Overview of Powder for Large Format Printing
Large format printing is a game-changer in the world of industrial printing, enabling the creation of high-quality images, text, and designs on a grand scale. But did you know that the powder used in large format printing plays a critical role in the quality, durability, and efficiency of the final product? This guide will delve into the specifics of powder for large format printing, covering everything from the types of powders available, their compositions, and properties, to their applications, advantages, and limitations.
Whether you’re an engineer, a printer, or just curious about the intricacies of large format printing, this article will provide you with all the insights you need to understand how the right powder can make all the difference in your printing projects.
Types of Powder for Large Format Printing
Different types of powders are used in large format printing depending on the desired outcome. Let’s explore the most commonly used powders and their characteristics.
Powder Type | Composition | Properties | Applications | Advantages | Limitations |
---|---|---|---|---|---|
Aluminum Powder | Aluminum particles | Lightweight, durable | Aerospace components, automotive parts | High strength-to-weight ratio | Can oxidize if not properly coated |
Copper Powder | Copper particles | Conductive, corrosion-resistant | Electrical components, heat exchangers | Excellent thermal conductivity | Expensive compared to other metals |
Stainless Steel Powder | Iron, chromium, nickel | Corrosion-resistant, strong | Medical devices, food processing equipment | Highly durable, resistant to rust | Heavy, can be costly |
Titanium Powder | Titanium particles | High strength, lightweight | Medical implants, aerospace parts | Biocompatible, strong, lightweight | High cost of raw material |
Nickel Powder | Nickel particles | Strong, corrosion-resistant | Turbine blades, batteries | Excellent mechanical properties | Can be difficult to process |
Zinc Powder | Zinc particles | Low melting point, durable | Galvanizing, batteries | Effective in corrosion prevention | Limited mechanical strength |
Iron Powder | Iron particles | Strong, magnetic properties | Automotive parts, machinery components | Cost-effective, readily available | Prone to rust if not treated |
Bronze Powder | Copper, tin | Durable, corrosion-resistant | Sculptures, decorative items | Aesthetic appeal, strong | Higher cost due to copper content |
Cobalt-Chromium Powder | Cobalt, chromium | Wear-resistant, biocompatible | Dental implants, turbine engines | Excellent for high-stress applications | Expensive, challenging to process |
Magnesium Powder | Magnesium particles | Lightweight, strong | Automotive, aerospace applications | High strength-to-weight ratio | Flammable in powder form |
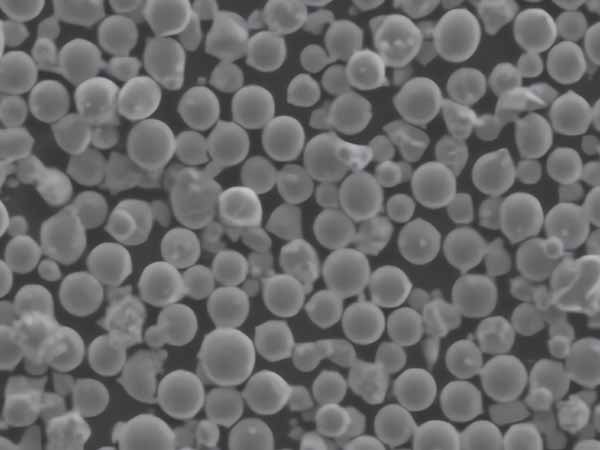
Composition of Powder for Large Format Printing
The composition of powder used in large format printing determines its suitability for various applications. Each powder type consists of a base metal or alloy, which is chosen based on the required mechanical, thermal, and electrical properties.
