Overview of High Purity Powder
High purity powder plays a critical role in various industrial applications, from advanced electronics to aerospace engineering. This comprehensive guide will delve into the intricacies of high purity powder, providing you with an in-depth understanding of its types, compositions, properties, and uses. We’ll also discuss the advantages and disadvantages, specifications, suppliers, and pricing details. By the end, you’ll have a clear picture of how high purity powder can benefit your projects.
What is High Purity Powder?
High purity powder refers to fine, granular materials that are manufactured to possess exceptionally high levels of purity. These powders are essential in industries where even the smallest impurities can significantly impact performance and quality. Metals like aluminum, copper, and titanium are often produced in high purity powder form to meet the stringent requirements of advanced manufacturing processes.
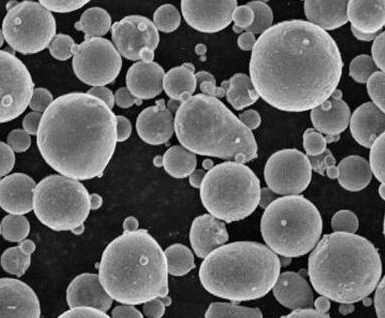
Types and Compositions of High Purity Powder
Different types of high purity powders are available, each tailored to specific applications and performance requirements. Here are ten popular models with their compositions:
Type of Powder | Composition | Purity Level | Properties |
---|---|---|---|
High Purity Aluminum Powder | Aluminum (Al) | 99.99% | Excellent conductivity, lightweight |
High Purity Copper Powder | Copper (Cu) | 99.999% | Superior electrical conductivity |
High Purity Titanium Powder | Titanium (Ti) | 99.9% | High strength, corrosion resistance |
High Purity Nickel Powder | Nickel (Ni) | 99.99% | High melting point, oxidation resistance |
High Purity Silicon Powder | Silicon (Si) | 99.9999% | Semiconductor properties, heat resistance |
High Purity Cobalt Powder | Cobalt (Co) | 99.99% | Magnetic properties, wear resistance |
High Purity Zinc Powder | Zinc (Zn) | 99.999% | Corrosion protection, lightweight |
High Purity Iron Powder | Iron (Fe) | 99.99% | High density, magnetic properties |
High Purity Magnesium Powder | Magnesium (Mg) | 99.99% | Lightweight, high strength-to-weight ratio |
High Purity Tungsten Powder | Tungsten (W) | 99.999% | High melting point, hardness |
Applications of High Purity Powder
High purity powders are utilized across a variety of industries due to their unique properties. Here’s a breakdown of their applications:
Industry | Application |
---|---|
Electronics | Conductive inks, semiconductor devices |
Aerospace | Lightweight components, high-strength alloys |
Medical | Implantable devices, prosthetics |
Automotive | Engine components, lightweight parts |
Energy | Solar panels, batteries |
Chemical | Catalysts, high-purity reagents |
Metallurgy | Alloy production, metallurgical research |
3D Printing | Additive manufacturing, rapid prototyping |
Pharmaceutical | Drug delivery systems, fine chemicals |
Nanotechnology | Nanoparticles, advanced materials research |
Specifications, Sizes, Grades, and Standards
When selecting high purity powder, it’s crucial to consider the specifications, sizes, grades, and standards to ensure compatibility with your application. Below is a detailed table outlining these parameters:
Type of Powder | Specification | Size Range | Grade | Standards |
---|---|---|---|---|
High Purity Aluminum Powder | ASTM B928 | 10-45 microns | 4N (99.99%) | ASTM B328, ISO 9001 |
High Purity Copper Powder | ASTM B216 | 20-50 microns | 5N (99.999%) | ASTM B243, ISO 14001 |
High Purity Titanium Powder | ASTM F67 | 15-60 microns | 3N (99.9%) | ASTM B299, ISO 13485 |
High Purity Nickel Powder | ASTM B333 | 10-50 microns | 4N (99.99%) | ASTM B377, ISO 16949 |
High Purity Silicon Powder | SEMI MF41 | 1-10 microns | 6N (99.9999%) | SEMI M12, ISO 14644 |
High Purity Cobalt Powder | ASTM B335 | 10-45 microns | 4N (99.99%) | ASTM B398, ISO 45001 |
High Purity Zinc Powder | ASTM B692 | 5-30 microns | 5N (99.999%) | ASTM B850, ISO 9001 |
High Purity Iron Powder | ASTM B243 | 20-100 microns | 4N (99.99%) | ASTM B328, ISO 14001 |
High Purity Magnesium Powder | ASTM B634 | 10-60 microns | 4N (99.99%) | ASTM B954, ISO 13485 |
High Purity Tungsten Powder | ASTM B777 | 1-20 microns | 5N (99.999%) | ASTM B897, ISO 16949 |
Suppliers and Pricing Details
Finding a reliable supplier is key to ensuring the quality and consistency of high purity powder. Here’s a table highlighting some top suppliers and their pricing details:
Supplier | Location | Types Available | Price Range (per kg) |
---|---|---|---|
American Elements | USA | Aluminum, Copper, Titanium, Nickel, Silicon | $300 – $5000 |
Goodfellow | UK | Cobalt, Zinc, Iron, Magnesium, Tungsten | $250 – $4500 |
Nanochemazone | Canada | Wide range of high purity powders | $200 – $6000 |
Sigma-Aldrich | Global | Comprehensive range of high purity powders | $350 – $5500 |
