불활성 가스 분무 (IGA)는 잘 알려지지는 않았지만 현대 사회에 절대적으로 중요한 기술 중 하나입니다. 이 공정은 3D 프린팅에서 항공우주 부품에 이르기까지 모든 분야에 사용되는 금속 분말을 생산하여 고순도, 미세 입자 크기, 일관된 품질을 보장합니다. 그렇다면 불활성 가스 원자화란 정확히 무엇일까요? 어떻게 작동하며 왜 그렇게 중요한 것일까요? 커피 한 잔을 들고 금속 분말과 분무 공정, 그리고 그 뒤에 숨겨진 흥미로운 과학의 세계에 대해 자세히 알아보세요.
불활성 가스 분무 개요
불활성 가스 분무는 불활성 가스(아르곤 또는 질소 등)의 고속 흐름을 사용하여 용융 금속을 미세한 방울로 분해하는 분말 야금 공정입니다. 이 방울은 미세한 구형의 금속 분말로 응고됩니다. 이 방법은 공정 중에 사용되는 불활성 분위기 덕분에 산화가 없는 매우 구형의 깨끗한 분말을 생산할 수 있기 때문에 널리 사용됩니다.
간단히 말해, 불활성 기체는 고성능 선풍기, 녹은 금속은 액체 초콜릿의 흐름이라고 생각하면 됩니다. 팬은 초콜릿을 작은 물방울로 만들어 냉각시키고 작고 둥근 조각으로 응고시킵니다. 물론 이 경우에는 초콜릿이 아닌 금속에 대해 이야기하고 있지만 원리는 매우 유사합니다.
불활성 가스 분무의 주요 구성 요소
고품질 금속 분말을 생산하려면 불활성 가스 분무 공정의 모든 단계가 중요합니다. 주요 구성 요소를 분석해 보겠습니다:
- 용광로: 금속을 정확한 온도로 녹이는 곳.
- 노즐 또는 분무 챔버: 용융 금속이 이 구멍을 통해 부어져 불활성 기체 흐름에 부딪힙니다.
- 불활성 가스 공급: 아르곤 또는 질소인 경우가 많은 이 가스는 산화를 방지하고 입자 크기를 제어합니다.
- 냉각 및 수집 시스템: 금속 방울이 응고되어 분말로 수집되는 곳입니다.
이러한 각 구성 요소는 최종 제품이 순도, 입자 크기 분포 및 모양에 대한 엄격한 사양을 충족하는 데 중추적인 역할을 합니다.
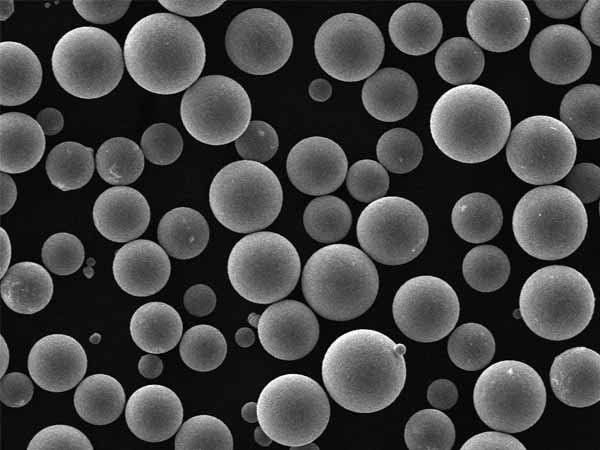
어떻게 불활성 가스 분무 일?
이 프로세스가 어떻게 작동하는지 자세히 살펴봅시다. 용융 금속을 챔버에 붓는다고 상상해 보세요. 금속이 작은 노즐을 통해 흐르면 즉시 불활성 가스의 고속 흐름으로 분사되어 금속이 미세한 방울로 부서집니다. 이 방울은 수집 챔버로 떨어지면서 빠르게 냉각되고 응고되어 미세한 분말로 변합니다.
불활성 가스 원자화 과정의 단계:
- 준비: 금속은 먼저 용광로에서 녹습니다. 금속의 종류와 녹는점에 따라 필요한 특정 용광로와 온도 제어가 결정됩니다.
