AlSi10Mg 분말은 회색 분말로 항공우주, 자동차, 산업 및 의료 분야의 3D 프린팅 및 적층 제조 응용 분야에 널리 사용됩니다.
레이저 용융 증착 기술은 일종의 레이저 금속 첨가제 제조 기술로, 와이어 공급 또는 분말 공급이 가능합니다. 그 장점은 조밀 한 구조, 미세 입자, 균일 한 구성 및 우수한 성능이며 수리 및 클래딩에도 적용 할 수 있다는 것입니다. 현재 티타늄 합금, 초합금 및 기타 합금에 대한 레이저 용융 증착 연구는 좋은 진전을 이루었지만 알루미늄 합금의 경우 알루미늄 합금의 높은 열전도율, 높은 레이저 반사율로 인해 알루미늄 합금의 레이저 용융 증착 연구는 여전히 매우 제한적입니다.
트루어 R&D 부서는 AlSi10Mg의 선택적 레이저 용융(SLM) 기술에 대한 조사를 수행했으며, 그 결과 SLM AlSi10Mg 부품의 인장 강도는 열처리 후 300MPa, 심지어 406MPa까지 도달할 수 있는 것으로 나타났습니다. 그리고 일부 학자들은 레이저 자원이 AlSi10Mg 증착 부품의 특성에 큰 영향을 미친다는 사실을 발견했습니다.
이 연구에서 트루어가 생산한 AlSi10Mg 분말의 화학적 조성 및 입자 크기(45-105um)는 표 1에 나와 있습니다. 그리고 그 SEM 사진은 그림 1에 나와 있습니다.
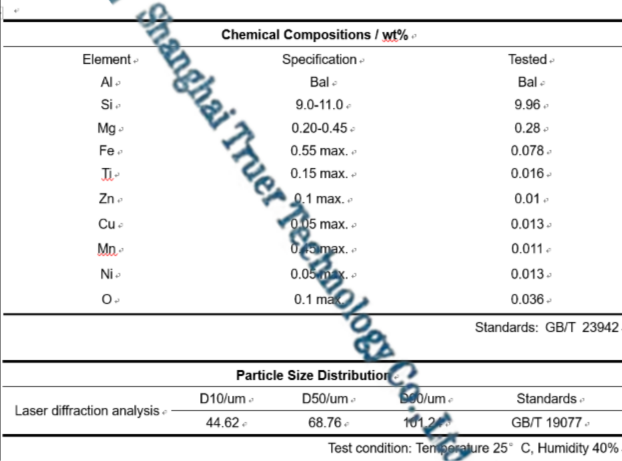
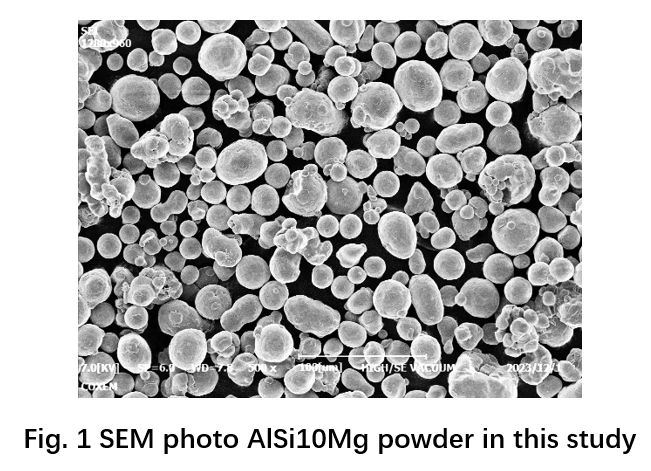
이 실험에 사용된 레이저 용융 증착 시스템은 IPG 파이버 레이저, GTV 분말 공급기, 아르곤 충전 챔버입니다. 레이저 용융 및 증착 과정에서 초점 스폿은 5mm이고 디 포커싱 스폿의 직경은 약 0.6mm입니다. 테스트 레이저 분말은 920W, 스캐닝 방향은 단방향, 스캐닝 속도는 1.2m / 분, 분말 공급 속도는 3.6g / 분, 각 층의 증착 높이는 0.42mm였습니다. 두께 2mm의 단일 벽 샘플을 준비했습니다. 그런 다음 부품의 다공성 및 기계적 특성을 분석했습니다.
그림 2는 기계적 특성 테스트를 위한 시편의 치수입니다.
