Overview
High sphericity powder is a specialized form of powdered material, engineered to possess nearly perfect spherical shapes. This property is critical in various industrial applications, particularly in additive manufacturing (3D printing), aerospace, automotive, electronics, and medical devices. The importance of sphericity in these powders lies in their flowability, packing density, and even melting properties, which are crucial in achieving consistent, high-quality production outputs.
In this extensive guide, we’ll explore everything you need to know about high sphericity powder. From understanding its composition and characteristics to comparing different metal powder models, we aim to provide a well-rounded, detailed resource. Whether you’re a materials engineer, a purchasing manager, or simply curious about the world of high sphericity powders, this article is designed to educate and inform.
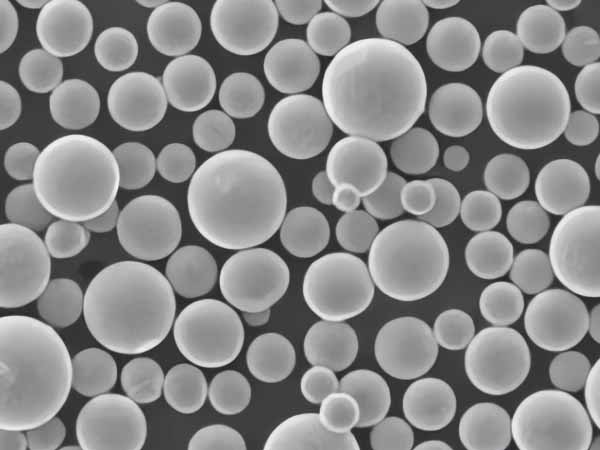
Understanding High Sphericity Powder
What is High Sphericity Powder?
High sphericity powder refers to powdered materials where the individual particles are nearly perfect spheres. This shape is achieved through various manufacturing processes such as gas atomization, plasma atomization, or centrifugal atomization. The spherical nature of these particles contributes to their high flowability and packing density, making them ideal for specific high-precision applications.
Why Does Sphericity Matter?
Imagine trying to stack irregularly shaped rocks versus stacking perfectly round marbles. The marbles would stack neatly with minimal gaps, right? That’s what high sphericity powder does on a microscopic level. Its spherical shape allows for better packing, which translates to higher density, improved flowability, and more consistent behavior during melting or sintering processes.
Key Benefits of High Sphericity Powder
- Improved Flowability: Spherical particles flow more easily than irregularly shaped ones, making them ideal for applications like 3D printing where consistent feeding of the powder is crucial.
- Higher Packing Density: The uniform shape allows for closer packing of particles, leading to higher density and, in turn, stronger final products.
- Better Melting Properties: Spherical powders melt uniformly, reducing the risk of defects in the final product.
Types and Composition of High Sphericity Powder
High sphericity powders can be made from a variety of metals and alloys, each suited for different applications. Below is a detailed table of some common types of high sphericity powders, along with their composition, properties, and applications.
Powder Type | Composition | Properties | Applications |
---|---|---|---|
316L Stainless Steel | Fe, Cr, Ni, Mo | High corrosion resistance, good mechanical properties | Medical devices, aerospace components |
AlSi10Mg | Al, Si, Mg | Lightweight, high strength, good thermal properties | Automotive parts, aerospace |
Inconel 718 | Ni, Cr, Fe, Nb, Mo, Ti, Al | High temperature strength, corrosion-resistant | Gas turbines, aerospace, nuclear reactors |
Ti-6Al-4V | Ti, Al, V | High strength-to-weight ratio, corrosion resistance | Aerospace, biomedical implants |
CoCrMo | Co, Cr, Mo | Biocompatibility, wear resistance, corrosion resistance | Medical implants, dental applications |
Copper (Cu) | Pure Cu | Excellent electrical conductivity, thermal conductivity | Electrical components, heat exchangers |
Hastelloy X | Ni, Cr, Fe, Mo, Co | Oxidation resistance, strength at high temperatures | Gas turbines, petrochemical applications |
Maraging Steel (18Ni300) | Fe, Ni, Co, Mo | Ultra-high strength, good toughness | Tooling, aerospace, nuclear applications |
Nickel 625 | Ni, Cr, Mo, Nb | Excellent corrosion resistance, high strength | Marine, chemical processing, aerospace |
Aluminum 6061 | Al, Mg, Si | Good mechanical properties, lightweight | Aerospace, automotive, electronics |
Characteristics of High Sphericity Powder
Understanding the specific characteristics of high sphericity powders is crucial for selecting the right material for your application. Here, we delve into the core properties that define these powders.
