Overview of Metal Additive Manufacturing (MAM)
Metal Additive Manufacturing (MAM) is revolutionizing the manufacturing industry, bringing unprecedented flexibility and innovation to the production of complex metal parts. Leveraging advanced technologies such as 3D printing, MAM allows for the creation of highly intricate and detailed metal components that were previously impossible to produce with traditional manufacturing methods. This article delves deep into the world of MAM, exploring its processes, materials, applications, and more.
What is Metal Additive Manufacturing?
At its core, MAM involves the layer-by-layer addition of metal material to build up a final product. Unlike subtractive manufacturing, which carves out parts from a larger block of material, MAM adds material only where it is needed. This process not only reduces waste but also allows for the creation of highly complex geometries and lightweight structures.
How Does MAM Work?
The process begins with a digital 3D model of the object to be manufactured. This model is then sliced into thin layers by specialized software. The MAM machine, guided by the sliced model, deposits metal powder or wire, fusing it layer by layer using a heat source such as a laser or electron beam. This additive approach enables the production of components with intricate internal features and optimized designs for specific applications.
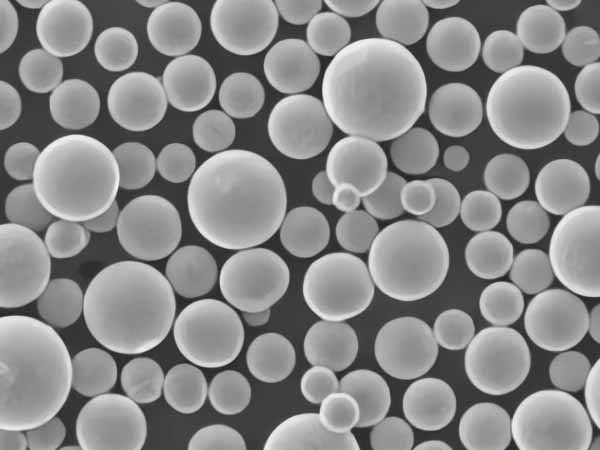
Types of Metal Additive Manufacturing Processes
There are several types of MAM processes, each with its own unique capabilities and applications. Below is a summary of the most commonly used methods:
Process Type | Description | Applications | Materials Used |
---|---|---|---|
Selective Laser Melting (SLM) | Uses a high-powered laser to melt and fuse metal powder. | Aerospace, medical implants, automotive. | Titanium, aluminum, stainless steel. |
Electron Beam Melting (EBM) | Uses an electron beam to melt metal powder in a vacuum. | Aerospace, medical implants. | Titanium, cobalt-chrome. |
Direct Metal Laser Sintering (DMLS) | Similar to SLM but sinters metal powder without fully melting it. | Aerospace, medical implants, tooling. | Titanium, aluminum, stainless steel. |
Binder Jetting | Uses a liquid binding agent to fuse metal powder, followed by sintering. | Prototyping, low-volume production. | Stainless steel, Inconel, copper. |
Directed Energy Deposition (DED) | Deposits metal powder or wire using a focused energy source. | Repair, maintenance, aerospace. | Titanium, Inconel, stainless steel. |
Composition of Metal Powders in MAM
Different metals and alloys are used in MAM, each offering unique properties and suited for specific applications. Here are some of the most commonly used metal powders:
Common Metal Powders Used in MAM
Metal Powder | Composition | Properties | Applications |
---|---|---|---|
Titanium (Ti-6Al-4V) | 90% Titanium, 6% Aluminum, 4% Vanadium. | High strength, corrosion resistance, biocompatibility. | Aerospace, medical implants. |
Aluminum (AlSi10Mg) | 90% Aluminum, 10% Silicon, 0.5% Magnesium. | Lightweight, good thermal properties. | Automotive, aerospace. |
Stainless Steel (316L) | Iron, 16-18% Chromium, 10-14% Nickel, 2-3% Molybdenum. | Corrosion resistance, high ductility. | Medical, food processing, marine. |
Inconel (718) | Nickel, 50-55% Nickel, 17-21% Chromium, 2.8-3.3% Molybdenum. | High temperature strength, corrosion resistance. | Aerospace, gas turbines. |
Cobalt-Chrome (CoCr) | 55-65% Cobalt, 26-30% Chromium, 5-7% Molybdenum. | Wear resistance, biocompatibility. | Medical implants, dental. |
Tool Steel (H13) | Iron, 0.32-0.45% Carbon, 4.75-5.5% Chromium, 1.1-1.8% Molybdenum. | High hardness, wear resistance. | Tooling, molds, dies. |
Copper (Cu) | 99.9% Copper. | Excellent thermal and electrical conductivity. | Electronics, heat exchangers. |
Maraging Steel (MS1) | Iron, 18% Nickel, 8% Cobalt, 5% Molybdenum. | High strength, toughness. | Aerospace, tooling. |
Nickel Alloy (HX) | 47% Nickel, 22% Chromium, 18% Iron. | High temperature strength, oxidation resistance. | Aerospace, chemical processing. |
Tungsten (W) | 99.95% Tungsten. | High density, high melting point. | Aerospace, defense. |
Characteristics of Metal Additive Manufacturing
Metal Additive Manufacturing brings several unique characteristics that set it apart from traditional manufacturing methods. Here’s a closer look at some key attributes:
Precision and Complexity
MAM allows for the production of highly complex geometries with intricate internal features that are often impossible to achieve with conventional methods. This precision enables the creation of components that are both lightweight and strong, optimizing performance in critical applications.
