개요
고구형성 파우더 은 거의 완벽한 구형을 갖도록 설계된 특수한 형태의 분말 소재입니다. 이러한 특성은 다양한 산업 분야, 특히 적층 제조(3D 프린팅), 항공우주, 자동차, 전자 및 의료 기기에서 매우 중요합니다. 이러한 분말에서 구형의 중요성은 유동성, 포장 밀도, 심지어 용융 특성까지 일관된 고품질 생산 결과물을 달성하는 데 중요한 역할을 합니다.
이 방대한 가이드에서는 고구면 분말에 대해 알아야 할 모든 것을 살펴봅니다. 구성과 특성 이해부터 다양한 금속 분말 모델 비교까지, 균형 잡힌 상세 자료를 제공하는 것을 목표로 합니다. 재료 엔지니어, 구매 관리자 또는 단순히 고구면 분말의 세계에 대해 궁금해하는 모든 분들을 위한 교육 및 정보 제공을 위해 이 문서를 작성했습니다.
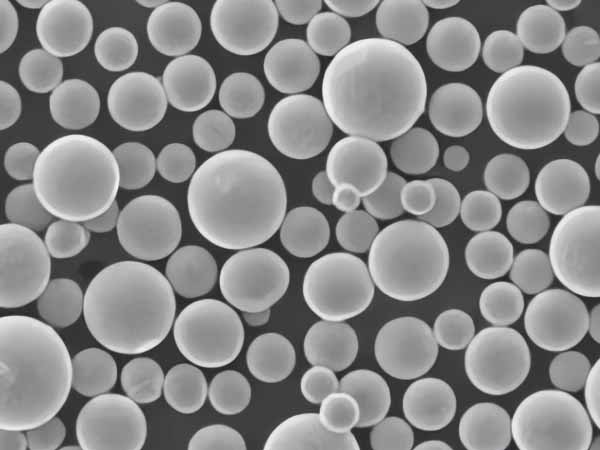
고구형성 분말의 이해
고구면 파우더란 무엇인가요?
고구형 분말은 개별 입자가 거의 완벽한 구형인 분말 재료를 말합니다. 이러한 형태는 가스 분무, 플라즈마 분무 또는 원심 분무와 같은 다양한 제조 공정을 통해 달성됩니다. 이러한 입자의 구형 특성은 높은 유동성과 포장 밀도에 기여하여 특정 고정밀 애플리케이션에 이상적입니다.
구형성이 중요한 이유는 무엇인가요?
불규칙한 모양의 돌을 쌓는 것과 완벽하게 둥근 구슬을 쌓는 것을 상상해 보세요. 구슬은 최소한의 간격으로 깔끔하게 쌓일 것 같죠? 구형도가 높은 분말은 미세한 수준에서 이러한 역할을 합니다. 구형은 더 나은 패킹을 가능하게 하여 용융 또는 소결 공정에서 더 높은 밀도, 향상된 유동성 및 더 일관된 거동을 가능하게 합니다.
고구형성 파우더의 주요 이점
- 향상된 흐름성: 구형 입자는 불규칙한 모양의 입자보다 더 쉽게 흐르기 때문에 분말의 일관된 공급이 중요한 3D 프린팅과 같은 애플리케이션에 이상적입니다.
- 더 높은 포장 밀도: 균일한 모양으로 입자를 더 촘촘하게 포장할 수 있어 밀도가 높아져 최종 제품의 강도가 높아집니다.
- 더 나은 녹는 특성: 구형 분말은 균일하게 녹아 최종 제품의 결함 위험을 줄입니다.
유형 및 구성 고구형성 파우더
고구면 분말은 다양한 금속과 합금으로 만들 수 있으며, 각각 다른 용도에 적합합니다. 아래는 몇 가지 일반적인 유형의 고구면 분말과 그 구성, 특성 및 용도에 대한 자세한 표입니다.
