Imagine a material so strong, it can withstand scorching temperatures that would melt your average barbeque grill. Imagine it being so resistant to corrosion, even the saltiest ocean depths wouldn’t stand a chance. That’s the magic of Inconel 625 powder, a superhero amongst metal powders, boasting exceptional properties that make it the go-to choice for demanding applications.
Properties of Inconel 625 Powder
Property | Description |
---|---|
High-Temperature Strength | Withstands extreme temperatures exceeding 1800°F (982°C), making it ideal for jet engines, turbines, and heat exchangers. |
Excellent Corrosion Resistance | Resists a wide range of corrosive environments, including acidic solutions, saltwater, and high-temperature gases. |
Oxidation Resistance | Maintains its strength and integrity even at elevated temperatures due to its resistance to forming oxides. |
Good Weldability | Can be readily joined using various welding techniques, crucial for complex component fabrication. |
Ductility and Formability | Can be shaped and formed into intricate designs, offering design flexibility. |
This unique combination of properties makes Inconel 625 powder a versatile material for various applications, pushing the boundaries of engineering possibilities.
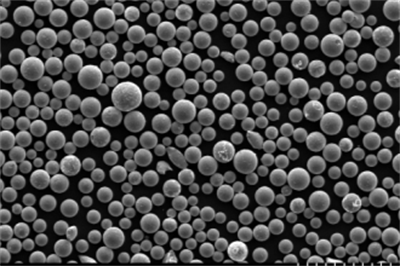
Different Models of Inconel 625 Powder
While Inconel 625 powder reigns supreme, there are variations within its ranks, each tailored for specific applications. Here’s a closer look at ten prominent models:
- AMDRY 625 (Oerlikon): This model excels in thermal spray applications, providing excellent high-temperature oxidation and corrosion resistance for restoring and repairing superalloy components.
- MSE PRO IN625 (MSE Supplies): This gas-atomized powder boasts a spherical shape and controlled particle size distribution, ideal for additive manufacturing (3D printing) of complex Inconel 625 parts.
- Water Atomized Inconel 625 (SLM Solutions): This water-atomized variant offers a cost-effective option for 3D printing applications, delivering good mechanical properties.
- Spherical Inconel 625 (3D Powder Hub): This spherical powder ensures smooth flow during the 3D printing process, enabling the creation of intricate geometries.
- IN625 Nickel Alloy Powder (GE Additive): Backed by the reputation of GE Additive, this powder promises high quality and consistency for demanding 3D printing needs.
- Inconel 625 Powder (Höganäs): Renowned for its tight particle size distribution, this powder is suitable for various additive manufacturing techniques, including laser melting and electron beam melting.
- Nickel Chrome Alloy Powder (Sandvik): This nickel-chromium alloy powder, similar to Inconel 625, offers a cost-conscious alternative for applications requiring good high-temperature strength and corrosion resistance.
- Inconel 625 Powder (AP&C): This AP&C offering provides a reliable source for Inconel 625 powder, catering to diverse industrial applications.
- Inconel 625 Powder (Albany Engineered Minerals): Engineered for optimal flowability, this powder minimizes waste during the additive manufacturing process.
- Custom Inconel 625 Powders (Various Suppliers): Several suppliers offer custom Inconel 625 powders with tailored properties, such as specific particle size distributions or enhanced flow characteristics, to meet unique application requirements.
A Breakdown of Key Differences
While all these models share the core properties of Inconel 625, some key differences set them apart. Here’s a breakdown to help you choose the right champion for your project:
- Production Method: Gas-atomized powders generally offer a more spherical shape and tighter size control compared to water-atomized variants, impacting flowability and printability in 3D printing.
- Particle Size Distribution: The size and distribution of particles significantly influence the final product’s properties. Finer powders can create smoother surfaces but may be more challenging to handle. Conversely, larger particles offer better flowability but might result in a rougher finish.
- Supplier Reputation: Consider the supplier’s experience and quality control processes when selecting a powder. Reputable brands often provide additional guarantees and technical support.
