AlSi10Mg powder is gray powder and is widely used in the application of 3D printing and Additive Manufacturing in the field of aerospace, automotive, industrial & medical.
Laser melting deposition technology is a kind of laser metal additive manufacturing technology, which can be wire feeding or powder feeding. Its advantage is that dense structure, fine grains, uniform composition and excellent performance, and also be applied to repair and cladding. At present, the research of laser melting deposition on titanium alloys, superalloys and other alloys had made good progress, but on aluminium alloys, the research of laser melting deposition of aluminium alloys is still very limited because of high thermal conductivity, high laser reflectance of aluminium alloys.
Truer R & D department did some investigation on selected laser melting (SLM) technology of AlSi10Mg, and the results showed its tensile strength of SLM AlSi10Mg parts can reach 300MPa, even as high as 406MPa after heat treatment. And some scholars found the laser resource has a great influence on the properties of AlSi10Mg deposited parts.
The chemical composition & particle size (45-105um) of AlSi10Mg powder produced by Truer in this study is shown in Table 1. And its SEM photo is shown in Fig. 1.
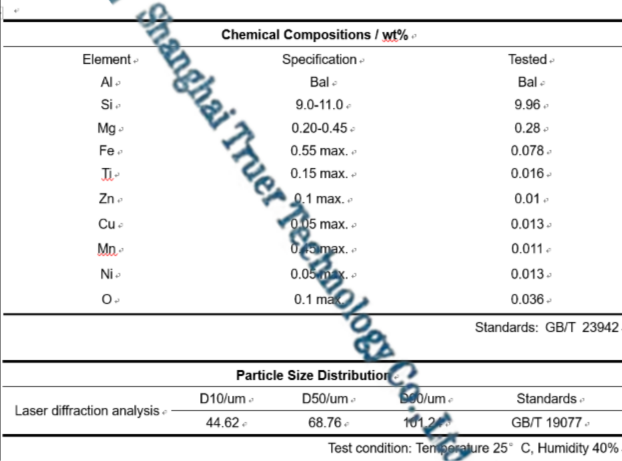
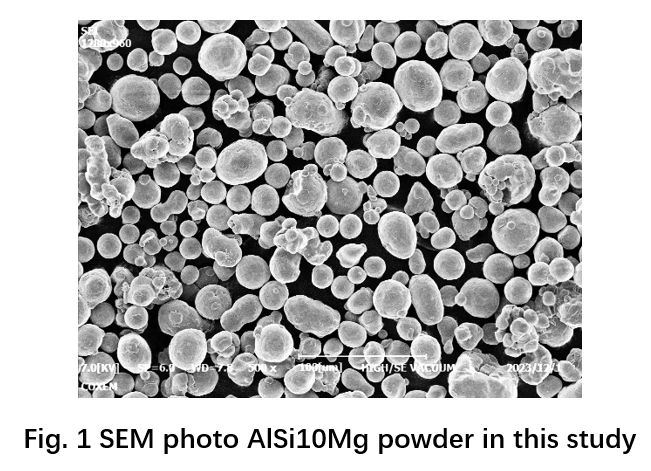
The laser melting deposition system used in this experiment is IPG fiber laser, GTV powder feeder, argon filling chamber. In the process of laser melting and deposition, the focused spot is 5mm and the diameter of the defocusing spot is about 0.6mm. The test laser powder was 920W, the scanning direction was unidirectional, the scanning speed was 1.2m/min, the powder feeding speed was 3.6g/min, and the deposition height of each layer was 0.42mm. A single wall sample with a thickness of 2mm was prepared. And then the porosity and mechanical properties of parts were analyzed.
Fig. 2 is the dimension of the specimen for mechanical properties test.
