High temperature alloy powders are materials that maintain their strength and durability at elevated temperatures. They are commonly used in applications that involve extreme heat like turbines, engines, and furnaces. This article provides a comprehensive overview of high temperature alloy powder including composition, properties, applications, specifications, pricing, safety, inspection, advantages, limitations and more.
Composition of High Temperature Alloy Powder
High temperature alloys are complex materials precisely engineered to withstand intense heat and stress. Their composition includes mixtures of metals like nickel, cobalt, iron, chromium, aluminum, titanium, tungsten, molybdenum, tantalum, rhenium. Trace elements like carbon, boron, zirconium, hafnium are also added.
Alloy Type | Major Alloying Elements |
---|---|
Nickel Based | Ni, Cr, Co, Mo, W, Nb, Ta, Al, Ti |
Cobalt Based | Co, Cr, Ni, W, Mo |
Iron Based | Fe, Cr, Al, Ni, Co, Ti, Mo, W |
Titanium Based | Ti, Al, Sn, Zr, Mo |
Nickel and cobalt are the primary base metals. Iron, chromium, aluminum and titanium are key alloying elements. The composition is optimized to impart unique properties like strength, oxidation resistance, thermal fatigue resistance etc. at high temperatures.
Properties of High Temperature Alloy Powder
The alloying elements in high temperature powders impart exceptional properties that make them suitable for extreme environments up to 1100°C or more.
Property | Description |
---|---|
High Strength | Maintain yield strength and creep resistance at high temperatures |
Oxidation Resistance | Form protective oxide layer to resist oxidation and corrosion |
Phase Stability | Microstructure and properties remain stable over time |
Thermal Fatigue Resistance | Withstand repeated heating and cooling cycles without cracking |
Creep Resistance | Resist deformation under sustained loads at high temperature |
Thermal Conductivity | Conduct and dissipate heat effectively |
Through precise composition control, these alloys achieve an optimal balance of properties like tensile strength, hardness, ductility, and thermal conductivity.
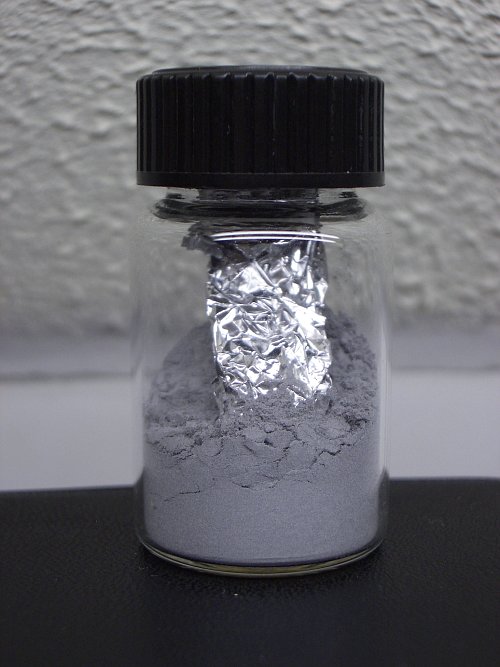
Applications of High Temperature Alloy Powder
The unique properties of high temperature alloy powders make them suitable for demanding applications in extreme environments:
Industry | Applications |
---|---|
Aerospace | Jet engines, turbine blades, exhaust systems |
Power Generation | Boilers, heat exchangers, steam and gas turbines |
Automotive | Turbochargers, exhaust valves, catalytic converters |
Industrial | Kilns, furnaces, incinerators, heat treatment equipment |
Petrochemical | Crackers, reactors, piping and valves |
These alloys enable components to withstand intense heat, pressure, and mechanical stress in critical systems. Their use improves efficiency, performance, safety, and reliability.
High Temperature Alloy Powder Specifications
High temperature alloy powders are available in various compositions, sizes, and forms to suit different manufacturing processes:
Parameter | Options |
---|---|
Alloy Grade | IN, MAR, Waspaloy, René, Haynes, Inconel, Hastelloy |
Particle Size | 15-45, 45-75, 75-250 microns |
Particle Shape | Spherical, porous, irregular |
Purity | 99.9%, 99.99% and higher |
Manufacturing Process | Gas atomized, water atomized, plasma rotated electrode process (PREP) |
Supply Form | Powder, paste, slurry, granules, pellets |
The grade, particle size distribution, shape and purity are specified based on the application requirements and manufacturing process limitations.
High Temperature Alloy Powder Pricing
High temperature alloy powders are more expensive than common metals due to complex compositions and special manufacturing processes:
Alloy | Price Range per Kg |
---|---|
Nickel Superalloys | $50 – $120 |
Cobalt Superalloys | $70 – $250 |
Iron Based Alloys | $20 – $60 |
Titanium Alloys | $100 – $600 |
Prices depend on alloy composition, particle size, manufacturing process, purity levels, order quantity and supply-demand dynamics. Custom alloys and special processing increase costs further.
High Temperature Alloy Powder Handling and Storage
Safe handling and proper storage helps maintain composition, properties and prevents contamination of high temperature alloy powders:
- Wear PPE like respiratory protection, gloves, eye protection when handling
- Avoid dust formation and ignition sources – powders are flammable
- Store sealed in original containers in a cool, dry place
- Avoid exposure to moisture – use desiccants if required
- Limit repackaging and dispensing only in ventilated areas
Following manufacturer’s recommendations for transportation, handling and storage is important. Take precautions against accidental inhalation or ingestion.
Safety Considerations for High Temperature Alloy Powder
High temperature alloy powders may pose certain health and safety hazards:
Hazard | Precautions |
---|---|
Dust Explosion | Avoid ignition sources, mitigate dust |
Toxicity | Use respiratory protection, minimize exposure |
Skin/Eye Irritation | Wear protective equipment |
Fire | Store away from flammables and ignition sources |
Reactivity | Some alloys may be moisture sensitive or pyrophoric |
Proper PPE, engineering controls, good housekeeping and training helps mitigate risks involved in handling fine metal powders. Follow manufacturer’s SDS and local regulations.