파우더 유형 | 구성 | 속성 | 애플리케이션 |
---|---|---|---|
316L 스테인리스 스틸 | Fe, Cr, Ni, Mo | 높은 내식성, 우수한 기계적 특성 | 의료 기기, 항공우주 부품 |
AlSi10Mg | Al, Si, Mg | 경량, 고강도, 우수한 열적 특성 | 자동차 부품, 항공우주 |
인코넬 718 | Ni, Cr, Fe, Nb, Mo, Ti, Al | 고온 강도, 내식성 | 가스터빈, 항공우주, 원자로 |
Ti-6Al-4V | Ti, Al, V | 높은 중량 대비 강도, 내식성 | 항공우주, 생체의학 임플란트 |
CoCrMo | Co, Cr, Mo | 생체 적합성, 내마모성, 내식성 | 의료용 임플란트, 치과용 애플리케이션 |
구리(Cu) | 퓨어 Cu | 뛰어난 전기 전도성, 열 전도성 | 전기 부품, 열교환기 |
하스텔로이 X | Ni, Cr, Fe, Mo, Co | 산화 저항성, 고온에서의 강도 | 가스터빈, 석유화학 애플리케이션 |
마레이징 스틸(18Ni300) | Fe, Ni, Co, Mo | 초고강도, 우수한 인성 | 툴링, 항공우주, 원자력 애플리케이션 |
니켈 625 | Ni, Cr, Mo, Nb | 우수한 내식성, 고강도 | 해양, 화학 공정, 항공 우주 |
알루미늄 6061 | Al, Mg, Si | 우수한 기계적 특성, 경량 | 항공우주, 자동차, 전자 |
고구형성 분말의 특성
고구면 분말의 특정 특성을 이해하는 것은 용도에 적합한 재료를 선택하는 데 매우 중요합니다. 여기에서는 이러한 분말을 정의하는 핵심 속성에 대해 자세히 살펴봅니다.
1. 입자 크기 분포
입자 크기 분포는 분말 배치의 입자 크기 범위를 나타냅니다. 일반적으로 좁은 크기 분포는 적층 제조와 같이 균일성이 필요한 응용 분야에서는 가공 중에 보다 일관된 동작을 유도하기 때문에 선호됩니다.
- 미세 분말(1-10 µm): 매끄러운 마감과 높은 정밀도가 필요한 애플리케이션에 적합합니다.
- 중간 분말(10-50 µm): 일반적인 3D 프린팅 애플리케이션에 일반적으로 사용되며 유동성과 정밀성 사이의 균형을 제공합니다.
- 굵은 분말(50-150 µm): 제작 속도는 높지만 표면 마감 품질이 낮은 애플리케이션에 적합합니다.
2. 흐름성
유동성은 파우더가 부드럽고 일관되게 흐르는 능력입니다. 이 특성은 균일한 층을 만들기 위해 파우더를 고르게 분산시켜야 하는 3D 프린팅과 같은 공정에서 매우 중요합니다.
- 높은 유동성: 적층 제조에서 일관된 레이어링을 보장하여 결함의 위험을 줄입니다.
- 낮은 유동성: 레이어가 고르지 않아 최종 제품에 결함이 발생할 가능성이 높아질 수 있습니다.
3. 순도
순도는 파우더에 오염 물질이 없는 상태를 말합니다. 특히 의료용 임플란트나 항공우주 부품과 같은 중요한 애플리케이션에서 최종 제품의 무결성을 유지하려면 높은 순도 수준이 필수적입니다.
- 고순도(>99%): 최종 제품이 엄격한 품질 표준을 충족하도록 보장하여 실패 위험을 줄입니다.
- 저순도(<99%): 오염 문제가 발생하여 최종 제품의 성능과 신뢰성에 영향을 미칠 수 있습니다.
4. 밀도
밀도는 최종 제품의 성능에 중요한 역할을 합니다. 일반적으로 고밀도 파우더는 더 강하고 내구성이 뛰어난 부품을 만들기 때문에 선호됩니다.
- 고밀도: 더 강력하고 내구성 있는 제품으로 이어집니다.
- 낮은 밀도: 잠재적인 구조적 문제로 인해 제품이 약해질 수 있습니다.
고구형성 분말의 응용 분야
고구면 분말은 다양한 산업 분야에서 사용되며, 각 산업은 이러한 분말이 제공하는 고유한 특성의 이점을 활용합니다. 아래에서는 고구면 분말의 주요 응용 분야 몇 가지를 살펴봅니다.
산업 | 애플리케이션 | 주요 이점 |
---|---|---|
적층 제조(3D 프린팅) | 프로토타이핑, 복잡한 형상 제작 | 고정밀, 일관된 품질, 향상된 기계적 특성 |
항공우주 | 터빈 블레이드, 구조 부품 | 고강도, 내열성, 경량 소재 |
의료 기기 | 임플란트, 수술 도구 | 생체 적합성, 내식성, 맞춤형 기계적 특성 |
자동차 | 경량 부품, 엔진 부품 | 연비 개선, 배기가스 감소, 고강도 실현 |
전자 제품 | 전도성 부품, 방열판 | 뛰어난 전기 및 열 전도성 |
방어 | 고성능 부품, 갑옷 | 높은 중량 대비 강도, 내구성 |
에너지 | 터빈, 원자로, 연료 전지 | 내식성, 고온 안정성 |
사양, 크기, 등급 및 표준
응용 분야마다 고구면 분말의 사양, 크기, 등급 및 표준이 다릅니다. 아래는 이러한 측면을 요약한 자세한 표입니다.
