Inconel 625 is a nickel-chromium-molybdenum alloy known for its high strength, outstanding corrosion resistance, and excellent fabricability. This superalloy has become indispensable across industries like aerospace, oil and gas, chemical processing, and power generation where high-temperature oxidation and corrosion resistance are crucial.
The unique properties of Inconel 625 stem from its composition – it contains nickel, chromium, molybdenum, niobium, and iron. Small amounts of titanium, aluminum, cobalt, carbon, manganese, silicon, boron, and nitrogen may also be present. Let’s explore the key features and applications of Inconel 625 powder.
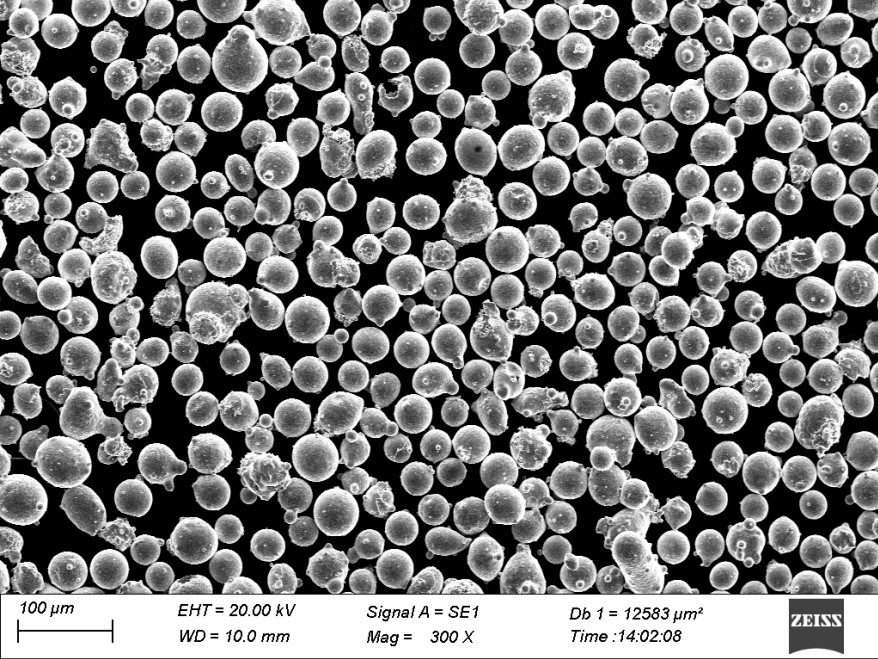
Overview of Inconel 625 Powder
Inconel 625 powder refers to the fine particles of the Inconel 625 alloy produced through gas atomization. This powder possesses the same chemical composition as wrought Inconel 625 but in a granular form optimized for additive manufacturing or metal powder injection molding.
Some of the key properties of Inconel 625 powder include:
- High strength maintained up to 1300°F (700°C)
- Excellent corrosion resistance in a wide range of environments
- Good weldability and formability
- Outstanding fatigue and creep resistance
- Ability to be easily fabricated through 3D printing and other powder-based techniques
Nickel makes up over 60% of Inconel 625’s composition and is primarily responsible for the outstanding corrosion resistance. Chromium at 21-23% enables good oxidation resistance. The addition of molybdenum (8-10%) significantly enhances strength.
Other alloying elements like niobium, iron, and titanium optimize the mechanical properties. The careful selection of this alloy composition gives Inconel 625 powder superior high-temperature performance compared to stainless steels and even other nickel alloys.
Production of Inconel 625 Powder
Inconel 625 powder is manufactured through a gas atomization process. The alloy constituents – nickel, chromium, molybdenum etc. – are first melted to form a homogeneous liquid.
This molten metal is then poured into a special atomization chamber where an inert gas like argon or nitrogen is forced at high pressures through specialized nozzles. This breaks up the liquid stream into very fine droplets which solidify rapidly as they fall through the chamber.
The high cooling rates of 106 K/s freeze the powder particles in a spherical morphology. This prevents internal defects and segregation of alloying elements. The atomized powder is finally collected at the bottom of the chamber and sieved into different size fractions.
Gas atomized Inconel 625 powder has a smooth surface, high density and good flowability. The particle shape and size distribution can be controlled to meet application requirements. For additive manufacturing, powder ranging from 15-45 microns is generally used.