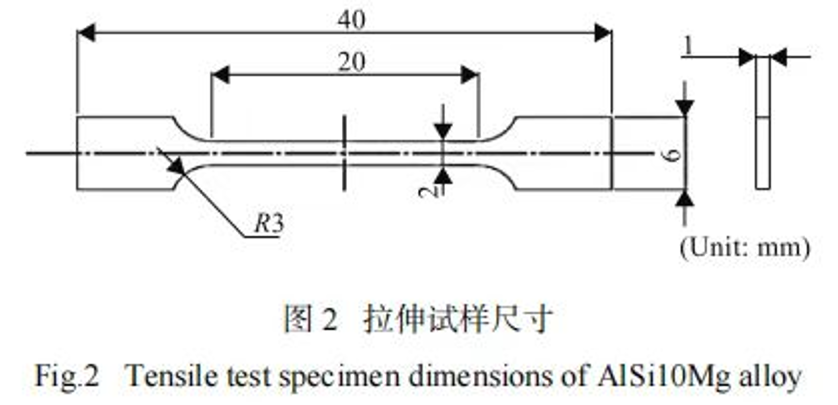
The density of the specimen is tested by Archimedean method 2.66g/cm3, while the density of the as-cast AlSi10Mg alloy is 2.68g/cm3, and relative to 99.3% of the casting.
In this test, a certain amount of oxygen content in the argon filled chamber involved in. So it microstructure showed some porosity showed in Fig. 3.
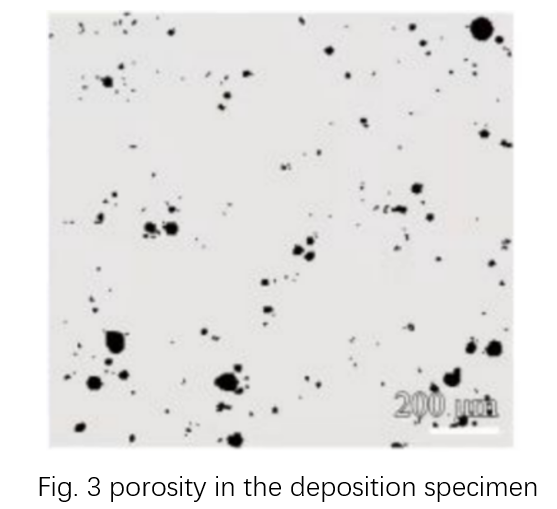
In the tensile test, the tensile curve was obtained as shown in Fig. 4. Tensile strength is 248MPa and elongation 6.2%.
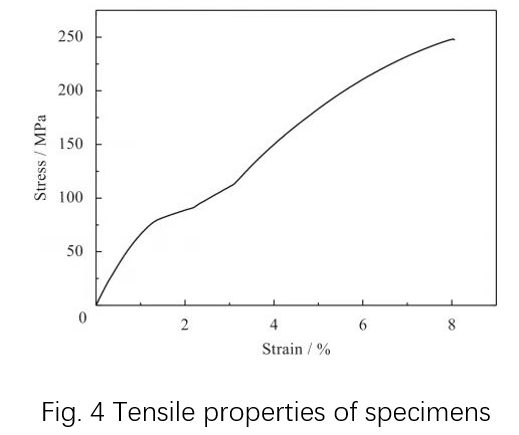
The fracture morphology of the tensile specimen is shown in Fig. 5. It can be seen that the crack propagation tends to expand along the thin wall between the porosity and the porosity.
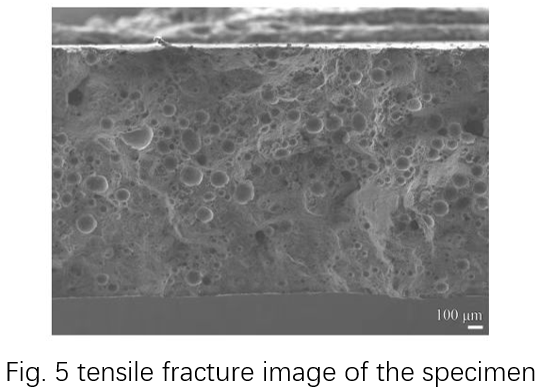
Therefore, the laser melting deposition additive manufacturing of aluminium alloy is recommended to be carried out in an argon-filled chamber environment to ensure the control of internal pore, which better improve tensile strength of deposition parts of AlSi10Mg.
Some scholars concluded the main reason for the high mechanical properties of AlSi10Mg deposition parts is that very fine Alpha Al secondary dendrites formed in the deposition state.
It can be concluded that strict control of oxygen content in the chamber is the key to improve the mechanical properties of AlSi10Mg laser melting deposition additive manufacturing parts.