재질 | 입자 크기(µm) | 등급 | 표준 | 일반적인 용도 |
---|---|---|---|---|
316L 스테인리스 스틸 | 15-45 | A, B | ASTM F3184 | 의료 기기, 항공우주 부품 |
AlSi10Mg | 20-63 | A | ISO 23510 | 자동차 부품, 항공우주 |
인코넬 718 | 15-53 | B, C | AMS 5662 | 가스터빈, 항공우주, 원자로 |
Ti-6Al-4V | 15-45 | A | ASTM F1472 | 항공우주, 생체의학 임플란트 |
CoCrMo | 10-45 | B | ISO 5832-12 | 의료용 임플란트, 치과용 애플리케이션 |
구리(Cu) | 20-60 | A | ASTM B212 | 전기 부품, 열교환기 |
하스텔로이 X | 15-53 | C | AMS 5536 | 가스터빈, 석유화학 애플리케이션 |
마레이징 스틸(18Ni300) | 20-63 | B | AMS 6514 | 툴링, 항공우주, 원자력 애플리케이션 |
니켈 625 | 15-45 | B, C | ASTM B443 | 해양, 화학 공정, 항공 우주 |
알루미늄 6061 | 20-70 | A | ASTM B221 | 항공우주, 자동차, 전자 |
공급업체 및 가격 세부 정보
고구면 분말 시장은 다양하며, 공급업체는 다양한 가격대의 다양한 재료를 제공합니다. 아래는 공급업체, 제공되는 재료 및 가격 세부 정보를 비교한 것입니다.
공급업체 | 재질 | 가격(kg당) | MOQ(최소 주문 수량) | 리드 타임 |
EOS GmbH | 316L 스테인리스 스틸 | $250 | 10kg | 4~6주 |
AP&C(GE 애디티브) | Ti-6Al-4V | $400 | 5kg | 3-4주 |
카펜터 기술 | 인코넬 718 | $300 | 15kg | 6~8주 |
샌드빅 | AlSi10Mg | $200 | 20kg | 5~7주 |
LPW 기술 | CoCrMo | $350 | 10kg | 4~5주 |
GKN 회가나에 | 알루미늄 606 | $150 | 25kg | 3-4주 |
회가나스 | 마레이징 스틸(18Ni300) | $450 | 10kg | 6~8주 |
프렉스에어 표면 기술 | 니켈 625 | $320 | 20kg | 5~6주 |
Tekna | 구리(Cu) | $180 | 30kg | 3~5주 |
올리콘 AM | 하스텔로이 X | $400 | 10kg | 4~6주 |
장점과 단점 고구형성 파우더
구형도가 높은 파우더를 선택할 때는 장단점을 잘 따져봐야 합니다. 아래는 이러한 재료의 장단점을 강조한 비교 표입니다.
장점 | 단점 |
---|---|
높은 유동성: 취급 및 처리가 간편합니다. | 비용: 일반적으로 불규칙한 분말보다 더 비쌉니다. |
일관된 멜팅: 최종 제품의 결함을 줄입니다. | 가용성: 일부 특수 합금의 경우 사용 가능 여부가 제한됩니다. |
높은 포장 밀도: 더 강력하고 내구성 있는 제품으로 이어집니다. | 처리 난이도: 일부 프로세스에는 특수 장비가 필요합니다. |
광범위한 애플리케이션: 산업 전반에 걸쳐 다양하게 활용하세요. | 제한된 사용자 지정: 표준 등급과 크기는 모든 요구 사항에 맞지 않을 수 있습니다. |
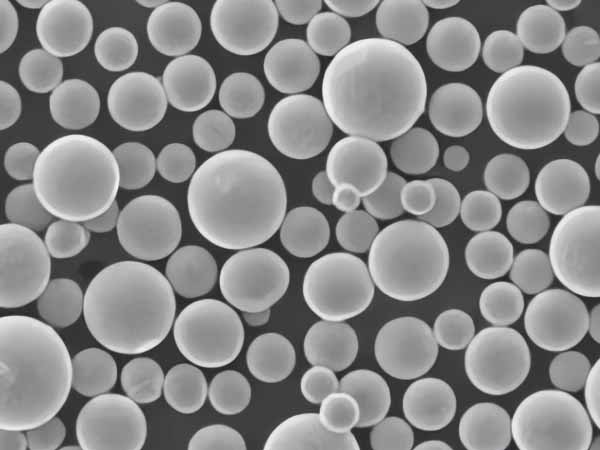
자주 묻는 질문
고구면 분말은 어떤 용도로 사용되나요?