Material Efficiency
One of the standout advantages of MAM is its ability to minimize material waste. By adding material only where needed, MAM significantly reduces the scrap generated during the manufacturing process. This efficiency not only lowers material costs but also contributes to more sustainable manufacturing practices.
Customization
With MAM, it’s possible to create customized parts tailored to specific needs. This is particularly beneficial in industries like healthcare, where patient-specific implants can be produced based on individual anatomical data. The flexibility of MAM also supports rapid prototyping, allowing for faster design iterations and innovation.
Reduced Lead Times
Traditional manufacturing often involves lengthy lead times due to the need for tooling and mold creation. MAM bypasses these steps, enabling faster production from digital design to finished part. This reduction in lead times accelerates product development cycles and time-to-market.
Advantages of Metal Additive Manufacturing
The advantages of MAM are numerous and impactful across various industries. Here are some of the most significant benefits:
Design Freedom
MAM offers unparalleled design freedom, allowing engineers to explore innovative geometries and structures. This freedom enables the production of parts with optimized performance characteristics, such as lattice structures that reduce weight without compromising strength.
Cost Savings
By reducing material waste and eliminating the need for expensive tooling, MAM can lead to significant cost savings. Additionally, the ability to produce complex parts in a single build reduces assembly time and associated costs.
Improved Performance
Components produced through MAM often exhibit superior performance due to their optimized designs and high-quality material properties. For instance, parts can be designed with internal cooling channels or optimized for weight reduction, leading to improved efficiency and functionality.
Sustainability
MAM contributes to more sustainable manufacturing practices by minimizing waste and reducing the environmental impact of production. The ability to produce parts on-demand also reduces the need for inventory, further contributing to sustainability.
Rapid Prototyping and Production
The speed and flexibility of MAM make it ideal for rapid prototyping and low-volume production. This capability allows companies to quickly test and iterate on designs, accelerating innovation and reducing time-to-market.
Applications of Metal Additive Manufacturing
Metal Additive Manufacturing is finding applications across a wide range of industries. Here’s a look at some of the key sectors benefiting from this technology:
Aerospace
The aerospace industry was an early adopter of MAM due to its need for lightweight, high-strength components. MAM allows for the production of complex parts such as fuel nozzles, turbine blades, and structural components, improving performance and fuel efficiency.
Medical and Dental
In the medical field, MAM is used to create customized implants, prosthetics, and surgical instruments. Patient-specific implants, such as hip and knee replacements, can be produced based on individual anatomical data, improving fit and function. In dentistry, MAM enables the production of crowns, bridges, and orthodontic devices with high precision.
Automotive
The automotive industry leverages MAM for the production of lightweight, high-performance parts. Applications include engine components, exhaust systems, and structural parts. The ability to produce complex geometries and lightweight structures helps improve fuel efficiency and performance.
Energy
In the energy sector, MAM is used to produce components for gas turbines, nuclear reactors, and oil and gas exploration. The technology allows for the creation of parts with optimized cooling channels and improved material properties, enhancing efficiency and durability.
Tooling and Manufacturing
MAM is also used to produce tooling and manufacturing aids, such as molds, dies, and fixtures. The ability to create complex geometries and incorporate conformal cooling channels improves the performance and lifespan of these tools.
Defense
The defense industry benefits from MAM through the production of lightweight, high-strength components for military vehicles, aircraft, and weaponry. The technology allows for the rapid production of parts in remote locations, supporting mission-critical applications.