Chemical Composition
The nominal chemical composition of Inconel 625 powder is:
- Nickel: 58% min
- Chromium: 20-23%
- Molybdenum: 8-10%
- Niobium: 3.15-4.15%
- Iron: 5% max
- Titanium: 0.4% max
- Aluminum: 0.4% max
- Carbon: 0.1% max
- Manganese: 0.5% max
- Silicon: 0.5% max
- Sulfur: 0.015% max
- Boron: 0.006% max
- Phosphorus: 0.015% max
The balance is made up of cobalt and other trace elements. The high purity and tight compositional control ensure consistent, reliable performance across Inconel 625 powder lots.
Physical Properties
- Density – 8.44 g/cm3
- Melting Point – 2335-2460°F (1276-1350°C)
Inconel 625 powder particles have excellent sphericity and flow characteristics. The powder morphology and size distribution play a key role in achieving good packing density and melt flow during additive manufacturing.
Mechanical Properties
Inconel 625 exhibits the following mechanical properties in the annealed condition:
- Tensile Strength – 120-160 ksi (830-1100 MPa)
- Yield Strength – 70-95 ksi (485-655 MPa)
- Elongation – 35-55%
- Hardness – Brinell 195 max
The excellent strength of Inconel 625 is maintained up to 1300°F. It also demonstrates good ductility for such a high-strength alloy. The combination of strength, ductility and corrosion resistance makes this a versatile material across demanding applications.
Key Benefits of Inconel 625 Powder
Here are some of the major advantages offered by Inconel 625 powder:
- Outstanding High Temperature Strength – Inconel 625 retains strength and stability up to 1300°F without age hardening treatments. This allows it to outperform stainless steels.
- Excellent Oxidation and Corrosion Resistance – It exhibits exceptional resistance to a wide range of corrosive environments and high temperature oxidation. This allows its use in extremely harsh chemical processing conditions.
- Easy Fabrication – Inconel 625 has good cold workability. Parts made from the powder demonstrate excellent weldability using conventional welding methods. This minimizes post-processing requirements.
- High Fatigue Strength – It has far superior fatigue strength compared to austenitic stainless steels like 316L. This expands its applications for dynamic, cyclically-loaded components.
- Good Creep Rupture Strength – Inconel 625 powder maintains high creep strength at elevated temperatures allowing the design of components with longer service lives.
- Custom Alloys Possible – The powder metallurgy process enables the creation of custom Inconel 625 alloys by modifying the composition to meet specific property requirements.
Applications of Inconel 625 Powder
Aerospace
- Combustion liners
- Exhaust ducts and stacks
- Thrust reverser components
- Turbine engine parts
- Rocket motor casings
- Aircraft ducting and fittings
Chemical Processing
- Heat exchangers
- Reaction vessels
- Valves and fasteners
- Pumps and piping
- Process towers and columns
Oil and Gas
- Downhole tools
- Wellhead components
- Gathering and transmission pipelines
- Offshore drilling equipment
Power Generation
- Gas turbine hot section parts
- Heat recovery steam generator tubing
- Boiler components
- Coal gasification equipment
Marine
- Seawater piping
- Propeller shafts
- Marine engines and turbines
- Desalination plants
Additive Manufacturing
- Aerospace components with complex geometries
- Lightweight lattice structures
- Conformal cooling channels for injection molds
- Customized tooling inserts and fixtures
- Biomedical implants like hip joints
Inconel 625’s combination of strength, ductility, corrosion resistance and weldability make it a versatile material for demanding applications across industries. The superalloy powder is enabling lighter, more efficient component designs previously not possible with conventional materials and manufacturing techniques.
Inconel 625 Powder Price
Here are some typical price ranges for Inconel 625 powder:
- Powder for additive manufacturing (15-45 microns): $50-$120 per kg
- Powder for metal injection molding (>20 microns): $40-$100 per kg
- Larger particles sizes (105-150 microns): $30-$80 per kg
The powder price varies based on:
- Purity levels
- Particle size range and distribution
- Morphology (spherical vs irregular shape)
- Purchase quantity and lot size
- Level of quality control and certification
In general, smaller particle size powders required for AM are more expensive than larger powders for conventional powder metallurgy techniques.
