Inconel 718 is a high strength, corrosion resistant nickel chromium alloy used in powder metallurgy for aerospace and industrial components. Its properties of heat resistance, fatigue strength andoxidation resistance enable demanding applications under extreme environments.
This guide covers Inconel 718 powder compositions, manufacturing methods, required specifications, pricing, applications and supplier comparisons.
Types and Classification of Inconel 718 Powder
Inconel 718 alloy powder categorized by:
Product Forms
- Pre-alloyed: Prealloyed nickel iron chromium powder
- Blended elemental: Mix of nickel, chromium, iron powders
Particle Sizes
Size | Description | Typical Uses |
---|---|---|
Fine | 10 – 45 microns | Thin wall structures, small intricacies |
Medium | 45 – 150 microns | Most general use powder size |
Coarse | Up to 300 microns | High deposition rate, large components |
Matching particle size ranges to part needs optimizes quality and economics.
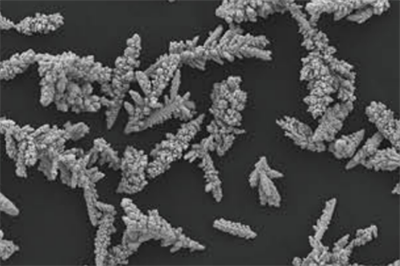
Nominal Composition
Element | Weight % | Role |
---|---|---|
Nickel (Ni) | 50 – 55% | Corrosion resistance, ductility |
Chromium (Cr) | 17 – 21% | Oxidation resistance |
Iron (Fe) | Balance | Cost, tensile properties |
Niobium (Nb) | 4.75 – 5.5% | Precipitate strengthening |
Molybdenum (Mo) | 2.8 – 3.3% | Creep rupture strength |
Titanium (Ti) | 0.65 – 1.15% | Grain boundary strengthening |
Aluminum (Al) | 0.2 – 0.8% | Limits low melting phases |
Cobalt (Co) | 1% max | |
Copper (Cu) | 0.3% max | Limits embrittlement |
Carbon (C) | 0.08% max | Restricts carbide formation |
Manganese (Mn) | 0.35% max | |
Silicon (Si) | 0.35% max | Deoxidizer |
Phosphorus (P) | 0.015% max | Impurity limit |
Sulfur (S) | 0.015% max | Impurity limit |
Limits on elemental composition ranges sustain desired mechanical properties. Each alloy addition serves specific metallurgical roles for strength, ductility and corrosion resistance.
Manufacturing Methods
- Gas Atomization: High pressure water or gas breaks up molten alloy stream into fine droplets creating spherical powders with good flow and packing properties. Nitrogen or argon gas prevents oxidation. Different nozzles generate desired size fractions.
- Plasma Rotating Electrode Process (PREP): Centrifugal forces from rotating molten alloy subjected to plasma jets break it into droplets which solidify into spherical powders. Achieves small sizes with narrow distribution.
- Vacuum Induction Melting (VIM): Alloys with high reactivity like IN718 are melted using VIM before atomization to achieve cleanliness and homogeneity.
Controlling process parameters like temperature, atmosphere and cooling rates result in quality powder feedstock for additive manufacturing, thermal spray or metal injection molding.
Specifications
Inconel 718 powder produced for commercial applications should conform to:
SAE AMS 5662: Composition limits, impurity levels, particle sizes and size distribution, hall flow rates, microstructure
AMS 2241: Heat treatment processing and hardness limits
ASTM B783: Annealing, grain size determination
review statistical batch certification data against these specifications from suppliers before purchase.
Mechanical Properties
Nominal values after heat treatment:
Property | As-Hipped | Hot-Isostatic-Pressed | Forged |
---|---|---|---|
Density (g/cc) | 8.19 | 8.19 | 8.19 |
Tensile Strength (MPa) | 1275 | 1310 | 1460 |
Yield Strength (MPa) | 1035 | 1105 | 1275 |
Elongation (%) | 22% | 19% | 15% |
Hardness (HRC) | 32-36 | 36-39 | 36-41 |
Achieving target properties depends significantly on powder quality and optimized thermal processes like hot isostatic pressing and heat treatment.
-
SCM 415 Low Alloy Steel Powder
-
AISI 4340 Low Alloy Steel Powder
-
Invar 36 alloy powder
-
52100 Alloy Steel Powder
-
2.25Cr1Mo alloy steel
-
Stainless Steel OP431 Powder
-
Best Stainless Steel 316L Powder for 3D Printing
-
stainless steel 304 Powder for 3D Printing
-
Best 17-4PH powder stainless steel powder for 3D Printing
Applications
- Aerospace: Engine components – seals, cases, blades, fasteners, gears
- Industrial Gas Turbines: Rotors, combustors, shafts
- Oil & Gas: Downhole tools, valves, pumps for corrosive environments
- Automotive: Turbocharger rotors and impellers
- Nuclear: Steam generator tubing containing superheated water, fission reactors
- Defense: Critical battlefield weapon systems exposed to heat, shock
Leverage excellent combination of heat, corrosion resistance and strength for critical equipment applications, especially under thermal cycling stresses over long lifetimes.
