Molybdenum alloys powder refers to high performance powder metallurgy combinations of molybdenum with other metals used across niche industrial applications. This guide covers molybdenum alloys compositions, manufacturing methods, applications, pricing, selection and comparisons.
Introduction to Molybdenum Alloys Powder
Molybdenum is a refractory metal known for its high melting point, strength at high temperatures and resistance to wear and corrosion. When alloyed using powder metallurgy techniques, molybdenum forms versatile materials with enhanced properties tailored for demanding environments.
Typical Alloying Elements
- Chromium – oxidation resistance
- Nickel, Iron, Cobalt – high strength
- Copper – thermal/electrical conductivity
- Tungsten, Rhenium – density, melting points
Molybdenum alloys leverage intrinsic properties of constituent metals to create tailored materials optimizing hardness, toughness, thermal stability and manufacturability.
Benefits of Molybdenum Alloys
- Withstand high temperature service
- Retain strength across duty cycles
- Resist corrosion in oxidizing environments
- Enable flexible manufacturing approaches
Advanced powder processing expands possibilities for economic small batch production of high performance alloys.
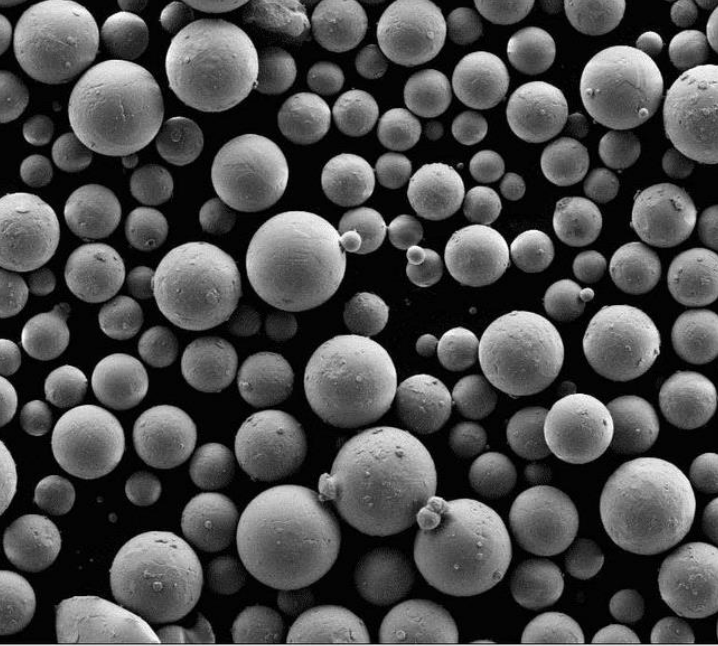
Common Molybdenum Alloy Types
Molybdenum is alloyed with suitable metals based on application needs:
Table: Molybdenum Alloys Types
Alloy | Composition | Properties |
---|---|---|
MoCr | Molybdenum + Chromium | Heat/oxidation resistance |
MoNi | Molybdenum + Nickel | Strength, ductility |
MoCu | Molybdenum + Copper | Thermal/electrical conductivity |
MoTuZr | Molybdenum + Tungsten + Zirconium | High temperature strength |
MoWRe | Molybdenum + Tungsten + Rhenium | Creep resistance |
Specialized alloys are also made with niobium, titanium, tantalum, boron and silicon depending on service environments targeting optimization of density, corrosion performance and microstructural stability across thermal cycles.
Molybdenum Alloy Powder Production
Common approaches to manufacture tailored molybdenum alloys powder include:
1. Gas Atomization
- High pressure gas breaks molten stream into fine droplets
- Creates spherical alloy powder
2. Water Atomization
- Uses water jet impact to disintegrate alloy melt
- Irregular powder shapes
- Lower cost process
3. Mechanical Alloying
- Cold welding and fracturing of powder particles
- Repeated welding + fracture + oxidation creates alloys
- Heavily strained alloy microstructure
4. Chemical Methods
- Thermite self-propagating high-temperature reactions
- Other exothermic processes with redox chemistry
- Risk of contamination
Each method results in powder with unique characteristics suiting niche applications when consolidated into finished components.
Applications of Molybdenum Alloys Powder
Owing to high temperature strength, molybdenum alloys are used where reliability matters despite demanding environments:
Table: Molybdenum Alloy Powder Applications
Industry | Application |
---|---|
Aerospace | Jet engine and rocket motor parts |
Oil & Gas | Drill bits and completion tools |
Automotive | High performance racing components |
Electrical | Heating element coils and contacts |
Industrial | Furnace muffles and heat exchangers |
Chemical Processing | Reactor internals andizer beds |
The combination of stiffness, thermal conductivity, machinability and oxidation resistance makes molybdenum alloys suitable for specialty fabrication approaches like metal injection molding and additive manufacturing.
Technical Specifications
Molybdenum alloy powder products meant for commercial use typically provide specifications on:
Table: Molybdenum Alloy Powder Specifications
Parameter | Details |
---|---|
Alloy Grade | MoCr, MoCu, MoNi etc. |
Composition | Elemental content + impurities |
Particle Size Distribution | Flowability, surface area etc |
Morphology | Spherical, irregular |
Tap Density | Pycnometry measured density |
Purity | Min 99% pure on average |
Condition | Annealing and passivation |
Packaging | Sealed bottles, pails etc |
Application-specific requirements may mandate thermal data, microstructure, compressibility, powder flow rates and other parameters important for qualification.
