal powders be recycled?
A: Yes, high performance metal powders can often be recycled. The recycling process involves re-melting and re-atomizing the powders to produce new material, which helps reduce waste and conserve resources.
Q: What is the future of high performance metal powders?
A: The future of high performance metal powders looks promising with advancements in manufacturing technologies, increasing demand for lightweight and high-strength materials, and growing applications in emerging industries such as space exploration and renewable energy.
Conclusion
High performance metal powders are at the forefront of material innovation, enabling the development of advanced components with exceptional properties. From aerospace to medical devices, these powders play a crucial role in various industries, offering unmatched performance and versatility. By understanding the types, compositions, characteristics, and applications of high performance metal powders, you can make informed decisions for your specific needs. Whether you’re involved in additive manufacturing, powder metallurgy, or any other high-tech application, high performance metal powders are your key to success.