Inconel 625 is a nickel-chromium-molybdenum alloy used across demanding applications requiring high strength oxidation and corrosion resistance. This guide covers Inconel 625 powder types, composition, specifications, manufacturing methods, suppliers, costs, pros/cons, and comparisons to inform buyers.
Inconel 625 Powder Overview
Inconel 625 metal alloy powder enables industrial additive manufacturing and thermal spray coating applications needing extreme temperature, pressure, and chemical resistance. Key attributes:
- Excellent strength up to 2100°F without melting
- Resists corrosion in severely oxidizing, sulfuric, and chloride environments
- Maintains flexibility without cracking under prolonged thermal fatigue cycling
- Nickel content drives corrosion resistance mechanisms
- Powder production methods create optimized particles for AM or thermal spray
With versatility spanning aerospace, chemical, and oil/gas sectors, understanding Inconel 625’s composition, powder specifications, use case tradeoffs, and procurement factors empowers engineers in leveraging this nickel superalloy effectively across industry.
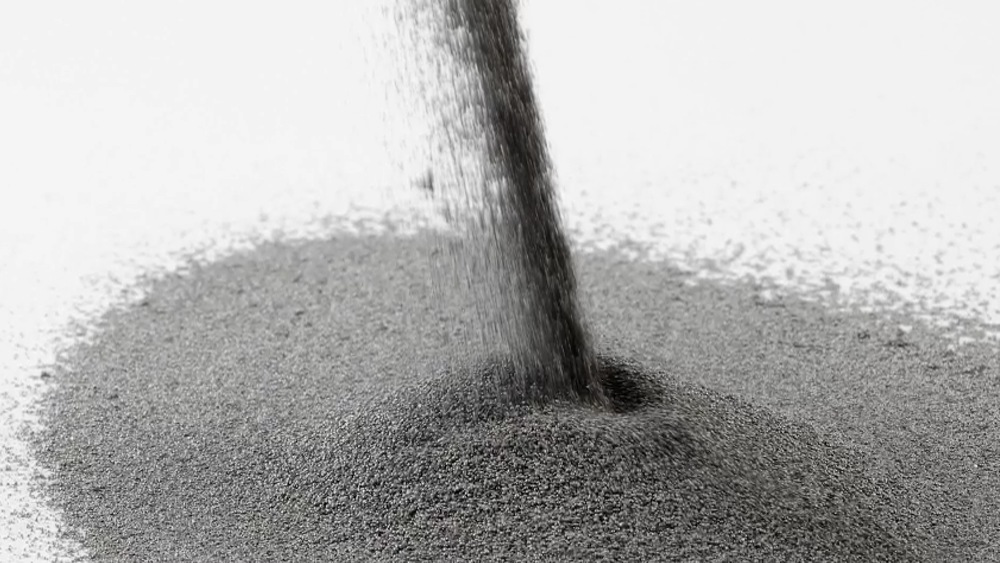
Composition of Inconel 625 Powder
Inconel 625 alloys blend nickel, chromium, molybdenum with small amounts of niobium and iron:
Element | Concentration Range | Role |
---|---|---|
Nickel | 58.0 – 63.0% | Corrosion resistance in organic and inorganic environments |
Chromium | 20.0 – 23.0% | Forms protective chromia oxide layer resisting oxidation up to 2100°F |
Molybdenum | 8.0 – 10.0% | Solid solution strengthener. Improves mechanical properties. |
Niobium | 3.15 – 4.15% | Carbide former increasing high temperature strength |
Iron | Remainder | Cost saver that can reduce ductility and oxidation resistance versus pure nickel |
Table 1. Chemical composition ranges and element functionality within Inconel 625 nickel alloy
The balanced blend resists corrosive environments up to 1300°F. Varying elements like aluminum, titanium or tungsten creates specialty derivatives for focused enhancements.
Inconel 625 Powder Characteristics and Properties
Physical Properties
- Density: 8.44 g/cm3
- Melting Point: 2,410°F
- Maximum Service Temperature: 2100°F
Mechanical Properties
- Tensile Strength: 110 ksi
- Yield Strength: 56 ksi
- Elongation at Break: 55%
- Hardness: 25 HRC
Performance Properties
- Corrosion Resistance: Resists pitting and crevice corrosion in acids, chlorides, sulfides and other aggressors especially at high temperatures
- Oxidation Resistance: Surface chromia layer provides exceptional oxidation resistance up to 2100°F
Blending high strength under prolonged 2100°F heat alongside unbeaten corrosion protection from sulfidation, oxidation, and saltwater makes this superalloy indispensible where alternatives fail rapidly.
