Metal Injection Moulding (MIM) is revolutionizing the world of metal parts manufacturing, offering unparalleled precision and complexity. This guide delves deep into MIM, providing a comprehensive overview, detailed insights into its process, and specific information on metal powders used in MIM. Let’s embark on a journey to understand the intricacies of this fascinating technology.
Overview of Metal Injection Moulding (MIM)
Metal Injection Moulding (MIM) is an advanced manufacturing process that combines the versatility of plastic injection molding with the strength and integrity of metal. MIM is particularly effective for producing small, intricate, and high-volume metal components. The process involves mixing fine metal powders with a binder to create a feedstock, which is then injected into a mold to form a desired shape. After molding, the part undergoes debinding and sintering to remove the binder and densify the metal.
Table: Key Details of Metal Injection Moulding (MIM)
Aspect | Details |
---|---|
Process | Mixing metal powders with binder, injection molding, debinding, sintering |
Materials | Stainless steel, titanium, copper, iron, nickel alloys |
Applications | Automotive, medical, aerospace, electronics |
Advantages | High precision, complex geometries, material efficiency, cost-effective for large volumes |
Limitations | Initial tooling cost, part size limitations, secondary operations may be required |
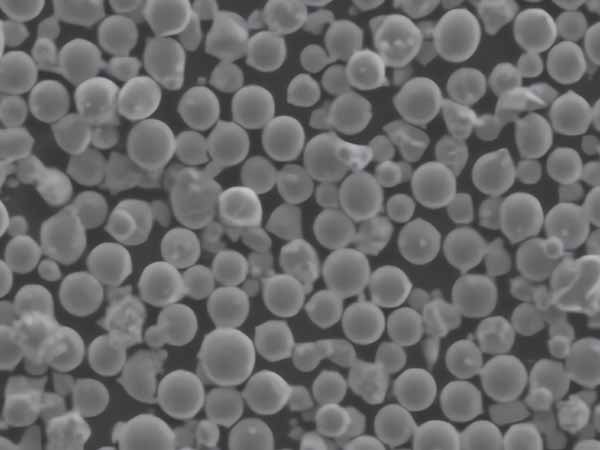
Composition of Metal Injection Moulding (MIM)
The composition of metal powders used in MIM is critical for achieving the desired mechanical properties and performance characteristics. Here, we explore ten specific metal powder models frequently used in MIM.
1. Stainless Steel 17-4 PH
- Composition: Iron, Chromium, Nickel, Copper, and Niobium
- Characteristics: High strength, good corrosion resistance, excellent mechanical properties
2. Stainless Steel 316L
- Composition: Iron, Chromium, Nickel, Molybdenum
- Characteristics: Superior corrosion resistance, non-magnetic, good weldability
3. Titanium Ti-6Al-4V
- Composition: Titanium, Aluminum, Vanadium
- Characteristics: High strength-to-weight ratio, excellent corrosion resistance, biocompatible
4. Iron Fe2Ni
- Composition: Iron, Nickel
- Characteristics: Good magnetic properties, moderate corrosion resistance, cost-effective
5. Nickel Alloy 718
- Composition: Nickel, Chromium, Iron, Molybdenum, Niobium
- Characteristics: High strength, good oxidation resistance, excellent fatigue resistance
6. Copper C110
- Composition: Copper
- Characteristics: Excellent electrical and thermal conductivity, good corrosion resistance
7. Cobalt-Chrome Alloy
- Composition: Cobalt, Chromium, Molybdenum
- Characteristics: High wear resistance, excellent biocompatibility, good mechanical strength
8. Tungsten Heavy Alloy
- Composition: Tungsten, Nickel, Iron/Copper
- Characteristics: High density, good thermal conductivity, high strength
9. Molybdenum TZM
- Composition: Molybdenum, Titanium, Zirconium, Carbon
- Characteristics: High strength at elevated temperatures, good thermal conductivity, low thermal expansion
10. Aluminum 6061
- Composition: Aluminum, Magnesium, Silicon
- Characteristics: Lightweight, good corrosion resistance, high machinability
Table: Metal Powder Models for MIM
Metal Powder Model | Composition | Characteristics |
---|---|---|
Stainless Steel 17-4 PH | Fe, Cr, Ni, Cu, Nb | High strength, corrosion resistance |
Stainless Steel 316L | Fe, Cr, Ni, Mo | Superior corrosion resistance, weldability |
Titanium Ti-6Al-4V | Ti, Al, V | High strength-to-weight ratio, biocompatible |
Iron Fe2Ni | Fe, Ni | Good magnetic properties, cost-effective |
Nickel Alloy 718 | Ni, Cr, Fe, Mo, Nb | High strength, oxidation resistance |
Copper C110 | Cu | Excellent electrical and thermal conductivity |
Cobalt-Chrome Alloy | Co, Cr, Mo | High wear resistance, biocompatible |
Tungsten Heavy Alloy | W, Ni, Fe/Cu | High density, thermal conductivity |
Molybdenum TZM | Mo, Ti, Zr, C | High strength at elevated temperatures |
Aluminum 6061 | Al, Mg, Si | Lightweight, machinable |
Characteristics of Metal Injection Moulding (MIM)
MIM offers unique characteristics that set it apart from other manufacturing processes. Understanding these traits can help in making informed decisions about its application.