Specifications, Sizes, Grades, and Standards in MAM
Metal Additive Manufacturing involves a variety of specifications, sizes, grades, and standards to ensure the quality and performance of produced parts. Here’s a detailed look at these aspects:
Specifications of MAM Metal Powders
Metal Powder | Particle Size (µm) | Purity (%) | Density (g/cm³) | Standard |
---|---|---|---|---|
Titanium (Ti-6Al-4V) | 15-45 | 99.5 | 4.43 | ASTM F2924 |
Aluminum (AlSi10Mg) | 20-63 | 99.7 | 2.68 | ASTM F3318 |
Stainless Steel (316L) | 15-45 | 99.9 | 7.99 | ASTM F3184 |
Inconel (718) | 15-53 | 99.5 | 8.19 | ASTM F3055 |
Cobalt-Chrome (CoCr) | 10-45 | 99.9 | 8.3 | ASTM F75 |
Tool Steel (H13) | 15-45 | 99.5 | 7.8 | ASTM A681 |
Copper (Cu) | 10-45 | 99.9 | 8.96 | ASTM B216 |
Maraging Steel (MS1) | 10-45 | 99.9 | 8.0 | ASTM A579 |
Nickel Alloy (HX) | 10-45 | 99.8 | 8.24 | ASTM B435 |
Tungsten (W) | 15-45 | 99.95 | 19.3 | ASTM B777 |
Applications and Uses of MAM Metal Powders
Industry | Application | Example Parts | Benefits |
---|---|---|---|
Aerospace | Structural components | Fuel nozzles, turbine blades | Lightweight, high strength |
Medical | Implants | Hip replacements, dental crowns | Customization, biocompatibility |
Automotive | Engine components | Pistons, exhaust systems | Weight reduction, performance |
Energy | Turbine components | Gas turbine blades | Efficiency, durability |
Tooling | Manufacturing aids | Molds, dies | Performance, longevity |
Defense | Military components | Vehicle parts, weaponry | Lightweight, strength |
Suppliers and Pricing of MAM Metal Powders
The market for MAM metal powders is diverse, with numerous suppliers offering a range of materials. Here’s a look at some key suppliers and pricing details:
Key Suppliers and Pricing Details
Supplier | Metal Powder | Price per kg | MOQ (Minimum Order Quantity) |
---|---|---|---|
Höganäs AB | Titanium (Ti-6Al-4V) | $300 | 10 kg |
Sandvik | Aluminum (AlSi10Mg) | $100 | 5 kg |
Carpenter Technology | Stainless Steel (316L) | $80 | 10 kg |
LPW Technology | Inconel (718) | $400 | 10 kg |
Oerlikon | Cobalt-Chrome (CoCr) | $350 | 5 kg |
EOS GmbH | Tool Steel (H13) | $90 | 10 kg |
GE Additive | Copper (Cu) | $70 | 5 kg |
Renishaw | Maraging Steel (MS1) | $120 | 10 kg |
AP&C | Nickel Alloy (HX) | $450 | 5 kg |
HC Starck | Tungsten (W) | $1000 | 5 kg |
Pros and Cons of Metal Additive Manufacturing
Metal Additive Manufacturing offers a range of advantages and limitations. Here’s a detailed comparison:
Advantages and Limitations of MAM
Advantages | Limitations |
---|---|
Design Flexibility | Material Limitations |
MAM allows for complex geometries and intricate designs. | Limited to certain metal powders and alloys. |
Reduced Waste | High Initial Cost |
Minimal material waste compared to traditional methods. | High cost of equipment and materials. |
Customization | Post-Processing Requirements |
Ability to produce customized parts for specific applications. | Often requires additional finishing processes. |
Rapid Prototyping | Size Constraints |
Fast production of prototypes and small batches. | Limited by the build volume of MAM machines. |
Improved Performance | Quality Control |
Parts can be optimized for specific performance characteristics. | Requires stringent quality control and testing. |
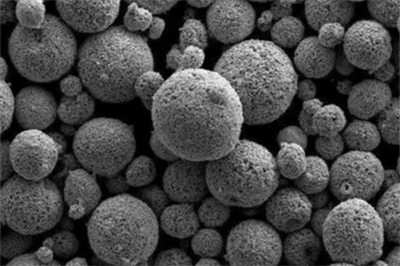
FAQ
Question | Answer |
---|---|
What is Metal Additive Manufacturing (MAM)? | MAM is a process that builds metal parts layer by layer using a digital model and a heat source to fuse metal powder or wire. |
What are the benefits of MAM? | Benefits include design flexibility, reduced waste, customization, rapid prototyping, and improved performance. |
What types of metal powders are used in MAM? | Common metal powders include titanium, aluminum, stainless steel, Inconel, cobalt-chrome, tool steel, copper, maraging steel, nickel alloys, and tungsten. |
Which industries use MAM? | Industries such as aerospace, medical, automotive, energy, tooling, and defense widely use MAM. |
What are the limitations of MAM? | Limitations include high initial costs, material restrictions, post-processing needs, size constraints, and quality control challenges. |
How does MAM reduce waste? | MAM adds material only where needed, minimizing scrap and reducing overall material usage. |
Can MAM produce customized parts? | Yes, MAM excels at producing customized parts tailored to specific requirements, especially beneficial in medical and dental applications. |
What is the difference between SLM and DMLS? | Both SLM and DMLS use lasers to fuse metal powder, but SLM fully melts the powder while DMLS sinters it without completely melting. |
What is the typical lead time for MAM parts? | Lead times for MAM parts can be significantly shorter than traditional methods, often ranging from a few days to a few weeks. |
What are the key factors to consider when choosing a metal powder for MAM? | Key factors include material properties, compatibility with the MAM process, part application, and cost. |
Conclusion
Metal Additive Manufacturing is a transformative technology that offers significant advantages over traditional manufacturing methods. With its ability to produce complex, high-performance parts efficiently and sustainably, MAM is poised to drive innovation across a wide range of industries. Whether you’re in aerospace, medical, automotive, or another sector, the potential of MAM to revolutionize manufacturing processes and product designs is immense. By understanding the various processes, materials, and applications, companies can harness the full potential of MAM to achieve new levels of performance and efficiency.