Particle Size Specifications for Inconel 625 Powder
Inconel 625 powder is produced in various size distributions based on usage:
Application | Size Range | Particle Morphology |
---|---|---|
Additive Manufacturing | 15-45 microns | Spherical |
Thermal Spray Coating | -45 +10 μm <5% >106 μm | Irregular angular |
Table 2. Industry grade powder size ranges and shapes demanded by AM versus thermal spray processes
Tighter distributions with near perfect sphericity support flowability in laser powder bed fusion 3D printers. Thermal spraying can accommodate wider distributions accepting some satellites without impacting coating integrity.
Inconel 625 Powder Production Methods
Key Inconel 625 powder manufacturing approaches include:
Gas Atomization – High purity ingots melted in inert atmospheres then impacted by supersonic gas jets, converting the molten stream into spherical droplets solidifying into powder. The rapid solidification produces finer grain structures tuned for additive manufacturing usage. But the batch method struggles achieving the 100+ tons annually required by high volume thermal spray industries.
Rotating Electrode Process – In this continuous wire production method, an electrically charged wire feeds towards an oppositely charged spinning disk which throws molten material off as droplets that solidify into powder. Lower purity and surface quality makes this more suitable for thermal spraying applications versus AM usage. The continuous nature enables very high volume output for industrial coating applications.
Plasma Rotating Electrode Process – By rotating and feeding a wire into a plasma hotter than traditional REP processes, higher particle purity and surface quality is achieved. The plasma’s energy melts more incoming wire enabling continuous production suitable for mid-volume thermal spray demand levels.
Matching production techniques to end application quality and volume requirements ensures availability of appropriately priced Inconel 625 feedstock powder when demanded by manufacturing systems.
Inconel 625 Powder Industry Specifications
Governments, trade groups, and individual companies issue various Inconel 625 material and powder standards. Common ones include:
Standard | Description |
---|---|
AMS 5666 | Aerospace Material Specification issued by SAE International |
ASTM B446 | American Society for Testing and Materials standard for Nickel alloy |
ASME SB-443 | Boiler and Pressure Vessel Code Spec |
AWS A5.14 | American Welding Society Nickel alloy welding electrode specification |
MIL-N-13161 | Military grade Inconel 625 forged bar and plate |
Praxair 1701 | Thermal spray grade powder specification |
Table 3. Various public standards and company specifications applicable to Inconel 625 powder material and quality requirements
Review specifications to ensure powder chemical, physical property, particle size distribution, and quality thresholds match expected production process needs and capabilities.
Inconel 625 Powder Applications
Leveraging high temperature corrosion resistance with manufacturing adaptability enables Inconel 625 usage across industries:
Additive Manufacturing
- Aerospace: Turbine blades, impellers and combustion components
- Chemical: Pumps, valves and vessels resisting corrosion
- Oil/Gas: Wellhead Christmas trees and drill tools expose to sulfidation
Thermal Spray Coating
- Firearm bolts need hardness plus release capability
- Printing roll surfaces withstand abrasion
- Aircraft hydraulic actuators see problematic saltwater exposure
- Offshore risers and reaction vessels fight sea water corrosion
Applicable anywhere needing stainless steel’s strength but further gains in oxidation and chemical resistance – especially under flexing dynamic loads across sustained heat.
Inconel 625 Powder Manufacturers and Suppliers
Prominent global suppliers providing Inconel 625 powder include:
Supplier | Description |
---|---|
Sandvik Osprey | Leading producer of nitinol and nickel superalloys via atomization. Known for spherical powders. |
Carpenter Technology | Major producer of specialty alloy ingots and powders. |
Höganäs | Significant inventor and producer of metal powders by atomization and HDH. |
PyroGenesis Canada | Specializes in very high purity plasma atomized titanium and nickel powders |
Tekna Advanced Materials | Investment casting superalloy powders. |
Table 4. Major commercial suppliers globally providing various Inconel 625 powder stock options
Be sure to evaluate manufacturers against needed capacity, quality certifications, and specialty process capabilities when sourcing.
Inconel 625 Powder Pricing
Inconel 625 pricing fluctuates with nickel index commodity pricing given concentration sensitivity. Current pricing averages:
Type | Price Per Kilogram |
---|---|
Additive manufacturing grade | $50+ |
Thermal spray grade | $30+ |
Alloy wire/rod | $15+ |
Pricing depends on powder production and qualification investments. Comparing against resulting mechanical properties and lifespan determines actual value against alternatives like 316L stainless steel costing 60-70% less.
Pros and Cons of Inconel 625 Powder
Advantages | Disadvantages |
---|---|
Resists oxidation/corrosion up to 2100°F | Costs 4-10X austenitic/ferritic stainless alternatives |
Retains ductility after prolonged heat cycling | Requires hot isostatic pressing to consolidate poorer flowing atomized powders |
Handles strongly reducing acids | Lower tensile strength than steel alternatives |
Powder production flexibility enables usage growth | Sensitive to control of elemental additions during production |
Table 5. Tradeoffs to consider when evaluating usage of Inconel 625 powder
Maximizing strengths while navigating limitations by avoiding overspecification ensures affordable deployment only where truly needing exceptional temperature corrosion resistance.
