Metal Injection Molding (MIM) is a groundbreaking technology that merges the versatility of plastic injection molding with the strength and integrity of metal. This process is widely used to create complex, high-performance metal parts with intricate geometries that are challenging to produce through traditional manufacturing methods. If you’re keen to dive deep into the world of MIM, buckle up as we unravel its secrets, applications, benefits, and much more.
Overview of Metal Injection Molding
MIM involves mixing metal powders with a binder material to create a feedstock that is injected into a mold, debound, and then sintered. The result is a dense, precision metal part that is ideal for various applications ranging from medical devices to automotive components.
Key Details:
- Process: Injection molding of metal powders with binders, followed by debinding and sintering.
- Materials: Wide range of metals including stainless steels, titanium, and superalloys.
- Applications: Medical, automotive, aerospace, electronics, consumer products.
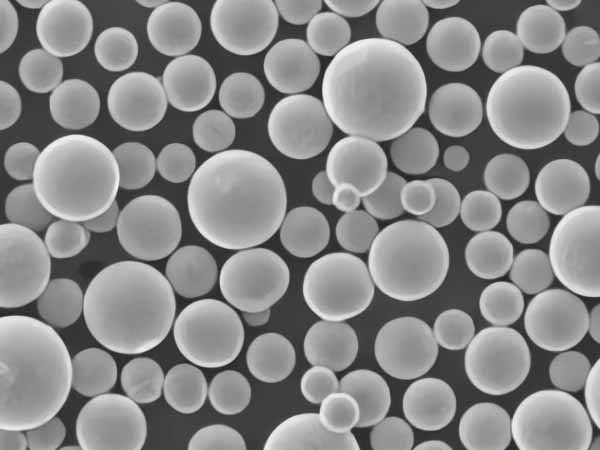
Types, Composition, Properties, and Characteristics of Metal Powders Used in MIM
Understanding the types of metal powders and their specific properties is crucial for selecting the right material for your MIM project. Below is a detailed table highlighting various metal powders used in MIM, along with their composition, properties, and characteristics.
Metal Powder Model | Composition | Properties | Characteristics |
---|---|---|---|
316L Stainless Steel | Fe-Cr-Ni-Mo | Corrosion resistant, high ductility | Ideal for medical and food processing applications |
17-4 PH Stainless Steel | Fe-Cr-Ni-Cu-Nb | High strength, good corrosion resistance | Used in aerospace and automotive components |
Titanium Ti-6Al-4V | Ti-Al-V | Lightweight, high strength-to-weight ratio | Perfect for aerospace and medical implants |
Inconel 718 | Ni-Cr-Fe-Mo | High temperature resistance, strength | Common in aerospace, power generation |
Copper | Pure Cu | Excellent electrical conductivity | Used in electrical and thermal applications |
Tungsten Heavy Alloy | W-Ni-Fe or W-Ni-Cu | High density, radiation shielding | Suitable for military, aerospace |
Cobalt-Chromium Alloy | Co-Cr-Mo | Wear resistance, biocompatible | Ideal for orthopedic implants |
Molybdenum | Pure Mo | High melting point, strength | Utilized in high-temperature applications |
Iron-Phosphorus Alloy | Fe-P | Soft magnetic properties | Used in magnetic cores, sensors |
Nickel Superalloy | Ni-Cr-Fe | Corrosion resistance, thermal stability | Employed in turbine blades, engine components |
Applications and Uses of Metal Injection Molding
MIM’s versatility allows for a wide range of applications across various industries. Below is a table showcasing the specific applications and uses of MIM components.
Industry | Applications | Examples |
---|---|---|
Medical | Surgical instruments, implants | Orthopedic screws, dental brackets |
Automotive | Engine components, transmission parts | Fuel injectors, turbocharger components |
Aerospace | Structural components, engine parts | Turbine blades, fasteners |
Electronics | Connectors, heat sinks | Microelectronic housings, thermal management |
Consumer Products | Watches, eyewear, kitchen appliances | Precision gears, frames |
Industrial Equipment | Tooling, machinery components | Cutting tools, pump parts |
Defense | Ammunition, firearm components | Projectile cores, gun parts |
Specifications, Sizes, Grades, and Standards
To ensure the highest quality and performance, MIM parts must adhere to specific standards and grades. The table below outlines some of the key specifications, sizes, grades, and standards for MIM materials.
Material | Sizes | Grades | Standards |
---|---|---|---|
316L Stainless Steel | 0.1mm to 50mm | ASTM A276 | ISO 5832-1, ASTM F138 |
17-4 PH Stainless Steel | 0.2mm to 60mm | ASTM A564 | AMS 5643, ASTM A693 |
Titanium Ti-6Al-4V | 0.1mm to 40mm | Grade 5 | ASTM B348, ISO 5832-3 |
Inconel 718 | 0.2mm to 50mm | AMS 5662 | AMS 5596, ASTM B637 |
Copper | 0.1mm to 30mm | C11000 | ASTM B152, B187 |
Tungsten Heavy Alloy | 0.2mm to 70mm | WHA 90/10 | ASTM B777, AMS-T-21014 |
Cobalt-Chromium Alloy | 0.1mm to 40mm | ASTM F75 | ISO 5832-4, ASTM F1537 |
Molybdenum | 0.2mm to 60mm | Grade 1 | ASTM B387, ISO 5721 |
Iron-Phosphorus Alloy | 0.1mm to 30mm | FeP02 | ISO 10027 |
Nickel Superalloy | 0.1mm to 50mm | IN718 | AMS 5663, ASTM B637 |
Suppliers and Pricing Details
Sourcing the right materials at competitive prices is essential for the success of any MIM project. Below is a table of key suppliers and their pricing details for various MIM powders.
