Low alloy powder is a crucial material in the manufacturing and metallurgy industries. Its unique properties and versatile applications make it indispensable for various industrial processes. In this comprehensive guide, we will explore everything there is to know about low alloy powder, including its composition, characteristics, types, applications, and more. We will also delve into specific metal powder models, providing detailed descriptions and comparisons to help you make informed decisions. Let’s dive in!
Overview of Low Alloy Powder
Low alloy powder consists of metal powders that contain alloying elements in small quantities, usually less than 5%. These alloying elements can include chromium, molybdenum, nickel, vanadium, and more. The primary purpose of these elements is to enhance the mechanical properties, corrosion resistance, and other desirable attributes of the base metal. Low alloy powders are widely used in industries such as aerospace, automotive, and tool manufacturing.
Composition of Low Alloy Powder
Understanding the composition of low alloy powder is essential for selecting the right material for specific applications. Here is a table summarizing the typical composition of various low alloy powders:
Alloy Type | Base Metal | Alloying Elements | Percentage Composition (%) |
---|---|---|---|
4140 | Iron | Chromium, Molybdenum | Cr: 0.80-1.10, Mo: 0.15-0.25 |
4340 | Iron | Nickel, Chromium, Molybdenum | Ni: 1.65-2.00, Cr: 0.70-0.90, Mo: 0.20-0.30 |
8630 | Iron | Nickel, Chromium, Molybdenum | Ni: 0.40-0.70, Cr: 0.40-0.60, Mo: 0.15-0.25 |
9310 | Iron | Nickel, Chromium, Molybdenum | Ni: 3.00-3.50, Cr: 1.00-1.40, Mo: 0.08-0.15 |
18Ni300 | Iron | Nickel, Molybdenum | Ni: 18.00, Mo: 0.50 |
Maraging 250 | Iron | Nickel, Cobalt, Molybdenum | Ni: 18.00, Co: 8.50, Mo: 4.80 |
Maraging 300 | Iron | Nickel, Cobalt, Molybdenum | Ni: 18.00, Co: 9.00, Mo: 5.00 |
Fe-Mo | Iron | Molybdenum | Mo: 2.00-4.00 |
Fe-Cr | Iron | Chromium | Cr: 2.00-4.00 |
42CrMo4 | Iron | Chromium, Molybdenum | Cr: 0.90-1.20, Mo: 0.15-0.30 |
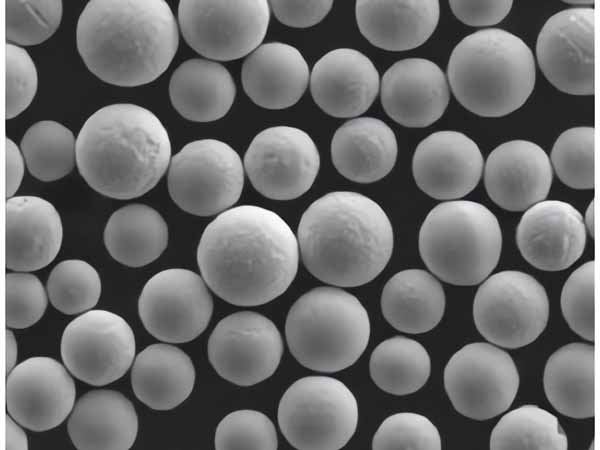
Characteristics of Low Alloy Powder
Low alloy powders offer a range of characteristics that make them suitable for various applications. These characteristics include:
- High Strength: The addition of alloying elements enhances the strength of the base metal.
- Improved Hardness: Low alloy powders exhibit higher hardness levels compared to pure metals.
- Corrosion Resistance: Alloying elements like chromium and nickel improve corrosion resistance.
- Wear Resistance: These powders are highly resistant to wear and abrasion.
- Toughness: Low alloy powders maintain toughness, making them suitable for dynamic and impact-loaded applications.
- Machinability: They offer good machinability, allowing for ease of fabrication and manufacturing.
Types of Low Alloy Powder
When it comes to low alloy powders, there are several specific models to consider. Here are ten popular low alloy powder models, along with their descriptions:
1. 4140 Low Alloy Powder
Description: 4140 is a versatile low alloy powder known for its high strength, hardness, and toughness. It contains chromium and molybdenum as the primary alloying elements. This powder is often used in the automotive and aerospace industries for components requiring high fatigue strength and wear resistance.
2. 4340 Low Alloy Powder
Description: 4340 powder is renowned for its exceptional toughness and fatigue resistance. With nickel, chromium, and molybdenum as alloying elements, it is commonly used in the production of gears, shafts, and other high-stress components in the aerospace and defense sectors.