- Cost: Pricing can vary depending on the specific model, quantity, and supplier. Gas-atomized powders and those from high-profile brands typically come at a premium compared to water-atomized or lesser-known suppliers.
the Application of Inconel 625 Powder
Inconel 625 powder isn’t just another pretty face (well, maybe not literally); it’s a workhorse material that finds applications in various demanding industries:
Industry | Application Examples |
---|---|
Aerospace: | Turbine blades, combustor liners, afterburner components, due to its exceptional high-temperature strength and resistance to harsh environments. |
Chemical Processing: | Pressure vessels, heat exchangers, valves, for handling corrosive chemicals and high temperatures. |
Oil and Gas: | Downhole tools, wellhead components, for withstanding extreme downhole pressures and temperatures encountered during oil and gas extraction. |
Power Generation: | Gas turbine components, heat exchangers, for enduring the high temperatures and corrosive byproducts of combustion in power plants. |
Medical Devices: | Implants, surgical instruments, requiring biocompatibility, corrosion resistance, and strength for long-lasting performance in the human body. |
These are just a few examples; the potential applications of Inconel 625 powder are constantly expanding as engineers discover new ways to leverage its unique properties.
Specifications, Sizes, Grades, and Standards
So, you’re convinced Inconel 625 powder is the material for your project. Now comes the nitty-gritty: understanding the specifications, sizes, grades, and standards that define this versatile powder.
Specification | Description |
---|---|
Chemical Composition | Nominally 62.5% nickel, 20% chromium, 9% iron, with controlled amounts of molybdenum, niobium, and other elements depending on the specific model. |
Particle Size Distribution | Typically ranges from 15 to 150 microns, with customized options available from some suppliers. |
Apparent Density | Around 4.5 to 5.5 g/cm³, depending on the production method and particle size distribution. |
Flowability | Measured by various techniques, with higher flowability powders offering better handling characteristics in additive manufacturing. |
Available Particle Sizes
The particle size distribution of Inconel 625 powder plays a crucial role in the final product’s properties and manufacturability. Here’s a breakdown of commonly available sizes:
- Finer Powders (15-45 microns): Produce smoother surface finishes in 3D printed parts but may be more challenging to handle due to lower flowability.
- Mid-Range Powders (45-100 microns): Offer a good balance between surface finish and flowability, making them suitable for various 3D printing applications.
- Coarser Powders (100-150 microns): Provide excellent flowability but may result in a rougher surface finish. These are often tercihsied (preferred) for applications where dimensional accuracy is less critical, and high deposition rates are desired.
Grades and Standards
Inconel 625 powder typically adheres to various industry standards, including ASTM B168 (nickel-chromium alloy powder) and AMS 5662 (aerospace material specifications). These standards ensure consistent quality and meet the stringent requirements of different industries.
Suppliers and Pricing
Inconel 625 powder isn’t exactly pocket change. The cost can vary depending on several factors, including:
- Quantity: Larger quantities typically come at a discounted price per unit weight.
- Supplier: Reputable brands with stringent quality control processes may command a premium.
- Powder Characteristics: Gas-atomized powders and those with tighter particle size control are generally more expensive.
Here’s a ballpark range for Inconel 625 powder pricing (subject to change):
- Price per kilogram: $100 – $300+
It’s always recommended to contact potential suppliers directly for accurate quotes based on your specific needs.
Pros and Cons of Inconel 625 Powder
While Inconel 625 powder boasts impressive properties, it’s essential to consider both its advantages and limitations before making a decision.
Pros:
- Exceptional high-temperature strength and creep resistance
- Outstanding corrosion resistance in various environments
- Good weldability for complex component fabrication
- Ductility and formability for intricate designs
- Suitable for additive manufacturing (3D printing), enabling the creation of complex geometries.
Cons:
- High cost compared to many other metal powders.
- Relatively high melting point, requiring specialized equipment for processing (welding, 3D printing).
- Abrasive nature can wear down processing equipment, increasing maintenance costs.