- 원자화: 용융 금속은 작은 노즐을 통해 강제로 주입됩니다. 동시에 불활성 가스(예: 아르곤 또는 질소)의 고속 분사가 금속을 타격하여 작은 물방울로 분해합니다.
- 냉각 및 응고: 물방울이 분무 챔버를 통과하면서 빠르게 냉각되고 응고됩니다.
- 컬렉션: 응고된 금속 입자는 챔버 바닥에 분말 형태로 수집됩니다.
이 공정은 가스 종류와 압력, 용융 금속의 온도, 분무 노즐의 설계와 같은 요소를 조정하여 특정 특성을 가진 분말을 생산하도록 맞춤화할 수 있습니다.
불활성 가스 분무로 생산되는 금속 분말의 특성
불활성 가스 분무로 생산되는 금속 분말의 품질은 여러 가지 요인에 의해 영향을 받습니다. 이러한 특성을 더 자세히 살펴보겠습니다:
특성 | 설명 |
---|---|
입자 크기 분포 | 불활성 가스 분무는 입자 크기 분포가 좁은 분말을 생산하므로 재료 특성을 정밀하게 제어해야 하는 애플리케이션에 매우 중요합니다. |
모양 | 분말은 일반적으로 구형이기 때문에 유동성과 포장 밀도가 향상됩니다. |
순도 | 불활성 가스를 사용하면 산화와 오염을 방지하여 고순도 분말을 얻을 수 있습니다. |
표면적 | 분말의 표면적은 소결 거동과 반응성에 영향을 미치는 분무 매개변수를 조정하여 제어할 수 있습니다. |
밀도 | 파우더는 애플리케이션 요구 사항에 따라 특정 밀도로 생산할 수 있습니다. |
이러한 특성으로 인해 불활성 기체 분무 분말은 정밀도와 품질이 가장 중요한 다양한 고성능 애플리케이션에 이상적입니다.
불활성 가스 분무로 생산되는 금속 분말의 종류
불활성 가스 분무를 사용하여 다양한 금속과 합금을 분무할 수 있으며, 각각 고유한 특성과 용도가 있습니다. 다음은 가장 일반적으로 생산되는 금속 분말 몇 가지를 살펴봅니다:
금속/합금 | 설명 | 애플리케이션 |
---|---|---|
스테인리스 스틸(316L) | 높은 내식성과 기계적 특성으로 의료 및 항공우주 분야에 이상적입니다. | 3D 프린팅, 의료용 임플란트, 항공우주 부품 |
티타늄 합금(Ti-6Al-4V) | 가볍고 강도가 높으며 내식성이 뛰어나 항공우주 및 생물의학 분야에서 자주 사용됩니다. | 항공우주 구조물, 정형외과 임플란트, 자동차 부품 |
알루미늄 합금(AlSi10Mg) | 가볍고 튼튼하며 다용도로 사용할 수 있는 합금으로 경량 건축 분야에 널리 사용됩니다. | 3D 프린팅, 자동차 부품, 항공우주 부품 |
니켈 초합금(인코넬 718) | 특히 열악한 환경에서도 고온 강도, 내식성, 안정성이 뛰어난 것으로 알려져 있습니다. | 터빈 블레이드, 항공우주 부품, 화학 처리 장비 |
코발트-크롬 합금 | 의료 및 치과 분야에서 자주 사용되는 고강도, 내마모성 및 생체 적합성이 결합되어 있습니다. | 치과 임플란트, 관절 교체, 고온 산업용 애플리케이션 |
구리 합금(CuCrZr) | 높은 열 및 전기 전도성을 제공하여 전기 및 열 관리 애플리케이션에 필수적입니다. | 열교환기, 전기 부품, 적층 제조 |
공구강(M2) | 경도, 내마모성 및 인성으로 잘 알려져 있으며 공구 및 금형 제작 산업에서 일반적으로 사용됩니다. | 절삭 공구, 금형, 금형, 적층 가공 |
마그네슘 합금(AZ91D) | 기계적 특성이 우수하고 가벼워 자동차 및 항공우주 분야에서 자주 사용됩니다. | 자동차 부품, 항공우주 구조물, 3D 프린팅 |
텅스텐 카바이드 | 매우 단단하고 내마모성이 뛰어나 절삭 공구 및 연마 용도에 널리 사용됩니다. | 절삭 공구, 내마모성 코팅, 채굴 장비 |
청동 합금 | 우수한 기계적 특성과 내식성을 갖춘 다목적 합금으로 산업 및 예술 분야에 자주 사용됩니다. | 베어링, 부싱, 조형물, 적층 가공 |
이러한 금속 분말은 각각 고성능 항공우주 부품부터 일상적인 산업용 도구에 이르기까지 다양한 용도에 적합한 특정 특성을 가지고 있습니다.