Advanced Engineering Materials | Germany | Specialty high purity metal powders | $400 – $7000 |
Pros and Cons of High Purity Powder
High purity powders offer numerous benefits, but they also come with some limitations. Let’s compare the pros and cons:
Advantages | Disadvantages |
---|---|
Superior Performance: High purity levels ensure exceptional performance in demanding applications. | Cost: High purity powders can be significantly more expensive than lower purity alternatives. |
Consistency: Reliable and consistent quality due to stringent manufacturing standards. | Availability: Some high purity powders may have limited availability depending on the supplier. |
Specialized Applications: Ideal for use in specialized industries like aerospace and electronics. | Handling: Requires careful handling and storage to maintain purity levels. |
Reduced Contaminants: Lower risk of contamination affecting the end product’s performance. | Processing: Specialized processing equipment may be needed to work with high purity powders. |
Advantages of High Purity Powder
Using high purity powders offers several key advantages, making them indispensable in many high-tech applications. Here’s a closer look at some of the benefits:
1. Enhanced Performance
High purity powders ensure optimal performance by reducing the risk of contaminants interfering with the material’s properties. This is particularly crucial in industries like electronics and aerospace, where precision and reliability are paramount.
2. Consistency and Reliability
Manufacturers of high purity powders adhere to strict quality control standards, ensuring consistent and reliable products. This consistency is vital for processes that require exacting specifications.
3. Specialized Applications
Certain applications demand the unique properties of high purity powders. For instance, in the medical field, high purity titanium powders are used for making biocompatible implants and prosthetics.
4. Reduced Contaminants
Lower levels of impurities mean that high purity powders are less likely to introduce unwanted elements into the final product, which can compromise performance and quality.
Disadvantages of High Purity Powder
While high purity powders offer many benefits, they also come with some downsides. Here’s what you need to consider:
1. High Cost
One of the main drawbacks of high purity powders is their cost. Producing powders with such high levels of purity is an expensive process, making the end product more costly.
2. Limited Availability
Not all high purity powders are readily available. Some types may have limited production runs, leading to potential supply issues.
3. Handling and Storage
Maintaining the purity of these powders requires careful handling and storage. Any contamination can negate the benefits of the high purity material.
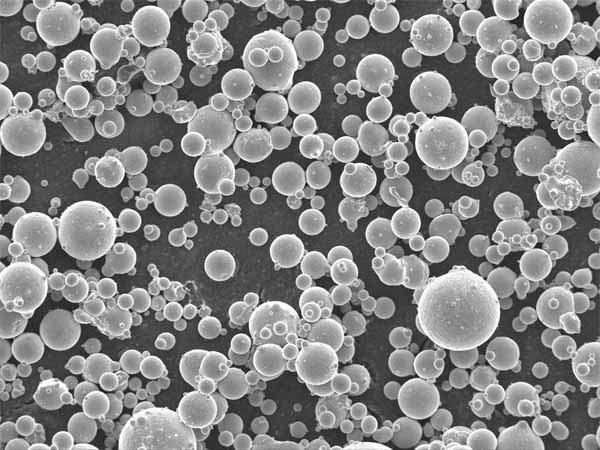
FAQs
Here are answers to some commonly asked questions about high purity powder:
What are the advantages of using high purity powder?
High purity powders offer enhanced performance due to their reduced contaminants, ensuring reliability and consistency in critical applications. They are also ideal for specialized uses where purity and performance are paramount.
How is high purity powder manufactured?
High purity powders are typically produced through processes like atomization or chemical vapor deposition (CVD). These methods ensure that the material maintains its purity by minimizing impurities during production.
What industries use high purity powder?
High purity powders find applications in electronics, aerospace, medical devices, automotive, energy, and nanotechnology industries. They are used for everything from semiconductors and catalysts to lightweight alloys and biomedical implants.
What challenges come with using high purity powder?
The main challenges include the high cost of production, limited availability of certain types, and the need for specialized handling and storage to maintain purity levels and prevent contamination.
How do I choose the right high purity powder for my application?
Consider factors such as the required purity level, material properties (e.g., conductivity, strength), and compatibility with your manufacturing processes. Consult with suppliers and consider testing samples to ensure suitability.
By understanding the nuances of high purity powder, from its diverse applications to the specific types available, you can make informed decisions for your projects. Whether you’re in electronics, aerospace, or any other high-tech industry, choosing the right high purity powder can significantly impact performance and product quality. For further exploration or specific inquiries, feel free to delve deeper into the details or consult with experts in the field.