전극 분말 용접 전극 및 용사 소모품 제조에 공급 원료로 사용되는 특수 금속, 합금 및 복합 분말을 말합니다. 분말 특성은 용접, 표면 처리, 클래딩, PTA 및 관련 고온 공정에서 코팅, 충진 및 인터페이스의 야금학적, 기계적 및 가공 성능을 결정하는 데 중요한 역할을 합니다.
전극 분말의 종류
전극에 사용되는 주요 파우더 카테고리는 다음과 같습니다:
유형 | 설명 | 공통 구성 요소 |
---|---|---|
베이스 파우더 | 대량의 증착된 용접 금속 조성물 제공 | 철, 니켈, 코발트, 구리 합금 |
매트릭스 파우더 | 구성 요소를 하나로 묶어주는 바인더 | 철, 니켈, 코발트, 붕소가 포함된 구리 합금, 실리콘 첨가제 |
합금 분말 | 목표 화학을 달성하기 위해 추가됨 | 망간, 크롬, 몰리브덴, 바나듐, 니오븀 |
플럭스 파우더 | 아크 안정성 및 습윤성 촉진 | 루틸, 규산염, 불소, 산화물 |
복합 분말 | 보증금 강화 또는 기능 부여 | 텅스텐 카바이드, 표면 탄성률 에이전트와 같은 경질 상 |
입자 크기 분포, 모양, 흐름 특성, 용융 중 층화 경향 및 재구성 거동은 모두 가공 품질과 일관성에 큰 영향을 미칩니다.
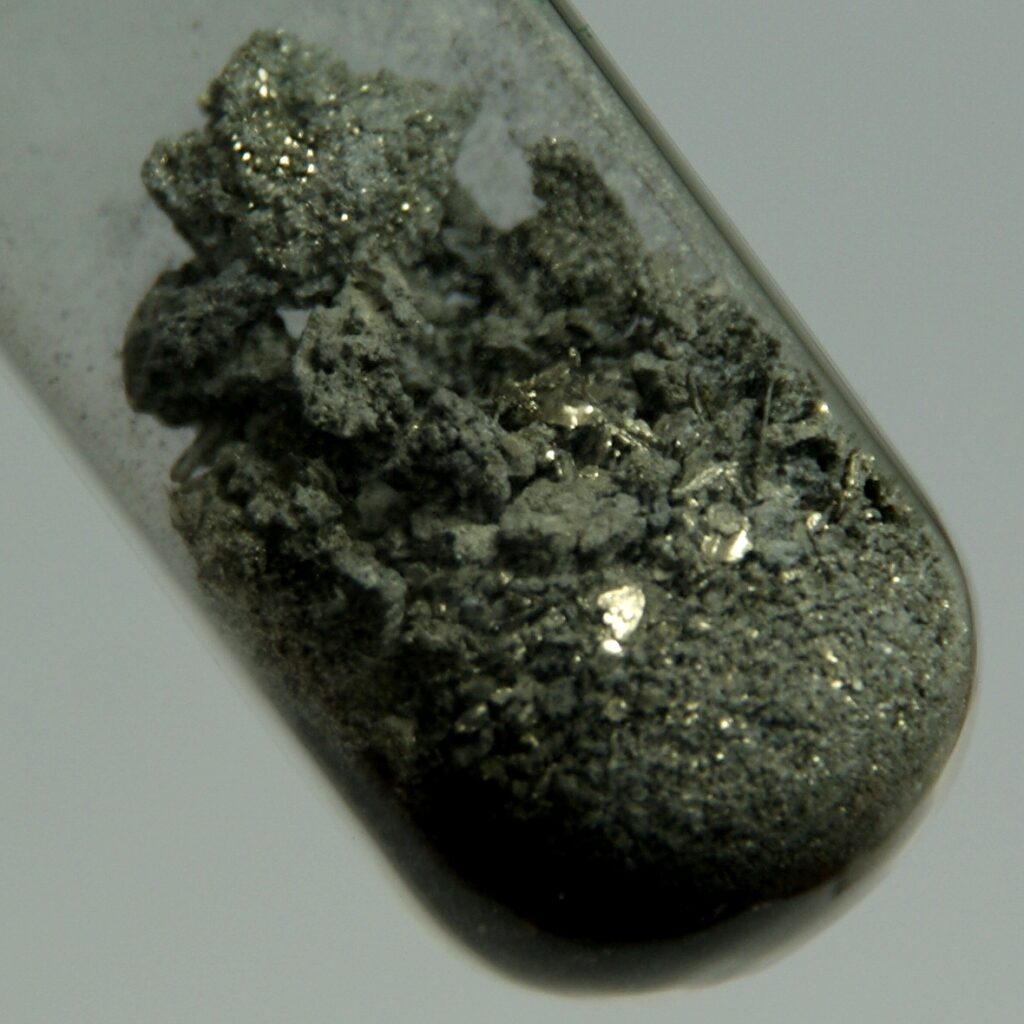
전극 분말 구성
전극 분말에는 용융 및 완성된 상태에서 원하는 특성과 성능을 개발하기 위해 맞춤화된 복잡한 구성이 포함되어 있습니다.
요소 | 주요 기능 |
---|---|
철 | 탄소강 및 저합금의 기본 구성 성분 |
니켈 | 내식성, 인장 강도를 위해 추가됨 |