구성 불활성 가스 분무 금속 분말
불활성 가스 분무로 생산되는 금속 분말의 구성은 사용되는 금속 또는 합금에 따라 크게 달라질 수 있습니다. 다음은 일반적으로 원자화되는 몇 가지 재료의 일반적인 조성을 자세히 살펴봅니다:
금속/합금 | 구성 |
---|---|
스테인리스 스틸(316L) | 철, 크롬(16-18%), 니켈(10-14%), 몰리브덴(2-3%), 망간, 실리콘, 탄소 |
티타늄 합금(Ti-6Al-4V) | 티타늄, 알루미늄(5.5-6.75%), 바나듐(3.5-4.5%), 철, 산소 |
알루미늄 합금(AlSi10Mg) | 알루미늄, 실리콘(9-11%), 마그네슘(0.2-0.4%), 철, 구리, 망간 |
니켈 초합금(인코넬 718) | 니켈, 크롬(17-21%), 철, 몰리브덴(2.8-3.3%), 니오븀(4.75-5.5%), 티타늄, 알루미늄, 코발트, 망간 |
코발트-크롬 합금 | 코발트, 크롬(27-30%), 몰리브덴(5-7%), 니켈, 철, 탄소 |
구리 합금(CuCrZr) | 구리, 크롬(0.5-1.2%), 지르코늄(0.03-0.2%), 철분 |
공구강(M2) | 철, 탄소(0.8-1.2%), 텅스텐(5-6.5%), 크롬(3.75-4.5%), 바나듐(1.75-2.2%), 몰리브덴(4.5-5.5%) |
마그네슘 합금(AZ91D) | 마그네슘, 알루미늄(8-9.5%), 아연(0.5-1.3%), 망간 |
텅스텐 카바이드 | 텅스텐, 탄소, 코발트(바인더) |
청동 합금 | 구리, 주석(10-12%), 아연, 납, 인 |
이러한 조성물은 분무 공정 중에 신중하게 제어되어 결과 분말이 의도한 용도에 맞게 원하는 특성을 갖도록 합니다.
불활성 가스 분무 금속 분말의 응용 분야
불활성 가스 분무 금속 분말은 다양한 산업과 응용 분야에서 사용됩니다. 고순도, 미세한 입자 크기, 뛰어난 유동성으로 인해 첨단 제조 공정에 이상적입니다. 주요 응용 분야를 자세히 살펴보세요:
애플리케이션 | 설명 | 사용된 금속 분말 |
적층 제조(3D 프린팅) | 레이어별 증착을 사용하여 복잡한 부품을 고정밀로 제조합니다. | 스테인리스 스틸, 티타늄, 알루미늄, 인코넬, 코발트-크롬 |
항공우주 부품 | 항공기 및 우주선용 고강도 경량 부품으로, 엄격한 재료 및 치수 공차로 생산되는 경우가 많습니다. | 티타늄, 니켈 초합금, 알루미늄 합금 |
의료용 임플란트 | 생체 적합성 금속 분말은 고관절, 치과 크라운 및 기타 의료 기기와 같은 임플란트 생산에 사용됩니다. | 티타늄 합금, 코발트-크롬, 스테인리스 스틸 |
자동차 부품 | 엔진 부품 및 구조 요소를 포함한 차량용 가볍고 내구성이 뛰어난 금속 부품. | 알루미늄 합금, 마그네슘 합금, 공구강 |
