Inconel 625 powder is an exceptional material that has earned its place in industries ranging from aerospace to marine engineering. Why? Because it’s built like a tank, metaphorically speaking. This nickel-based alloy powder is a go-to solution when strength, corrosion resistance, and versatility are non-negotiable. In this guide, we’ll dive deep into what makes Inconel 625 powder tick. Grab a coffee, sit back, and let’s explore everything you need to know.
Overview of Inconel 625 Powder
Inconel 625 powder is a high-performance nickel-based alloy powder known for its excellent strength and resistance to corrosion, oxidation, and extreme temperatures. This material’s unique properties make it ideal for applications in harsh environments, from deep-sea exploration to jet engines. Manufactured using advanced atomization techniques, Inconel 625 powder is optimized for additive manufacturing (3D printing), thermal spraying, and more.
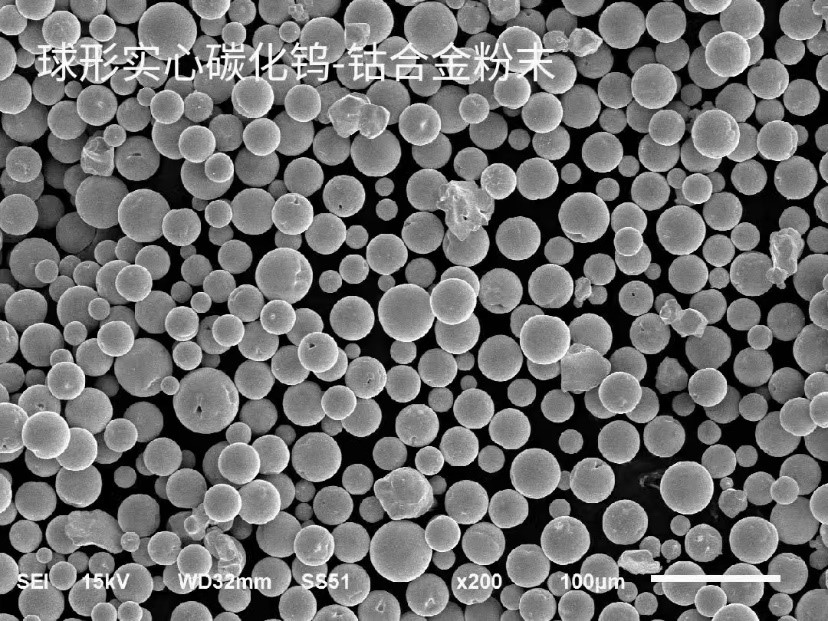
Composition of Inconel 625 Powder
Inconel 625 powder is composed of carefully balanced elements that deliver its remarkable properties. Here’s a detailed breakdown:
Element | Composition (% by Weight) |
---|---|
Nickel (Ni) | 58.0 min |
Chromium (Cr) | 20.0 – 23.0 |
Molybdenum (Mo) | 8.0 – 10.0 |
Niobium (Nb) + Ta | 3.15 – 4.15 |
Iron (Fe) | 5.0 max |
Cobalt (Co) | 1.0 max |
Carbon (C) | 0.10 max |
Silicon (Si) | 0.50 max |
Manganese (Mn) | 0.50 max |
Phosphorus (P) | 0.015 max |
Sulfur (S) | 0.015 max |
This robust composition is engineered to handle the toughest conditions while maintaining stability and performance.
Key Characteristics of Inconel 625 Powder
What sets Inconel 625 powder apart? Let’s delve into its defining traits:
- High Strength: Retains superior mechanical strength at elevated temperatures.
- Corrosion Resistance: Resists pitting, crevice corrosion, and oxidation.
- Thermal Stability: Performs well in extreme temperatures, from cryogenic levels to 980°C (1796°F).
- Versatility: Suitable for additive manufacturing, welding, and thermal spraying.
- Fatigue Resistance: Withstands repeated stress without cracking.
Applications of Inconel 625 Powder
Thanks to its impressive properties, Inconel 625 powder finds use across numerous industries. Here are some common applications:
Application | Details |
---|---|
Aerospace Components | Turbine blades, exhaust systems, engine parts |
Marine Engineering | Subsea piping, heat exchangers, risers |
Chemical Processing Equipment | Reactors, scrubbers, distillation columns |
Power Generation | Heat shields, industrial boilers |
Medical Devices | Prosthetics, surgical instruments |
Automotive | Exhaust manifolds, turbocharger components |
The versatility of Inconel 625 powder ensures its relevance across diverse fields.