크롬 | 스테인리스강의 주요 합금 원소, 마모, 열 및 부식에 대한 내성 |
몰리브덴 | 고체 용액 강화제, 고온 경도 지원 |
망간, 바나듐, 니오븀, 티타늄 | 강화를 위한 탄화물/질화물을 형성하는 중요한 미세 합금 원소 |
실리콘, 붕소 | 건전한 용접에 필수적인 탈산제 |
탄소 | 강도, 경도 및 용접성에 영향을 미치는 철강 성분의 기본 구성 요소입니다. |
구리 | 여러 합금 제품군의 내식성 향상 |
합금 원소의 역할
- 입자 경계를 강화하는 유익한 침전물 형성
- 기계적 특성 개선을 위한 다양한 미세 구조 단계 개발
- 경화성을 높여 관통 두께 특성 향상
- 높은 작동 온도에서 내열성 활성화
- 염화물 및 황화물과 같은 부식성 물질에 의한 손상 방지
고급 전극은 공융 반응과 같은 복잡한 야금학적 메커니즘을 활용하여 탁월한 사용 중 성능을 생성합니다.
전극 분말 속성
속성 | 일반적인 값 | 측정 방법 |
---|---|---|
파티클 모양 | 불규칙, 수지상, 분쇄됨 | 현미경, SEM 이미징 |
입자 크기 분포 | 10~150미크론 | 레이저 회절, 체질 |
겉보기 밀도 | 2~6g/cc | 홀 유량계 |
탭 밀도 | 4~8g/cc | ASTM B527 |
유량 | 20~50초/50g | 홀 유량계 |
점화 시 손실 | 1 ~ 10% | 열 중량 분석 |
잔류 탄소 | 최대 0.1% | 연소 적외선 감지 |
잔류 산소 | 최대 1% | 불활성 기체 융합 분석 |
구형 가스 분무 전극 분말은 불규칙한 모양에 비해 흐름과 패킹이 우수하지만 기계적 고정은 감소합니다. 증착 공정에 맞춘 사양 - 와이어, 코팅, 열 스프레이.
