Welcome to the ultimate guide on metal binder jetting. If you’re curious about this innovative technology, you’ve come to the right place. We’re diving deep into what metal binder jetting is, how it works, its applications, benefits, limitations, and much more. Ready to explore this fascinating world? Let’s get started!
Overview of Metal Binder Jetting
Metal binder jetting is a form of additive manufacturing that stands out for its ability to create complex metal parts with high precision and relatively low costs. This technology uses a binding agent to join metal powders layer by layer, creating intricate designs that traditional manufacturing methods often struggle with. Unlike other 3D printing techniques, metal binder jetting doesn’t rely on high temperatures to fuse materials, which opens up a wide range of possibilities in terms of materials and applications.
Key Details of Metal Binder Jetting
- Technology: Additive Manufacturing
- Material: Metal Powders
- Binding Agent: Polymer or other adhesives
- Process: Layer-by-layer construction
- Applications: Aerospace, automotive, medical devices, and more
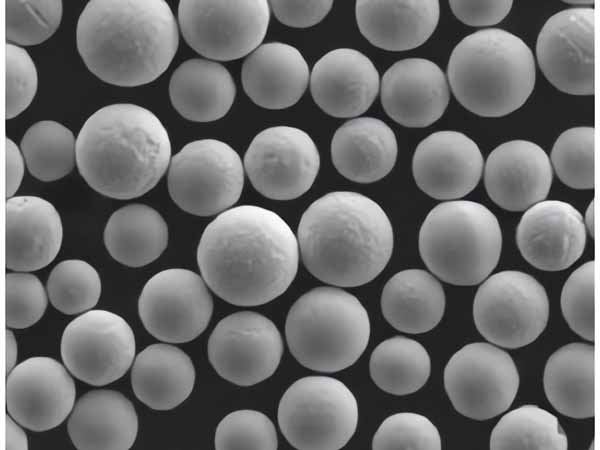
Types and Composition of Metal Binder Jetting Powders
When it comes to metal binder jetting, the type of metal powder used can significantly influence the final product’s properties. Here are some of the most commonly used metal powders in binder jetting:
Metal Powder | Composition | Properties | Characteristics |
---|---|---|---|
Stainless Steel 316L | Iron, Chromium, Nickel, Molybdenum | High corrosion resistance, excellent mechanical properties | Durable, suitable for harsh environments |
Inconel 625 | Nickel, Chromium, Molybdenum, Niobium | High strength, excellent fatigue and thermal fatigue resistance | Ideal for high-temperature applications |
Titanium Ti-6Al-4V | Titanium, Aluminum, Vanadium | High strength-to-weight ratio, biocompatible | Perfect for medical implants and aerospace |
Copper | Pure Copper | Excellent thermal and electrical conductivity | Suitable for electrical components |
Bronze | Copper, Tin | Good machinability, corrosion resistance | Ideal for decorative and functional parts |
Tool Steel M2 | Tungsten, Molybdenum, Chromium, Vanadium | High wear resistance, high hardness | Perfect for cutting tools and dies |
Cobalt-Chrome | Cobalt, Chromium, Molybdenum | High strength, wear resistance, biocompatible | Used in medical and dental applications |
Aluminum | Pure Aluminum or alloys | Lightweight, good strength | Ideal for automotive and aerospace parts |
Nickel Alloy 718 | Nickel, Chromium, Iron, Niobium | High yield, tensile, and creep-rupture properties | Suitable for aerospace and power generation |
Maraging Steel | Iron, Nickel, Cobalt, Molybdenum | Ultra-high strength, good toughness | Used in high-stress applications like tooling |
Applications of Metal Binder Jetting
Metal binder jetting’s versatility makes it suitable for a wide array of industries. Here are some key applications:
Application | Description |
---|---|
Aerospace | Lightweight, complex parts that can withstand high temperatures and stresses |
Automotive | Customized components, prototypes, and high-performance parts |
Medical Devices | Custom implants, surgical instruments, and dental prosthetics |
Industrial Equipment | Tooling, fixtures, and machine components |
Consumer Goods | Customized jewelry, electronics, and household items |
Energy | Parts for turbines, generators, and other power equipment |
Art and Design | Complex, aesthetically pleasing sculptures and decorative items |
Specifications, Sizes, Grades, and Standards
Metal binder jetting offers a range of specifications, sizes, and grades to meet different industry standards.
Material | Specifications | Sizes | Grades | Standards |
---|---|---|---|---|
Stainless Steel 316L | ASTM A240, ASTM A276 | 1-100 microns | Grade A, B, C | ISO 5832-1, UNS S31603 |
Inconel 625 | ASTM B443, ASTM B446 | 10-45 microns | Grade 1, 2 | UNS N06625 |
Titanium Ti-6Al-4V | ASTM B348, ASTM F136 | 15-45 microns | Grade 5, 23 | ISO 5832-3, UNS R56400 |
Copper | ASTM B170, ASTM B379 | 20-63 microns | C11000, C10200 | UNS C11000 |
Bronze | ASTM B505, ASTM B427 | 20-45 microns | C90700, C93200 | UNS C90700 |
Tool Steel M2 | ASTM A600, ASTM A681 | 1-100 microns | Grade M2 | UNS T11302 |
Cobalt-Chrome | ASTM F75, ASTM F1537 | 5-25 microns | CoCr28Mo6, CoCr20W15Ni | UNS R31538 |
Aluminum | ASTM B221, ASTM B234 | 15-45 microns | 6061, 7075 | UNS A96061 |
Nickel Alloy 718 | ASTM B670, ASTM B637 | 15-53 microns | Grade 1, 2 | UNS N07718 |
Maraging Steel | ASTM A538, ASTM A646 | 10-45 microns | Grade 250, 300 | UNS K93120 |
Suppliers and Pricing Details
Finding the right supplier is crucial for ensuring the quality and cost-effectiveness of metal binder jetting materials.
