Imagine a world where complex metal parts could be crafted layer by layer, where worn-out surfaces could be revitalized with a metallic kiss, and where the strength and resilience of a material could be precisely tailored. Enter the fascinating realm of nickel-based powders, the unassuming heroes behind a multitude of cutting-edge industrial applications.
Nickel-based powders are finely divided metallic particles, typically ranging in size from a few micrometers to hundreds of micrometers. Due to their unique properties, these powders find themselves at the forefront of various manufacturing techniques, revolutionizing the way we create and enhance metal components.
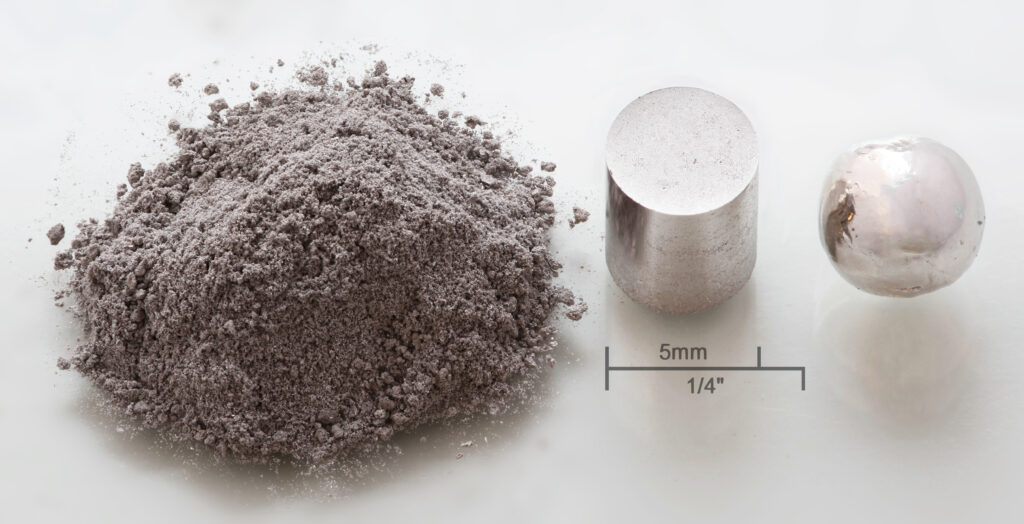
Nickel-Based Powders: A Compositional Kaleidoscope
Nickel, a versatile and robust metal, forms the foundation of these powders. However, to achieve specific properties like enhanced strength, corrosion resistance, or high-temperature performance, nickel is often alloyed with other elements. This creates a spectrum of nickel-based powder compositions, each catering to distinct industrial needs.
Here’s a glimpse into some of the most commonly encountered nickel-based powder types, along with their key characteristics:
Nickel-Based Powder Type | Composition | Key Characteristics |
---|---|---|
Pure Nickel | Ni (min. 99.5%) | High ductility, excellent electrical conductivity, good corrosion resistance |
Nickel-Chromium | Ni-Cr | Enhanced strength, good oxidation resistance at elevated temperatures |
Nickel-Iron | Ni-Fe | Magnetic properties, suitable for soft magnetic applications |
Inconel 625 | Ni-Cr-Mo-Fe | Exceptional high-temperature strength, resistance to various corrosive environments |
Inconel 718 | Ni-Cr-Fe-Nb | High strength-to-weight ratio, excellent weldability, ideal for aerospace applications |
Monel 400 | Ni-Cu | Superior corrosion resistance, particularly in saltwater environments |
Hastelloy C-276 | Ni-Cr-Mo-W | Exceptional resistance to a wide range of corrosive media, ideal for chemical processing applications |
INVAR | Ni-Fe | Ultra-low thermal expansion coefficient, crucial for applications requiring dimensional stability with temperature changes |
Atomized Nickel Aluminum (ANA) | Ni-Al | High wear resistance, excellent thermal conductivity, used for coatings and pistons |
Nickel Titanium (NiTi) | Ni-Ti | Shape memory effect, superelasticity, used for medical devices and actuators |
Understanding the Nuances: A Deeper Dive
Each of these nickel-based powder types boasts a unique set of properties that make it ideal for specific applications. Let’s delve deeper into some noteworthy examples:
- Pure Nickel Powders: Imagine crafting intricate electronic components with exceptional conductivity. Pure nickel powders, with their unmatched electrical conductivity, are the perfect choice. Their high ductility makes them ideal for applications requiring formability, like thin-walled tubes.
