Nickel based superalloys represent an elite class of materials exhibiting remarkable mechanical and corrosion resistance properties even at extreme temperatures. This comprehensive guide provides engineers, researchers, and technical buyers an in-depth reference covering all essential aspects of nickel based superalloys – ranging from metallurgy characteristics, processing methods, critical properties data, specifications, grades, and major applications.
Overview of Nickel Based Superalloys
Nickel based superalloys comprise a high percentage of nickel alloyed primarily with chromium, cobalt, molybdenum, tungsten, aluminum, titanium, iron, niobium, tantalum and other minor constituents. This tailored composition provides an exceptional combination of properties even at hot temperatures up to 85% of their melting point.
Key Characteristics:
- Retain strength and toughness at high temps
- Resist creep deformation
- Withstand thermal fatigue
- Excellent corrosion and oxidation resistance
Their capabilities empower performance in demanding industries including aerospace, oil and gas, automotive, chemical processing, and power generation where traditional materials fall short.
Composition of Nickel Based Superalloys
Alloying Element | Role | Weight % |
---|---|---|
Nickel | Corrosion resistance, ductility | 40-80% |
Chromium | Oxidation resistance | 10-25% |
Cobalt | Strength at high temps | 0-15% |
Molybdenum | Creep strength | 0-6% |
Tungsten | Stability at high temps | 2-12% |
Aluminum | Oxidation resistance | 0-6% |
Titanium | Strength, grain control | 0-5% |
Iron | Cost reduction | 0-20% |
Balancing primary elements enables optimizing for key application requirements like tensile strength, creep life, oxidation resistance or cost targets.
Types of Nickel Based Superalloys
Type | Description |
---|---|
Solid solution strengthened | Primary alloying for high temp strength |
Precipitation strengthened | Secondary alloying forms precipitates |
ODS (Oxide dispersion strengthened) | Nanoscale oxides for ultra-strength |
Single crystal | Directional solidification, no grain boundaries |
Advanced melting technologies allow creation of a widening range of nickel based superalloys for ever more extreme environments.

Manufacturing Processes
Producing nickel based superalloys is complex, requiring tightly controlled methods.
Primary Production Methods
Process | Details |
---|---|
Vacuum Induction Melting (VIM) | Purity, composition control |
Vacuum Arc Remelting (VAR) | Minimizes defects, improves structure |
Investment Casting | Complex shapes |
Wrought Processing | Deformation mechanisms enhance strength |
Powder Metallurgy | High uniformity and performance |
Direct Laser Deposition | Additive layering flexibility |
Appropriate post processing like hot isostatic pressing (HIP), heat treatment, thermomechanical working and machining completes parts.
Form Availability
- Cast ingots
- Wrought billets
- Powder for AM
- Net shape castings
- Plate, sheet, bar
Properties of Nickel Based Superalloys
Property | Typical Value |
---|---|
Density | 8.0-9.2 g/cm3 |
Melting Point | 1250-1380°C |
Young’s Modulus | 150-210 GPa |
Yield Strength | 500-1300 MPa |
Tensile Strength | 1000-1800 MPa |
Elongation | 3-60% |
Fatigue Strength | 100-800 MPa |
Fracture Toughness | 20-250 MPa-m^1/2 |
Creep Strength | 100-800 MPa |
Thermal Conductivity | 5-40 W/m-K |
Thermal Expansion | 12-16 μm/m-K |
Engineers select optimal nickel superalloy grades balancing properties like tensile strength, temperature rating, weldability, castability and cost for their operating environments.
Nickel Superalloy Specifications and Grades
Extensive superalloy classification systems have been developed to categorize thousands of complex chemistries available.
Alloy Categorization Systems
System | Basis |
---|---|
UNS (Unified Numbering System) | Composition based |
AMS (SAE Aerospace Material Specs) | Performance based |
Proprietary | Company branding |
Widely Used Nickel Superalloy Grades
Grade | Description |
---|---|
Inconel 718 | Aircraft engines, withstand 650°C |
Inconel 625 | Corrosion resistant, oxidizes slowly |
Hastelloy X | Jet engine parts, resists 1090°C |
Haynes 230 | Withstand extremes of heat flux |
Waspaloy | Aerospace components, stable microstructure |
René 41 | Aircraft engine cases, 1095°C rating |
New proprietary alloys continually get developed, aiming to push performance boundaries further.
Machining Nickel Superalloys
Given excellent but complex metallurgical characteristics, machining nickel superalloys can prove uniquely challenging compared to conventional materials.
Following best practices is key:
- Utilize rigid setups to minimize vibration
- Employ sharper cutting tools for shearing
- Use high pressure coolant directional spraying
- Apply deflective tools path strategies
- Optimize speeds, feeds and depths
- Allow time for tools to cool
Thorough planning balancing tool life against quality and productivity prevents common pitfalls when working with these high performance alloys.