Supplier | Material | Pricing | Contact Details |
---|---|---|---|
Sandvik Osprey | 316L Stainless Steel | $30/kg | www.sandvik.com |
Carpenter Technology | 17-4 PH Stainless Steel | $40/kg | www.cartech.com |
ATI Metals | Titanium Ti-6Al-4V | $120/kg | www.atimetals.com |
Special Metals Corporation | Inconel 718 | $100/kg | www.specialmetals.com |
American Elements | Copper | $15/kg | www.americanelements.com |
Plansee Group | Tungsten Heavy Alloy | $90/kg | www.plansee.com |
Arcam AB | Cobalt-Chromium Alloy | $80/kg | www.arcam.com |
H.C. Starck | Molybdenum | $50/kg | www.hcstarck.com |
Höganäs AB | Iron-Phosphorus Alloy | $25/kg | www.hoganas.com |
VDM Metals | Nickel Superalloy | $110/kg | www.vdm-metals.com |
Comparing Pros and Cons: Advantages and Limitations
When deciding whether to use MIM for your next project, it’s essential to weigh the pros and cons. Here’s a comparative table to help you make an informed decision.
Aspect | Advantages | Limitations |
---|---|---|
Complexity and Design Freedom | Allows for intricate designs and complex geometries | Initial tooling costs can be high |
Material Properties | Excellent mechanical properties and material choices | Limited to small to medium-sized parts |
Production Volume | Cost-effective for high-volume production | Less cost-effective for low-volume production |
Surface Finish | Superior surface finish, often no need for machining | May require secondary operations for specific finishes |
Consistency and Precision | High dimensional accuracy and repeatability | Some materials may experience shrinkage or warping |
Lead Time | Fast production cycle for large quantities | Longer lead times for initial setup and tooling |
In-Depth Look at Metal Powder Models for MIM
Now, let’s take a deeper dive into the specific metal powder models used in Metal Injection Molding. Understanding these materials in detail will help you choose the best option for your application.
1. 316L Stainless Steel
Composition: Fe-Cr-Ni-Mo
Properties: Known for its exceptional corrosion resistance, high ductility, and good weldability, 316L stainless steel is a popular choice for medical and food processing applications. This low-carbon variant of 316 stainless steel minimizes the risk of carbide precipitation, enhancing its resistance to intergranular corrosion.
Characteristics: The austenitic structure of 316L stainless steel provides excellent toughness, even at cryogenic temperatures. It’s also non-magnetic in the annealed condition, which can be advantageous for certain applications.
2. 17-4 PH Stainless Steel
Composition: Fe-Cr-Ni-Cu-Nb
Properties: This precipitation-hardening stainless steel offers a unique combination of high strength, good corrosion resistance, and excellent mechanical properties at elevated temperatures. It is often used in aerospace and automotive applications where reliability is paramount.
Characteristics: 17-4 PH stainless steel can
be heat-treated to various strength levels, allowing for flexibility in design and manufacturing. Its high hardness and strength make it suitable for demanding environments.
3. Titanium Ti-6Al-4V
Composition: Ti-Al-V
Properties: This titanium alloy is prized for its high strength-to-weight ratio, excellent corrosion resistance, and biocompatibility, making it ideal for aerospace and medical implants. The addition of aluminum and vanadium enhances the alloy’s mechanical properties and thermal stability.
Characteristics: Ti-6Al-4V can be heat-treated for further strengthening, and its low density makes it an excellent choice for applications requiring lightweight and strong materials. It also exhibits good fatigue resistance, which is critical in dynamic environments.
4. Inconel 718
Composition: Ni-Cr-Fe-Mo
Properties: Inconel 718 is a nickel-chromium alloy known for its high strength and corrosion resistance at elevated temperatures. This makes it a preferred material for aerospace and power generation applications.
Characteristics: The alloy maintains its mechanical properties in extreme environments, including high temperatures and corrosive atmospheres. It also exhibits good weldability and formability, which is beneficial for complex part designs.
5. Copper
Composition: Pure Cu
Properties: Copper is renowned for its excellent electrical and thermal conductivity, making it essential in electrical and thermal management applications. Its ductility and malleability also make it easy to work with.
Characteristics: Pure copper is soft and highly conductive, which is why it is widely used in electrical wiring, heat exchangers, and other applications requiring efficient heat and electricity transfer.
