Niobium, also known as columbium, is a rare, soft, gray transition metal that is corrosion resistant. It has an atomic number of 41 and is represented by the symbol Nb.
niobium alloys powder refers to metallic powders containing niobium and other alloying elements processed via gas atomization into fine spherical powders suitable for specialized metal alloy applications. The unique properties of niobium alloys powder make them ideal for use in a variety of industries and applications.
Overview of Niobium Alloys Powder
Niobium alloys powders contain small amounts of alloying elements like titanium, tungsten, molybdenum and zirconium added to impart desirable characteristics and properties. They have higher strength at elevated temperatures, better corrosion resistance and creep rupture strength than unalloyed niobium.
Common product forms include spherical atomized powder, hydride dehydride powder and agglomerated/sintered powder. Particle size ranges from 10 to 150 microns based on the production method.
The following table summarizes the key details about niobium alloy powders:
Parameter | Details |
---|---|
Products | Spherical powder, crushed powder, blended elemental powder |
Alloying Elements | Titanium, tungsten, molybdenum, zirconium |
Particle Size | 10 – 150 microns |
Purity | 98 to 99.8% |
Key Properties | High heat resistance, corrosion resistance, good workability |
Melting Point | 1300 to 1380°C |
Main Application Areas | Aerospace, oil and gas, automotive, electrical |
niobium alloys powder materials feature a set of exceptional properties that prove very useful in niche applications spanning multiple industries:
- High heat resistance with melting point above 2400°F
- Excellent corrosion resistance properties
- Low thermal neutron capture cross-section
- Ability to absorb neutrons without formation of long life isotopes
- High vibration damping capacity
- Superconducting properties with high critical temperature
- Good workability using conventional fabricating techniques
- Combination of light weight, high strength and stiffness
These unique characteristics make niobium alloys suitable for specialized uses in high temperature structural applications. Parts and components made from consolidated niobium alloy powder offer superior elevated temperature capabilities well beyond the limits of traditional alloys.
The next section covers the equipment needed for producing niobium alloys powder.
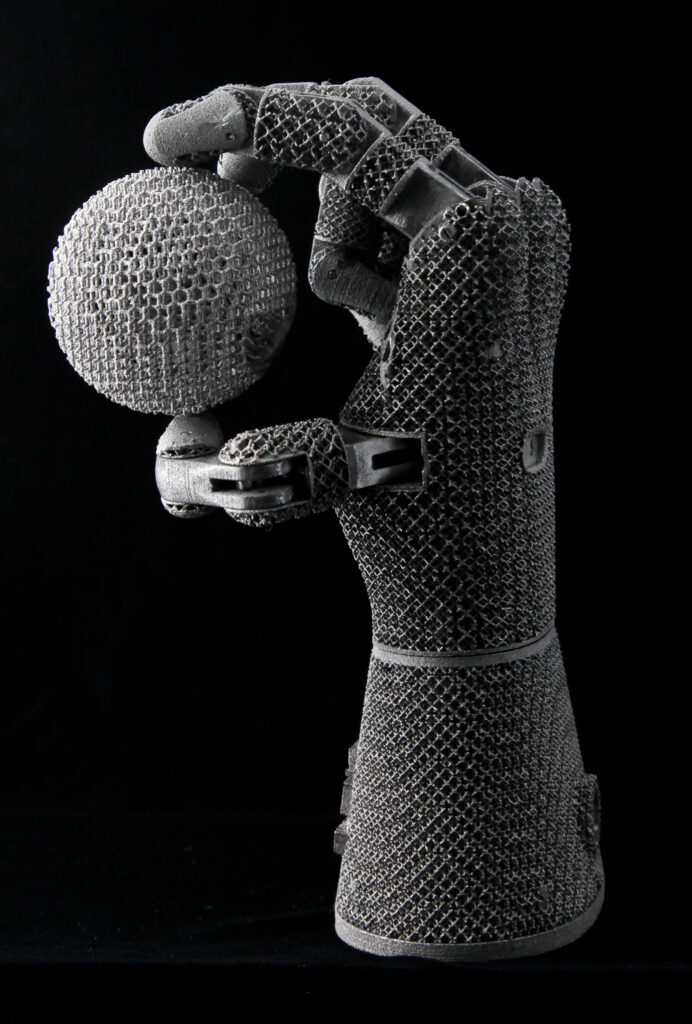
Equipment for Niobium Alloy Powder Production
Specialized equipment and powder metallurgy processing is necessary to manufacture advanced niobium alloy powders with fine particle sizes and narrow distribution.