절단 도구 및 금형 | 내마모성과 내구성이 뛰어난 절삭 공구, 금형 및 금형 생산에 사용되는 고경도 금속 분말입니다. | 공구강, 텅스텐 카바이드, 티타늄 합금 |
용사 코팅 | 마모, 부식 및 고온에 노출된 표면에 보호 코팅을 적용하기 위해 용사 공정에 사용되는 금속 분말입니다. | 니켈 초합금, 텅스텐 카바이드, 코발트-크롬 |
전기 부품 | 커넥터, 접점, 방열판과 같은 전기 및 전자 부품 제조에 사용되는 전도성 금속 분말입니다. | 구리 합금, 은 합금, 알루미늄 합금 |
필터링 시스템 | 산업, 의료 및 환경 애플리케이션을 위한 다공성 필터 및 여과 시스템을 생산하는 데 사용되는 금속 분말입니다. | 스테인리스 스틸, 청동, 니켈 초합금 |
에너지 저장 및 배터리 | 전기 자동차 및 재생 에너지 애플리케이션을 포함한 첨단 배터리 및 에너지 저장 시스템 개발에 사용되는 금속 분말입니다. | 니켈, 코발트, 티타늄 합금, 마그네슘 합금 |
보석 및 장식 예술 | 적층 제조 및 기타 고급 기술을 통해 복잡한 보석류와 장식용 물건을 제작하는 데 사용되는 미세 금속 분말입니다. | 골드, 실버, 브론즈, 플래티넘 |
이러한 각 응용 분야에는 입자 크기, 순도 및 화학 성분과 같은 특정 특성을 가진 금속 분말이 필요하며, 불활성 가스 분무를 통해 정밀하게 제어할 수 있습니다.
불활성 가스 분무의 장점
불활성 가스 분무는 다른 분말 생산 방법에 비해 여러 가지 장점이 있어 많은 고성능 애플리케이션에 적합한 선택입니다. 그 이유는 다음과 같습니다:
이점 | 설명 |
---|---|
고순도 | 불활성 가스(아르곤 및 질소 등)를 사용하면 산화와 오염을 방지하여 화학적 순도가 높은 분말을 만들 수 있습니다. |
구형 파티클 모양 | 이 공정은 고도로 구형화된 입자를 생성하여 분말의 유동성, 패킹 밀도 및 소결 거동을 개선합니다. |
제어된 입자 크기 | 불활성 가스 원자화를 통해 입자 크기 분포를 정밀하게 제어할 수 있으며, 이는 적층 제조 및 분말 야금과 같은 애플리케이션에 매우 중요합니다. |
다용도성 | 이 방법은 다른 방법으로 처리하기 어려운 금속과 합금을 포함하여 다양한 금속과 합금으로 분말을 생산하는 데 사용할 수 있습니다. |
확장성 | 이 공정은 확장성이 뛰어나 특수 분말의 소규모 생산과 대규모 산업 응용 분야 모두에 적합합니다. |
낮은 불순물 수준 | 불활성 가스 분무는 불순물이 적은 분말을 생성하므로 항공우주 및 의료 기기와 같은 고성능 애플리케이션에 필수적입니다. |
최소한의 분리 | 분무 공정의 균일성은 분말의 분리 위험을 최소화하여 배치 전체에서 일관된 재료 특성을 보장합니다. |
이러한 장점으로 인해 불활성 가스 분무는 특히 품질과 성능이 저하될 수 없는 응용 분야에서 금속 분말을 생산하는 데 선호되는 방법입니다.