Inspection and Testing of High Temperature Alloy Powder
To ensure powders meet the required specifications, various inspection and testing procedures are used:
Method | Parameters Inspected |
---|---|
Optical microscopy | Particle size distribution, morphology |
Laser diffraction | Precise particle size analysis |
SEM/EDS | Particle shape, elemental composition |
XRD | Phase identification, crystal structure |
Pycnometry | Density, porosity |
Hall flowrate | Powder flowability |
Tap density test | Packed density |
By testing both physical characteristics and chemical composition, the alloy powder quality can be verified. This data helps optimize parameters for the application process.
Pros and Cons of High Temperature Alloy Powder
Advantages | Limitations |
---|---|
Withstand extreme temperatures | Expensive compared to steel or aluminum |
High strength-to-weight ratio | Limited number of suppliers globally |
Superior corrosion resistance | Complex compositions with exotic elements |
Oxidation and wear resistance | Require specialized manufacturing and processing |
Enables lightweight, efficient designs | Sensitive to contamination during production and handling |
Customizable properties | Difficult to machine or weld |
Understanding the trade-offs helps select the optimal alloy for specific application requirements and operating conditions.
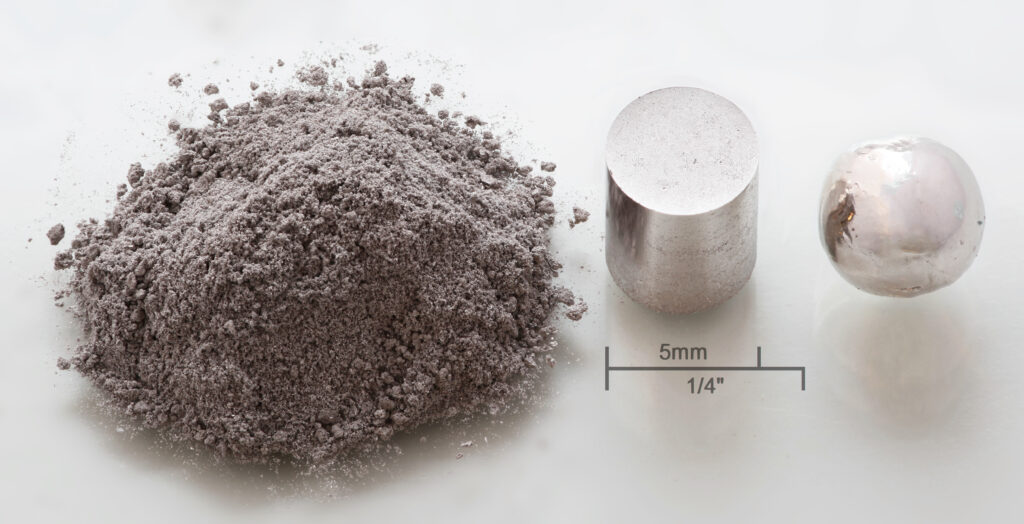
Comparison of High Temperature Alloy Powder Manufacturing Processes
Gas Atomization | Water Atomization | Plasma Rotating Electrode | |
---|---|---|---|
Method | Molten alloy disintegrated by high pressure gas jet | Disintegration by high speed water jet | Centrifugal disintegration of molten alloy in plasma jet |
Particle Shape | Mostly spherical | Irregular, satelliting | Spherical |
Particle Size | 15 – 150 μm | 20 – 300 μm | 15 – 125 μm |
Size Distribution | Narrow | Broad | Narrow |
Purity | High | Moderate | High |
Oxygen Pickup | Low | Moderate | Low |
Cost | High | Low | Moderate |
Gas atomization and PREP allow precise control over particle size, shape and oxygen content. Water atomization is economical but has limitations. The process is selected based on application requirements.
FAQs
Q: What are the main advantages of using high temperature alloy powder?
A: The main advantages are the ability to retain high strength and resistance to heat, corrosion, and oxidation at elevated temperatures exceeding 1000°C in some cases. This enables lightweight, efficient component designs for extreme environments.
Q: What industries use high temperature alloy powder the most?
A: Aerospace is the largest consumer due to the high-temperature requirements of aircraft engines, followed by power generation, automotive, and petrochemical industries.
Q: What precautions are necessary when handling high temperature alloy powder?
A: It is important to minimize dust, avoid ignition sources, wear PPE to limit exposure, and follow proper procedures for storage and handling to prevent contamination or accidents.
Q: What are some examples of common high temperature alloy grades?
A: Some popular grades include Inconel, Hastelloy, Haynes, René, Waspaloy, and MAR-M series nickel and cobalt based alloys. Each has a tailored composition for specific temperature capabilities.
Q: What manufacturing techniques are used to produce high temperature alloy powder?
A: Main methods include gas atomization, water atomization and plasma rotating electrode process. Each has advantages and limitations. Gas atomization offers the most control over particle characteristics.
Q: How much does high temperature alloy powder cost compared to other metals?
A: These alloys are significantly more expensive than carbon steel, stainless steel or aluminum due to complex compositions, high purity requirements, and special manufacturing processes. Cost can range from $20 per kg for iron-based alloys up to $600 per kg for specialized grades.
In summary, high temperature alloy powders are indispensable materials for applications involving extreme environments thanks to their precisely engineered composition and properties. With proper handling and processing, they can be fabricated into high performance components capable of withstanding intense heat and stress. Their unique capabilities come at a premium cost which is justified for critical applications in aerospace, power generation and other industries.