- Nickel-Chromium Powders: Think jet engines roaring through the sky. Nickel-chromium powders, with their enhanced strength and resistance to oxidation at high temperatures, are the backbone of many aerospace components. They can withstand the intense heat generated by jet engines, ensuring their safe and reliable operation.
- Inconel Powders: Inconel 625 and Inconel 718 are two superstars in the nickel-based powder world. Inconel 625, with its exceptional high-temperature strength and resistance to harsh environments, finds applications in chemical processing plants and nuclear reactors. Inconel 718, on the other hand, takes the cake for its incredible strength-to-weight ratio and weldability. This makes it a favorite for crafting lightweight yet robust aerospace components.
- Monel Powders: Monel 400, with its unwavering resistance to corrosion, particularly in saltwater environments, is a lifesaver for marine applications. Ship propellers, shafts, and other components exposed to the harsh embrace of the sea are often protected by coatings made from Monel powders.
This is just a taste of the diverse applications enabled by nickel-based powders. We’ll explore these applications in more detail in the following sections.
A Multifaceted Marvel: Unveiling the Applications of Nickel-Based Powders
Nickel-based powders transcend the boundaries of a single application. Their versatility allows them to shine in various sectors, each offering unique benefits. Here’s a breakdown of some of the most prominent applications:
1. Nickel-Based Powder in Powder Metallurgy
Powder metallurgy (PM) is a fascinating process that utilizes metal powders to create complex shapes. Nickel-based powders, particularly pure nickel and nickel-chromium alloys, play a crucial role in PM.
Here’s how it works:
- The nickel-based powder is precisely shaped into the desired form using techniques like die compaction or injection molding.
- The compacted powder is then subjected to high pressure and heat in a sintering furnace. This process fuses the individual powder particles together, forming a solid and robust metal component.
The Advantages of PM using Nickel-Based Powders:
- Complex Geometries: Nickel-based powders excel at creating intricate shapes that are difficult or impossible to achieve with traditional machining techniques. This opens doors for innovative part designs.
- Near-Net Shape Manufacturing: PM allows for the creation of parts with minimal material waste. This translates to cost savings and reduced environmental impact.
- Material Efficiency: Nickel-based powders with specific properties can be chosen for each application, optimizing material usage and performance.
- Tailored Properties: By controlling the powder composition and the sintering process, manufacturers can tailor the properties of the final component, such as strength, porosity, and wear resistance.
Applications of PM with Nickel-Based Powders:
- Automotive Parts: Gears, connecting rods, and other high-stress components can be manufactured using PM with nickel-based powders for their exceptional strength and wear resistance.
- Aerospace Components: PM with nickel-based powders is used to create lightweight yet robust parts for aircraft engines and landing gear, leveraging the high strength-to-weight ratio of these materials.
- Electronic Components: The high electrical conductivity of pure nickel powders makes them ideal for creating electrical contacts and connectors used in various electronic devices.
- Medical Devices: PM with biocompatible nickel-based powders is finding increasing applications in the creation of orthopedic implants and other medical devices.
2. Nickel-Based Powders for Surface Coatings
Nickel-based powders aren’t just limited to creating new components; they can also breathe new life into existing ones. Thermal spraying techniques, like plasma spraying and high-velocity oxy-fuel (HVOF) spraying, utilize nickel-based powders to create protective coatings on various surfaces.