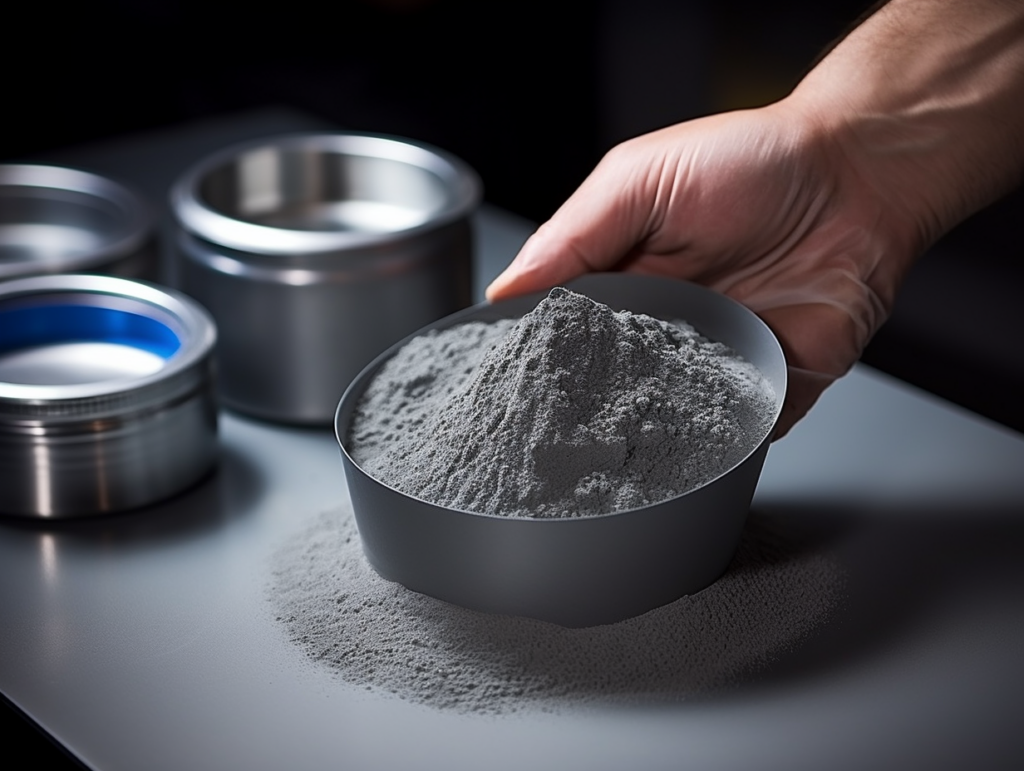
Comparison to Stainless Steel Powder Materials
Versus alternatives like 316/304 stainless steel powders, Inconel 625 contrasts:
Parameter | Inconel 625 | 316/304 Stainless Powder |
---|---|---|
Cost | 4-10X higher | Low material cost per lb/kg |
Temperature Resistance | Resists oxidation up to 2100°F | Loses strength rapidly above 900°F |
Chemical Resistance | Virtually impervious to organic and oxidizing acids | Susceptible to chloride pitting and acid corrosion |
Thermal Fatigue | Excellent flexibility without cracking through cycles | Develops microfissures degrading properties |
Welding Compatibility | Challenging to successfully fuse material without cracking | Much simpler welding characteristics |
Table 6. Comparing properties of Inconel 625 nickel superalloy powder versus stainless steel alternatives
Inconel 625 powder steals applications needing stainless steel strength coupled with thermal heat/chemical resistance otherwise rapidly degrading alternatives.
FAQ
Q: Does Inconel 625 powder require hot isostatic pressing when 3D printed?
A: Yes, poorer flowing atomized particles benefit from HIP to eliminate internal porosity, improving fatigue resistance.
Q: What particle size is best for laser powder bed fusion additive manufacturing?
A: 15-45 microns ensures dense packing with good interparticle bonding. Anything above 45μm struggles in additive system material beds.
Q: Is Inconel 625 weldable?
A: Yes but matching filler material crystal structure and minimizing carbon intake is critical to avoid post-weld cracking around heat affected zones.
Q: What industries use Inconel 625 coatings?
A: Aerospace, oil/gas valves and pumps, chemical and paper machine rolls all leverage corrosion and heat resistance.
Q: Does recycled Inconel 625 retain original properties?
A: Yes, powder can reuse spatter powder without issue. Components can remelt into specification chemistry and microstructures.