- High Precision: MIM allows for the production of parts with tight tolerances and intricate geometries, making it ideal for complex components.
- Material Efficiency: The process minimizes material waste, as nearly all the feedstock can be used in the final product.
- Cost-Effective for Large Volumes: While initial tooling costs are high, MIM becomes cost-effective for large production runs due to reduced per-part costs.
- Diverse Material Selection: MIM supports a wide range of materials, including various metals and alloys, providing flexibility in part design.
- Good Mechanical Properties: Parts produced by MIM often exhibit excellent mechanical properties, comparable to those made by traditional methods like casting or forging.
Applications of Metal Injection Moulding (MIM)
MIM is used across various industries due to its ability to produce complex parts with high precision. Here are some of its key applications:
1. Automotive
- Components: Gears, turbocharger parts, fuel injector nozzles
- Benefits: High strength, precision, cost-effective for mass production
2. Medical
- Components: Surgical instruments, orthodontic brackets, implants
- Benefits: Biocompatibility, precision, ability to produce complex shapes
3. Aerospace
- Components: Engine components, fasteners, brackets
- Benefits: High strength-to-weight ratio, precision, material diversity
4. Electronics
- Components: Connectors, heat sinks, structural parts
- Benefits: Miniaturization, complex geometries, high electrical conductivity
Table: Applications of Metal Injection Moulding (MIM)
Industry | Components | Benefits |
---|---|---|
Automotive | Gears, turbocharger parts, fuel injector nozzles | High strength, precision |
Medical | Surgical instruments, orthodontic brackets, implants | Biocompatibility, precision |
Aerospace | Engine components, fasteners, brackets | High strength-to-weight ratio |
Electronics | Connectors, heat sinks, structural parts | Miniaturization, high conductivity |
Specifications, Sizes, Grades, and Standards
When selecting materials for MIM, it’s essential to consider specifications, sizes, grades, and standards to ensure the final product meets the desired requirements.
Table: Specifications, Sizes, Grades, and Standards for MIM
Material | Specifications | Sizes | Grades | Standards |
---|---|---|---|---|
Stainless Steel 17-4 PH | ASTM A564 | Various | 630 | AMS 5643 |
Stainless Steel 316L | ASTM A276 | Various | 316L | AMS 5653 |
Titanium Ti-6Al-4V | ASTM B348 | Various | Grade 5 | AMS 4928 |
Iron Fe2Ni | ASTM A203 | Various | Class 2 | N/A |
Nickel Alloy 718 | ASTM B637 | Various | N07718 | AMS 5662 |
Copper C110 | ASTM B152 | Various | C11000 | N/A |
Cobalt-Chrome Alloy | ASTM F75 | Various | F75 | ISO 5832-4 |
Tungsten Heavy Alloy | ASTM B777 | Various | WHA | N/A |
Molybdenum TZM | ASTM B386 | Various | TZM | N/A |
Aluminum 6061 | ASTM B221 | Various | 6061 | AMS 4027 |
Suppliers and Pricing Details
Understanding the suppliers and pricing details is crucial for budgeting and sourcing materials for MIM projects.