The Benefits of Thermal Spraying with Nickel-Based Powders:
- Enhanced Wear Resistance: Nickel-based powders like Inconel 625 and ANA (Nickel Aluminum) offer superior wear resistance, protecting components from abrasion, erosion, and other wear mechanisms. This extends the lifespan of critical parts in industries like mining, oil and gas, and power generation.
- Improved Corrosion Resistance: Monel 400 and Hastelloy C-276 powders provide exceptional protection against corrosion, safeguarding components exposed to harsh environments like chemical plants and marine applications.
- Thermal Barrier Properties: Some nickel-based powders offer thermal insulation capabilities, shielding components from extreme temperatures. This finds applications in gas turbine components and other high-heat environments.
Applications of Thermal Spraying with Nickel-Based Powders:
- Gas Turbine Components: Thermal sprayed coatings made from nickel-chromium and Inconel powders protect turbine blades and other components from the detrimental effects of high temperatures and hot gas erosion.
- Pumps and Valves: Components in these applications are often exposed to corrosive fluids. Thermal spraying with Monel or Hastelloy powders safeguards them against corrosion and extends their service life.
- Repair and Rebuilding: Worn-out or damaged shafts, gears, and other components can be revitalized using thermal spraying with nickel-based powders. This offers a cost-effective alternative to complete component replacement.
3. Nickel-Based Powders for 3D Printing
The world of 3D printing has been revolutionized by the introduction of nickel-based powders. Additive manufacturing techniques like selective laser melting (SLM) and electron beam melting (EBM) utilize these powders to create complex, three-dimensional metal parts.
The Advantages of 3D Printing with Nickel-Based Powders:
- Design Freedom: 3D printing allows for the creation of intricate geometries that are impossible with traditional manufacturing methods. This opens doors for innovative and lightweight designs.
- Rapid Prototyping: Nickel-based powders facilitate the rapid creation of functional prototypes, accelerating the development process for new products.
- Mass Customization: 3D printing with nickel-based powders enables the production of customized parts in small batches, catering to specific needs.
Applications of 3D Printing with Nickel-Based Powders:
- Aerospace Components: The ability to create lightweight and high-strength components using Inconel and other nickel-based powders makes 3D printing ideal for aerospace applications.
- Medical Implants: Customized prosthetics and other medical implants can be created using biocompatible nickel-based powders, offering patients improved functionality and
- Molds and Dies: Complex molds and dies for various manufacturing processes can be 3D printed using nickel-based powders, reducing lead times and production costs.
4. Other Applications of Nickel-Based Powders
Beyond the aforementioned applications, nickel-based powders find use in various other sectors:
- Brazing: Nickel-based powders are used as filler metals in brazing processes, joining dissimilar metals to create strong and reliable bonds.
- Electrodes: Specific nickel-based powders can be used to manufacture electrodes for batteries and other electrochemical applications.
- Catalysts: Certain nickel-based powders exhibit catalytic properties, making them ideal for use in chemical reactions.
