HIP Technology
Hot Isostatic Pressing (HIP) technology works by placing the product in a closed container, filling it with inert gas and sintering or densifying the product at a very high temperature (usually close to the forging temperature of the material) and at a very high pressure (usually 100 – 140 MPa). This allows the product to be sintered or densified. For metallic materials, hot isostatic pressing technology can achieve densification to eliminate defects because: at high temperatures, metal materials have very low strength and excellent plasticity, the metal in the area of the hole is subjected to external gas pressure and plastic deformation occurs, the metal in the area of the hole is in contact with each other and the metallurgical structure causes the hole to disappear.
What is HIP Technology
The main parameters of the hot isostatic pressing process are heating temperature, gas pressure, holding time, and gas medium. Different materials selected temperature, pressure, holding time are very different, mainly based on the material solid phase change and high-temperature strength, plasticity selection process parameters. For example, the TC4 titanium alloy hot isostatic pressing process is usually 920 ℃ and 110 – 120 MPa conditions of insulation 1 – 2 hours, inert gas using argon.
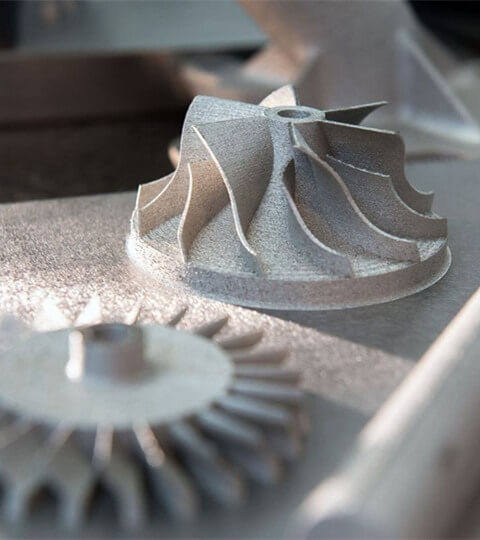
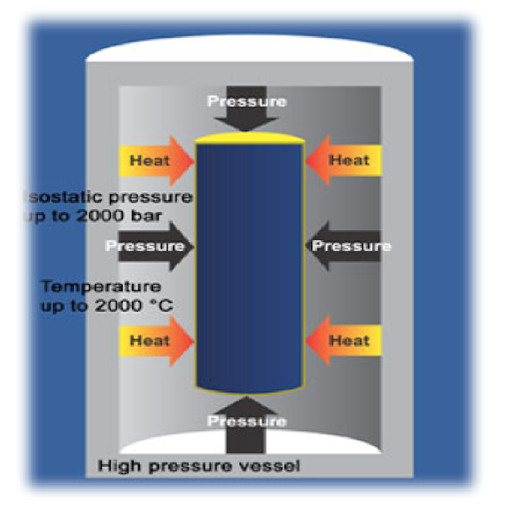
HIP Technology Process Principle
HIP technology is now widely used in cemented carbide sintering, densification of refractory metals and alloys such as tungsten, aluminium and titanium, defect repair of products (e.g. 3D printed metal parts), near net forming of large and shaped components, production and processing of composite materials and special materials.The role of hot isostatic pressing for 3D printed metal parts
Hot isostatic pressing can eliminate internal defects. As mentioned above, the application of hot isostatic pressing in the field of 3D printing is to eliminate defects inside the final part.
Hot isostatic pressing can improve subcooled or sub-stable tissue formed by excessive cooling rates. Hot isostatic pressing usually involves heating at a very high temperature, equivalent to a high temperature annealing process. Hot isostatic pressing completely eliminates the martensite and other tissues formed during rapid forming due to the rapid cooling rate, thus transforming the tissues into a high temperature annealed form.
Process Characteristics
Hot isostatic pressing can improve mechanical properties. Whether it is laser SLM forming or electron beam EBM forming, there is a tendency for the strength of the material to decrease and the plasticity to increase after hot isostatic pressing, especially for materials with SLM technology. The reason for this phenomenon is that the cooling rate of the SLM forming process is faster and more martensite is formed in the formed part, which decomposes after HIP annealing, causing the strength of the material to drop and the plasticity to rise. At the same time, the hardness of the material will also change with HIP, with a 5-10% drop in hardness after HIP. Overall, hot isostatic pressing improves the material’s toughness and resistance to fatigue crack extension.
Limitations of hot isostatic pressing treatment
Hot isostatic pressing does not work well on any material and for any defect elimination, and improper setup of the hot isostatic pressing process can have very serious consequences, so the following should be noted when using hot isostatic pressing.
(1) For open defects (defects that extend from the inside of the part to the surface of the part and the external gas medium) hot isostatic pressing does not have any effect on the elimination of defects.
(2) When a large defect (over 2mm) exists within the part it will form a crater on the surface of the part, as shown in Figure 5, and will require welding to repair. When the crater is in a position where a weld repair is not possible, it may result in the scrapping of the part, such as some thin-walled parts, thin-walled parts or blades.
(3) No effect on the elimination of cracks and inclusions defects.
(4) Hot isostatic pressing may cause oxidation of the surface of the part, forming a thin oxide film, preferably between finishing operations.
(5) Hot isostatic pressing may cause severe distortion of the part and measures to prevent distortion should always be considered before doing so.
(6) Improperly set process temperatures and pressures may result in thinning of the wall thickness of the part and, in severe cases, in severe coarsening of the grain size of the part, resulting in poor material properties and scrap of the part.
(7) For alloys with large differences in melting points of alloying elements may result in burnout of low melting point chemical elements.
(8) Not suitable for eutectic alloys, easy to form liquefaction cracks.