불활성 가스 분무의 단점
불활성 가스 분무는 강력한 기술이지만 문제가 없는 것은 아닙니다. 다음은 몇 가지 잠재적인 단점입니다:
단점 | 설명 |
---|---|
높은 비용 | 불활성 가스 분무에 필요한 장비와 에너지가 비싸기 때문에 다른 방법으로 생산한 분말보다 비용이 많이 들 수 있습니다. |
복잡한 프로세스 제어 | 이 공정은 가스 압력, 온도, 유량 등 다양한 파라미터를 정밀하게 제어해야 하므로 생산이 복잡하고 숙련된 작업자가 필요합니다. |
제한된 입자 크기 범위 | 이 공정은 미세 분말을 생산할 수 있지만, 달성할 수 있는 입자 크기 범위에는 제한이 있어 모든 애플리케이션의 요구 사항을 충족하지 못할 수 있습니다. |
환경 문제 | 아르곤과 질소와 같은 불활성 가스를 사용하는 것은 효과적이기는 하지만 자원 집약적일 수 있으며 생산 규모에 따라 환경 문제를 야기할 수 있습니다. |
장비 유지보수 | 분무 장비, 특히 노즐은 마모되기 쉬우므로 정기적인 유지보수나 교체가 필요해 운영 비용이 증가할 수 있습니다. |
특히 비용에 민감하거나 대규모 응용 분야에서 분말 생산 방법으로 불활성 가스 분무를 선택할 때는 이러한 제한 사항을 이해하는 것이 중요합니다.
비교: 불활성 가스 분무와 다른 분말 생산 방법 비교
불활성 가스 분무는 금속 분말을 생산하는 데 사용되는 여러 방법 중 하나에 불과합니다. 다른 인기 있는 기법과 비교해 보겠습니다:
방법 | 불활성 가스 분무 | 물 분무 | 플라즈마 원자화 | 기계적 합금 |
---|---|---|---|---|
파티클 모양 | 구형 | 불규칙 | 구형 | 벗겨지거나 불규칙한 |
순도 | 높음(불활성 대기로 인해) | 더 낮음(물에서 산화 가능성으로 인해) | 매우 높음(불활성 대기, 고순도 사료) | 다양함(시작 자료에 따라 다름) |
입자 크기 분포 | 좁은 | 광범위 | 좁은 | 광범위 |
생산 비용 | 보통에서 높음 | 낮음에서 보통 | 높음 | 낮음 |
애플리케이션 | 항공우주, 의료, 적층 제조 | 구조 부품, 용접, 분말 야금 | 고성능 합금, 항공우주, 의료용 | 특수 합금, 나노 복합재 |
확장성 | 높음 | 매우 높음 | 낮음에서 보통 | 낮음 |
재료 범위 | 와이드(대부분의 금속 및 합금) | 와이드(대부분의 금속 및 합금) | 제한적(일반적으로 고가 재료) | 와이드(비금속 포함) |
환경 영향 | 보통(불활성 가스 사용) | 낮음(물을 사용하지만 폐기물이 발생함) | 높음(에너지 집약적, 희귀 재료) | 보통(에너지 사용, 자재 낭비) |
각 방법에는 장단점이 있어 다양한 유형의 분말과 용도에 적합합니다. 불활성 가스 분무는 입자 크기가 제어된 고순도 구형 분말을 생산할 수 있어 까다로운 응용 분야에 이상적입니다.
불활성 가스 분무 금속 분말의 사양 및 표준
금속 분말을 생산할 때는 품질과 성능을 보장하기 위해 특정 표준 및 사양을 충족하는 것이 중요합니다. 다음은 불활성 가스 분무 분말과 관련된 몇 가지 일반적인 사양 및 표준입니다:
표준/사양 | 설명 | 관련 파우더 |
---|---|---|
ASTM B214 | 금속 분말의 체 분석 표준 시험 방법 | 모든 금속 분말 |
ISO 4497 | 금속 분말 - 건식 체질에 의한 입자 크기 측정 | 모든 금속 분말 |
ASTM B822 | 광 산란에 의한 금속 분말 및 관련 화합물의 입자 크기 분포에 대한 표준 시험 방법 | 모든 금속 분말 |
ISO 3923-1 | 금속 분말 - 겉보기 밀도 측정 - 1부: 깔때기 방법 | 모든 금속 분말 |
ASTM B213 | 홀 유량계 깔때기를 이용한 금속 분말의 유량 표준 시험 방법 | 모든 금속 분말 |
AMS 4999 | 항공우주 응용 분야를 위한 적층 제조 티타늄-6Al-4V 합금 분말 | 티타늄 합금 |
ISO 22068 | 금속 분말 - 탭 밀도 측정 | 모든 금속 분말 |
ASTM F3302 | 적층 제조 표준 - 완제품 속성 - 적층 제조에 사용되는 티타늄 합금의 표준 사양 | 티타늄 합금 |
AMS 5659 | 니켈 합금, 부식 및 내열성, 바, 단조 및 링 등, UNS N07718 | 인코넬 718 |
ISO 17804 | 니켈 합금 - 크리프 및 응력 파열 특성 측정 | 니켈 합금 |
이 표준은 불활성 가스 분무로 생산된 금속 분말이 의도된 용도에 필요한 품질 및 성능 요구 사항을 충족하도록 보장합니다.