Table: Suppliers and Pricing Details for MIM Materials
Material | Supplier | Pricing (per kg) |
---|---|---|
Stainless Steel 17-4 PH | Carpenter Technology | $25 – $30 |
Stainless Steel 316L | Sandvik | $20 – $25 |
Titanium Ti-6Al-4V | ATI Metals | $120 – $150 |
Iron Fe2Ni | Höganäs | $5 – $8 |
Nickel Alloy 718 | VDM Metals | $70 – $90 |
Copper C110 | KME | $8 – $10 |
Cobalt-Chrome Alloy | Straumann | $90 – $110 |
Tungsten Heavy Alloy | Global Tungsten & Powders | $60 – $80 |
Molybdenum TZM | Plansee | $45 – $60 |
Aluminum 6061 | Alcoa | $3 – $5 |
Comparing Pros and Cons of Metal Injection Moulding (MIM)
MIM has its advantages and limitations, making it suitable for some applications but not for others. Let’s compare its pros and cons.
Table: Advantages and Limitations of Metal Injection Moulding (MIM)
Advantages | Limitations |
---|---|
High precision | High initial tooling cost |
Complex geometries | Part size limitations |
Material efficiency | Secondary operations may be required |
Cost-effective for large volumes | Longer lead times for tooling |
Diverse material selection | Limited to certain materials |
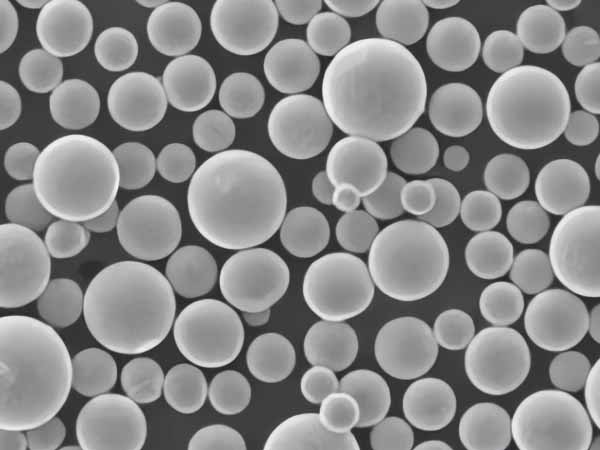
FAQ
Q: What is Metal Injection Moulding (MIM)?
A: Metal Injection Moulding (MIM) is a manufacturing process that combines metal powders with a binder to create a feedstock, which is then molded into complex shapes, debound, and sintered to form high-strength metal parts.
Q: What materials are commonly used in MIM?
A: Common materials include stainless steels (e.g., 17-4 PH, 316L), titanium alloys (e.g., Ti-6Al-4V), iron alloys, nickel alloys (e.g., Alloy 718), copper, cobalt-chrome alloys, tungsten heavy alloys, molybdenum alloys, and aluminum alloys (e.g., 6061).
Q: What are the advantages of MIM?
A: MIM offers high precision, the ability to create complex geometries, material efficiency, cost-effectiveness for large production runs, and a diverse selection of materials.
Q: What are the limitations of MIM?
A: MIM has high initial tooling costs, part size limitations, potential need for secondary operations, and longer lead times for tooling.
Q: Which industries benefit the most from MIM?
A: Industries such as automotive, medical, aerospace, and electronics benefit significantly from MIM due to its precision, material properties, and ability to produce complex parts.
Conclusion
Metal Injection Moulding (MIM) is a groundbreaking technology that combines the best of metalworking and plastic injection molding. It provides manufacturers with the ability to produce complex, high-precision metal parts efficiently and cost-effectively. By understanding the materials, processes, and applications of MIM, manufacturers can leverage this technology to innovate and improve their products.
MIM continues to evolve, offering new opportunities for various industries. Whether you’re in automotive, medical, aerospace, or electronics, exploring MIM could open doors to enhanced product capabilities and market competitiveness. Embrace the future of metal parts manufacturing with Metal Injection Moulding!