Specifications, Sizes, Grades, and Standards
Here’s a quick glance at the common specifications for Inconel 625 powder:
Specification | Details |
---|---|
Powder Size Range | 15-45 μm, 45-150 μm (customizable) |
Grade | Aerospace, Medical, Industrial |
Standards | ASTM B443, AMS 5666, AMS 5599 |
Particle Shape | Spherical (for additive manufacturing) |
These standards ensure compatibility and reliability for demanding applications.
Popular Models of Inconel 625 Powder
Let’s take a closer look at ten specific models of Inconel 625 powder, each with unique features:
- Inconel 625 Fine Powder: Ideal for intricate 3D printing and thin coatings.
- Inconel 625 AM Grade: Specifically optimized for additive manufacturing.
- Inconel 625 Coarse Powder: Suited for high-volume thermal spray applications.
- Inconel 625 Weld Powder: Designed for welding repairs and overlays.
- Inconel 625 Gas Atomized: Ensures excellent sphericity and flowability.
- Inconel 625 Plasma Atomized: Superior purity for critical industries.
- Inconel 625 Spray Grade: Tailored for thermal spraying in marine environments.
- Inconel 625 Binder Jetting Grade: Compatible with binder jet 3D printing.
- Inconel 625 Medical Grade: Meets stringent standards for biomedical applications.
- Inconel 625 High-Density: High-density powder for specialized parts.
Pros and Cons of Inconel 625 Powder
Every material has its strengths and limitations. Here’s how Inconel 625 powder stacks up:
Advantages | Limitations |
---|---|
Exceptional strength-to-weight ratio | High cost |
Superior corrosion and oxidation resistance | Difficult to machine |
Compatible with various manufacturing methods | Requires specialized handling |
Excellent weldability | Limited availability in some regions |
High fatigue resistance | Higher lead times for large-scale projects |
Suppliers and Pricing
The cost of Inconel 625 powder varies based on specifications, quantity, and supplier. Here are some key details:
Supplier | Grade | Price Range ($/kg) | Availability |
---|---|---|---|
AP&C | AM Grade | $100 – $150 | Global |
Sandvik Osprey | Plasma Atomized | $120 – $180 | Europe, North America |
Carpenter Technology | Medical Grade | $150 – $200 | Global |
Praxair Surface Tech | Spray Grade | $110 – $160 | North America, Asia |
Metco Additive | Binder Jetting Grade | $90 – $140 | Global |
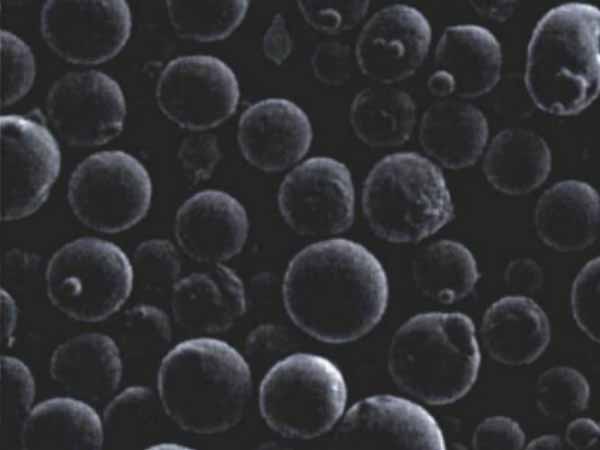
FAQs
Question | Answer |
---|---|
What makes Inconel 625 powder unique? | Its blend of strength, corrosion resistance, and thermal stability. |
Is Inconel 625 powder suitable for 3D printing? | Yes, especially the AM and binder jetting grades. |
What industries use Inconel 625 powder? | Aerospace, marine, chemical processing, automotive, medical, and energy. |
How much does Inconel 625 powder cost? | Prices range from $90 to $200 per kg, depending on grade and supplier. |
Can Inconel 625 powder withstand high temperatures? | Yes, up to 980°C (1796°F) without degradation. |
Conclusion
Inconel 625 powder is nothing short of a marvel in the world of high-performance materials. Whether you’re building jet engines or exploring the ocean depths, its unique properties ensure reliable performance under extreme conditions. While it may come with a hefty price tag, the benefits far outweigh the costs for critical applications. With growing demand and advances in manufacturing technology, Inconel 625 powder is set to remain a top choice for industries that require nothing but the best.