Imagine a material so robust, it can withstand the scorching heat of a jet engine or the intense pressure of a deep-sea exploration vessel. That’s the realm of high-temperature alloy powders, the unsung heroes of various industries pushing the boundaries of heat, stress, and corrosion resistance.
These fine, metallic particles are meticulously crafted to possess exceptional properties, making them the go-to choice for applications where ordinary materials simply wouldn’t stand a chance.
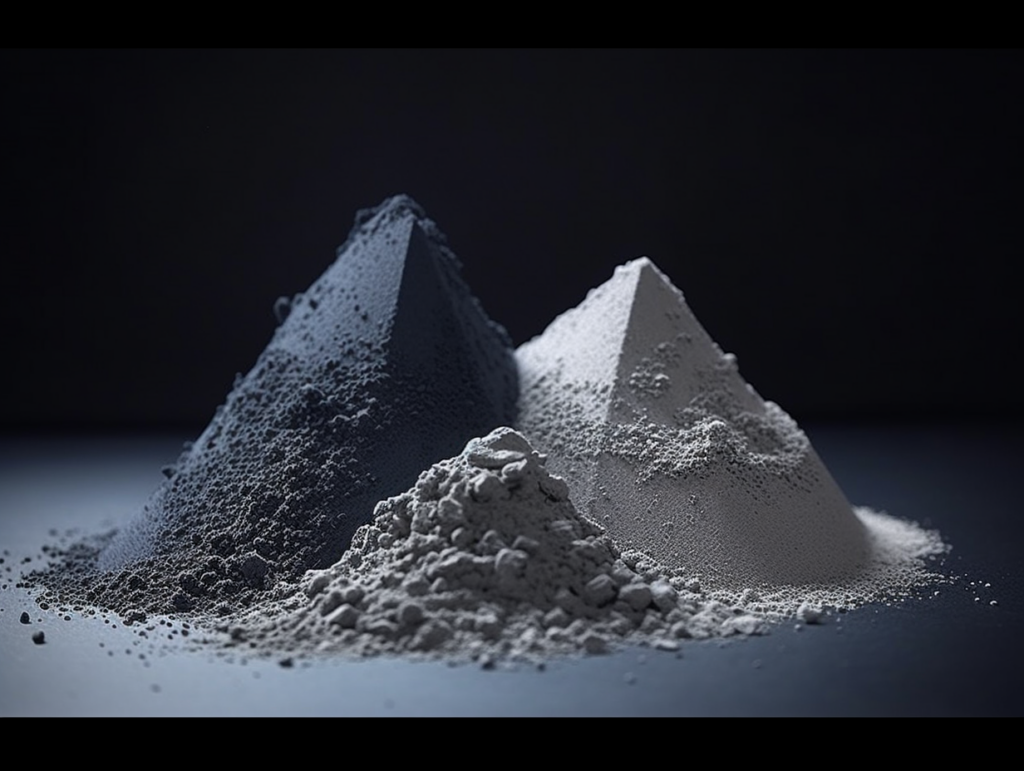
Delving into the World of High-Temperature Alloy Powders
Before diving into the specifics, let’s establish a foundational understanding of these remarkable materials. High-temperature alloy powders are typically composed of a blend of elements like nickel, chromium, cobalt, and others, meticulously formulated to achieve a unique synergy of properties. This synergistic effect grants them the ability to:
- Withstand extreme temperatures: Soaring past the limitations of conventional materials, these powders can endure temperatures exceeding 1,100 degrees Celsius (2,012 degrees Fahrenheit) without succumbing to melting or losing their structural integrity.
- Combat relentless wear and tear: Imagine a material that can shrug off constant friction and abrasion. High-temperature alloy powders possess exceptional wear resistance, making them ideal for components subjected to extreme mechanical stresses.
- Defy corrosion’s wrath: Highly resistant to various corrosive environments, these powders excel in applications where exposure to harsh chemicals, salt, or even seawater is inevitable.
