Overview
Minor gas-trapped pores powders, often referred to as metal powders, are crucial in various industrial applications. These powders are characterized by tiny gas pockets trapped within their structure, affecting their properties and performance. This guide delves into the specifics of minor gas-trapped pores powders, including their types, compositions, properties, applications, specifications, suppliers, and pricing. We will also explore the advantages and disadvantages of different metal powder models, offering detailed comparisons to help you make informed decisions.
What Are Minor Gas-Trapped Pores Powders?
Minor gas-trapped pores powders are fine particles of metal that contain small gas-filled cavities. These powders are produced through various manufacturing processes, including atomization, reduction, and electrolysis. The presence of gas pores can influence the density, strength, and overall behavior of the powders during application.
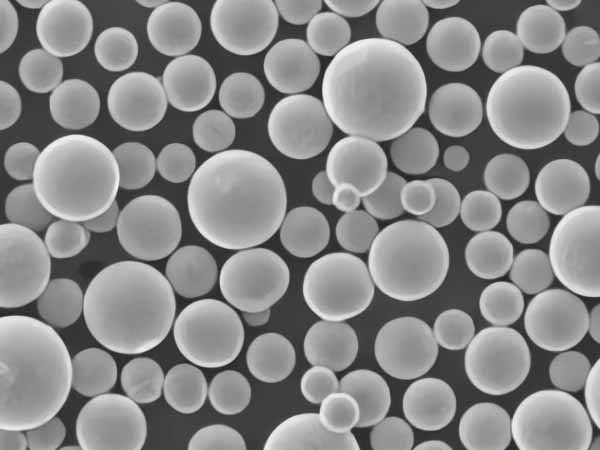
Types of Minor Gas-Trapped Pores Powders
Here’s a detailed look at some specific metal powder models with minor gas-trapped pores, including their descriptions:
Aluminum Powder (Grade 4047)
- Description: High silicon content for increased fluidity and reduced shrinkage.
- Properties: Lightweight, corrosion-resistant, excellent thermal conductivity.
2. Stainless Steel Powder (316L)
- Description: Low carbon content with added molybdenum for enhanced corrosion resistance.
- Properties: High strength, good ductility, excellent corrosion resistance.
3. Copper Powder (Cu-OFHC)
- Description: Oxygen-free high conductivity copper.
- Properties: Superior electrical and thermal conductivity, good formability.
4. Nickel Powder (Nickel 200)
- Description: Commercially pure nickel with excellent mechanical properties.
- Properties: High corrosion resistance, good thermal and electrical conductivity.
5. Titanium Powder (Ti-6Al-4V)
- Description: Titanium alloy with aluminum and vanadium for improved strength.
- Properties: High strength-to-weight ratio, excellent corrosion resistance.
6. Iron Powder (ASC100.29)
- Description: Atomized iron powder for high-density applications.
- Properties: High compressibility, good green strength, cost-effective.
7. Cobalt-Chromium Powder (CoCrMo)
- Description: Cobalt-based alloy powder for medical and dental applications.
- Properties: Biocompatible, high wear and corrosion resistance.
8. Magnesium Powder (AZ91D)
- Description: Magnesium alloy with aluminum and zinc for improved properties.
- Properties: Lightweight, good castability, moderate strength.
9. Tungsten Powder (W-Ni-Fe)
- Description: Tungsten heavy alloy powder for high-density applications.
- Properties: High density, good radiation shielding, high strength.
10. Zinc Powder (Zn-4Al)
- Description: Zinc alloy with aluminum for enhanced mechanical properties.
- Properties: Good corrosion resistance, moderate strength, easy to cast.