불활성 가스 분무 금속 분말의 공급업체 및 가격
고성능 애플리케이션을 위한 금속 분말을 소싱할 때는 적합한 공급업체를 찾는 것이 중요합니다. 다음은 주요 공급업체 목록과 대략적인 가격입니다:
공급업체 | 위치 | 특수 분말 | 대략적인 가격(kg당 USD) |
---|---|---|---|
H.C. 스탁 솔루션 | 미국, 독일 | 티타늄, 텅스텐, 몰리브덴 | $100 – $500 |
샌드빅 재료 기술 | 스웨덴, 미국 | 스테인리스 스틸, 티타늄, 공구강 | $50 – $200 |
LPW 기술 | 영국, 미국 | 스테인리스 스틸, 니켈 합금, 코발트-크롬 | $75 – $300 |
아르곤화물 주식회사 | 미국 | 티타늄, 스테인리스 스틸, 알루미늄 합금 | $150 – $400 |
ExOne | 미국 | 3D 프린팅을 위한 다양한 금속 분말 | $200 – $600 |
금속 분석 | UK | 티타늄, 스테인리스 스틸, 알루미늄 합금 | $100 – $350 |
프렉스에어 표면 기술 | 미국 | 니켈 초합금, 코발트-크롬 | $120 – $500 |
3D Systems | 미국 | 3D 프린팅을 위한 다양한 합금 | $150 – $500 |
커트 J. 레스커 컴퍼니 | 미국 | 티타늄, 스테인리스강, 공구강 | $100 – $250 |
고급 파우더 제품 | 미국 | 특수 응용 분야를 위한 고순도 분말 | $200 – $700 |
참고: 가격은 분말 크기, 순도, 구매량 등의 요인에 따라 크게 달라질 수 있습니다. 견적 및 구체적인 요구 사항은 공급업체에 직접 문의하는 것이 가장 좋습니다.
불활성 가스 분무의 장단점
불활성 가스 분무의 장단점을 이해하면 불활성 가스 분무가 여러분의 필요에 적합한 방법인지 평가하는 데 도움이 됩니다. 다음은 핵심 사항을 분석한 내용입니다:
장점 | 단점 |
---|---|
고순도 | 고가의 장비 |
이 공정은 산화와 오염을 방지하여 고순도 분말을 보장합니다. | 분무 장비와 불활성 가스를 사용하는 데 드는 비용이 상당히 높을 수 있습니다. |
일관된 파티클 모양 | 복잡한 프로세스 제어 |
일정한 유동성과 밀도를 가진 구형 입자를 생성합니다. | 가스 압력 및 온도와 같은 매개변수에 대한 정밀한 제어가 필요하며, 이는 복잡하고 까다로울 수 있습니다. |
좁은 입자 크기 분포 | 제한된 입자 크기 범위 |
고정밀 애플리케이션에 필수적인 좁은 범위의 입자 크기를 가진 분말을 제공합니다. | 미세 분말을 생산할 수는 있지만, 달성 가능한 크기의 범위가 모든 요구 사항을 충족하지 못할 수 있습니다. |
다양한 소재의 활용성 | 환경 영향 |
다양한 금속 및 합금에 적합하며 유연성을 제공합니다. | 생산 공정은 특히 에너지와 불활성 가스 사용 측면에서 자원 집약적일 수 있습니다. |
확장 가능한 프로덕션 | 유지 관리 요구 사항 |
이 프로세스는 소규모 배치와 대규모 배치 모두에 맞게 확장할 수 있습니다. | 장비, 특히 노즐은 정기적인 유지보수가 필요하므로 운영 비용이 증가합니다. |
불활성 가스 분무는 정밀도와 다목적성을 결합한 고급 방법이지만, 그 자체의 어려움과 비용이 따릅니다.