- Retain their strength: Even under immense heat and pressure, these powders maintain their remarkable strength, ensuring the structural integrity of the components they form.
Exploring the Diverse Landscape of High-Temperature Alloy Powders:
With their unique blend of properties, high-temperature alloy powders come in a variety of compositions, each catering to specific needs. Here’s a glimpse into some of the most widely used models:
1. INCONEL® 625:
A nickel-chromium-molybdenum alloy renowned for its exceptional strength, oxidation resistance, and good fabricability. This versatile powder finds applications in jet engine components, chemical processing equipment, and heat exchangers.
2. INCONEL® 718:
Another versatile nickel-chromium-molybdenum alloy, offering superior strength, creep resistance, and good weldability. It’s extensively used in aerospace components, turbine blades, and demanding industrial applications.
3. Hastelloy® X:
This nickel-chromium-molybdenum-tungsten alloy shines in environments with high temperatures and corrosive media. Its impressive resistance to oxidation, stress corrosion cracking, and chloride-ion attack makes it ideal for chemical processing equipment, heat exchangers, and pollution control systems.
4. Haynes® 230:
A cobalt-chromium-tungsten-nickel alloy known for its exceptional high-temperature strength and oxidation resistance. It’s commonly used in gas turbine combustors, afterburners, and other applications demanding superior performance at elevated temperatures.
5. AM30B:
A stainless-steel-based alloy powder offering a balance of affordability, good mechanical properties, and corrosion resistance. It’s often used in applications requiring moderate high-temperature strength and corrosion resistance, such as exhaust manifolds and heat exchangers.
6. Ti-6Al-4V:
This titanium alloy powder offers a unique combination of high strength-to-weight ratio, good corrosion resistance, and biocompatibility. It’s widely used in the aerospace industry, biomedical implants, and demanding sporting goods.
7. Inconel® 738LC:
A low-carbon variant of INCONEL® 718, specifically formulated to minimize weld-related issues like sensitization and cracking. This powder is favored in applications requiring exceptional weldability alongside high-temperature strength and creep resistance, such as aircraft structures and turbine discs.
8. Rene® 41:
A nickel-based superalloy known for its exceptional high-temperature strength, creep resistance, and resistance to oxidation and hot corrosion. It’s primarily used in hot-section components of jet engines and industrial gas turbines.
9. Nimonic® 90:
A nickel-chromium-cobalt alloy offering outstanding creep resistance and high-temperature strength. This powder finds applications in hot-section components of jet engines, land-based gas turbines, and other demanding applications requiring exceptional performance at elevated temperatures.
10. CM247LC:
A nickel-chromium-cobalt alloy specifically designed for laser additive manufacturing (LAM). This powder possesses good printability, high-temperature strength, and oxidation resistance, making it suitable for various LAM applications, including aerospace components and heat exchangers.
Understandingthe Applications of High-Temperature Alloy Powders:
These extraordinary powders find applications in a multitude of industries where pushing the boundaries of performance is paramount. Here are some of the key areas where they shine:
- Aerospace: From the fiery belly of jet engines to the lightweight structures of spacecraft, high-temperature alloy powders play a critical role in aerospace applications. Their exceptional strength, heat resistance, and ability to withstand harsh environments make them ideal for components like turbine blades, combustors, and airframes.
- Energy Production: Whether it’s harnessing the power of fossil fuels or exploring alternative energy sources like nuclear and geothermal, high-temperature alloy powders are essential for ensuring the safe and efficient operation of power plants. Their ability to withstand extreme temperatures, pressure, and corrosion makes them crucial for components like boiler tubes, heat exchangers, and turbine blades.
- Chemical Processing: In the harsh world of chemical processing, where exposure to corrosive chemicals and high temperatures is commonplace, high-temperature alloy powders offer a lifeline. Their exceptional resistance to corrosion, erosion, and oxidation ensures the integrity of equipment and prevents costly breakdowns. They are extensively used in reactors, heat exchangers, and piping systems.
