Overview
Hot Isostatic Pressing (HIP) is a critical manufacturing process used in the field of materials science and engineering. It combines high temperature and high-pressure gas to eliminate porosity in metals and improve their mechanical properties. This article will dive deep into the specifics of HIP, exploring its composition, characteristics, applications, and various metal powder models used in this process. We’ll also compare the pros and cons of HIP, discuss the advantages and limitations, and provide detailed tables to facilitate understanding.
What is Hot Isostatic Pressing (HIP)?
Hot Isostatic Pressing (HIP) is a manufacturing process that applies high temperature and pressure uniformly to materials, enhancing their mechanical properties and eliminating internal defects such as pores and voids. This process is particularly significant in the production of high-performance components used in aerospace, automotive, medical implants, and other industries requiring superior material properties.
How Does HIP Work?
HIP works by placing the material inside a high-pressure vessel filled with an inert gas, usually argon. The vessel is then heated to a temperature that allows the material to deform plastically. Under these conditions, the gas pressure eliminates internal voids and densifies the material, resulting in a component with enhanced mechanical properties and structural integrity.
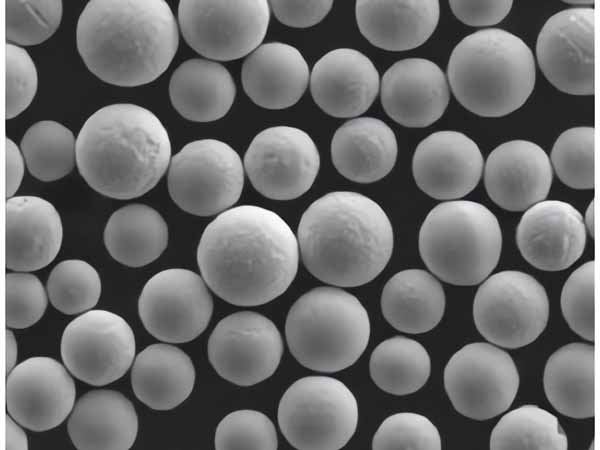
Composition of Hot Isostatic Pressing (HIP)
HIP involves a variety of metal powders, each with unique compositions tailored to specific applications. Here are ten commonly used metal powder models:
Metal Powder Models and Descriptions
Metal Powder Model | Description |
---|---|
1. Ti-6Al-4V | A titanium alloy known for its high strength-to-weight ratio and corrosion resistance, commonly used in aerospace and biomedical applications. |
2. Inconel 718 | A nickel-chromium alloy with excellent high-temperature strength and oxidation resistance, used in gas turbines and aerospace components. |
3. 316L Stainless Steel | An austenitic stainless steel with low carbon content, offering excellent corrosion resistance and good formability, ideal for medical and food processing equipment. |
4. CoCrMo | A cobalt-chromium-molybdenum alloy known for its wear resistance and biocompatibility, often used in medical implants. |
5. AlSi10Mg | An aluminum alloy with good castability and high strength, used in automotive and aerospace industries. |
6. Maraging Steel | A high-strength steel alloy with excellent toughness, used in aerospace and tooling applications. |
7. CuCrZr | A copper alloy with high strength and thermal conductivity, suitable for electrical and heat exchanger components. |