The table below outlines the major types of equipment used:
Equipment | Details |
---|---|
Induction Melting Furnace | Melts niobium or ferro-niobium ingot |
**Casting Equipment ** | Casts molten metal into rods/billets |
Atomizing Equipment | Turns metal into fine droplets using gas/water |
Screening Equipment | Classifies powder into size fractions |
Metal Powder Processing | Handles and contains fine reactive powders |
Induction melting furnace with inert gas protection melts pure niobium or ferro-niobium ingots. Common melting methods include vacuum induction melting and vacuum arc melting to achieve ultrahigh purity levels.
The molten metal is then cast into rods, billets or other shapes suitable for feeding into the atomizing equipment.
Atomizing equipment uses forced gas or water to turn the liquid metal stream into fine droplets upon cooling. Gas atomization using argon or nitrogen is common. Water atomization is also used. This produces fine spherical niobium powder from 15 – 150 microns diameter.
The gas-atomized particles undergo screening and classification using sieves and air classifiers to separate them into specific powder size distributions required by clients.
Metal powder handling/processing equipment load, unload and move these fine reactive powders while avoiding contamination or exposure during subsequent consolidation and forming.
Installing Niobium Alloy Powder Production Line
Constructing a complete production line for niobium alloy powder requires extensive planning, large capital investment and technical expertise. Companies specializing in building turnkey systems are listed later.
The key steps for installing the equipment are:
- Site layout and floor planning
- Equipment procurement and delivery
- Foundation and civil construction works
- Assembly and erection of equipment
- Installation of hydraulics, electricals and utilities
- Instrumentation and control system integration
- Commissioning and trial production runs
Sufficient lead time of around 12-18 months should be allotted – depending on scope and scale of production envisaged.
Most equipment OEMs also offer support services for installation and commissioning when required. Engaging qualified powder metallurgy consultants is highly recommended during project planning and execution.
Operating Niobium Alloy Powder Production Line
Operating a niobium alloy powder plant requires technically skilled manpower for specialized production processes.
The major activities involved in powder production are:
- Operation of melting furnaces
- Casting niobium into feedstock
- Operating gas atomizers
- Metal powder handling and containment
- Running sieves and classifiers *Powder sampling and quality control
- Packing final products for shipping
All operators need extensive training for conducting procedures safely while achieving purity, particle size and Shape specifications.
Since fine niobium powder is highly reactive and prone to explosion, strict protocols must govern material handling, equipment operation and maintenance. Explosion protection and mitigation measures are mandatory.
Maintaining Niobium Powder Production Line
To maximize production uptime while meeting specifications, a comprehensive maintenance strategy must be implemented after commissioning and during operation spanning:
- Preventive maintenance schedules
- Breakdown maintenance procedures
- Equipment overhauling policies
- Standard operating procedures
- Spares inventory management
- Safety and loss prevention
- Training programs
Highly qualified technicians and engineers will oversee the maintenance effort. Original equipment manufacturers also provide maintenance services and support.
Types of Niobium Alloy Powder
Based on production method and morphology, niobium alloy powders can be categorized into:
- Gas Atomized Powder
- HDH (Hydride-Dehydride) Powder
- Blended Elemental Powder
Comparison between the different powder types:
Parameter | Gas Atomized | HDH | Blended Elemental |
---|---|---|---|
Particle Shape | Spherical | Irregular, porous | Variable |
Particle Size | 15 – 150 μm | 50 – 500 μm | 150 – 1000 μm |
Production Method | Inert gas atomization | Hydriding/Dehydriding | Mechanical blending |
Tap Density | High | Low | Medium |
Powder Flow | Excellent | Poor | Fair |
Consolidation | Hot/Cold compaction + sintering | Compaction + Reaction sintering | |
Purity Control | Very good | Moderate | Difficult |
Cost | High | Low | Medium |
Gas atomized powder has highest quality with spherical morphology, but costs more than others.
HDH niobium powder has irregular shape and wide particle size distribution, but lower cost.
Blended elemental mixes niobium with alloying powders – suitable for some applications.