3. 8630 Low Alloy Powder
Description: 8630 powder offers a good balance of strength and toughness, making it suitable for applications like drilling tools and oilfield equipment. Its composition includes nickel, chromium, and molybdenum, enhancing its hardenability and wear resistance.
4. 9310 Low Alloy Powder
Description: 9310 powder is a high-strength, low alloy material that contains nickel, chromium, and molybdenum. It is widely used in the manufacture of gears, pinions, and other components requiring excellent toughness and fatigue strength.
5. 18Ni300 Low Alloy Powder
Description: 18Ni300 is a maraging steel powder known for its ultra-high strength and toughness. It contains nickel and molybdenum as the primary alloying elements. This powder is used in high-performance applications like aerospace components and tooling.
6. Maraging 250 Low Alloy Powder
Description: Maraging 250 powder is a high-strength maraging steel with nickel, cobalt, and molybdenum. It is used in applications requiring high strength and toughness, such as rocket motor cases and tooling.
7. Maraging 300 Low Alloy Powder
Description: Maraging 300 is another high-strength maraging steel powder. It contains nickel, cobalt, and molybdenum, providing excellent mechanical properties. This powder is used in critical applications like aerospace and defense components.
8. Fe-Mo Low Alloy Powder
Description: Fe-Mo powder consists of iron and molybdenum, offering enhanced strength and hardness. It is used in applications requiring high wear resistance, such as cutting tools and dies.
9. Fe-Cr Low Alloy Powder
Description: Fe-Cr powder is composed of iron and chromium, providing excellent corrosion resistance and strength. It is used in the production of stainless steel components and other applications where corrosion resistance is crucial.
10. 42CrMo4 Low Alloy Powder
Description: 42CrMo4 powder is known for its high strength, toughness, and good hardenability. It contains chromium and molybdenum as alloying elements and is used in the manufacturing of shafts, gears, and other high-stress components.
Applications of Low Alloy Powder
Low alloy powders find applications across various industries due to their unique properties. Here’s a table summarizing the key applications:
Industry | Applications |
---|---|
Automotive | Engine components, gears, shafts, fasteners |
