진공 유도 용융 개요
진공 유도 용융 (VIM)은 고순도 금속 합금과 분말을 생산하는 데 필수적인 역할을 하는 현대 야금학의 핵심 공정입니다. 항공우주부터 바이오메디컬에 이르기까지 다양한 산업에서 사용되는 금속이 엄격한 순도 및 성능 기준을 충족하도록 하는 보이지 않는 영웅과도 같습니다.
그렇다면 VIM이란 정확히 무엇일까요? 진공 유도 용해의 핵심은 전자기 유도를 사용하여 진공 상태에서 금속을 용해하는 공정입니다. 이 공정은 금속의 특성을 변화시킬 수 있는 산소 및 질소와 같은 가스로 인한 오염을 최소화합니다. VIM은 순도가 가장 중요한 초합금, 스테인리스강 및 기타 특수 소재를 생산하는 데 특히 유용합니다.
이 가이드의 목표는 진공 유도 용해의 세계를 깊이 파고들어 그 원리, 응용 분야, 이 방법을 통해 생산되는 특정 금속 분말 등을 탐구하는 것입니다. 노련한 금속공학자이든, 비행기 엔진의 부품이 어떻게 만들어지는지 궁금한 분이든, 이 가이드는 VIM의 모든 측면을 안내해 드릴 것입니다.
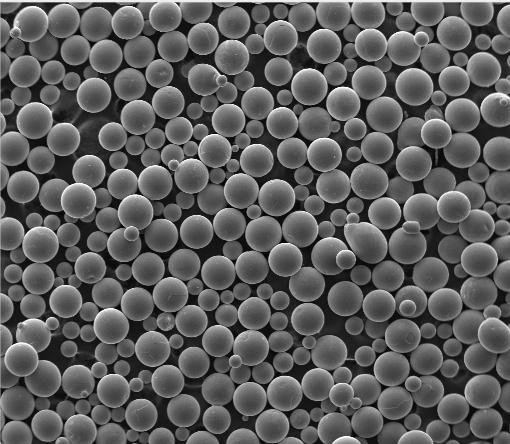
진공 유도 용융의 원리
진공 유도 용융이란 무엇인가요?
진공 유도 용해는 기본적으로 진공 환경에서 금속을 용해하는 공정으로, 대기 가스로 인한 오염 위험을 줄여줍니다. 하지만 단순히 금속을 녹이는 것 이상의 의미가 있습니다. 진공 환경은 금속의 화학적 특성을 제어하여 고순도의 최종 제품을 생산할 수 있도록 합니다. 용융은 고주파 전류가 금속이 들어 있는 도가니를 둘러싼 코일을 통과하는 전자기 유도를 통해 이루어집니다. 이렇게 하면 금속에 전류가 유도되어 금속이 가열되고 결국 녹게 됩니다.
이 공정은 특히 극한 조건에서 기계적 특성을 유지하기 위해 불순물이 없어야 하는 고성능 합금을 정제하는 데 적합합니다.
진공 유도 용융은 어떻게 작동하나요?
진공 유도 용융 과정에는 몇 가지 주요 단계가 포함됩니다:
- 충전: 고철, 합금 원소 및 필요한 첨가제를 포함한 원재료가 도가니에 적재됩니다.
- 녹는: 고주파 전류가 유도 코일을 통과하여 자기장을 생성합니다. 이 자기장은 금속에 전류를 유도하여 녹는점까지 가열합니다.
- 가스 제거: 금속이 녹으면서 원료에 갇혀 있던 가스가 방출됩니다. 진공 상태에서는 이러한 가스가 제거되어 금속에 갇히는 것을 방지합니다.
- 정제: 용융 중에 추가 합금 원소를 첨가하여 원하는 조성을 얻을 수 있습니다. 진공 환경은 금속의 화학적 특성을 제어하는 데 도움이 됩니다.
- 붓기: 용융물이 정제되면 추가 가공을 위해 금형에 붓거나 잉곳으로 주조합니다.