For critical applications like aerospace components, gas atomized powder is preferred. HDH powder suffices for industrial applications requiring high temperature strength like automotive turbocharger rotors.
Next section covers the niobium alloy powder compositions.
Niobium Alloy Powder Compositions
By adding various alloying elements to niobium, unique material properties can be developed to meet application needs. Common niobium alloys include:
1. Niobium-Titanium: Nb-Ti is highly ductile and fabricable. With 10% titanium, it has excellent corrosion resistance to alkalis.
2. Niobium-Molybdenum-Titanium: Nb-Mo-Ti combines corrosion resistance with high temperature strength through solid solution hardening.
3. Niobium-Molybdenum-Hafnium-Titanium-Zirconium: Complex niobium alloys with low density and excellent high temperature properties. Used in aerospace applications.
4. Niobium-Tantalum-Tungsten: Nb-Ta-W refractory alloys retain strength at temperatures exceeding 2600°F. Serves as thrust nozzles in rocket engines.
5. Niobium-Tin: NbSn is uniquely superconducting below critical temperature. Used to make MRI scanners, research magnets and particle accelerators.
6. Niobium-Germanium: NbGe films offer special superconductivity properties for electronic devices and research.
The table below shows typical composition ranges:
Alloy | Chemical Composition |
---|---|
Niobium-Titanium | Niobium bal.; Titanium 10 – 50 wt% |
Niobium-Molybdenum-Titanium | Niobium bal.; Molybdenum 5 – 20 wt.%; Titanium 5 – 10 wt% |
Niobium-Molybdenum-Hafnium-Titanium-Zirconium | Niobium bal.; Mo 8-10%; Hf 1-5%; Ti 2-5%; Zr 0.5% |
Niobium-Tantalum-Tungsten | Niobium bal.; Tantalum 10%; Tungsten 5 – 10% |
Niobium-Tin | Niobium bal.; Tin 4 – 25 wt% |
Niobium-Germanium | Niobium bal.; Germanium 5 -50 atomic % |
By optimizing alloy chemistry, niobium alloys deliver outstanding performance for extreme demands of next-generation aerospace engines, spacecraft structures and radiation environments.
Applications of Niobium Alloy Powder
Aerospace: Aircraft engines, rockets, jets
- Turbine blades, thrust nozzles and combustion chambers
- Airframes, wings and fuselage structures
Oil and gas: Drilling equipment, pipelines
- High strength seamless tubes, corrosion resistant linings
Automotive: Turbocharger rotors, fuel cells
- Heat resistant superalloy turbine wheels
Nuclear: Fission/fusion reactors, particle accelerators
- Radiation resistant structural materials
- Superconducting magnets
Electronics: Superconductors, semiconductors
- Josephson junctions, SQUIDs, sensors
- NbGe films
Why Niobium Alloys?
Niobium alloys offer an exceptional combination of properties creating high performance, lightweight structural materials for extreme environments, especially:
High heat and thermal shock resistance
- Can withstand over 2500°F without losing strength
- Operate hundreds of degrees hotter than typical superalloys
Excellent corrosion resistance
- Withstand corrosive effects in hot acidic environments
High specific strength
- Very strong relative to their low density
- Niobium has density of 8.57 gm/cc only
Thermal stability
- Retain high strength levels upon prolonged exposures
Easy fabricability
- Good formability allows conventional metalworking
Enhanced functionality
- Unique superconductivity and electromagnetics behavior
These desirable characteristics help engineers advance the frontiers of materials technology – to boost efficiency, power and reliability of critical systems operating in the most challenging conditions.
Global Suppliers of Niobium Alloy Powder
Highly specialized metal powder producers have niobium alloy capacity. They offer custom gas atomized powders of various niobium alloys.
Company | HQ Location |
---|---|
CABOT Corporation | USA |
H.C. Starck Solutions | Germany |
ATI Powder Metals | USA |
Praxair Surface Technologies | USA |
CNPC Powder Group | China |
These powder metallurgy specialists have end-to-end capability including R&D, melting, gas atomization, sieving, controlling particle size distribution, morphology and purity levels of metallic niobium alloys.
Both domestic use and export to international customers is catered to.
Pricing
Price range for niobium alloy powders is between USD 50 – 500 per kg depending on:
- Alloy composition
- Powder particle size distribution
- Purity levels
- Purchase volumes
- Supplier capability and capacity utilization
Rare, specialty alloys cost much more than common grades. Research quantities of rare Nb alloys can cost thousands of dollars per kg.