1. Particle Size Distribution
Particle size distribution refers to the range of particle sizes in a batch of powder. A narrow size distribution is generally preferred for applications requiring uniformity, such as additive manufacturing, as it leads to more consistent behavior during processing.
- Fine Powders (1-10 µm): Best for applications requiring smooth finishes and high precision.
- Medium Powders (10-50 µm): Commonly used in general 3D printing applications, offering a balance between flowability and precision.
- Coarse Powders (50-150 µm): Suitable for applications requiring higher build rates but less surface finish quality.
2. Flowability
Flowability is the ability of the powder to flow smoothly and consistently. This characteristic is critical in processes like 3D printing, where the powder needs to be evenly distributed to create uniform layers.
- High Flowability: Ensures consistent layering in additive manufacturing, reducing the risk of defects.
- Low Flowability: Can lead to uneven layers, increasing the likelihood of defects in the final product.
3. Purity
Purity refers to the absence of contaminants in the powder. High purity levels are essential for maintaining the integrity of the final product, especially in critical applications like medical implants or aerospace components.
- High Purity (>99%): Ensures that the final product meets stringent quality standards, reducing the risk of failures.
- Low Purity (<99%): May lead to contamination issues, affecting the performance and reliability of the final product.
4. Density
Density plays a significant role in the performance of the final product. High-density powders are typically preferred as they result in stronger and more durable components.
- High Density: Leads to stronger, more durable products.
- Low Density: May result in weaker products with potential structural issues.
Applications of High Sphericity Powder
High sphericity powders are used across various industries, each benefiting from the unique properties these powders offer. Below, we explore some of the primary applications of high sphericity powders.
Industry | Applications | Key Benefits |
---|---|---|
Additive Manufacturing (3D Printing) | Prototyping, production of complex geometries | High precision, consistent quality, improved mechanical properties |
Aerospace | Turbine blades, structural components | High strength, heat resistance, lightweight materials |
Medical Devices | Implants, surgical tools | Biocompatibility, corrosion resistance, tailored mechanical properties |
Automotive | Lightweight components, engine parts | Improved fuel efficiency, reduced emissions, high strength |
Electronics | Conductive components, heat sinks | Excellent electrical and thermal conductivity |
Defense | High-performance components, armor | High strength-to-weight ratio, durability |
Energy | Turbines, reactors, fuel cells | Corrosion resistance, high temperature stability |
Specifications, Sizes, Grades, and Standards
Different applications require different specifications, sizes, grades, and standards of high sphericity powders. Below is a detailed table outlining these aspects.
Material | Particle Size (µm) | Grade | Standard | Typical Uses |
---|---|---|---|---|
316L Stainless Steel | 15-45 | A, B | ASTM F3184 | Medical devices, aerospace components |
AlSi10Mg | 20-63 | A | ISO 23510 | Automotive parts, aerospace |
Inconel 718 | 15-53 | B, C | AMS 5662 | Gas turbines, aerospace, nuclear reactors |
Ti-6Al-4V | 15-45 | A | ASTM F1472 | Aerospace, biomedical implants |
CoCrMo | 10-45 | B | ISO 5832-12 | Medical implants, dental applications |
Copper (Cu) | 20-60 | A | ASTM B212 | Electrical components, heat exchangers |
Hastelloy X | 15-53 | C | AMS 5536 | Gas turbines, petrochemical applications |
Maraging Steel (18Ni300) | 20-63 | B | AMS 6514 | Tooling, aerospace, nuclear applications |
Nickel 625 | 15-45 | B, C | ASTM B443 | Marine, chemical processing, aerospace |
Aluminum 6061 | 20-70 | A | ASTM B221 | Aerospace, automotive, electronics |
Suppliers and Pricing Details
The market for high sphericity powders is diverse, with suppliers offering a range of materials at different price points. Below is a comparison of suppliers, materials offered, and pricing details.
Supplier | Material | Price (per kg) | MOQ (Minimum Order Quantity) | Lead Time |
EOS GmbH | 316L Stainless Steel | $250 | 10 kg | 4-6 weeks |
AP&C (GE Additive) | Ti-6Al-4V | $400 | 5 kg | 3-4 weeks |
Carpenter Technology | Inconel 718 | $300 | 15 kg | 6-8 weeks |
Sandvik | AlSi10Mg | $200 | 20 kg | 5-7 weeks |
LPW Technology | CoCrMo | $350 | 10 kg | 4-5 weeks |
GKN Hoeganaes | Aluminum 606 | $150 | 25 kg | 3-4 weeks |
Höganäs | Maraging Steel (18Ni300) | $450 | 10 kg | 6-8 weeks |
Praxair Surface Technologies | Nickel 625 | $320 | 20 kg | 5-6 weeks |
Tekna | Copper (Cu) | $180 | 30 kg | 3-5 weeks |
Oerlikon AM | Hastelloy X | $400 | 10 kg | 4-6 weeks |
Advantages and Disadvantages of High Sphericity Powder
When choosing high sphericity powders, it’s essential to weigh the pros and cons. Below is a comparative table that highlights the advantages and disadvantages of these materials.