Powder Type | Primary Element | Alloying Elements | Composition Details |
---|---|---|---|
Aluminum Powder | Aluminum | Silicon, copper, magnesium | Often alloyed to enhance strength, conductivity, or corrosion resistance |
Copper Powder | Copper | Zinc, tin | Brass (copper-zinc), bronze (copper-tin) for various mechanical properties |
Stainless Steel Powder | Iron | Chromium, nickel, molybdenum | Specific grades vary based on the application, such as 304, 316, etc. |
Titanium Powder | Titanium | Aluminum, vanadium | Common alloy is Ti-6Al-4V, known for high strength and lightweight |
Nickel Powder | Nickel | Chromium, molybdenum | Often used in high-performance alloys like Inconel |
Zinc Powder | Zinc | Aluminum, copper | May include minor alloying elements to enhance properties for galvanizing |
Iron Powder | Iron | Carbon, manganese | Low-carbon and high-carbon varieties available, sometimes alloyed |
Bronze Powder | Copper | Tin | Proportion of tin affects hardness and wear resistance |
Cobalt-Chromium Powder | Cobalt | Chromium, tungsten | Cobalt-chromium-tungsten alloys are highly wear-resistant and biocompatible |
Magnesium Powder | Magnesium | Aluminum, zinc | AZ31B is a common alloy used for its combination of strength and formability |
Characteristics of Powder for Large Format Printing
Understanding the characteristics of the powder used in large format printing is crucial in selecting the right material for the job. Below are the key characteristics that define the performance of different powders.
Characteristic | Description | Relevance to Printing |
---|---|---|
Particle Size | Refers to the size of individual powder particles | Affects the smoothness and resolution of the print |
Flowability | How easily the powder flows and spreads | Important for even distribution during printing |
Sphericity | The roundness of powder particles | Higher sphericity improves flowability and packing density |
Purity | The absence of contaminants or unwanted elements | High purity ensures consistent and predictable printing outcomes |
Density | Mass per unit volume of the powder | Affects the strength and weight of the final printed object |
Moisture Content | Amount of water present in the powder | Low moisture content is necessary to prevent clumping and ensure smooth printing |
Oxidation Resistance | Ability to resist oxidation when exposed to air | Crucial for maintaining the integrity of the powder during storage and printing |
Thermal Conductivity | How well the powder conducts heat | Affects the cooling and solidification process during printing |
Electrical Conductivity | Ability to conduct electricity | Important for applications requiring electrical connectivity |
Corrosion Resistance | Ability to resist corrosion from environmental factors | Essential for durability in harsh conditions |
Particle Size Distribution in Powder for Large Format Printing
The size distribution of particles in powder affects everything from the final texture of the print to the precision of the details. A powder with uniform particle size distribution ensures consistent quality across the print.
Particle Size Range | Typical Application | Advantages |
---|---|---|
<10 µm | Fine details, smooth surfaces | High resolution, better surface finish |
10-50 µm | General-purpose printing | Balanced between resolution and flowability |
50-100 µm | Structural components with less detail | Higher deposition rates, suitable for larger parts |
>100 µm | Coarse textures, bulk printing | Faster printing, less clogging of nozzles |
Applications of Powder for Large Format Printing
Powder for large format printing is used across various industries, each requiring specific properties from the powder. Below are the primary applications.
Industry | Application | Preferred Powder Type | Reason for Preference |
---|---|---|---|
Aerospace | Jet engine parts, structural components | Titanium, aluminum | Lightweight, high strength |
Automotive | Engine parts, exhaust components | Stainless steel, aluminum | Corrosion-resistant, durable |
Medical | Implants, prosthetics | Titanium, cobalt-chromium | Biocompatible, strong |
Electronics | Circuit boards, connectors | Copper, silver | High electrical conductivity |
Construction | Architectural models, structural parts | Iron, steel | Cost-effective, strong |
Energy | Turbine blades, battery components | Nickel, cobalt | High-temperature resistance, durability |
Art and Design | Sculptures, decorative elements | Bronze, stainless steel | Aesthetic appeal, durability |
Food Processing | Equipment, utensils | Stainless steel | Non-reactive, corrosion-resistant |
Marine | Boat components, underwater structures | Aluminum, stainless steel | Corrosion-resistant, lightweight |
Defense | Armored vehicles, weapons parts | Titanium, steel | High strength, impact-resistant |
Specifications, Sizes, Grades, and Standards for Powder for Large Format Printing
When choosing powder for large format printing, it’s essential to consider the specifications, sizes, and grades that meet the standards of your application.