Installing Niobium Alloy Powder Plant
Constructing a complete powder production line for niobium alloys is best left to engineering firms specializing in turnkey powder metallurgy solutions. They provide seamless execution from design to commissioning of the facility.
Advantages of engaging a specialist contractor:
- Single point responsibility for the project
- Strong experience in similar projects
- Quote fixed price for entire turnkey plant
- Offer performance guarantees
- Execute all aspects – design, civil, equipment, installation & commissioning
- Specialist knowledge to customize layout and machinery for specific powder grades and parameters
Steps for Installing Plant
1. Planning & Layout: Create equipment layout, utility flow diagrams, facility design considering safety guidelines for pyrophoric metals
2. Engineering & Design: Carry out required engineering for structural, piping, electrical, instrumentation, automation, safety systems
3. EquipmentProcurement & Shipping: Procure equipment from vendors meeting technical specifications. Includes melting furnace, atomizer unit, powder handling systems etc. plus auxiliary equipment.
4. Civil Construction & Erection: Construct foundations, structures and mezzanines required for plant considering floor space, heights and load-bearing
5. Installation & Commissioning: Assemble and install equipment, piping, electrics & instrumentation, control systems. Test for safety compliance and production capability.
Timeline
Under normal circumstances, setting up a 500 ton per year capacity niobium alloy powder production plant takes 12 to 18 months from approval of drawings to commissioning activities when executed by a competent contractor.
Choosing Niobium Alloy Powder Plant Supplier
Carefully evaluate and select an equipment partner using criteria like:
Track Record: Number of years designing and building niobium alloy powder plants. Strong client references.
Technical Strength: In-house expertise for engineering, design, manufacturing, construction and commissioning.
Quality Standards: ISO certified for design, manufacturing, quality assurance etc.
Safety: Implement international guidelines for constructing explosive atmosphere facilities.
Reliability: Ability to deliver reliable and robust equipment with after-sales support
Cost: Overall pricing and payment terms
Support: Agreements for technical support, spares, maintenance available
The table below shows leading international suppliers of niobium alloy powder plants with capabilities:
Company | HQ | Technical Capability |
---|---|---|
Ecosystem USA | Ohio, USA | Furnaces, gas/water atomizers for Nb, Mo, Ti alloys |
PyroGenesis Canada | Montreal, Canada | Plasma atomization, gas atomizers |
MLP India | Chennai, India | Vacuum induction furnaces, special alloy expertise |
Evaluate shortlisted vendors on capability, experience, pricing and local support to choose right partner. Visit reference sites before commitment.

Pros and Cons of Niobium Alloys Powder
Advantages of Niobium Alloy Powder
- Imparts extremely high heat and corrosion resistance in components
- Provides high specific strength for weight critical applications
- Withstands extreme temperatures exceeding 2500°F
- Improves tensile, fatigue and creep rupture strength
- Offers tailored functionality like superconductivity
Limitations of Niobium Alloy Powder
- Very expensive compared to common alloy powders
- Requires specialized production and processing equipment
- Prone to contamination – needs controlled atmosphere handling
- Limited number of global suppliers and high switching costs
- Exotic grades need long lead times for custom development
- Handling fine powders hazardous without adequate safety measures
For niche applications, the unique benefits of niobium alloys outweigh higher costs and processing challenges involved. Demand grows steadily as next-generation technologies rely more on their capabilities.
FAQ
Q: What are the critical characteristics needed for niobium alloy powder?
A: Key parameters are particle size distribution, spherical morphology, chemical composition including alloying additions, high tap density, purity levels and cost effectiveness.
Q: What affects the final powder price per kg?
A: Rarity of specific niobium alloy composition, purchase quantity, powder morphology and technical specifications will determine pricing which can vary widely.
Q: What particle size is best suited for Additive Manufacturing?
A: For AM techniques like DED and PBF-LB, niobium alloy powder between 45 to 105 microns is recommended. Finer fractions improve density and surface finish.
Q: What is the recommended investment cost for setting up a niobium alloy powder plant?
A: For a production capacity of 500 metric ton annually, the capital investment would be around USD 8 to 12 million including equipment, factory infrastructure and auxiliary facilities.