Advantages | Disadvantages |
---|---|
High Flowability: Easy to handle and process. | Cost: Generally more expensive than irregular powders. |
Consistent Melting: Reduces defects in final products. | Availability: Limited availability for some specialized alloys. |
High Packing Density: Leads to stronger, more durable products. | Processing Difficulty: Requires specialized equipment for some processes. |
Wide Range of Applications: Versatile use across industries. | Limited Customization: Standard grades and sizes may not fit all needs. |
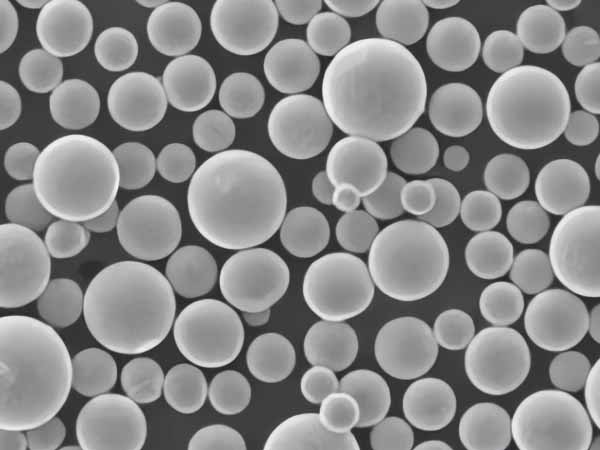
FAQs
What is high sphericity powder used for?
High sphericity powder is primarily used in additive manufacturing, aerospace, medical devices, and other industries requiring high precision and consistency. Its spherical shape allows for better flowability, packing density, and melting properties, making it ideal for creating high-quality, defect-free products.
Why is the sphericity of powder important?
Sphericity affects the flowability, packing density, and melting properties of the powder. Higher sphericity leads to better flow during processing, higher packing density, which improves the strength of the final product, and more consistent melting, reducing defects.
How is high sphericity powder made?
High sphericity powder is typically made through processes like gas atomization, plasma atomization, or centrifugal atomization. These methods ensure that the particles are nearly perfect spheres, which is crucial for the powder’s performance in various applications.
What are the common materials used in high sphericity powders?
Common materials include 316L stainless steel, Ti-6Al-4V, Inconel 718, AlSi10Mg, and CoCrMo. Each material has its unique properties and is chosen based on the specific requirements of the application.
Is high sphericity powder expensive?
High sphericity powders are generally more expensive than irregular powders due to the specialized processes used to create them and the superior properties they offer. The cost can vary depending on the material, particle size, and supplier.
Can high sphericity powder be customized?
While most suppliers offer standard grades and sizes, customization is possible, though it may come at a higher cost and with longer lead times. Customization options depend on the supplier and the specific material.
What industries benefit most from high sphericity powder?
Industries that benefit the most include aerospace, medical devices, automotive, electronics, and additive manufacturing. These industries require materials with high precision, consistency, and specific properties that high sphericity powders provide.
What are the limitations of high sphericity powder?
Limitations include higher cost, potential availability issues for specialized alloys, and the need for specialized processing equipment. Additionally, standard grades and sizes may not fit all applications, requiring customization.
How do I choose the right high sphericity powder for my application?
Choosing the right powder depends on factors like the required material properties, application requirements, budget, and available equipment. Consulting with suppliers and experts in the field can help ensure the best choice is made for your specific needs.
Conclusion
High sphericity powders represent a critical component in modern manufacturing, offering unparalleled precision, consistency, and performance. Their unique properties make them indispensable in high-tech industries like aerospace, medical devices, and additive manufacturing. While the cost and availability can be challenging, the benefits they offer often outweigh these drawbacks, particularly for applications where quality and reliability are paramount.
Whether you’re a seasoned engineer or just stepping into the world of materials science, understanding high sphericity powder is crucial in today’s advanced manufacturing landscape. As technology continues to evolve, so too will the applications and capabilities of these remarkable powders, making them a key player in the future of manufacturing.