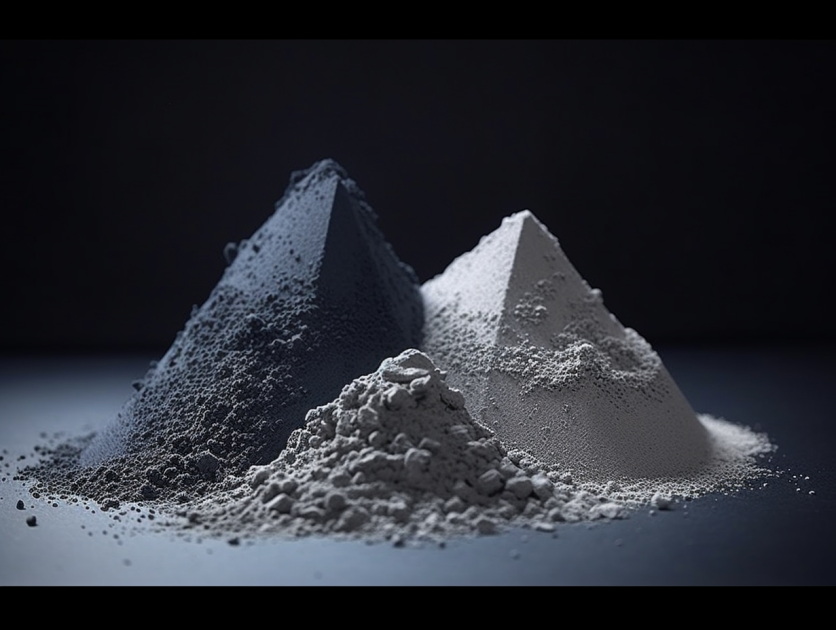
A Look at Nickel-Based Powder Properties
Nickel-based powders come in a variety of specifications, catering to diverse application needs. Here’s a breakdown of some key parameters to consider:
- Particle Size Distribution: The size and distribution of the powder particles significantly impact the final component’s properties. Finer powders generally lead to denser and smoother surfaces, while coarser powders may offer improved flowability during processing.
- Powder Flowability: The ease with which the powder flows is crucial for smooth operation in various manufacturing techniques. Powders with good flowability ensure consistent application and minimize processing issues.
- Sintering Characteristics: The behavior of the powder during the sintering process determines the final properties of the component. Factors like sintering temperature and atmosphere play a vital role.
- Chemical Composition: As discussed earlier, the specific alloying elements in the nickel-based powder significantly influence its properties like strength, corrosion resistance, and high-temperature performance.
Standards and Regulations
The manufacturing and use of nickel-based powders are often governed by specific industry standards and regulations. These standards ensure the quality and consistency of the powders, as well as their safety for use in various applications. Some prominent standards include:
- ASTM International (ASTM) standards, such as ASTM B880 for nickel powder and ASTM B939 for amorphous nickel-based alloy powders.
- Military specifications (Mil-Specs) for aerospace and defense applications.
- AMS (Aerospace Material Specifications) standards established by SAE International.
Suppliers and Pricing
Nickel-based powders are readily available from a multitude of global suppliers. The pricing of these powders can vary depending on several factors, including:
- Powder type and composition: More complex alloys with specific properties tend to be more expensive than pure nickel powders.
- Particle size and distribution: Finely milled powders typically command a higher price compared to coarser powders.
- Quantity: Bulk purchases often benefit from economies of scale, leading to lower per-unit costs.
Here are some resources to help you locate suppliers of nickel-based powders:
- Online directories of metal powder manufacturers and distributors.
- Industrial trade publications and websites.
- Networking with companies involved in powder metallurgy, thermal spraying, and 3D printing technologies.
the Pros and Cons of Nickel-Based Powders
While nickel-based powders offer a plethora of advantages, it’s essential to consider their limitations as well.
Advantages:
- Exceptional Properties: Nickel-based powders boast a combination of strength, corrosion resistance, high-temperature performance, and other desirable properties.
- Design Flexibility: These powders enable the creation of complex geometries and near-net shape components, pushing the boundaries of traditional manufacturing.
- Material Efficiency: PM and other techniques using nickel-based powders minimize material waste, promoting sustainability.
- Tailored Performance: By selecting the appropriate powder composition and processing techniques, manufacturers can achieve specific properties for their desired applications.
Disadvantages:
- Cost: Nickel-based powders can be more expensive than some conventional materials, particularly for complex alloy compositions and finer particle sizes.
- Processing Complexity: Techniques like PM, thermal spraying, and 3D printing using nickel-based powders may require specialized equipment and expertise, adding to the production cost.
- Safety Considerations: Nickel dust can pose health risks if not handled appropriately. Proper safety protocols are essential when working with nickel-based powders.