Powder Type | Size Range | Common Grades | Relevant Standards |
Aluminum Powder | 10-100 µm | 6061, 7075 | ASTM B928, AMS 4068 |
Copper Powder | 10-50 µm | C10100, C11000 | ASTM B170, ASTM B187 |
Stainless Steel Powder | 15-100 µm | 304L, 316L | ASTM A276, ASTM F138 |
Titanium Powder | 15-50 µm | Ti-6Al-4V | ASTM F2924, AMS 4998 |
Nickel Powder | 20-80 µm | Inconel 625, 718 | ASTM B443, AMS 5666 |
Zinc Powder | 10-60 µm | Zn99.9, ZnCu | ASTM B846, ISO 14977 |
Iron Powder | 20-100 µm | Fe-C, Fe-Si | ASTM A848, ASTM B783 |
Bronze Powder | 10-50 µm | CuSn10, CuSn12 | ASTM B427, EN 1982 |
Cobalt-Chromium Powder | 20-70 µm | CoCrMo | ASTM F75, ISO 5832-4 |
Magnesium Powder | 10-60 µm | AZ31B | ASTM B107, AMS 4377 |
Suppliers and Pricing of Powder for Large Format Printing
The cost of powder can vary based on the type, quality, and supplier. Below is an overview of common suppliers and pricing ranges.
Supplier | Powder Type | Price Range (per kg) | Location | Notable Features |
---|---|---|---|---|
Höganäs | Iron, stainless steel | $15 – $50 | Sweden | High-quality metal powders, wide range of alloys |
Carpenter Additive | Titanium, nickel | $100 – $500 | USA | Specialized in high-performance powders |
GKN Additive | Aluminum, magnesium | $50 – $150 | Germany | Focus on lightweight materials for aerospace |
LPW Technology | Aluminum, stainless steel | $50 – $200 | UK | Offers traceability and consistency in powder quality |
Sandvik | Cobalt-chromium, titanium | $150 – $600 | Sweden | Known for high-purity, specialized alloys |
AMG Advanced Metallurgical Group | Iron, copper | $20 – $100 | Netherlands | Offers a wide variety of powders for different industries |
Praxair Surface Technologies | Nickel, aluminum | $75 – $300 | USA | High-quality powders with extensive R&D |
Valimet | Aluminum, zinc | $25 – $120 | USA | Focus on spherical powders for enhanced flowability |
Kennametal | Tungsten, cobalt-chromium | $200 – $800 | USA | Known for hard materials and wear-resistant powders |
VDM Metals | Nickel, cobalt | $150 – $700 | Germany | Specializes in high-performance, corrosion-resistant powders |
Comparing the Pros and Cons of Different Powders for Large Format Printing
Selecting the right powder involves weighing the pros and cons of each type. Here’s a comparison to help you make an informed decision.
Powder Type | Pros | Cons |
---|---|---|
Aluminum Powder | Lightweight, corrosion-resistant | Prone to oxidation, lower melting point |
Copper Powder | Excellent conductivity, corrosion-resistant | Expensive, heavier than aluminum |
Stainless Steel Powder | Strong, corrosion-resistant | Heavy, can be difficult to work with |
Titanium Powder | High strength-to-weight ratio, biocompatible | Very expensive, complex processing requirements |
Nickel Powder | High-temperature resistance, strong | Difficult to process, costly |
Zinc Powder | Cost-effective, good for galvanizing | Limited strength, lower melting point |
Iron Powder | Cost-effective, magnetic properties | Prone to rust, requires treatment for durability |
Bronze Powder | Aesthetic appeal, durable | Higher cost due to copper content |
Cobalt-Chromium Powder | Wear-resistant, biocompatible | Expensive, challenging to process |
Magnesium Powder | Extremely lightweight, strong | Highly flammable in powder form, expensive |
Advantages of Powder for Large Format Printing
Using powder in large format printing offers several advantages, making it a preferred choice for many industries.
Precision and Detail
Powder-based printing allows for extremely fine details and smooth surfaces, which is critical for applications like aerospace components and medical implants.
Material Efficiency
Powder printing reduces waste, as the unused powder can often be recycled for future prints, making it a cost-effective solution over time.