Aerospace | Structural components, landing gear, fasteners |
Tool Manufacturing | Cutting tools, dies, molds |
Oil & Gas | Drilling tools, valves, pumps |
Defense | Weapon components, armor |
Industrial Machinery | Bearings, gears, hydraulic components |
Medical Devices | Surgical instruments, orthopedic implants |
Specifications, Sizes, Grades, and Standards
When selecting low alloy powder, it’s essential to consider specifications, sizes, grades, and standards. Here’s a table to help you understand these parameters:
Alloy Type | Specifications | Sizes | Grades | Standards |
---|---|---|---|---|
4140 | ASTM A29 | Various | 4140 | ASTM, SAE |
4340 | ASTM A322 | Various | 4340 | ASTM, SAE, AMS |
8630 | ASTM A519 | Various | 8630 | ASTM, SAE |
9310 | AMS 6265 | Various | 9310 | AMS, MIL-SPEC |
18Ni300 | AMS 6520 | Various | 18Ni300 | AMS, MIL-SPEC |
Maraging 250 | AMS 6512 | Various | Maraging 250 | AMS, MIL-SPEC |
Maraging 300 | AMS 6522 | Various | Maraging 300 | AMS, MIL-SPEC |
Fe-Mo | Custom | Various | Fe-Mo | Custom |
Fe-Cr | Custom | Various | Fe-Cr | Custom |
42CrMo4 | DIN EN 10083-3 | Various | 42CrMo4 | DIN, EN |
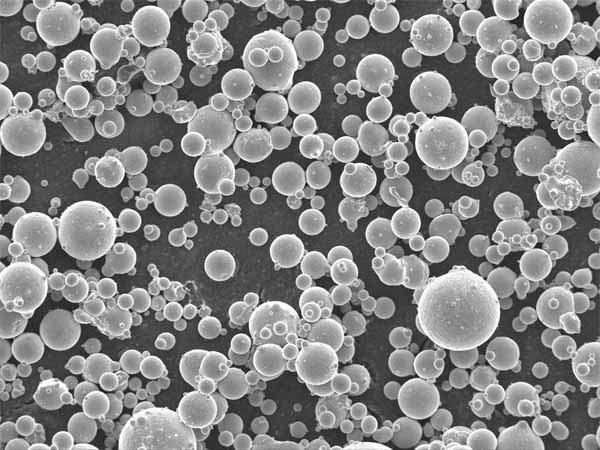
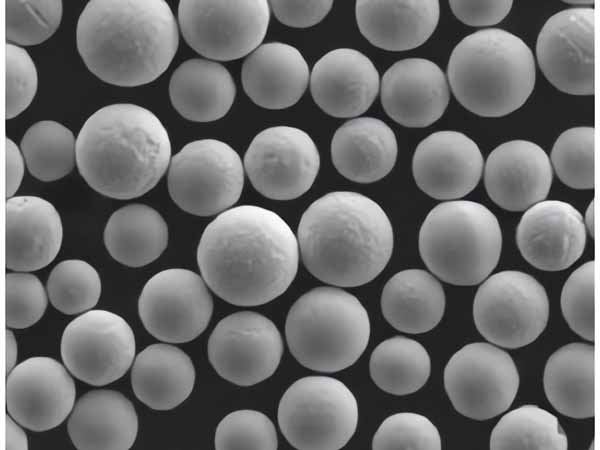
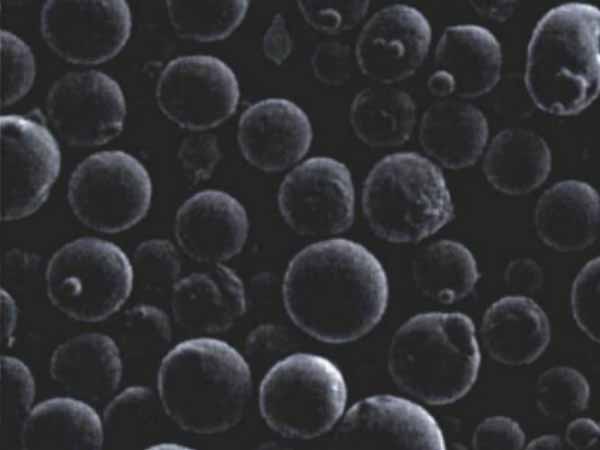
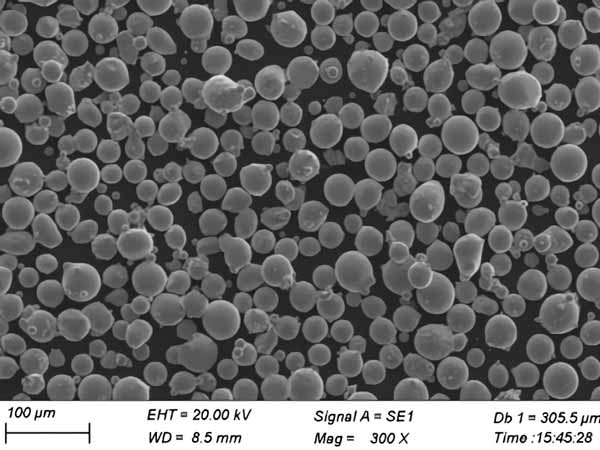
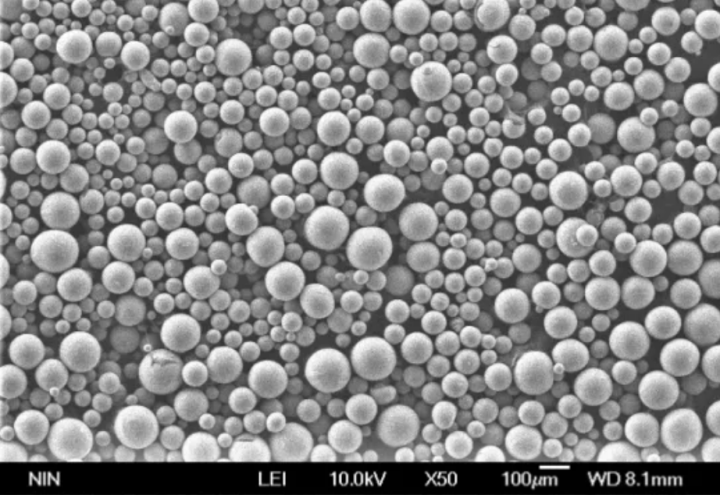
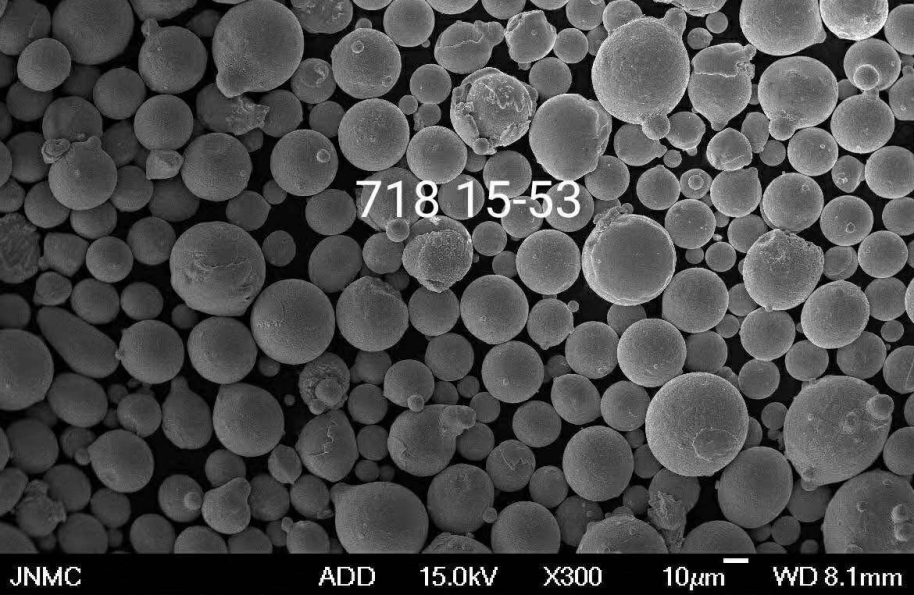
Suppliers and Pricing Details
Here’s a table to help you identify suppliers and pricing details for various low alloy powders:
Alloy Type | Supplier | Pricing ($/kg) |
---|---|---|
4140 | Carpenter Technology | $10 – $15 |
4340 | TimkenSteel | $12 – $18 |
8630 | Allegheny Technologies | $11 – $16 |
9310 | Carpenter Technology | $13 – $20 |
18Ni300 | Höganäs | $25 – $35 |
Maraging 250 | Sandvik | $30 – $40 |
Maraging 300 | Carpenter Technology | $32 – $42 |
Fe-Mo | Höganäs | $20 – $25 |
Fe-Cr | Sandvik | $18 – $22 |
42CrMo4 | Voestalpine | $10 – $14 |
Pros and Cons of Low Alloy Powder
When selecting low alloy powders, it’s essential to weigh their pros and cons. Here’s a table comparing the advantages and limitations:
Advantages | Disadvantages |
---|---|
High strength and toughness | Higher cost compared to pure metals |
Excellent wear and corrosion resistance | Complex processing requirements |
Versatile applications | Potential for alloy segregation |