전극 분말 응용 분야
전극 분말은 접합, 표면 처리 및 적층 제조 공정 전반에 걸쳐 중요한 기능을 수행합니다:
애플리케이션 | 세부 정보 | 일반적으로 사용되는 파우더 |
---|---|---|
차폐 금속 아크 용접(SMAW) | 수동 스틱 전극 | 루틸, 셀룰로오스, 철 분말, 합금철 |
가스 금속 아크 용접(GMAW) | 연속 솔리드/금속 코어 와이어 피드 | 탄소강, 스테인리스강, 니켈 합금 |
플럭스 코어 아크 용접(FCAW) | 플럭스 코어가 있는 튜브형 소모품 | 합금강, 크롬, 니켈, 망간 |
서브머지드 아크 용접(SAW) | 세분화된 플럭스로 자동화된 와이어 프로세스 | 실리콘, 망간, 크롬, 니켈 |
일렉트로슬래그 용접 | 플럭스 풀이 있는 수직 업 패스 | 크롬, 니켈, 구리, 버논 |
플라즈마 전달 아크(PTA) | 플라즈마 기둥에 공급되는 분말 | 텅스텐 카바이드, 크롬 카바이드, 니오븀 카바이드 |
열 스프레이
연소, 전기 아크 및 플라즈마 스프레이 방식을 통한 코팅 증착을 위한 특수 전극형 분말입니다.
따라서 전극 분말은 산업 환경의 수동, 자동, 고증착, 표면 엔지니어링 용접 및 용사 공정에서 다양하게 사용됩니다.
전극 분말 크기 사양
사이즈 클래스 | 일반적인 범위 | 애플리케이션 |
---|---|---|
추가 벌금 | 10-38 미크론 | 고합금강, 듀플렉스/슈퍼합금 |
괜찮아요 | 38-75 미크론 | 자동화된 GMAW 와이어, SAW 플럭스 |
Medium | 75-150 미크론 | 수동 스모 스틱, FCAW |
거친 | 150-300 미크론 | 고증착 서브머지드 아크 |
국제전기기술위원회 표준 IEC 60544는 치수 공차, 크기 분석 방법론 및 체의 크기를 관리합니다.
화학적 특성 외에도 입자 크기 분포는 아크 안정성, 야금학적 미세 구조, 증착 효율, 속도, 표면 마감 및 성능에 매우 중요합니다.
전극 분말의 분류
구성, 용도 및 관련 표준을 다루는 여러 분류 시스템을 통해 적합한 분말을 식별할 수 있습니다:
표준 | 기초 |
---|---|
AWS A5.0 | 합금 제품군 및 전극 유형 - 연강, 저합금강, 스테인리스강, 표면 처리 등 |
ASME SFA-5.0 | 합금을 유사한 베이스 유형으로 그룹화한 용접 와이어 사양 |
ISO 14172 | 강철 및 니켈 필러 금속의 화학적 조성 범위 |
ISO 17632 | 전선 치수, 차폐, 전류 유형 및 위치 지정하기 |
ISO 13916 | 금속 충전재에 대한 합격 검사 수준 |
CEN EN 758 | 플럭스 코팅 아크 용접 스틱에 대한 요구 사항 정의 |
CEN EN 760 | 플럭스 코어 전선 유형에 대한 사양 |
이러한 분류는 전극 개발, 테스트 및 적용을 조정하여 애플리케이션 요구 사항을 충족하는 반복 가능한 고품질 용접을 생성하는 데 도움이 됩니다.
전극 분말의 비용 분석
파우더 등급 | 가격 범위 | 주요 드라이버 |
---|---|---|
탄소강 및 저합금강 | 1파운드당 $3-6 | 대량 상품 가격, 안정적인 비용 |
스테인리스 스틸 | 1파운드당 $6-12 | 니켈/크롬의 가격 변동성 |
고강도 저합금 | 1파운드당 $15-25 | 코발트와 같은 합금 첨가물의 공급원 |
공구강, 초합금 | 1파운드당 $30-60 | 공급 원료 방법, 엄격한 화학 요구 사항 |
탄화물, 복합재 | $50-150 파운드당 | 기본 분말 합성 경로, 낮은 수요 |
- 고순도 전구체 재료 필요
- 미세 제어 분말의 경우 비용 상승
- 특수한 용도의 틈새 합금은 더 비쌉니다.