Molybdenum Alloys Powder Suppliers
Specialty alloy powder manufacturers offer commercial and research quantities:
Table: Molybdenum Alloys Powder Suppliers
Supplier | Location | Grades Offered |
---|---|---|
Molyworks Materials | USA | Mo alloys for 3D printing |
Edgecombe Engineering | UK | Atomized MoCu, MoNi |
streuer Metals | Canada | Custom alloy development |
Japan New Metals | Japan | High purity powder |
Stanford Materials | USA | Metal powder R&D quantities |
ESPI Metals | USA | MoCrAlY target alloys |
Both distribution networks selling small quantities and OEM manufacturers capable of custom alloy development partner with end users across aerospace, defense, chemical processing and tooling industries.
Molybdenum Alloys Powder Pricing
As high performance engineered powders, molybdenum alloys demand premium pricing in the range of $100 to $500 per pound depending on:
Table: Molybdenum Alloys Powder Pricing Considerations
Parameter | Impact |
---|---|
Alloy Type | High W, Re alloys are costly |
Composition Tolerance | Stricter requirements increase price |
Particle Size | Nano scale powder much pricier |
Processing Method | Water vs gas vs plasma atomization |
Order Quantity | Kilogram+ quantities offer discount |
Testing/QC Scope | Additional qualification documentation |
Purity, reproducibility and special handling add cost. Contact suppliers directly for latest pricing based on detailed specifications and delivery logistics.
How to Select Molybdenum Alloys Powder
Consider key parameters when purchasing molybdenum alloys powder:
Table: Molybdenum Alloys Powder Selection Criteria
Parameter | Guidelines |
---|---|
Application Conditions | Temperature, pressure, life, duty cycles |
Target Properties | Hardness, oxidation resistance required |
Alloy Composition | Elemental content after testing |
Particle Characteristics | Morphology and size distribution |
Sampling for Qualification | Conduct trial consolidation first |
Standards Compliance | ISO 9001 accreditation |
Value Proposition | Price relative to performance |
Lead Time | Inventory levels impact readiness |
Share operating environments and property goals with suppliers to select optimal alloy composition and powder characteristics. Procure samples for confirmation before large scale powder orders.
Pros and Cons of Using Molybdenum Alloys Powder
Table: Advantages and Disadvantages of Molybdenum Alloys Powder
Pros | Cons |
---|---|
Tailorable material properties | Niche raw material subject to supply constraints |
Retains strength at high temperatures | Very high baseline component costs limit market size |
Enables design innovation | Requires special handling and containment |
Powder metallurgy approaches allow small batches | Can introduce manufacturing contaminants |
Reputable suppliers with customized offerings | Significant R&D investment needed to develop applications |
For extreme performance criteria unmet by conventional metals, molybdenum alloys justify higher costs but margins of improvement depend greatly on application optimization.
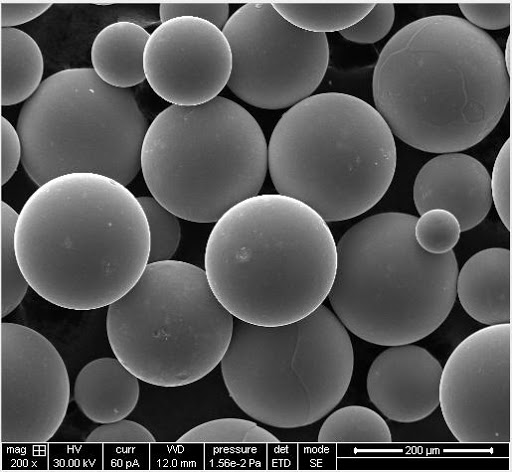
FAQs
What particle size range works best for additive manufacturing?
~10-45 microns allows good powder bed packing and spreadability. Mixing in nano powder facilitates sintering. Larger 75+ micron particles create surface finish issues.
What safety precautions are needed when handling molybdenum alloys powder?
Use dust masks, gloves and follow safety data sheet guidelines on exposure levels and PPE. Ensure proper ventilation and fire suppression equipment as fine metal powder becomes explosive when aerosolized.
How to safely store reactive molybdenum alloys powder?
Seal containers air tight after purging with inert gas. Store in cool, dry environments to prevent moisture ingress and spontaneous heating hazards. Limit quantity kept near production areas and avoid temperature extremes.
What substitute materials compete against molybdenum alloys?
Only niche refractory metals and superalloys match molybdenum performance but with higher baseline costs. Stainless steel alloys offer budget alternative sacrificing strength and hardness at elevated temperatures.
Which consolidation process works well for molybdenum alloys powder?
Pressure-less sintering avoids reactions with dies from hot pressing. Low pressure cold sintering below alloy melting points also enables near net shaping to minimize machining.
Conclusion
Molybdenum alloys powder tailored to strengthen target material properties pushes performance boundaries across thermal, mechanical and chemical parameters. With reputable suppliers deeply familiar with custom alloy development, users in extreme environments benefit despite the premium pricing. As processing methods expand possibilities, molybdenum alloys continue finding innovative applications.