Customization
With powder printing, you can easily adjust the material properties by mixing different powders or changing the printing parameters, allowing for custom-tailored parts.
Speed
Large format powder printing can be faster than traditional manufacturing methods, especially for complex parts that would require multiple steps in conventional processes.
Limitations of Powder for Large Format Printing
While powder for large format printing has many advantages, there are also some limitations to consider.
Cost
High-quality powders, especially those made from rare or complex alloys like titanium or cobalt-chromium, can be expensive, which might limit their use to high-value applications.
Complexity of Processing
Handling and processing powder for large format printing require specialized equipment and expertise, which can add to the overall cost and complexity of production.
Safety Concerns
Some powders, particularly those made from magnesium or other reactive metals, can be hazardous if not handled properly, requiring strict safety protocols.
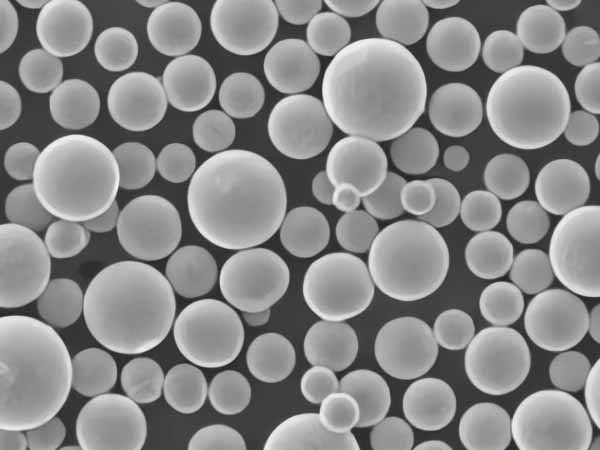
Comparison of Powder for Large Format Printing: Performance and Applications
To help you decide which powder is best suited for your specific needs, here’s a performance and application comparison.
Powder Type | Strength | Best For | Not Suitable For |
---|---|---|---|
Aluminum Powder | High strength-to-weight | Aerospace, automotive parts | Applications requiring very high temperature |
Copper Powder | Excellent conductivity | Electrical components, heat exchangers | Weight-sensitive applications |
Stainless Steel Powder | Corrosion-resistant, strong | Medical devices, food processing equipment | Lightweight or ultra-fine detail applications |
Titanium Powder | High strength, lightweight | Medical implants, aerospace parts | Budget-sensitive projects |
Nickel Powder | Strong, corrosion-resistant | Turbine blades, high-temperature applications | Lightweight applications |
Zinc Powder | Low melting point | Galvanizing, batteries | High-stress or high-temperature applications |
Iron Powder | Strong, magnetic properties | Automotive parts, machinery components | Corrosion-sensitive environments |
Bronze Powder | Durable, aesthetic | Sculptures, decorative items | Cost-sensitive applications |
Cobalt-Chromium Powder | Wear-resistant, biocompatible | Dental implants, turbine engines | Lightweight or low-cost applications |
Magnesium Powder | Lightweight, strong | Automotive, aerospace applications | High-temperature applications |
FAQ
Question | Answer |
---|---|
Which powder is most commonly used in large format printing? | Aluminum powder is widely used due to its balance of strength, lightweight properties, and cost-effectiveness. |
Can I reuse the powder that wasn’t fused during the printing process? | Yes, unused powder can often be recycled for future prints, depending on the material and specific process used. |
Is powder-based printing safe? | With proper handling and safety protocols, powder-based printing is safe, but certain powders (like magnesium) can pose risks. |
How do I choose the right powder for my application? | Consider factors like the strength, weight, corrosion resistance, and thermal properties required for your specific application. |
What are the main benefits of using powder in large format printing? | Powder printing allows for high precision, material efficiency, customization, and faster production times. |
Is it possible to mix powders to create custom materials? | Yes, mixing different powders is a common practice to achieve specific material properties tailored to unique applications. |
How does particle size affect the quality of the print? | Smaller particle sizes can produce finer details and smoother surfaces, while larger particles may be better for structural strength. |