- 광범위한 R&D 및 테스트 필요
- 대량 생산으로 인한 규모의 경제
권장 사항
합금 개발 과정에서 파우더 생산업체와 긴밀히 협력하여 애플리케이션의 중요도에 따라 성능과 예산의 균형을 맞출 수 있습니다.
등급 전극 분말
설명 | 일반적인 애플리케이션 | 예제 |
---|---|---|
상품용 일반 탄소강 및 저합금강 | 구조물 제작, 인프라, 운송 | AISI/SAE 1018, 4140 컴포지션 |
일반적인 오스테나이트계 스테인리스강 | 탱크, 프로세스 용기, 해양 하드웨어 | 304L, 316L 등급 |
저온 서비스 강재 | 극저온 보관, 액화 가스 봉쇄 | AWS A5.11을 충족하는 9% 니켈강 |
고속 결합을 위한 솔리드 와이어 | 자동차 조립, 가전제품 | ER70S-6, ER308LSi |
고증착을 위한 금속 코어 와이어 | 구조용 철골 제작, 교량 | EM12K와 같은 AWS 분류 |
경질 합금 | 내마모성 오버레이 | Stoody D Dur 600과 같은 크롬 탄화물 |
내식성 합금 | 화학 처리 장비 | AWS A5.14에 따른 니켈 및 코발트 합금 |
고강도 강재 | 항공우주, 압력 용기, 터빈 | 맞춤형 니켈 및 코발트 초합금 |
탄소강용 대량 상품용 필러 와이어부터 까다로운 환경을 위한 특수 등급까지 다양한 스펙트럼을 제공합니다. 맞춤형 배합으로 고유한 요구 사항을 해결합니다.
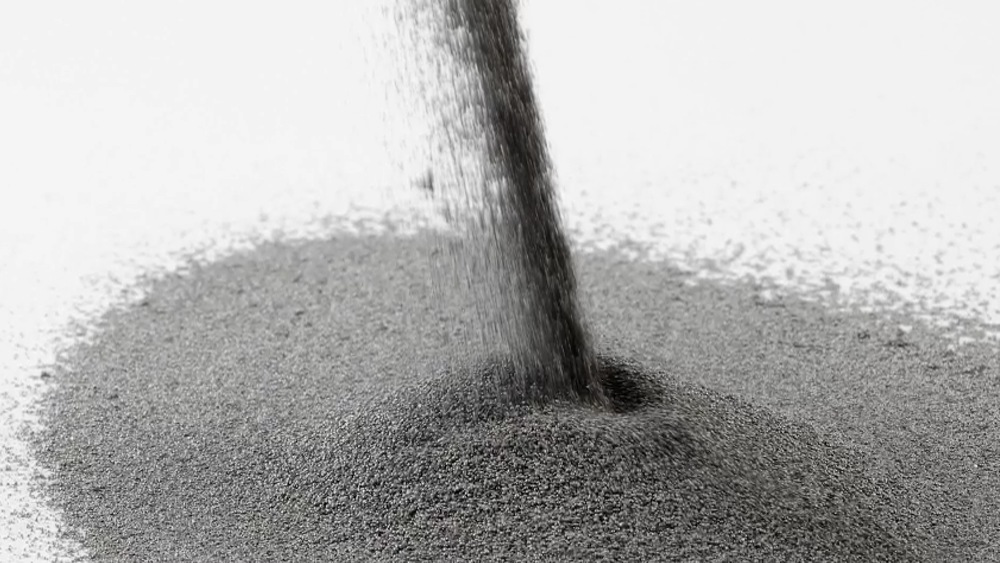
자주 묻는 질문
용접 전극은 어떻게 제조되나요?