Composition and Properties
Type | Composition | Key Properties |
---|---|---|
Aluminum Powder 4047 | Aluminum, Silicon | Lightweight, corrosion-resistant, good thermal conductivity |
Stainless Steel 316L | Iron, Chromium, Nickel, Mo | High strength, ductility, corrosion resistance |
Copper Powder Cu-OFHC | Pure Copper | Superior electrical and thermal conductivity, formability |
Nickel Powder 200 | Pure Nickel | High corrosion resistance, good thermal and electrical conductivity |
Titanium Ti-6Al-4V | Titanium, Aluminum, Vanadium | High strength-to-weight ratio, corrosion resistance |
Iron Powder ASC100.29 | Pure Iron | High compressibility, good green strength |
Cobalt-Chromium CoCrMo | Cobalt, Chromium, Molybdenum | Biocompatible, high wear and corrosion resistance |
Magnesium AZ91D | Magnesium, Aluminum, Zinc | Lightweight, good castability, moderate strength |
Tungsten W-Ni-Fe | Tungsten, Nickel, Iron | High density, good radiation shielding, high strength |
Zinc Zn-4Al | Zinc, Aluminum | Good corrosion resistance, moderate strength, easy to cast |
Applications of Minor Gas-Trapped Pores Powders
Powder Type | Applications |
---|---|
Aluminum 4047 | Automotive, aerospace, electronics |
Stainless Steel 316L | Medical devices, marine equipment, food processing |
Copper Cu-OFHC | Electrical components, heat exchangers |
Nickel 200 | Chemical processing, aerospace, electronics |
Titanium Ti-6Al-4V | Aerospace, biomedical implants, sports equipment |
Iron ASC100.29 | Automotive parts, machinery, sintered components |
Cobalt-Chromium CoCrMo | Medical implants, dental applications |
Magnesium AZ91D | Automotive, aerospace, portable electronics |
Tungsten W-Ni-Fe | Radiation shielding, aerospace, military |
Zinc Zn-4Al | Die casting, corrosion protection, batteries |
Specifications, Sizes, Grades, and Standards
Powder Type | Specifications | Sizes | Grades | Standards |
---|---|---|---|---|
Aluminum 4047 | ASTM B928 | -325 mesh | 4047 | ASTM B928, AMS 4185 |
Stainless Steel 316L | ASTM A276 | -100 mesh | 316L | ASTM A276, ISO 5832-1 |
Copper Cu-OFHC | ASTM B170 | -200 mesh | OFHC | ASTM B170, ASTM F68 |
Nickel 200 | ASTM B160 | -150 mesh | 200 | ASTM B160, AMS 5553 |
Titanium Ti-6Al-4V | ASTM B348 | -325 mesh | Ti-6Al-4V | ASTM B348, ASTM F136 |
Iron ASC100.29 | MPIF 35 | -325 mesh | ASC100.29 | MPIF 35, ASTM B783 |
Cobalt-Chromium CoCrMo | ASTM F75 | -150 mesh | CoCrMo | ASTM F75, ISO 5832-4 |
Magnesium AZ91D | ASTM B93 | -325 mesh | AZ91D | ASTM B93, ASTM B94 |
Tungsten W-Ni-Fe | ASTM B777 | -200 mesh | W-Ni-Fe | ASTM B777, AMS-T-21014 |
Zinc Zn-4Al | ASTM B669 | -200 mesh | Zn-4Al | ASTM B669, ASTM B860 |
Suppliers and Pricing Details
Supplier | Powder Type | Price Range (per kg) |
---|---|---|
American Elements | Aluminum 4047, Titanium Ti-6Al-4V | $50 – $150 |
Höganäs AB | Iron ASC100.29, Stainless Steel 316L | $20 – $80 |
Stanford Advanced Materials | Nickel 200, Tungsten W-Ni-Fe | $80 – $200 |
Belmont Metals | Copper Cu-OFHC, Zinc Zn-4Al | $30 – $100 |
ATI Metals | Cobalt-Chromium CoCrMo, Magnesium AZ91D | $70 – $180 |
Comparing Pros and Cons
Powder Type | Advantages | Limitations |
---|---|---|
Aluminum 4047 | Lightweight, good thermal properties | Lower strength compared to other alloys |
Stainless Steel 316L | Excellent corrosion resistance, high strength | Higher cost, can be difficult to machine |
Copper Cu-OFHC | Exceptional electrical conductivity | Prone to oxidation, relatively soft |
Nickel 200 | High corrosion resistance, versatile | Expensive, heavy |
Titanium Ti-6Al-4V | High strength-to-weight ratio, biocompatible | Very expensive, challenging to work with |
Iron ASC100.29 | Cost-effective, good mechanical properties | Prone to rust without coating |
Cobalt-Chromium CoCrMo | High wear resistance, biocompatible | Very hard and brittle, expensive |
Magnesium AZ91D | Lightweight, good castability | Highly reactive, flammable in powder form |
Tungsten W-Ni-Fe | High density, excellent radiation shielding | Extremely heavy, hard to process |
Zinc Zn-4Al | Good corrosion resistance, easy to cast | Lower strength, not suitable for high-temperature applications |
Advantages of Minor Gas-Trapped Pores Powders
- Improved Mechanical Properties: The presence of gas pores can enhance the powder’s mechanical properties, making them suitable for high-stress applications.