고구형 분말은 주로 적층 제조, 항공우주, 의료 기기 및 기타 높은 정밀도와 일관성을 요구하는 산업에서 사용됩니다. 구형이기 때문에 유동성, 포장 밀도 및 용융 특성이 우수하여 고품질의 결함 없는 제품을 만드는 데 이상적입니다.
파우더의 구형성이 중요한 이유는 무엇인가요?
구형은 분말의 유동성, 포장 밀도, 용융 특성에 영향을 미칩니다. 구형도가 높을수록 가공 중 흐름이 개선되고 패킹 밀도가 높아져 최종 제품의 강도가 향상되며 용융이 일정하게 유지되어 결함이 줄어듭니다.
고구형 분말은 어떻게 만들어지나요?
고구형 분말은 일반적으로 가스 분무, 플라즈마 분무 또는 원심 분무와 같은 공정을 통해 만들어집니다. 이러한 방법은 입자가 거의 완벽한 구형을 이루도록 하며, 이는 다양한 응용 분야에서 파우더의 성능에 매우 중요합니다.
고구면 분말에 사용되는 일반적인 재료는 무엇인가요?
일반적인 재료로는 316L 스테인리스 스틸, Ti-6Al-4V, 인코넬 718, AlSi10Mg, CoCrMo 등이 있습니다. 각 소재는 고유한 특성을 가지고 있으며 애플리케이션의 특정 요구 사항에 따라 선택됩니다.
구형도가 높은 파우더는 비쌉니까?
고구형 분말은 일반적으로 이를 만드는 데 사용되는 특수한 공정과 우수한 특성으로 인해 불규칙한 분말보다 더 비쌉니다. 비용은 재료, 입자 크기 및 공급업체에 따라 달라질 수 있습니다.
구형도가 높은 파우더를 맞춤 제작할 수 있나요?
대부분의 공급업체는 표준 등급과 크기를 제공하지만 사용자 지정이 가능하지만 비용이 더 많이 들고 리드 타임이 길어질 수 있습니다. 사용자 지정 옵션은 공급업체와 특정 소재에 따라 다릅니다.
고구면 분말의 가장 큰 이점은 어떤 산업에 있나요?
항공우주, 의료 기기, 자동차, 전자, 적층 제조 등의 산업에서 가장 큰 혜택을 누릴 수 있습니다. 이러한 산업에서는 고구면 분말이 제공하는 높은 정밀도, 일관성 및 특정 특성을 가진 소재가 필요합니다.
구형도가 높은 파우더의 한계는 무엇인가요?
특수 합금의 경우 높은 비용, 잠재적인 가용성 문제, 특수 가공 장비의 필요성 등의 한계가 있습니다. 또한 표준 등급과 크기가 모든 애플리케이션에 적합하지 않을 수 있으므로 맞춤화가 필요할 수 있습니다.
내 용도에 적합한 고구면 파우더를 선택하려면 어떻게 해야 하나요?
올바른 파우더를 선택하는 것은 필요한 재료 특성, 적용 분야, 예산, 사용 가능한 장비 등의 요인에 따라 달라집니다. 해당 분야의 공급업체 및 전문가와 상담하면 특정 요구 사항에 가장 적합한 제품을 선택하는 데 도움이 될 수 있습니다.
결론
고구형성 분말 는 탁월한 정밀도, 일관성, 성능을 제공하는 현대 제조업의 핵심 구성 요소입니다. 이러한 고유한 특성 덕분에 항공우주, 의료 기기, 적층 제조와 같은 첨단 기술 산업에서 없어서는 안 될 필수 요소입니다. 비용과 가용성이 문제가 될 수 있지만, 특히 품질과 신뢰성이 가장 중요한 애플리케이션의 경우 이러한 단점보다 더 큰 이점을 제공하는 경우가 많습니다.
숙련된 엔지니어든 이제 막 재료 과학의 세계에 발을 들여놓은 초보자이든, 오늘날의 첨단 제조 환경에서는 고구면 분말을 이해하는 것이 매우 중요합니다. 기술이 계속 발전함에 따라 이 놀라운 분말의 응용 분야와 기능도 발전하여 미래의 제조 분야에서 핵심적인 역할을 하게 될 것입니다.