8. H13 Tool Steel | A chromium-molybdenum hot work steel with excellent toughness and heat resistance, used in die casting and forging tools. |
9. Ti-5Al-2.5Sn | A titanium alloy with high strength and good weldability, used in aerospace and marine applications. |
10. Rene 41 | A nickel-based superalloy with excellent high-temperature strength and oxidation resistance, used in jet engines and gas turbines. |
Characteristics of Hot Isostatic Pressing (HIP)
Key Characteristics
Characteristic | Description |
---|---|
High Density | HIP produces components with near-theoretical density, eliminating internal voids and defects. |
Uniform Properties | The process ensures uniform mechanical properties throughout the material. |
Improved Strength | HIP-treated materials exhibit enhanced tensile and yield strengths. |
Enhanced Fatigue Life | Materials processed by HIP have improved fatigue resistance due to the elimination of internal flaws. |
Superior Toughness | The process improves the toughness of materials, making them less prone to brittle fracture. |
Corrosion Resistance | HIP can enhance the corrosion resistance of certain alloys. |
Applications of Hot Isostatic Pressing (HIP)
Common Applications
Application | Description |
---|---|
Aerospace Components | HIP is used to produce high-performance parts like turbine blades and structural components. |
Medical Implants | The process ensures the biocompatibility and mechanical strength of implants. |
Automotive Parts | HIP-treated components are used in high-stress environments like engines and transmissions. |
Power Generation | The process is used in the production of components for gas and steam turbines. |
Tooling and Molds | HIP improves the life and performance of die casting and forging tools. |
Oil and Gas | Components like valves and fittings benefit from the enhanced properties provided by HIP. |
Nuclear Industry | The process is used to produce components for reactors and other critical applications. |
Military and Defense | HIP-treated materials are used in the production of armor and weaponry. |
Electronics | The process ensures the reliability of components used in electronic devices. |
Custom Prototyping | HIP is used to produce high-quality prototypes with excellent mechanical properties. |
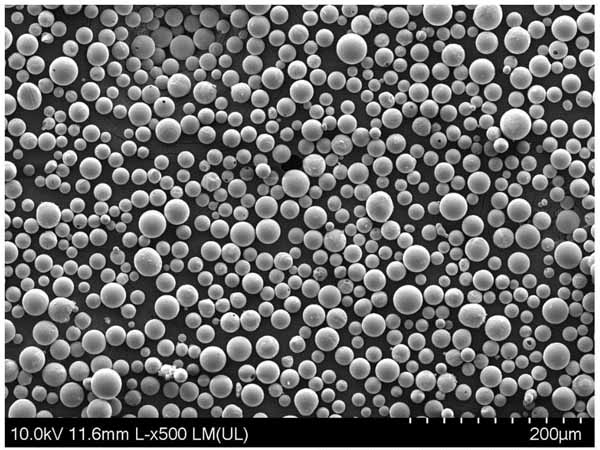
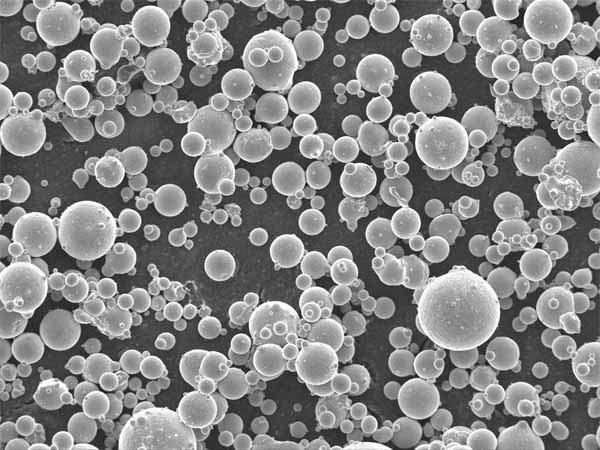
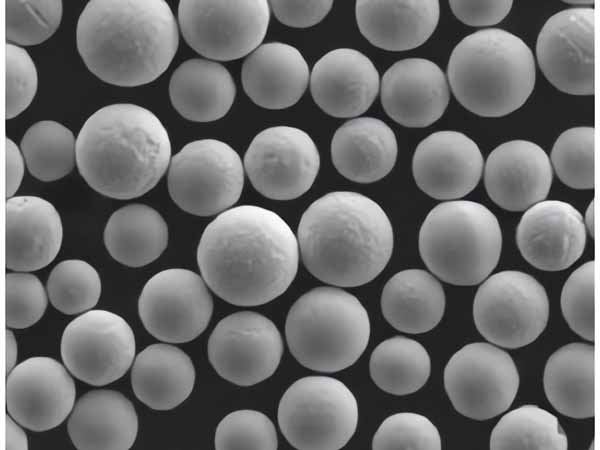
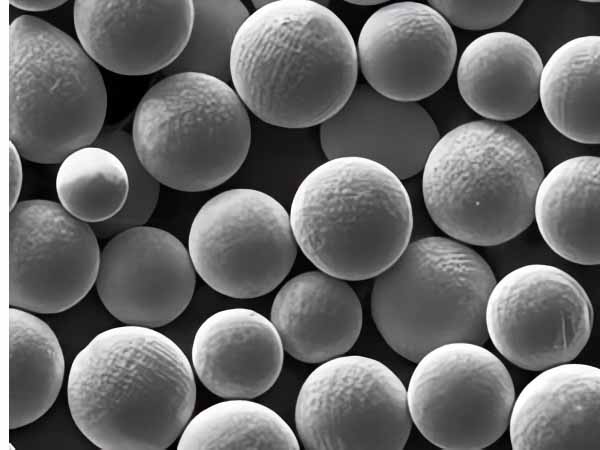
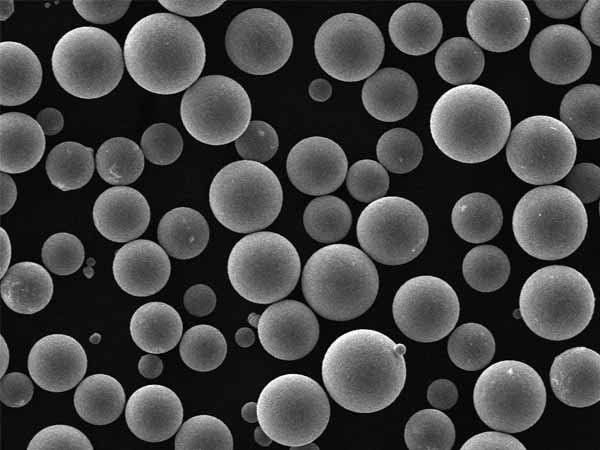
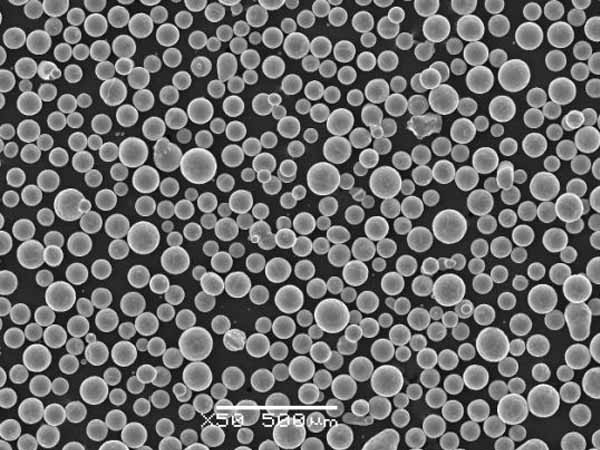
Specifications, Sizes, Grades, Standards of HIP Products
Common Specifications
Specification | Description |
---|---|
Density | Near-theoretical density, typically >99% |
