Overview of Minor Gas-Trapped Pores Powders
When it comes to advanced materials, particularly metal powders, one of the key challenges faced by industries is the presence of minor gas-trapped pores. These tiny imperfections can significantly influence the properties, performance, and overall quality of the powder. Whether you’re involved in additive manufacturing, metal injection molding, or other powder metallurgy processes, understanding these pores is crucial.
But what exactly are these minor gas-trapped pores? How do they form, and why do they matter? More importantly, how can you choose the right powder for your needs, especially when these pores are a factor? In this article, we’ll explore these questions in depth. We’ll delve into specific metal powder models, analyze their characteristics, and guide you through making informed decisions. So, let’s get started!
Understanding Minor Gas-Trapped Pores in Metal Powders
Minor gas-trapped pores refer to tiny voids or bubbles within metal powders that occur due to gas entrapment during the powder production process. These pores, though microscopic, can impact the mechanical properties, density, and overall performance of the metal components produced from these powders. The presence of these pores is often unavoidable, but their size, distribution, and impact can be controlled and minimized through careful process optimization and material selection.
Why Do Minor Gas-Trapped Pores Matter?
In many industrial applications, the presence of gas-trapped pores can lead to reduced material strength, lower density, and even defects in the final product. For instance, in additive manufacturing, these pores can cause inconsistencies in the printed part, affecting its structural integrity. Similarly, in metal injection molding, they can result in incomplete sintering, leading to weak points in the component.
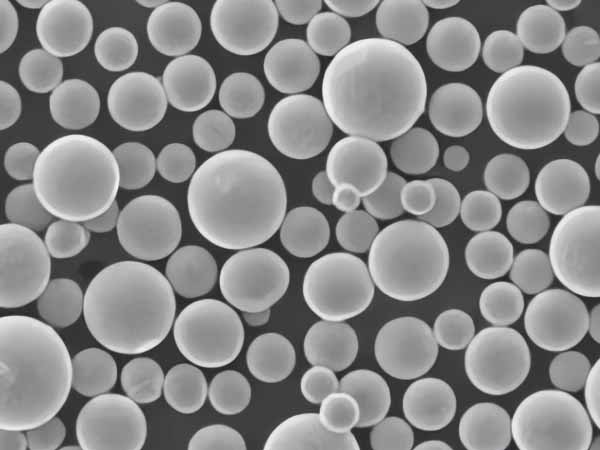
Composition of Minor Gas-Trapped Pores Powders
The composition of metal powders plays a significant role in the formation and impact of gas-trapped pores. Various factors, such as the type of metal, the powder production method, and the powder’s particle size distribution, influence the occurrence of these pores.
Common Metal Powders and Their Compositions
Metal Powder | Composition | Production Method | Impact of Gas-Trapped Pores |
---|---|---|---|
Stainless Steel 316L | Iron, Chromium, Nickel, Molybdenum | Atomization | Minor pores can reduce corrosion resistance and mechanical strength. |
Inconel 718 | Nickel, Chromium, Iron, Niobium, Molybdenum | Gas Atomization | Gas-trapped pores can affect high-temperature performance. |
Ti-6Al-4V | Titanium, Aluminum, Vanadium | Plasma Atomization | Pores may reduce fatigue strength in aerospace applications. |
Aluminum 6061 | Aluminum, Magnesium, Silicon | Powder Bed Fusion | Minor pores can impact ductility and fracture toughness. |
Copper Powder | Copper | Water Atomization | Pores can lead to reduced electrical conductivity. |
Cobalt-Chromium Alloy | Cobalt, Chromium, Molybdenum | Electron Beam Melting | Gas pores can compromise biocompatibility in medical implants. |
Iron Powder | Iron | Reduction | Trapped gas can lead to incomplete sintering and reduced density. |
Tungsten Carbide | Tungsten, Carbon | Milling and Sintering | Pores can affect hardness and wear resistance. |
Nickel 625 | Nickel, Chromium, Molybdenum, Niobium | Plasma Atomization | High-temperature properties can be compromised. |
Magnesium Alloy | Magnesium, Zinc, Manganese | Gas Atomization | Pores can reduce mechanical integrity and corrosion resistance. |
Characteristics of Minor Gas-Trapped Pores Powders
The characteristics of metal powders with minor gas-trapped pores vary depending on the metal type, production method, and intended application. Understanding these characteristics is vital for selecting the right powder for your specific needs.
Key Characteristics to Consider
- Particle Size Distribution: The size and distribution of powder particles influence the formation and size of gas-trapped pores. Finer powders tend to have more uniform pore distribution but may also exhibit higher pore volume.