전극은 전극 분말이 증착되어 고체 또는 플럭스 코어를 둘러싸는 코팅을 만드는 금속 막대 또는 와이어로 구성됩니다:
- 목표 특성 개발을 위한 맞춤형 전극 분말 조성물
- 분말 혼합, 컨디셔닝 및 막대 부착
- 압출 또는 압축을 통한 코팅 강화
- 사용 전 최종 건조 및 품질 검사
플럭스 성분은 아크 안정성을 촉진하고 합금 원소는 용접 중에 코팅이 녹아 접합부에 재료를 전달할 때 증착된 용접 화학 물질을 풍부하게 합니다.
다양한 용사 파우더에는 어떤 것이 있나요?
보호 코팅, 내마모성 및 내식성을 위한 다양한 용사 기술은 특수한 특성을 가진 전극형 공급 원료 분말을 활용합니다:
- 연소 분말 - 고순도의 철, 니켈, 코발트 합금
- 와이어 아크 스프레이 - 더 굵은 강철 및 스테인리스 와이어
- 플라즈마 스프레이 - 매우 미세하고 구형이며 부드러운 분말
- 고속 산소 연료(HVOF) - 고속에 최적화됨
- 콜드 스프레이 - 연성, 어닐링 및 작업 경화 금속
증착 메커니즘은 입자 크기 분포, 모양 및 미세 구조와 같은 최적의 파우더 특성에 영향을 미칩니다.
올바른 전극을 선택하는 방법은 무엇인가요?
전극 선택의 기준이 되는 요소는 다음과 같습니다:
- 서비스 조건 - 온도, 부식, 충격
- 기본 금속 표준 및 구성
- 필요한 기계적 성능 - 경도, 균열, 연성
- 극저온 또는 고온 사용
- 재료 두께 및 조인트 준비
- 용접 공정 - 스틱, MIG, 서브머지드 아크
- 필수 구조적 무결성 사양 - 응력 파열, 크리프
제조업체와 협력하여 분말 구성, 표준 분류 및 지원 자격 데이터를 통해 소모품 성능을 운영 요구사항에 맞게 조정합니다.
전극 코팅의 다공성 한계는 무엇인가요?
제조 중 가스 포획으로 인한 전극 코팅의 다공성은 공정 불일치 및 완성된 용접의 결함으로 이어집니다. AWS, ASME 및 ISO 표준에 따른 코팅 밀도 요건:
- 최소 95% 이론 밀도
- 10배 확대 시 시각적 다공성 1% 미만
- 이미지 분석에 따른 최대 5% 다공성
최적화된 파우더 블렌드, 강판 표면 처리, 압출 파라미터, 엄격한 품질 관리 점검을 통해 달성합니다.
전극 연기는 어떻게 형성되나요?
아크 용접은 용융 방울의 합금 원소를 기화시켜 흄 형성 메커니즘을 유도합니다:
- 산화물 형성 - 대기 중 산소와의 반응
- 냉각 시 과포화 금속 증기의 핵 생성
- 기체 종의 미세 입자로의 응축
흄의 발생률과 구성은 전극 코팅, 모재, 공정 매개변수, 오염물질의 존재 여부에 따라 달라집니다. 적절한 추출과 개인보호장비 착용이 필수적입니다.
결론
특수 금속 합금, 플럭스 및 복합재의 구성, 분말 특성, 균질화 및 레이어링을 통해 국부적 인챈트와 설계된 용접 인터페이스를 갖춘 맞춤형 야금 구조가 가능합니다. 광범위한 산업 응용 분야와 운영 환경에서 균열, 마모, 피로 및 부식에 견디는 반복 가능한 용접을 달성하려면 원자재부터 완제품까지 엄격한 제어를 유지하는 것이 필수적입니다. 새로운 합금, 스마트 와이어, 센서 및 자동화의 발전은 더욱 정교한 전극 배합을 통해 차세대 용접 공정의 범위와 기능을 지속적으로 확장할 것입니다.