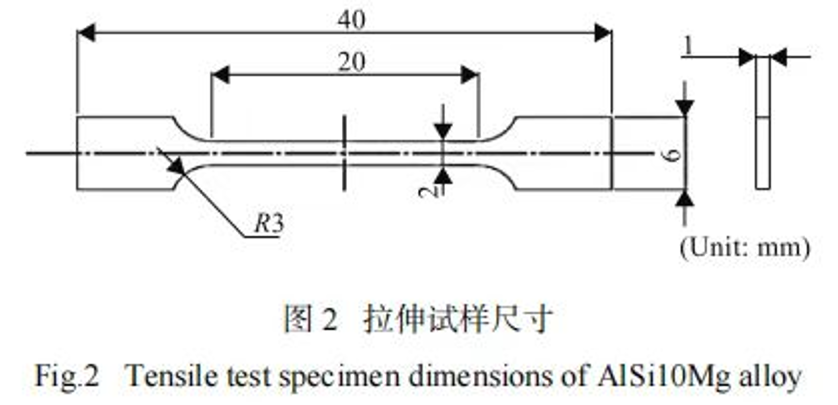
시편의 밀도는 아르키메데스 방법 2.66g/cm3으로 테스트한 결과, 주조된 AlSi10Mg 합금의 밀도는 2.68g/cm3이며, 주물의 99.3%에 비해 상대적으로 높습니다.
이 테스트에서는 아르곤으로 채워진 챔버에 일정량의 산소 함량이 관여했습니다. 따라서 미세 구조는 그림 3에 표시된 일부 다공성을 보여주었습니다.
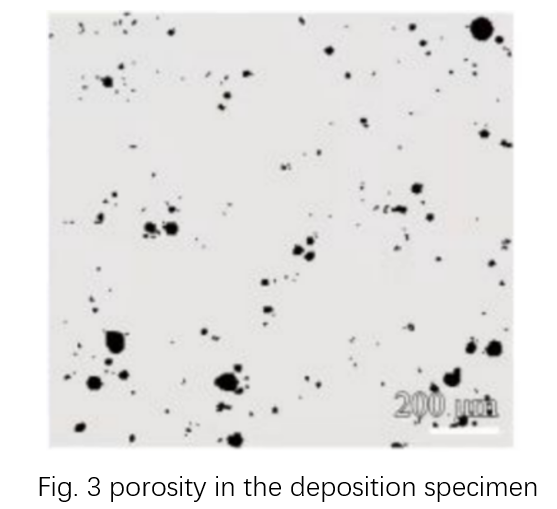
인장 시험에서 그림 4와 같이 인장 곡선을 얻었습니다. 인장 강도는 248MPa, 연신율은 6.2%입니다.
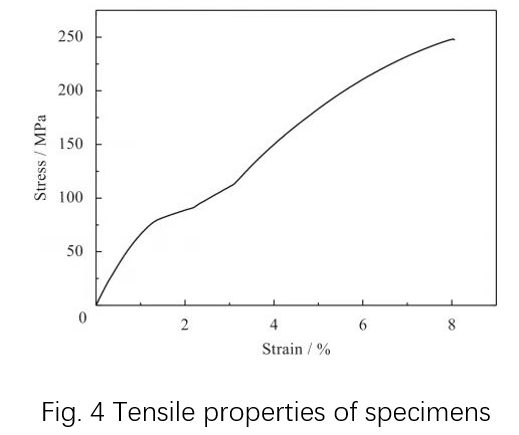
인장 시편의 파괴 형태는 그림 5에 나와 있습니다. 균열 전파는 다공성과 다공성 사이의 얇은 벽을 따라 확장되는 경향이 있음을 알 수 있습니다.
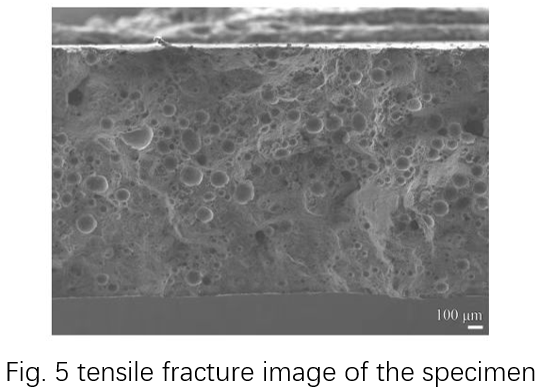
따라서 알루미늄 합금의 레이저 용융 증착 적층 제조는 내부 기공 제어를 보장하기 위해 아르곤으로 채워진 챔버 환경에서 수행하여 AlSi10Mg의 증착 부품의 인장 강도를 더 잘 향상시키는 것이 좋습니다.
일부 학자들은 AlSi10Mg 증착 부품의 높은 기계적 특성의 주된 이유는 증착 상태에서 매우 미세한 알파 Al 이차 수상 돌기가 형성되기 때문이라고 결론지었습니다.
챔버의 산소 함량을 엄격하게 제어하는 것이 AlSi10Mg 레이저 용융 증착 적층 제조 부품의 기계적 특성을 개선하는 열쇠라는 결론을 내릴 수 있습니다.