Industrial Specifications
Standard | Description |
---|---|
AMS 5662 | Nickel Alloy, Corrosion and Heat-Resistant, Bars, Forgings, and Rings 52.5Ni – 19Cr – 3.0Mo – 5.1 Nb – 0.90Ti – 0.50Al – 18Fe |
AMS 5663 | Nickel Alloy, Corrosion and Heat-Resistant, Extrusions 52.5Ni – 19Cr – 3.0Mo – 5.1Nb – 0.90Ti – 0.50Al – 18Fe |
AS7263 | Thermal Treatment 54Ni – 19Cr – 3.0Mo – 5.0 Nb – 0.90 Ti – 0.50 Al – Remainder Fe |
ASTM B637 | Standard Specification for Precipitation-Hardening Nickel Alloy Bars, Forgings, and Forging Stock for High-Temperature Service |
ISO 4967 | Nickel Alloys – Hot Forged or Hot Rolled Nickel Alloy Parts – Technical Specification |
Review certification documents confirming conformity to grade requirements before purchase from new vendors.
Quality Considerations
Metric | Acceptable Level | Test Method |
---|---|---|
Composite Purity | >99.9% | ASTM E2371 |
Oxygen(O) | <500 ppm | Inert gas fusion |
Moisture(H2O) | <300 ppm | Karl Fischer Titration |
Nitrogen(N) | <50 ppm | Inert gas fusion |
Particle Shape | Spherical >80% | Microscopy |
Particle Size Distribution | Per AMS 5662 | Laser diffraction |
Apparent Density | Typically 4.0-4.5 g/cc | Hall flowmeter |
Powder Microstructure | Solution annealed, no carbides/Laves phase | Image analysis |
Powder feedstock quality determines integrity of final sintered part properties.
Price Range
Grade | Particle Size | Price per kg |
---|---|---|
Inconel 718 | 10 – 45 μm | $75 – $125 |
Inconel 718 | 150 – 300 μm | $45 – $95 |
Research grade | 1 – 10 μm | $250+ |
Pricing varies based on order volumes, powder specification and geographic region. Get latest quote from shortlisted suppliers against target application needs.
Buying Criteria
Parameter | Importance |
---|---|
Quality Certifications | High |
Sampling Support | High |
Consistency | High |
Technical Expertise | Medium |
Customer References | Medium |
Price | Low |
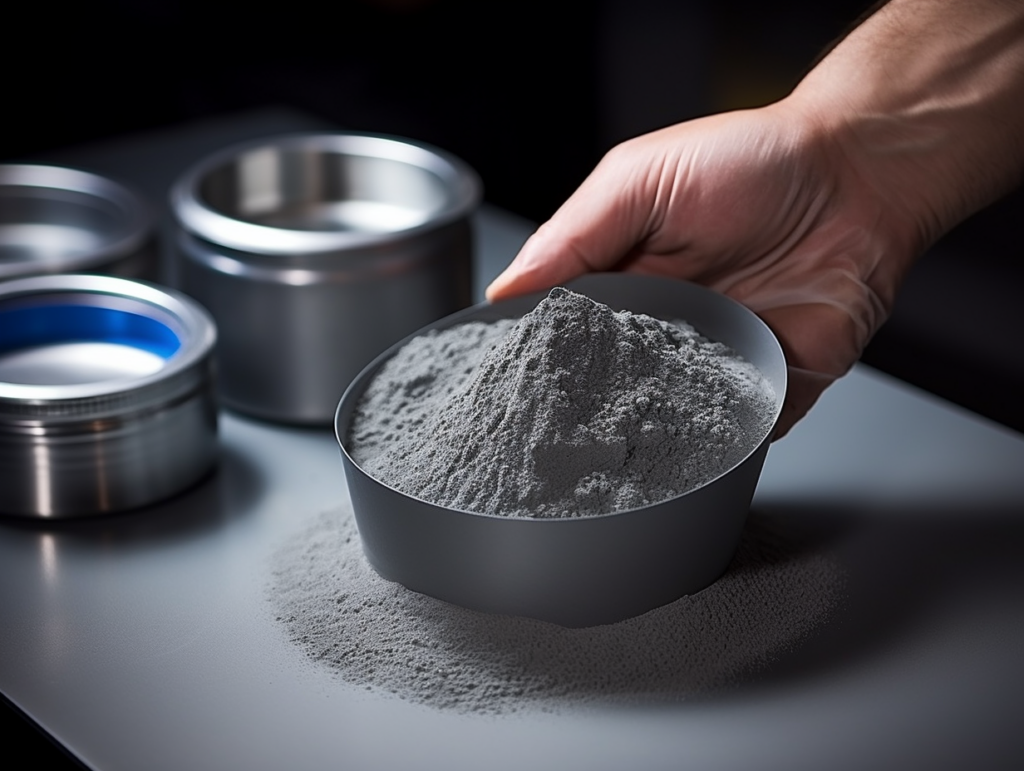
FAQs
Q: What is the difference between Inconel 625 vs 718 alloy powder?
A: IN625 offers better weldability and corrosion resistance but lower temperature strength than IN718 which has higher tensile properties from heat treatment strengthening response.
Q: Does Inconel 718 powder require special storage?
A: Keep sealed below 10°C with dessicants to prevent moisture ingress. Limit oxygen exposure through unopened containers. Discard if oxidation like color change observed.
Q: What powder size is best for laser powder bed fusion?
A: 15-45 micron Inconel 718 powders spread smoothly and pack densely enabling good laser melting with minimal porosity and overflow issues for optimal part properties.
Q: What are common nickel alloy blends using Inconel 718 powder?
A: IN718 is sometimes blended with Inconel 625, stainless steels like 316L or cobalt alloys to tailor corrosion or wear properties at lower costs than pure IN718 powder.