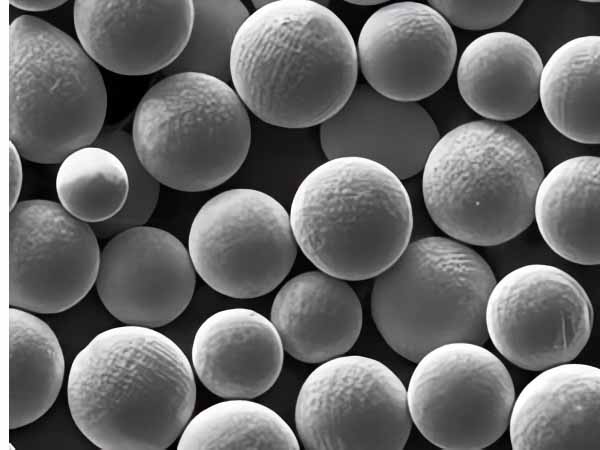
자주 묻는 질문
다음은 불활성 가스 분무에 대한 일반적인 질문에 대한 간단한 답변입니다:
질문 | 답변 |
---|---|
불활성 가스 분무의 주요 장점은 무엇인가요? | 가장 큰 장점은 산화를 방지하는 불활성 가스를 사용하기 때문에 생산되는 분말의 순도가 높다는 것입니다. |
불활성 가스 분무는 모든 금속에 사용할 수 있나요? | 다용도로 사용할 수 있지만 모든 금속이 불활성 가스 분무에 적합한 것은 아닙니다. 스테인리스 스틸, 티타늄, 니켈 합금을 포함한 다양한 금속에 적합합니다. |
입자 크기가 파우더 사용에 어떤 영향을 미치나요? | 입자 크기는 유동성, 소결 거동 및 응용 분야 적합성에 영향을 미칩니다. 더 미세한 분말은 적층 제조와 같은 고정밀 애플리케이션에 자주 사용됩니다. |
불활성 가스 분무 분말의 일반적인 응용 분야는 무엇입니까? | 일반적인 애플리케이션으로는 항공우주 부품, 의료용 임플란트, 자동차 부품, 절삭 공구 등이 있습니다. |
불활성 가스 분무는 다른 방법과 어떻게 다른가요? | 불활성 가스 분무는 물 분무나 기계적 합금과 같은 방법에 비해 순도가 높고 입자 모양이 더 좋지만 비용이 더 많이 듭니다. |
불활성 가스 분무 분말의 일반적인 비용은 얼마인가요? | 비용은 재료와 수량에 따라 다르며, 일반적으로 킬로그램당 $50에서 $700까지 다양합니다. |
불활성 가스 분무와 관련된 환경 영향은 없나요? | 예, 이 공정은 특히 불활성 가스를 사용하고 분무에 필요한 에너지로 인해 자원 집약적일 수 있습니다. |
결론
불활성 가스 분무 는 고품질 금속 분말을 생산하기 위한 정교한 기술로 돋보입니다. 입자 크기가 제어된 구형의 고순도 분말을 생산할 수 있기 때문에 다양한 첨단 응용 분야에 필수적입니다. 높은 비용과 복잡한 제어 요구 사항에도 불구하고, 특히 정밀도와 재료 품질이 가장 중요한 산업에서는 이점이 단점보다 더 큰 경우가 많습니다.
항공우주, 의료 기기, 적층 제조 등 어떤 분야에 종사하든 불활성 가스 분무에 대해 자세히 이해하면 재료 요구 사항에 대해 정보에 입각한 결정을 내리는 데 도움이 될 수 있습니다. 이 가이드는 기술적 이점부터 실제 응용 분야 및 공급업체 옵션에 이르기까지 불활성 가스 분무의 세계와 현대 제조에서의 역할에 대한 포괄적인 개요를 제공합니다.