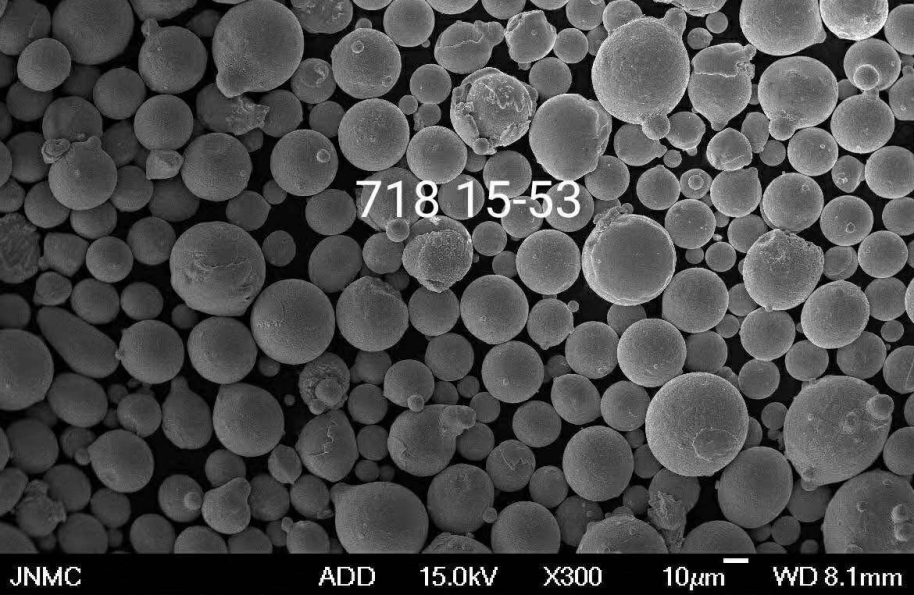
FAQ
Q: Are nickel-based powders safe to use? (Continued)
A: Nickel dust can be harmful if inhaled. However, following proper safety protocols like using appropriate ventilation systems and personal protective equipment (PPE) like respirators can significantly minimize risks.
Q: What are some of the environmental considerations for using nickel-based powders?
A: Nickel-based powders can be recycled in some cases, reducing waste and environmental impact. Additionally, PM and other techniques using these powders can offer near-net shape manufacturing, minimizing material waste compared to traditional methods. However, responsible disposal of nickel-based powder waste is crucial to prevent environmental contamination.
Q: How does the choice of nickel-based powder impact the final product?
A: The selection of nickel-based powder significantly influences the final product’s properties. Here’s a breakdown:
- Powder Composition: The specific alloying elements in the powder determine its strength, corrosion resistance, high-temperature performance, and other properties. For instance, Inconel 625 is ideal for high-temperature applications due to its exceptional heat resistance, while Monel 400 excels in resisting saltwater corrosion.
- Particle Size Distribution: Finer powders generally lead to denser components with smoother surfaces. Coarser powders, on the other hand, may offer improved flowability during processing but might result in a rougher surface finish.
Q: What are the future prospects for nickel-based powders?
A: The future of nickel-based powders appears bright. Advancements in powder metallurgy, thermal spraying, and 3D printing technologies are expected to unlock new possibilities for these versatile materials. Here are some exciting trends to watch:
- Development of new nickel-based powder compositions: Researchers are continuously exploring new alloy combinations to achieve even better properties like higher strength, improved corrosion resistance, and enhanced wear resistance.
- Advancements in 3D printing: As 3D printing technology matures, it’s expected to become more cost-effective and widely adopted. This will likely lead to increased use of nickel-based powders for creating complex, high-performance components in various industries.
- Sustainability Focus: The focus on sustainable manufacturing practices will likely drive the development of more environmentally friendly processes for producing and using nickel-based powders.
Conclusion
Nickel-based powders have emerged as a game-changer in the manufacturing landscape. Their unique combination of properties and the ever-evolving processing techniques have opened doors for innovative designs, improved product performance, and efficient material utilization. As technology continues to advance, nickel-based powders are poised to play an even more significant role in shaping the future of manufacturing.