- Lightweight Materials: Powders like aluminum and magnesium are lightweight, making them ideal for aerospace and automotive industries.
- Corrosion Resistance: Many of these powders, such as stainless steel and titanium, offer excellent corrosion resistance.
- Versatility: These powders can be used in a wide range of applications, from electronics to medical devices.
- Thermal and Electrical Conductivity: Copper and nickel powders provide superior conductivity for electronic applications.
Disadvantages of Minor Gas-Trapped Pores Powders
- Cost: Some powders, particularly those like titanium and nickel, can be expensive.
- Processing Challenges: Powders with high hardness, such as cobalt-chromium, can be difficult to process and machine.
- Reactivity: Powders like magnesium can be highly reactive and flammable in certain conditions.
- Density Issues: High-density powders like tungsten can be extremely heavy, posing handling and processing challenges.
- Oxidation: Powders such as copper are prone to oxidation, which can affect their performance over time.
Optimizing Minor Gas-Trapped Pores Powders for Applications
When selecting minor gas-trapped pores powders for specific applications, consider the following factors:
Application Requirements
- Mechanical Properties: Ensure the powder meets the required strength, ductility, and wear resistance.
- Environmental Conditions: Consider corrosion resistance and thermal stability.
- Weight Considerations: Choose lightweight powders for applications where weight is critical, such as aerospace.
Manufacturing Processes
- Powder Metallurgy: Suitable for complex shapes and high-volume production.
- Additive Manufacturing: Ideal for customized parts and prototypes.
- Coating Applications: Powders can be used for protective and functional coatings.
Cost and Availability
- Budget Constraints: Balance cost with performance requirements.
- Supplier Reliability: Choose reputable suppliers to ensure consistent quality.
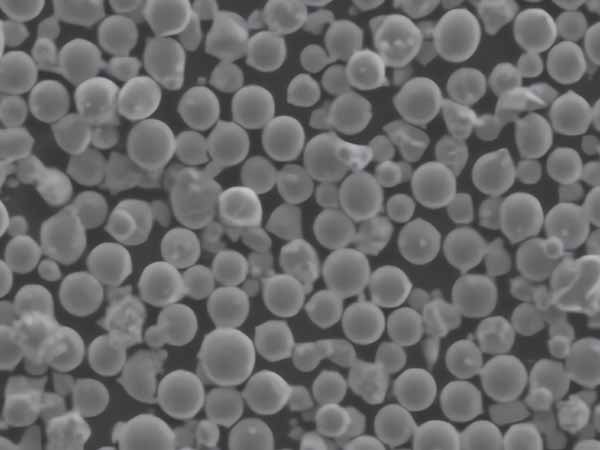
FAQs
Question | Answer |
---|---|
What are minor gas-trapped pores powders used for? | They are used in various industries, including aerospace, automotive, electronics, and medical devices. |
Why are gas pores important in metal powders? | Gas pores can enhance mechanical properties, reduce weight, and influence the behavior of the powders during application. |
Which metal powder is best for corrosion resistance? | Stainless steel 316L and titanium Ti-6Al-4V offer excellent corrosion resistance. |
How do I choose the right metal powder for my application? | Consider the mechanical properties, environmental conditions, weight, and cost requirements. |
Are these powders safe to handle? | Most powders are safe with proper handling, but some, like magnesium, can be reactive and require careful management. |
Conclusion
Minor gas-trapped pores powders are versatile materials with a wide range of applications. Understanding their types, properties, and applications can help you select the right powder for your needs. Whether you’re looking for lightweight options like aluminum or high-density materials like tungsten, there’s a minor gas-trapped pores powder to meet your requirements. Always consider the specific properties and limitations of each powder type to optimize performance and cost-efficiency in your applications.