- Oil and Gas: From drilling deep into the earth’s crust to transporting oil and gas across vast distances, high-temperature alloy powders play a vital role in the oil and gas industry. Their ability to withstand the high pressures and temperatures encountered during drilling and transportation makes them ideal for downhole tools, pipelines, and valves.
- Automotive: Even in the ever-evolving world of automotive engineering, high-temperature alloy powders are finding their place. Their ability to handle the demanding thermal and mechanical stresses of modern engines makes them suitable for components like exhaust manifolds, turbochargers, and valve seats.
the Advantages and Considerations
While the benefits of high-temperature alloy powders are undeniable, it’s crucial to consider both their advantages and limitations to make informed decisions.
Advantages:
- Exceptional performance: These powders boast superior strength, wear resistance, and corrosion resistance compared to conventional materials, enabling them to excel in demanding environments.
- Design flexibility: Additive manufacturing (AM) techniques like laser powder bed fusion (LPBF) unlock new design possibilities with high-temperature alloy powders. Complex geometries and lightweight structures become achievable, pushing the boundaries of design and functionality.
- Reduced weight: Compared to heavier traditional materials, high-temperature alloy powders can offer significant weight savings, leading to improved fuel efficiency and performance in applications like aerospace and automotive.
Considerations:
- Cost: Due to the complex manufacturing processes involved, high-temperature alloy powders can be more expensive than conventional materials. However, their superior performance and extended lifespan can often justify the initial investment.
- Processing challenges: Working with these powders requires specialized equipment and expertise due to their unique properties. This can add complexity and cost to the manufacturing process.
- Limited availability: Certain high-temperature alloy powders might have limited availability or require longer lead times due to the specialized production processes involved.
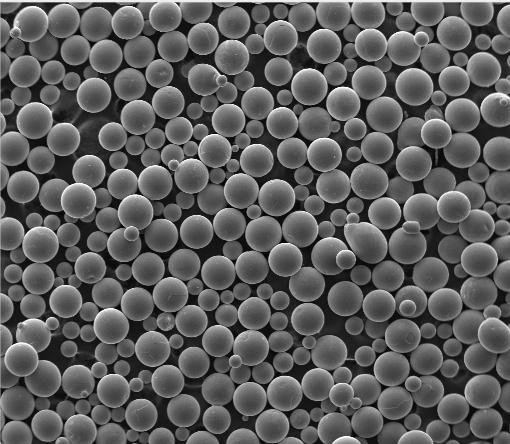
FAQs
Q: What are the different methods for producing high-temperature alloy powders?
A: Several methods exist for producing high-temperature alloy powders, including gas atomization, water atomization, and plasma atomization. Each method offers its own advantages and limitations in terms of powder size, shape, and cost.
Q: How are high-temperature alloy powders used in additive manufacturing?
A: High-temperature alloy powders are used in AM techniques like LPBF, where they are selectively melted and fused layer-by-layer to create complex three-dimensional objects. This allows for the creation of intricate components with high design freedom.
Q: What are the future prospects for high-temperature alloy powders?
A: The future of high-temperature alloy powders looks promising, driven by advancements in AM technologies and the increasing demand for lightweight, high-performance materials in various industries. As research and development continue, we can expect to see the development of new and improved powders with even more exceptional properties, further expanding their applications.
Conclusion
High-temperature alloy powders represent a revolutionary advancement in material science, pushing the boundaries of performance and enabling groundbreaking applications across diverse industries. Their exceptional combination of strength, heat resistance, and corrosion resistance makes them the go-to choice for demanding environments where conventional materials simply wouldn’t suffice. As technology continues to evolve and research delves deeper, the future of high-temperature alloy powders is undoubtedly bright, promising even more remarkable possibilities in the years to come.