Good machinability | Limited availability for some alloys |
Enhanced hardenability | Risk of distortion during heat treatment |
FAQs
Here’s a table to address common questions about low alloy powder:
Question | Answer |
---|---|
What is low alloy powder used for? | Low alloy powder is used in automotive, aerospace, tool manufacturing, and other industries for high-strength and wear-resistant components. |
How is low alloy powder made? | Low alloy powder is typically made through atomization, where molten metal is sprayed into fine droplets and solidified. |
What are the benefits of low alloy powder? | Benefits include high strength, toughness, wear resistance, and corrosion resistance. |
Can low alloy powder be 3D printed? | Yes, low alloy powders can be used in additive manufacturing for producing complex parts. |
How does low alloy powder differ from high alloy? | Low alloy powders contain fewer alloying elements (<5%) compared to high alloy powders, which have more alloying elements (>5%). |
What are common alloying elements in low alloy powder? | Common elements include chromium, molybdenum, nickel, and vanadium. |
Is low alloy powder expensive? | The cost varies depending on the specific alloy, but it is generally higher than pure metals due to the added alloying elements. |
How do I choose the right low alloy powder? | Consider factors like mechanical properties, corrosion resistance, application requirements, and cost. |
What industries benefit most from low alloy powder? | Automotive, aerospace, tool manufacturing, oil & gas, and defense industries benefit the most. |
Are there any environmental concerns with low alloy powder? | Proper handling and recycling can mitigate environmental concerns associated with metal powders. |
Conclusion
Low alloy powder is a vital material in modern manufacturing and industrial applications. Its unique blend of strength, toughness, and resistance properties make it a go-to choice for various high-performance components. By understanding its composition, characteristics, and applications, as well as comparing specific models and suppliers, you can make informed decisions for your projects. Whether you’re in the automotive, aerospace, or tool manufacturing industry, low alloy powder offers the versatility and reliability you need to succeed.