Temperature Range | Up to 2000°C, depending on the material |
Pressure Range | Up to 200 MPa |
Cycle Time | Varies from hours to days based on material and component size |
Material Grades | Various grades of metals and alloys, including titanium, nickel-based superalloys, stainless steels, etc. |
Standards | ASTM F2924, AMS 4991, ISO 5832-3, etc. |
Suppliers and Pricing Details
Leading Suppliers
Supplier | Products Offered | Price Range |
---|---|---|
Bodycote | Full range of HIP services for various industries | Pricing varies by project |
Quintus Technologies | HIP systems and equipment | Custom quotes based on specifications |
Kennametal Stellite | HIP-treated metal powders and components | Varies by material and quantity |
Carpenter Technology | Specialty alloys and HIP services | Custom pricing available |
Arcam AB | Metal powders and HIP services for additive manufacturing | Varies by project scope |
Plansee Group | Refractory metals and HIP processing | Custom quotes provided |
Sandvik Materials Technology | Metal powders and HIP services | Price dependent on material and application |
Precision Castparts Corp | Aerospace components and HIP services | Custom pricing based on project |
ATI Metals | Specialty materials and HIP processing | Pricing varies by material and quantity |
GKN Powder Metallurgy | Metal powders and HIP-treated components | Custom quotes based on specifications |
Pros and Cons of Hot Isostatic Pressing (HIP)
Advantages and Limitations
Advantages | Limitations |
---|---|
Eliminates Porosity | High equipment and operational costs |
Improves Mechanical Properties | Requires specialized equipment |
Uniform Material Properties | Long processing times for large components |
Enhances Fatigue and Creep Resistance | Limited to materials that can withstand high temperatures and pressures |
Can Process Complex Geometries | Potential for microstructural changes in some materials |
Reduces Material Waste | Not suitable for all types of materials |
Improves Surface Finish | Requires precise control of process parameters |
Comparing HIP with Other Metal Processing Techniques
HIP vs. Traditional Sintering
Parameter | HIP | Traditional Sintering |
---|---|---|
Density | Near-theoretical density | Typically 90-95% density |
Mechanical Properties | Superior | Good but lower than HIP |
Porosity | Eliminates porosity | Some residual porosity |
Processing Time | Longer | Shorter |
Cost | Higher | Lower |
Applications | High-performance components | General applications |
HIP vs. Casting
Parameter | HIP | Casting |
---|---|---|
Density | Near-theoretical density | Varies, typically lower |
Mechanical Properties | Enhanced | Good but lower than HIP |
Porosity | Eliminates porosity | Possible porosity issues |