Supplier | Materials Offered | Pricing (Approx.) | Location |
---|---|---|---|
XYZ Metals | Stainless Steel, Inconel, Titanium | $50 – $100/kg | USA |
ABC Materials | Copper, Bronze, Tool Steel | $30 – $80/kg | Germany |
Metal Powders Co. | Cobalt-Chrome, Aluminum, Nickel Alloys | $60 – $120/kg | UK |
TechMetals Inc. | Stainless Steel, Maraging Steel | $40 – $90/kg | China |
Global Alloys | Inconel, Titanium, Tool Steel | $70 – $150/kg | Japan |
Advantages and Limitations of Metal Binder Jetting
Like any technology, metal binder jetting comes with its pros and cons. Let’s break them down:
Advantages
- Complex Geometries: Capable of producing intricate and complex shapes that are difficult or impossible with traditional methods.
- Material Efficiency: Reduces waste as only the necessary amount of material is used.
- Cost-Effective: Lower production costs compared to other additive manufacturing techniques like laser sintering.
- Scalability: Suitable for both small batch production and mass manufacturing.
- Flexibility: Can use a wide range of metal powders, offering versatility in applications.
Limitations
- Mechanical Properties: Parts may have lower mechanical properties compared to those made with traditional methods.
- Post-Processing: Often requires post-processing steps like sintering to achieve desired properties.
- Surface Finish: May result in a rough surface finish that needs additional treatment.
- Size Limitations: Typically limited to smaller parts, though advancements are being made.
- Binder Residue: Potential for binder residue to affect material properties if not fully removed.
Characteristics of Metal Binder Jetting
Understanding the characteristics of metal binder jetting can help you determine if this technology is right for your needs.
Strength and Durability
Metal binder jetted parts are generally strong and durable, but they often require post-processing to achieve the mechanical properties needed for high-stress applications.
Precision and Accuracy
One of the key benefits of metal binder jetting is its high precision and accuracy, making it ideal for producing complex geometries with tight tolerances.
Material Versatility
Metal binder jetting supports a wide range of materials, from stainless steel and Inconel to titanium and copper. This versatility makes it suitable for various industries and applications.
Production Speed
Compared to other additive manufacturing techniques, metal binder jetting is relatively fast, making it a good choice for rapid prototyping and small batch production.
Cost Efficiency
Due to its material efficiency and relatively low production costs, metal binder jetting is a cost-effective option for many applications.
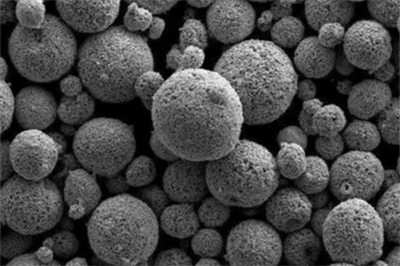
FAQs
What is metal binder jetting?
Metal binder jetting is an additive manufacturing process that uses a binding agent to join metal powders layer by layer, creating intricate and complex metal parts.
What materials can be used in metal binder jetting?
Common materials include stainless steel, Inconel, titanium, copper, bronze, tool steel, cobalt-chrome, aluminum, nickel alloys, and maraging steel.
What is metal binder jetting?
Metal binder jetting is an additive manufacturing process that uses a liquid binding agent to join metal powder particles together, layer by layer, to create a 3D object. Think of it like inkjet printing for metal parts.
How does it work?
The process involves spreading a thin layer of metal powder. A printhead then jets a binding agent onto the powder, selectively gluing particles together according to a digital design. New layers of powder are added and bonded until the entire part is complete. The printed part then undergoes additional steps like debinding (removing the binder) and sintering (fusing the metal particles) to create a final, solid metal object.
What are the advantages of metal binder jetting?
- Faster production: Compared to other metal 3D printing methods, binder jetting can be much faster, making it suitable for mass production.
- Lower cost: Binder jetting machines are generally less expensive than other metal 3D printing technologies.
- No support structures: Because unbound powder surrounds the printed part, support structures are typically not required, reducing post-processing needs.
- Wide range of materials: Metal binder jetting can work with a variety of metal powders, offering design flexibility.
4. What are the disadvantages of metal binder jetting?
- Limited part properties: Compared to some other methods, metal binder jetting parts may have slightly lower strength and density.
- Surface finish: The surface finish of binder jetted parts may be rougher than those produced by other methods.
- Post-processing: While less complex than some methods, debinding and sintering steps add time and cost to the process.
What is metal binder jetting used for?
Metal binder jetting is suitable for a variety of applications, including:
- Prototyping: Quickly creating functional metal prototypes for testing and design iteration.
- Low-volume production: Producing small batches of complex metal parts.
- Mass production: High-speed production of metal parts for certain applications, especially those that don’t require the absolute highest strength.