Applications of Nickel Superalloys
Aerospace and Aviation
- Jet engine parts – combustor, turbine blades
- Structural airframe components
- Missile hardware
- Instrumentation systems
Power Generation
- Gas turbine hot section parts
- Coal plant boiler components
- Nuclear reactors
- Waste incineration
Oil and Gas Industry
- Downhole tools and drilling
- Offshore platform equipment
- Crack resistant piping
- Corrosive process vessel parts
Nickel superalloys confer critical temperature, corrosion and wear resistance in the most unforgiving mechanical systems across industries.
Suppliers and Pricing
Obtaining raw forms or finished components requires connecting with highly specialized metalworking partners intimately familiar with nickel superalloys’ processing intricacies.
Leading Nickel Superalloy Manufacturers and Suppliers
Company | Location |
---|---|
Aperam | Europe |
Allegheny Technologies | United States |
Carpenter Technologies | United States |
Haynes International | United States |
High Performance Alloys | United States |
Special Metals Corporation | United States |
Nickel Superalloys Price Ranges
Product Form | Price Estimate Per Kilogram |
---|---|
Raw Material | $25-60 |
Bar Stock | $40-150 |
Plate/Sheet | $50-250 |
Castings | $80-600 |
Fasteners | $80-1000 |
Cost multipliers stemming from specialized expertise required in manufacturing unique geometries and achieving critical quality standards account for their premium pricing.
Pros vs Cons
Pros | Cons |
---|---|
Retain high strength at extreme temps | Requires advanced alloy knowledge |
Outstanding oxidation resistance | Sensitive processing methods |
Resist thermal fatigue | Challenging/costly to machine |
Withstand aggressive corrosion | Higher material cost |
Meet most demanding applications | Limited weldability for some grades |
For mission-critical components where failure proves catastrophic, nickel superalloys confer irreplaceable capabilities despite increased input requirements during production.
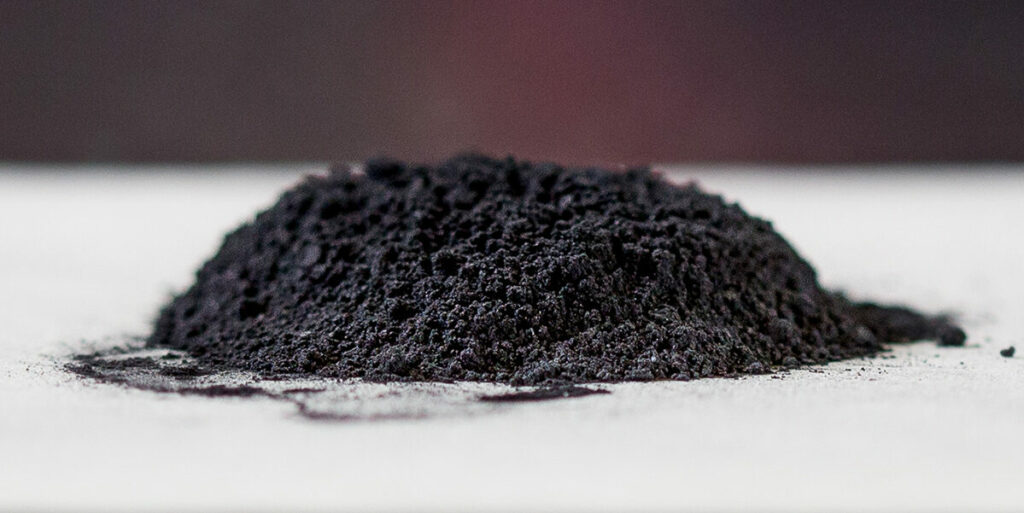
FAQs
Q: What is the difference between a superalloy and high performance alloy?
A: Superalloys exhibit exceptional properties at temperatures over 650°C. High performance alloys feature enhanced characteristics below this threshold. Both demonstrate capabilities exceeding standard stainless, tool or structural steels.
Q: Which nickel superalloy offers the best weldability?
A: Nickel alloy 625 provides the easiest welding for minimal dilution and cracking thanks to optimized chemistry and slow aging kinetics. Reduce heat inputs and allow generous post-weld stress relief for other grades.
Q: Can you 3D print nickel superalloys using metal AM?
A: Yes, selective laser melting and electron beam powder bed fusion now enable complex geometries once impossible through conventional methods alone. Repeatable quality still proves challenging.
Q: What is a nickel iron chromium superalloy?
A: This subset optimized as turbine blade materials balances high strength with imparting ductility – augmenting creep life through smart compositional adjustments lowering gamma prime formation rates.
Conclusion
From enabling efficient air travel to generating abundant clean power, nickel based superalloys represent the unsung hero material behind history’s greatest technological achievements. This guide sought as a foundational reference encapsulating everything technical professionals require when deciding if nickel superalloys prove the ideal selection. Please connect with an alloy expert for further insights answering your most pressing questions. The future beckons.