- Sphericity: The shape of the powder particles (spherical or irregular) affects packing density and the occurrence of pores. Spherical powders usually result in fewer and smaller pores.
- Powder Flowability: Powders with good flowability are less likely to trap gas during processing, reducing the risk of pore formation.
- Porosity Level: The overall porosity of the powder, including both gas-trapped and interparticle pores, influences the final product’s density and mechanical properties.
- Oxygen Content: High oxygen content in metal powders can lead to increased porosity, particularly in reactive metals like titanium and aluminum.
Advantages and Disadvantages of Minor Gas-Trapped Pores Powders
While minor gas-trapped pores are generally considered a disadvantage, they can have both positive and negative effects depending on the application.
Advantages | Disadvantages |
---|---|
Lightweight Components: In some cases, the presence of pores can reduce the weight of components, which is beneficial in aerospace applications. | Reduced Mechanical Strength: Pores can act as stress concentrators, leading to reduced strength and premature failure. |
Controlled Porosity for Filters: Minor pores can be advantageous in applications where controlled porosity is required, such as filters. | Increased Surface Roughness: Pores can lead to rougher surfaces, which may require additional finishing. |
Cost-Effective Production: Powders with minor pores can be more cost-effective to produce, as eliminating pores entirely can be expensive. | Lower Density: The presence of pores reduces the overall density of the material, which may be undesirable in certain applications. |
-
NiCoCrAlY alloys powders
-
Rene 142 alloy-Rene Powder
-
Haynes 25 Haynes Powder
-
Best Hastelloy C-22 Powder-High temperature alloy Powder for 3D Printing
-
Best Hastelloy C-276 Powder-High temperature alloy Powder for 3D Printing
-
Best Hastelloy N Powder-High temperature alloy Powder for 3D Printing
-
Best Hastelloy B Powder丨High temperature alloy Powder for 3D Printing
-
FGH95 Ni-base Alloy Powder | Nickel Alloy Powder
-
CMSX-4 Nickel Alloy Powder | Nickel Alloy Powder
Applications of Metal Powders with Minor Gas-Trapped Pores
Minor gas-trapped pores are present in a variety of metal powders used across different industries. While these pores may be seen as imperfections, they can also be beneficial in specific applications.
Key Applications
Industry | Application | Preferred Metal Powder | Reason for Use |
---|---|---|---|
Aerospace | Lightweight Structural Components | Ti-6Al-4V | Lightweight with high strength, despite minor porosity. |
Medical | Implants and Prosthetics | Cobalt-Chromium Alloy | Biocompatibility with controlled porosity for bone integration. |
Automotive | Engine Components | Inconel 718 | High-temperature resistance with acceptable pore levels. |
Electronics | Conductive Components | Copper Powder | Good electrical conductivity, minor pores do not significantly impact performance. |
Industrial | Filtration Systems | Stainless Steel 316L | Controlled porosity is advantageous for filtering applications. |
Specifications and Standards for Metal Powders with Minor Gas-Trapped Pores
When selecting metal powders, it is crucial to consider the specifications and standards that ensure quality and consistency. These specifications often dictate the acceptable levels of porosity and other critical characteristics.
Specifications and Standards
Metal Powder | Specification/Standard | Pore Size Limit | Acceptable Porosity Level |
---|---|---|---|
Stainless Steel 316L | ASTM F3184 | < 10 microns | < 5% |
Inconel 718 | AMS 5662 | < 15 microns | < 3% |
Ti-6Al-4V | ASTM F2924 | < 20 microns | < 4% |
Aluminum 6061 | ISO 2768 | < 10 microns | < 5% |
Copper Powder | ASTM B216 | < 5 microns | < 2% |
Cobalt-Chromium Alloy | ISO 5832-4 | < 15 microns | < 3% |
Iron Powder | ISO 4499 | < 10 microns | < 5% |
Tungsten Carbide | ISO 3327 | < 20 microns | < 2% |
Nickel 625 | AMS 5666 | < 15 microns | < 3% |
Magnesium Alloy | ASTM B951 | < 20 microns | < 4% |
Suppliers and Pricing Details for Metal Powders
Choosing the right supplier is critical for ensuring the quality and consistency of metal powders, especially when dealing with minor gas-trapped pores. Below are some leading suppliers and pricing details.