- Health hazards: Nickel, a component of Inconel 625, can pose health risks if proper handling procedures are not followed.
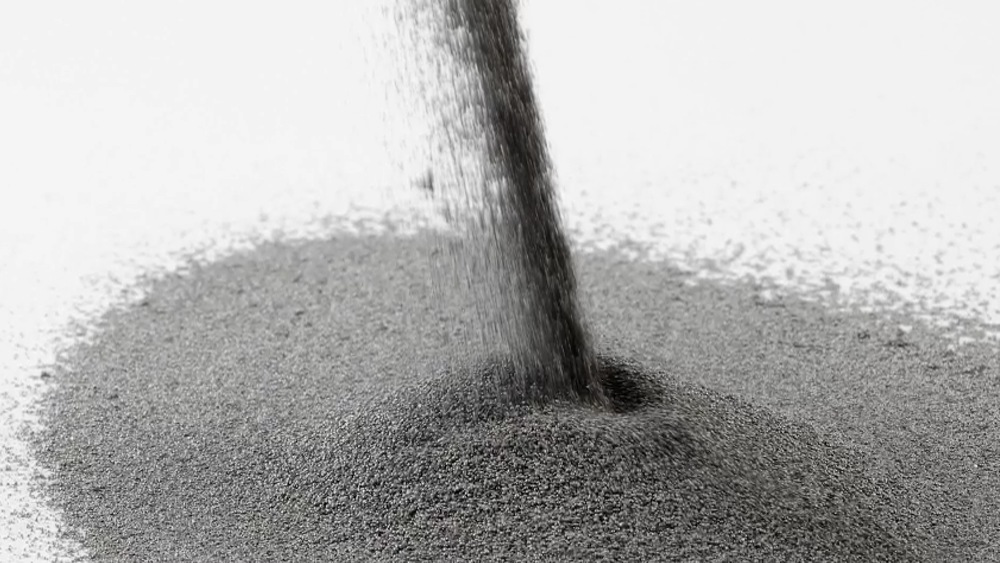
Making the Right Choice
The decision to use Inconel 625 powder depends on your specific application requirements. Here are some considerations:
- Is high-temperature strength and corrosion resistance paramount? If so, Inconel 625 powder might be the ideal choice, despite the higher cost.
- Are there alternative materials that offer similar properties at a lower cost? Explore other options like stainless steels or nickel-based superalloys if cost is a major concern.
- Do you have the necessary equipment and expertise to handle Inconel 625 powder? Consider the investment in equipment and worker training if opting for this material.
By carefully evaluating your needs and weighing the pros and cons, you can make an informed decision about whether Inconel 625 powder is the right fit for your project.
FAQ
Question | Answer |
---|---|
What are some alternative materials to Inconel 625 powder? | Depending on the specific application, alternative materials like Inconel 617, Hastelloy C-276, or even some high-performance stainless steels could be considered. |
Can Inconel 625 powder be recycled? | Yes, Inconel 625 powder can be recycled using specialized techniques, reducing waste and promoting sustainability. |
What safety precautions should be taken when handling Inconel 625 powder? | Proper personal protective equipment (PPE) like gloves, respirators, and eye protection is crucial to minimize exposure to nickel dust. |
How is Inconel 625 powder stored? | The powder should be stored in a dry, inert environment to prevent moisture absorption and contamination. Sealed containers with desiccant packets are recommended. |
By understanding these frequently asked questions, you can gain a more comprehensive understanding of Inconel 625 powder and its use.
Conclusion
Inconel 625 powder isn’t just a metal powder; it’s a gateway to innovation. Its exceptional properties unlock possibilities in industries pushing the boundaries of engineering. Whether it’s building jet engines that can withstand scorching temperatures or creating medical implants that last a lifetime, Inconel 625 powder plays a vital role in shaping the future. So, the next time you see a plane soar through the sky or a complex medical device perform its life-saving function, remember, there’s a good chance Inconel 625 powder played a part in making it possible.