6. Tungsten Heavy Alloy
Composition: W-Ni-Fe or W-Ni-Cu
Properties: Tungsten heavy alloys are known for their high density, excellent radiation shielding properties, and good mechanical strength. These characteristics make them suitable for military, aerospace, and medical applications.
Characteristics: The high density of tungsten alloys provides effective radiation shielding, while their mechanical properties ensure durability and reliability in demanding environments. They are also resistant to wear and corrosion.
7. Cobalt-Chromium Alloy
Composition: Co-Cr-Mo
Properties: Cobalt-chromium alloys offer excellent wear resistance, biocompatibility, and corrosion resistance, making them ideal for orthopedic implants and dental applications.
Characteristics: These alloys can withstand harsh biological environments without degrading, ensuring long-term performance and reliability. Their high wear resistance also contributes to their durability in joint replacement and dental restoration applications.
8. Molybdenum
Composition: Pure Mo
Properties: Molybdenum is known for its high melting point, excellent thermal conductivity, and good mechanical strength at elevated temperatures. It is commonly used in high-temperature applications.
Characteristics: Pure molybdenum retains its strength and stability at temperatures where other metals would fail. This makes it an ideal material for furnace components, electrical contacts, and other high-temperature environments.
9. Iron-Phosphorus Alloy
Composition: Fe-P
Properties: Iron-phosphorus alloys possess soft magnetic properties, making them suitable for use in magnetic cores and sensors.
Characteristics: These alloys offer high magnetic permeability and low coercivity, which are essential for efficient magnetic field generation and detection. They are often used in transformers, inductors, and other magnetic applications.
10. Nickel Superalloy
Composition: Ni-Cr-Fe
Properties: Nickel superalloys are characterized by their excellent corrosion resistance, high thermal stability, and exceptional mechanical properties at high temperatures. They are widely used in turbine blades and engine components.
Characteristics: The combination of nickel, chromium, and iron in these superalloys provides outstanding resistance to oxidation and thermal fatigue, ensuring reliability and longevity in extreme conditions.
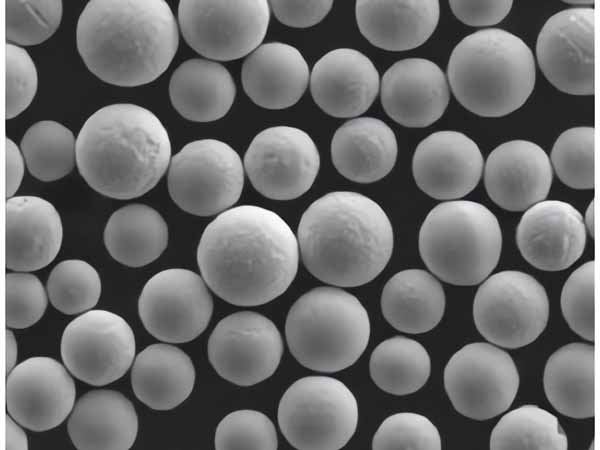
FAQs
Here are some frequently asked questions about Metal Injection Molding, along with detailed answers to help you understand this fascinating process better.
Question | Answer |
---|---|
What is Metal Injection Molding? | Metal Injection Molding (MIM) is a manufacturing process that combines metal powders with a binder to create complex, high-strength metal parts through injection molding, debinding, and sintering. |
What materials can be used in MIM? | A wide range of metals can be used, including stainless steels, titanium, nickel alloys, cobalt-chromium alloys, tungsten, and more. |
What are the benefits of using MIM? | MIM offers design flexibility, excellent material properties, high precision, and cost-effectiveness for high-volume production. |
What are the limitations of MIM? | Initial tooling costs can be high, and it is less cost-effective for low-volume production. There are also size limitations for parts. |
How does the MIM process work? | The process involves mixing metal powders with a binder to form a feedstock, injecting it into a mold, debinding to remove the binder, and sintering to create a dense metal part. |
What industries use MIM components? | MIM components are used in various industries, including medical, automotive, aerospace, electronics, consumer products, industrial equipment, and defense. |
Can MIM produce parts with complex geometries? | Yes, MIM is particularly well-suited for producing parts with complex geometries and intricate designs that are difficult to achieve through traditional manufacturing methods. |
What is the typical lead time for MIM parts? | Lead times can vary depending on the complexity of the part and the production volume, but MIM generally offers fast production cycles for large quantities. |
How do MIM parts compare to traditionally manufactured parts? | MIM parts offer comparable or superior mechanical properties and precision compared to traditionally manufactured parts, with the added benefit of greater design flexibility. |
What are some common applications of MIM? | Common applications include surgical instruments, engine components, structural aerospace parts, electrical connectors, and precision gears. |
Conclusion
Metal Injection Molding is a powerful manufacturing process that opens up new possibilities for creating complex, high-performance metal parts. Whether you’re in the medical, automotive, aerospace, or any other industry, MIM offers a range of benefits that can enhance your products and streamline your production processes. By understanding the materials, processes, and applications of MIM, you can make informed decisions and leverage this technology to its fullest potential. So, why not explore the world of Metal Injection Molding and discover how it can revolutionize your manufacturing capabilities?