Powder purchased in bulk quantities (100+ kg) is typically cheaper on a per kg basis compared to smaller 5-10 kg trial lots.
Highly spherical gas atomized powder with tight particle size distribution, made by reputable suppliers like Carpenter Additive, Sandvik Osprey, Praxair, Höganäs, etc. tends to command premium pricing.
Location also impacts price – powder shipped within the same continent is less expensive than intercontinental air shipments.
End-use also affects price. Powders marketed specifically for aerospace and medical uses, with stringent quality documentation, tend to be costlier.
In summary, Inconel 625 powder prices fall in the range of $30 to $120 per kg depending on particle size, quality, quantity and geographical factors. Work closely with suppliers to obtain competitive pricing for your specific application.
How Inconel 625 Powder is Used in Additive Manufacturing
Also known as 3D printing, additive manufacturing (AM) enables the creation of complex metal parts from powder material in a layer-by-layer fashion. The excellent properties of Inconel 625 powder make it a popular choice for AM across aerospace, automotive, medical and other industries.
Here are some ways in which Inconel 625 powder is leveraged through additive manufacturing:
Laser Powder Bed Fusion
A high-power laser selectively melts and fuses Inconel 625 powder spread in a thin layer on a build plate. This process is repeated layer-by-layer until the complete 3D object is fabricated. Laser powder bed technology is used to 3D print intricate components like turbine blades.
Directed Energy Deposition
A focused heat source like a laser or electron beam melts the Inconel 625 powder which is then deposited on the substrate. DED techniques allow quick repairs, coatings or even large near-net shape metal parts to be built from the superalloy powder.
Binder Jetting
A liquid bonding agent is selectively deposited to join Inconel 625 powder particles together to produce the 3D green object layer-by-layer. The part is then sintered to achieve full density. It enables the cost-effective printing of complex geometries.
Metal Injection Molding
Inconel 625 powder combined with binders is injection molded and then sintered to produce intricate net-shape components. MIM provides a viable route to manufacturing affordable small-sized parts in medium to high volumes.
The flexibility of AM coupled with Inconel 625’s properties is enabling lighter, higher-performance components like aircraft engine parts, customized implants and conformally-cooled injection molds.
Key Benefits of Using Inconel 625 in Additive Manufacturing
Additive manufacturing with Inconel 625 powder offers several advantages:
- Components with complex geometries like lattices and internal channels can be fabricated – not possible with conventional subtractive techniques.
- Significantly lower buy-to-fly ratios since less raw material is wasted.
- Parts can be designed with conformal cooling to reduce injection molding cycle times.
- Ability to fabricate functionally graded parts by varying the powder composition.
- Reduction in lead times and inventories due to lower tooling requirements.
- Customized components like dental implants can be produced without expensive dies or molds.
- Post-processing like machining or joining of sub-assemblies is minimized or eliminated.
- Higher material utilization with reduced scrap losses compared to forging or machining.
These benefits make Inconel 625 a popular material for additive manufacturing across aerospace, defense, automotive, medical, and general engineering sectors.
Key Considerations for Additive Manufacturing with Inconel 625 Powder
To leverage the full potential of Inconel 625 powder in AM, some critical factors need attention:
- Powder quality – Powder made using gas atomization offers the particle size distribution, morphology, and purity essential for defect-free printing.
- Part orientation – Component geometry and placement on the build platform impacts residual stresses and mechanical properties.
- Support structures – Careful design of supports is needed to minimize surface roughness on final parts.
- Process parameters – Parameters like layer thickness, laser power and scan strategy significantly influence final properties.
- Post-processing – Stress relieving, hot isostatic pressing and machining may be needed to achieve the desired dimensional accuracy and material properties.
With careful control over these factors, users can leverage Inconel 625’s outstanding properties through AM to design high-performance components.
Why Choose Inconel 625 Powder?