진공 유도 용융 공정의 주요 단계
단계 | 설명 |
---|---|
충전 | 도가니에 원료를 적재합니다. |
녹는 | 고주파 전류는 유도를 통해 열을 발생시켜 금속을 녹입니다. |
가스 제거 | 진공 상태에서 가스를 제거하여 오염을 방지합니다. |
정제 | 제어된 조건에서 합금 원소를 추가하고 용융물을 정제합니다. |
붓기 | 정제된 용융물은 몰드에 붓거나 잉곳으로 주조합니다. |
진공 유도 용융의 장점
진공 유도 용융은 다른 금속 정제 공정에 비해 몇 가지 장점이 있습니다:
- 순도: 진공 환경으로 오염을 최소화하여 매우 순수한 금속을 얻을 수 있습니다.
- 제어: 이 공정을 통해 금속의 화학 성분을 정밀하게 제어할 수 있습니다.
- 다용도성: VIM은 다양한 금속 및 합금, 특히 산소와 질소에 민감한 금속에 적합합니다.
- 효율성: 유도 가열 방식은 매우 효율적이어서 에너지 소비를 줄여줍니다.
진공 유도 용해와 기존 용해의 비교
측면 | 진공 유도 용융 | 기존 용융 |
---|---|---|
순도 | 진공 환경으로 인한 고순도 | 대기 중 가스 노출로 인한 순도 저하 |
제어 | 컴포지션에 대한 정밀한 제어 | 화학 성분에 대한 통제력 감소 |
에너지 효율성 | 유도 가열로 인한 높은 효율성 | 일반적으로 낮은 효율성 |
애플리케이션 | 고성능 합금, 초합금, 특수강 | 기본 합금을 포함한 광범위한 금속 |
금속의 구성 및 특성 진공 유도 용융
VIM의 금속 구성 이해
VIM에서 금속의 구성에 대해 이야기할 때 금속을 녹여 금형에 붓는 것만이 능사가 아닙니다. 진정한 마법은 금속의 구성을 제어하고 정제하는 과정에서 일어납니다. 항공우주용 고순도 티타늄을 생산하든 의료 기기용 스테인리스 스틸을 생산하든, 금속 공학자들은 VIM을 통해 합금의 조성을 조정하고 완벽하게 만들 수 있습니다.
일반적으로 가공되는 금속에는 초합금, 스테인리스강, 고순도 구리 등이 있습니다. 이러한 재료에는 니켈, 크롬, 몰리브덴, 코발트 등의 원소가 복잡하게 혼합되어 있는 경우가 많으며, 각 원소는 최종 제품에 특정 특성을 부여합니다.
표: 진공 유도 용융의 일반적인 요소와 그 속성
요소 | 기호 | 일반적인 합금 | 속성 |
---|---|---|---|
니켈 | Ni | 인코넬, 모넬, 하스텔로이 | 내식성, 고온 강도 |
크롬 | Cr | 스테인리스 스틸, 초합금 | 내식성, 경화성 |
몰리브덴 | Mo | 몰리브덴 강철, 하스텔로이 | 고온 강도, 크리프 저항성 |
코발트 | Co | 코발트-크롬 합금, 초합금 | 내마모성, 고온에서의 내식성 |
티타늄 | Ti | Ti-6Al-4V, CP 티타늄 | 높은 중량 대비 강도, 내식성 |
구리 | Cu | 고순도 구리, 황동, 청동 | 전기 전도성, 내식성 |
진공 유도 용융의 응용 분야
진공 유도 용융은 어디에 사용되나요?
VIM의 고유한 기능은 다양한 산업 분야에서 없어서는 안 될 필수 요소입니다. 항공우주 분야에서는 제트 엔진에 사용되는 고강도, 고온 합금을 생산하기 위해 VIM에 크게 의존하고 있습니다. 생의학 분야에서는 수술용 임플란트용 스테인리스강과 티타늄 합금을 생산하기 위해 VIM을 사용하여 인체에 부작용을 일으키지 않도록 최고 수준의 순도를 보장합니다.