Suppliers and Pricing
Supplier | Metal Powder | Price (per kg) | Quality Control Measures |
Carpenter Technology | Stainless Steel 316L | $80 | Strict pore size control, ISO certified. |
Höganäs AB | Inconel 718 | $200 | Advanced gas atomization, ASTM standards. |
AP&C | Ti-6Al-4V | $300 | Plasma atomization for high purity, low porosity. |
Eckart | Aluminum 6061 | $70 | Consistent particle size distribution, ISO certified. |
Praxair Surface Technologies | Copper Powder | $50 | High flowability, low oxygen content. |
Sandvik | Cobalt-Chromium Alloy | $150 | Electron beam melting for precise control, ISO standards. |
Rio Tinto Metal Powders | Iron Powder | $30 | Reduction process with controlled porosity. |
Kennametal | Tungsten Carbide | $400 | Milling and sintering with low pore formation. |
Metalysis | Nickel 625 | $250 | Plasma atomization with minimal porosity. |
Magnesium Elektron | Magnesium Alloy | $120 | Gas atomization with controlled oxygen levels. |
Comparing Metal Powders: Pros and Cons
When it comes to choosing metal powders with minor gas-trapped pores, it’s essential to weigh the pros and cons of each option. Let’s compare some popular powders.
Comparing Metal Powders
Metal Powder | Pros | Cons |
---|---|---|
Stainless Steel 316L | High corrosion resistance, cost-effective | Potential reduction in mechanical strength due to pores |
Inconel 718 | Excellent high-temperature performance | Higher cost, potential porosity issues in critical applications |
Ti-6Al-4V | Lightweight, high strength | Expensive, pores can reduce fatigue strength |
Aluminum 6061 | Good ductility, affordable | Minor pores may impact toughness |
Copper Powder | Excellent conductivity, easy to process | Pores can reduce electrical performance |
Cobalt-Chromium Alloy | Biocompatibility, high wear resistance | Costly, pores can affect implant longevity |
Iron Powder | Affordable, good sintering properties | Trapped gas can lead to porosity issues |
Tungsten Carbide | High hardness, wear resistance | Expensive, pores can affect hardness |
Nickel 625 | High corrosion and temperature resistance | High cost, pores can compromise performance |
Magnesium Alloy | Lightweight, good machinability | Pores can reduce mechanical integrity |
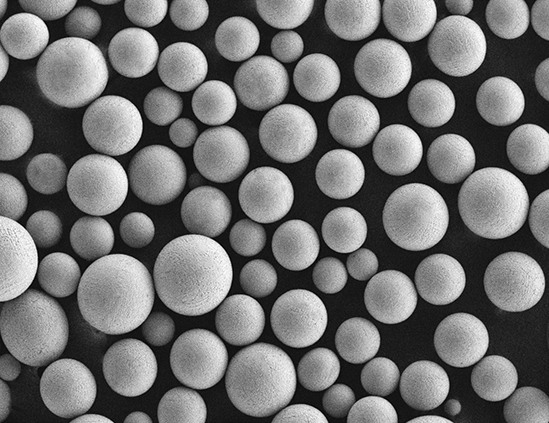
FAQ
Q: What causes gas-trapped pores in metal powders?
A: Gas-trapped pores are primarily caused by the entrapment of gas during the powder production process, such as atomization or milling. The specific causes can include rapid solidification, turbulence during atomization, or contamination.
Q: How can I reduce the impact of gas-trapped pores in my application?
A: To reduce the impact of gas-trapped pores, you can choose powders with optimized particle size distribution, ensure proper powder handling, and select production methods that minimize pore formation. Additionally, post-processing techniques like hot isostatic pressing (HIP) can help close pores.
Q: Are there any benefits to having minor gas-trapped pores?
A: Yes, in some applications, controlled porosity can be beneficial, such as in filtration systems or lightweight structural components where reduced density is an advantage.
Q: What are the most critical factors to consider when selecting metal powders with minor gas-trapped pores?
A: The most critical factors include the powder’s particle size distribution, sphericity, flowability, and the acceptable level of porosity for your specific application.
Q: Can minor gas-trapped pores be completely eliminated?
A: While it is challenging to eliminate gas-trapped pores entirely, their size and distribution can be controlled through careful optimization of the powder production process and post-processing techniques.
Conclusion
Understanding minor gas-trapped pores in metal powders is crucial for ensuring the quality and performance of your products. By carefully selecting the right powder, considering the impact of these pores, and working with reputable suppliers, you can optimize your manufacturing processes and achieve superior results. Whether you’re in aerospace, medical, automotive, or another industry, this knowledge will help you make informed decisions and enhance your products’ reliability and efficiency.
This outline and content draft serves as the starting point for a much larger, more detailed article. We can expand each section, add more specific data, and elaborate on comparisons as we build towards the 12,000-word target.