Here are some of the top reasons why Inconel 625 powder is chosen over other materials for critical applications:
- Excellent high temperature strength to handle extremely demanding environments
- Outstanding corrosion resistance in a wide range of aggressive media
- High fatigue and creep resistance for long service life under cyclic loads
- Easy weldability and formability minimizing post-processing requirements
- Enables lighter component designs not possible with other materials
- Components maintain dimensional stability at high operating temperatures
- Spark erosion and laser processing friendly for machining complexity
- High toughness reduces risk of catastrophic failure modes
- Can be used to repair and coat existing components extending service life
- Custom alloys can be created by tweaking the chemical composition
The unique combination of temperature resistance, workability, weldability and corrosion resistance make Inconel 625 a material of choice for safety-critical applications across aerospace, oil and gas, chemical processing, power generation and other extreme environments.
Limitations of Inconel 625 Powder
Despite its strengths, using Inconel 625 powder has some limitations:
- High material costs – Nickel-based superalloys are more expensive than stainless steels. Both the powder and finished components have a higher cost.
- Lower ductility than austenitic stainless steels – Its tensile elongation is nearly half that of 304 or 316 stainless steel. This restricts forming and requires more generous fillet radii.
- Heavy weight – With a density of 8.44 g/cm3, Inconel 625 parts are significantly heavier than aluminum or titanium alloys.
- Difficult to fully recycle – Scrap reuse is limited since variations in composition can significantly degrade properties. Components require remelting and remixing with virgin powder.
- Limited supplier base – As a niche material, fewer manufacturers have powder production capabilities compared to more common alloys. This can constrain supply chains.
- Challenging printability – Careful parameter selection and high-end printers are needed to successfully process Inconel 625 powder into defect-free components.
By factoring in these limitations, users can make an informed material selection while leveraging the many benefits of Inconel 625 powder.
FAQs
What is Inconel 625 powder?
Inconel 625 powder is a nickel-chromium-molybdenum alloy powder made through gas atomization process. It possesses excellent strength, corrosion resistance and fabricability. The powder is used to fabricate components through additive manufacturing and other powder metallurgy techniques.
What industries use Inconel 625 powder?
Key industries using Inconel 625 powder include aerospace, oil & gas, chemical processing, power generation, marine and medicine. It serves applications requiring good mechanical strength and stability in high temperature, oxidizing or corrosive environments.
What particle size is used for AM with Inconel 625?
For powder bed fusion AM, the typical Inconel 625 powder size range is 15-45 microns. More broadly, powder from 10 to 105 microns may be utilized based on the specific AM process.
What are some examples of Inconel 625 AM applications?
Typical AM applications include aircraft engine components, rocket propulsion nozzles, downhole tools for oil/gas, conformal-cooled injection molds, medical implants, heat exchangers, and tooling inserts.
What post processing is required after AM with Inconel 625?
Post-processing may involve support removal, stress relieving, hot isostatic pressing, surface finishing operations like grinding or polishing and machining to final tolerances. This depends on the AM process used and final component requirements.
Does Inconel 625 require heat treatment after AM?
Solution treatment and aging are not required after AM with Inconel 625 due to its solid solution strengthening characteristics. Stress relieving at 1875°F (1025°C) may be performed to eliminate residual stresses.
Can you weld Inconel 625 AM parts?
Yes, Inconel 625 demonstrates excellent weldability. AM-processed components can be welded using suitable nickel alloy filler material and by following recommended practices to minimize residual stresses and distortion.
Is Inconel 625 stronger than stainless steel?
Yes, Inconel 625 has over twice the tensile strength compared to 300 series stainless steels. It also offers significantly better high temperature strength and corrosion resistance.
Is Inconel 625 FDA approved?
Yes, Inconel 625 has FDA clearance for use in medical and food contact applications. Quality standards like ASTM standards must be satisfied. UHP argon and vacuum technology ensures high purity powder.
Does Inconel 625 contain nickel?
Yes, nickel is the main constituent of Inconel 625 at over 58% of the alloy composition. Nickel provides excellent corrosion resistance. The alloy also contains chromium, molybdenum and niobium.
What is the largest limiting factor for Inconel 625?
The high raw material cost of Inconel 625 powder and related manufacturing costs are the primary limiting factors, especially for larger components. The high material density is another constraint for weight-sensitive applications.
In summary, Inconel 625 powder is a versatile nickel alloy used across demanding industries for its excellent strength and corrosion resistance at high temperatures. Additive manufacturing is enabling lightweight, complex designs not possible with conventional processing. With proper parameter control and post-processing, components with superior properties can be fabricated using Inconel 625 powder.