표: 진공 유도 용융으로 생산된 금속의 응용 분야
산업 | 애플리케이션 | 일반적으로 사용되는 합금 |
---|---|---|
항공우주 | 제트 엔진 부품, 터빈 블레이드 | 인코넬, 하스텔로이, 티타늄 합금 |
바이오메디컬 | 수술용 임플란트, 치과 기기 | 스테인리스 스틸, 티타늄 합금 |
에너지 | 발전 터빈, 원자로 부품 | 초합금, 고순도 강재 |
자동차 | 고성능 엔진 구성 요소 | 몰리브덴 강, 스테인리스 강 |
전자 제품 | 고순도 구리 배선, 커넥터 | 고순도 구리, 특수 합금 |
툴링 | 고강도 공구, 절단 도구 | 공구강, 코발트-크롬 합금 |
진공 유도 용융으로 생산되는 특정 금속 분말
이제 진공 유도 용융을 사용하여 생산되는 특정 금속 분말에 대해 자세히 알아보겠습니다. 이러한 분말은 3D 프린팅에서 복잡한 고성능 부품을 만드는 데 사용되는 적층 제조와 같은 애플리케이션에 필수적입니다.
1. 인코넬 718 분말
- 설명: 인코넬 718은 니켈-크롬 합금으로 고온에서 강도와 내식성이 뛰어난 것으로 알려져 있습니다. 항공우주 분야, 특히 제트 엔진과 가스 터빈에 주로 사용됩니다.
- 애플리케이션: 항공우주, 가스터빈, 원자로.
2. Ti-6Al-4V 분말
- 설명: 이 티타늄 합금은 무게 대비 강도 비율과 생체 적합성으로 높은 평가를 받고 있습니다. 생체 의학 임플란트 및 항공 우주 부품에 널리 사용됩니다.
- 애플리케이션: 바이오메디컬 임플란트, 항공우주, 군사.
3. 하스텔로이 X 파우더
- 설명: 하스텔로이 X는 고온 환경에서 탁월한 성능을 발휘하는 니켈-크롬-철-몰리브덴 합금입니다. 가스 터빈 및 산업용 용광로 애플리케이션에 자주 사용됩니다.
- 애플리케이션: 가스터빈, 산업용 용광로, 화학 공정.
4. 316L 스테인리스 스틸 파우더
- 설명: 316L 스테인리스 스틸은 내식성이 뛰어나며 의료 기기, 식품 가공 및 화학 산업에서 일반적으로 사용됩니다.
- 애플리케이션: 의료 기기, 식품 가공, 화학 장비
5. 코발트-크롬 합금 분말
- 설명: 이 합금은 내마모성과 생체 적합성으로 잘 알려져 있어 치과 및 정형외과 임플란트에 이상적입니다.
- 애플리케이션: 치과 임플란트, 정형외과 임플란트, 절삭 공구.
6. 마징 강 분말
- 설명: 마레이징 강은 강도와 인성이 높아 항공우주 및 툴링 응용 분야에 적합한 것으로 알려져 있습니다.
- 애플리케이션: 항공우주, 툴링, 고강도 구조 부품.
7. 니오븀 합금 분말
- 설명: 니오븀 합금은 강도가 우수하고 열팽창이 적어 초전도 자석 및 기타 첨단 기술 응용 분야에 사용됩니다.
- 애플리케이션: 초전도 자석, 항공우주, 원자로.
8. AlSi10Mg 알루미늄 분말
- 설명: 이 알루미늄 합금은 기계적 특성이 우수하고 가벼워 적층 제조에 널리 사용됩니다.
- 애플리케이션: 자동차, 항공우주, 산업 부품
9. 탄탈륨 합금 분말
- 설명: 탄탈륨은 부식에 강하며 의료용 임플란트 및 전자 부품에 사용됩니다.
- 애플리케이션: 의료 임플란트, 전자, 화학 처리.