Surface Finish | Improved | May require post-processing |
Complexity of Shapes | Can handle complex geometries | Limited by casting techniques |
Cost | Higher | Lower |
HIP vs. Forging
Parameter | HIP | Forging |
---|---|---|
Density | Near-theoretical density | High density |
Mechanical Properties | Superior | Excellent |
Porosity | Eliminates porosity | Minimal porosity |
Processing Flexibility | Can handle complex shapes | Limited to simpler shapes |
Cost | Higher | Moderate |
Applications | High-performance components | Structural components |
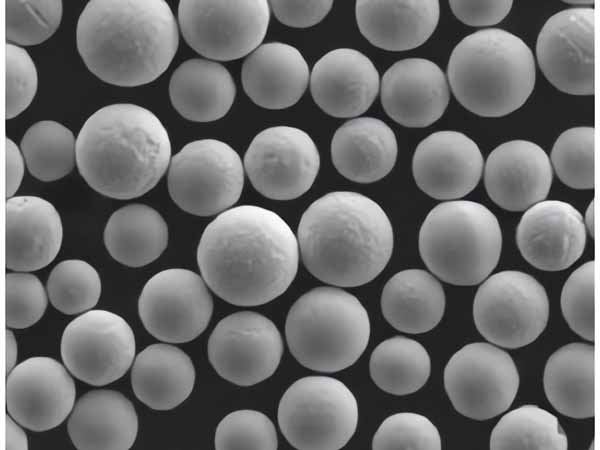
FAQ
Question | Answer |
---|---|
What is HIP used for? | HIP is used to improve the mechanical properties and density of materials, eliminating porosity and enhancing performance in high-stress applications. |
How does HIP work? | HIP involves placing materials in a high-pressure vessel filled with inert gas, heating them to high temperatures, and applying uniform pressure to eliminate internal voids. |
What materials can be processed using HIP? | Various metals and alloys, including titanium, nickel-based superalloys, stainless steels, aluminum alloys, and more. |
What are the advantages of HIP? | HIP offers high density, improved mechanical properties, uniform material properties, enhanced fatigue resistance, and the ability to process complex geometries. |
Are there any limitations to HIP? | HIP is associated with high costs, requires specialized equipment, has long processing times for large components, and is limited to materials that can withstand high temperatures and pressures. |
How does HIP compare to traditional sintering? | HIP achieves near-theoretical density and superior mechanical properties, eliminates porosity, but has higher costs and longer processing times compared to traditional sintering. |
Is HIP suitable for all materials? | No, HIP is not suitable for materials that cannot withstand the high temperatures and pressures involved in the process. |
What industries benefit most from HIP? | Aerospace, medical, automotive, power generation, tooling, oil and gas, nuclear, military and defense, electronics, and custom prototyping industries. |
Can HIP process complex shapes? | Yes, HIP can handle complex geometries and shapes, making it suitable for producing intricate components. |
What is the cost range for HIP services? | The cost varies depending on the material, component size, and project specifications, with custom quotes provided by suppliers. |
Hot Isostatic Pressing (HIP) stands as a transformative technology in the field of materials science and engineering, offering unmatched improvements in material density, mechanical properties, and overall performance.