10. 구리-크롬 합금 분말
- 설명: 이 합금은 구리의 높은 전도성과 크롬의 강도를 결합하여 전기 및 열 응용 분야에 적합합니다.
- 애플리케이션: 전기 접점, 열교환기, 용접 전극.
사양, 크기, 등급 및 표준
VIM에서 생산한 재료로 작업할 때는 이러한 재료에 적용되는 사양, 크기, 등급 및 표준을 이해하는 것이 중요합니다. 이러한 매개변수는 금속 또는 합금이 의도한 용도에 필요한 성능 기준을 충족하는지 확인합니다.
표: 표: 일반적인 VIM 생산 합금의 사양 및 표준
합금 | 표준 | 등급 | 크기 범위 |
---|---|---|---|
인코넬 718 | ASTM B637, AMS 5662 | UNS N07718 | 분말: 15-53 미크론 |
Ti-6Al-4V | ASTM B348, AMS 4911 | 5학년 | 분말: 10-45 미크론 |
하스텔로이 X | ASTM B435, AMS 5536 | UNS N06002 | 분말: 20-63 미크론 |
316L 스테인리스 스틸 | ASTM F138, ISO 5832-1 | UNS S31603 | 분말: 15-53 미크론 |
코발트-크롬 | ASTM F75, ISO 5832-4 | CoCrMo 합금 | 분말: 15-45 미크론 |
마레이징 스틸 | AMS 6514, ASTM A538 | 300등급 | 분말: 10-45 미크론 |
니오븀 합금 | ASTM B393, AMS 7852 | Nb-1Zr | 분말: 20-63 미크론 |
AlSi10Mg | ASTM B209, EN AW-5052 | AlSi10Mg | 분말: 15-45 미크론 |
탄탈륨 합금 | ASTM B365, ASTM F560 | T-111 | 분말: 20-63 미크론 |
구리-크롬 | ASTM B624, AMS 4631 | C18150 | 분말: 20-53 미크론 |
공급업체 및 가격 세부 정보
진공 유도 용융 재료의 신뢰할 수 있는 공급업체를 찾는 것은 품질과 일관성을 보장하는 데 매우 중요합니다. 아래는 다양한 금속 분말에 대한 일반적인 가격 세부 정보와 함께 주요 공급업체를 나열한 표입니다.
표: 표: VIM 생산 금속 분말의 공급업체 및 가격
공급업체 | 위치 | 공급되는 합금 | 가격 책정 |
---|---|---|---|
회가나스 AB | 스웨덴 | 인코넬 718, Ti-6Al-4V, 316L SS | 인코넬 718: ~$50/kg, Ti-6Al-4V: ~$300/kg |
카펜터 기술 | 미국 | 마레이징 스틸, 하스텔로이 X | 마레이징 스틸: ~$150/kg, 하스텔로이 X: ~$250/kg |
샌드빅 머티리얼즈 | 스웨덴 | 코발트-크롬, 니오븀 합금 | 코발트-크롬: ~$200/kg, 니오븀 합금: ~$400/kg |
GKN 첨가제 | 독일 | AlSi10Mg, 구리-크롬 | AlSi10Mg: ~$30/kg, 구리-크롬: ~$100/kg |
ATI 금속 | 미국 | 탄탈륨 합금, 인코넬 718 | 탄탈륨 합금: ~$600/kg, 인코넬 718: ~$50/kg |
진공 유도 용융의 장단점
모든 야금 공정에는 장단점이 있으며 진공 유도 용해도 예외는 아닙니다. VIM의 장단점을 자세히 살펴보겠습니다.
진공 유도 용융의 장점
- 고순도: 진공 환경은 가스로 인한 오염을 현저히 줄여 매우 순수한 금속을 만들어냅니다.
- 정밀한 제어: 이 공정을 통해 합금 조성을 정확하게 제어할 수 있어 특수 합금 생산에 이상적입니다.
- 다용도성: VIM은 다양한 금속과 합금을 가공할 수 있어 다양한 산업에 유연한 옵션이 될 수 있습니다.
- 에너지 효율성: 유도 가열은 금속을 녹이는 매우 효율적인 방법으로 전체 에너지 소비를 줄입니다.
진공 유도 용융의 단점
- 높은 비용: VIM과 관련된 장비 및 에너지 비용은 기존 용융 공정에 비해 높습니다.
- 복잡성: 이 프로세스는 고도로 숙련된 작업자와 정밀한 제어가 필요하므로 다른 방법보다 더 복잡합니다.
- 제한된 규모: VIM은 일반적으로 고부가가치 합금의 소량 배치에 사용되므로 대규모 생산에는 사용이 제한됩니다.
표: 진공 유도 용해의 장점과 단점 비교: 표
측면 | 장점 | 단점 |
---|---|---|
순도 | 진공 환경으로 인한 고순도 | – |
제어 | 합금 조성에 대한 정밀한 제어 | – |
다용도성 | 다양한 금속 및 합금에 적합 | 소규모 배치 크기로 제한 |
에너지 효율성 | 유도 가열을 통한 고효율 | 높은 장비 및 운영 비용 |
복잡성 | – | 고도로 숙련된 운영자 필요 |
규모 | – | 소규모 생산으로 제한 |
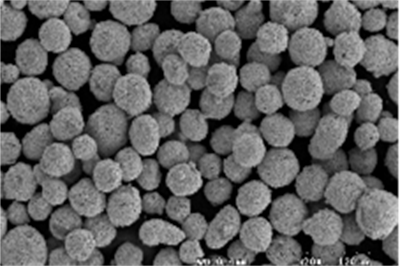
자주 묻는 질문
마지막으로 진공 유도 용해에 대해 자주 묻는 질문 몇 가지를 정리해 보겠습니다.
질문 | 답변 |
---|---|
VIM을 사용하여 가공할 수 있는 금속은 무엇인가요? | 초합금, 스테인리스강, 티타늄 합금 등을 포함한 다양한 금속을 사용할 수 있습니다. |
VIM에 진공이 필요한 이유는 무엇인가요? | 진공은 가스로 인한 오염을 줄여 고순도의 최종 제품을 보장합니다. |
VIM에서 생산된 금속의 주요 응용 분야는 무엇인가요? | 항공우주, 생물의학, 에너지, 고성능 자동차 부품. |
VIM은 다른 용융 공정과 어떻게 다른가요? | VIM은 더 높은 순도와 정밀한 제어를 제공하지만 비용과 복잡성이 더 높습니다. |
생산되는 금속 분말의 일반적인 크기는 어떻게 되나요? | 분말 크기는 일반적으로 합금과 용도에 따라 10~63미크론입니다. |
VIM에서 생산된 금속이 더 비쌉니까? | 예, 프로세스와 관련된 비용이 높지만 우수한 성능을 제공합니다. |
결론
진공 유도 용융 은 고순도, 고성능 금속 및 합금을 생산하는 데 중요한 역할을 하는 정교한 공정입니다. 항공우주, 바이오메디컬 또는 최고급 소재를 필요로 하는 모든 산업 분야에서 VIM은 자주 사용되는 공정입니다. 합금 구성을 정밀하게 제어하고 오염을 최소화하며 고품질 금속 분말을 효율적으로 생산할 수 있는 능력 덕분에 VIM은 현대 금속 공학에서 필수적인 기술로 자리 잡았습니다. 이 공정의 원리부터 응용 분야, 생산되는 특정 재료에 이르기까지 이 공정의 복잡성을 이해하는 것은 재료 과학이나 엔지니어링에 종사하는 모든 사람에게 중요합니다.
이 가이드를 통해 진공 유도 용해에 대한 이해와 산업 전반의 혁신을 주도하는 첨단 소재 생산에 있어 진공 유도 용해의 중요성에 대해 확실히 이해하셨을 것입니다. 공급업체를 선택하거나 합금을 비교하거나 단순히 공정이 어떻게 작동하는지 궁금하다면 여기서 얻은 지식이 도움이 될 것입니다.