Overview of FeCoNiCrMo Powder
FeCoNiCrMo powder, also known as stainless tool steel powder, is an iron-based alloy powder composed primarily of iron (Fe), cobalt (Co), nickel (Ni), chromium (Cr), and molybdenum (Mo). This multiphase alloy powder offers an exceptional combination of properties including high strength, hardness, wear resistance, corrosion resistance, and dimensional stability.
FeCoNiCrMo powder can be compacted into parts via powder metallurgy techniques such as metal injection molding (MIM), hot isostatic pressing (HIP), additive manufacturing, and conventional press and sinter methods. The unique qualities of FeCoNiCrMo enable the production of intricate, net-shape components with the strength approaching that of wrought materials. Typical applications include aerospace components, industrial tooling, automotive parts, biomedical implants, and wear components.
Table 1: Overview of FeCoNiCrMo Powder
Composition | Iron-based alloy with Co, Ni, Cr, Mo |
---|---|
Key Properties | High strength, wear resistance, corrosion resistance, dimensional stability |
Production Methods | Metal injection molding (MIM), Hot isostatic pressing (HIP), Additive manufacturing, Press & sinter |
Applications | Aerospace, Industrial tooling, Automotive, Biomedical implants, Wear components |
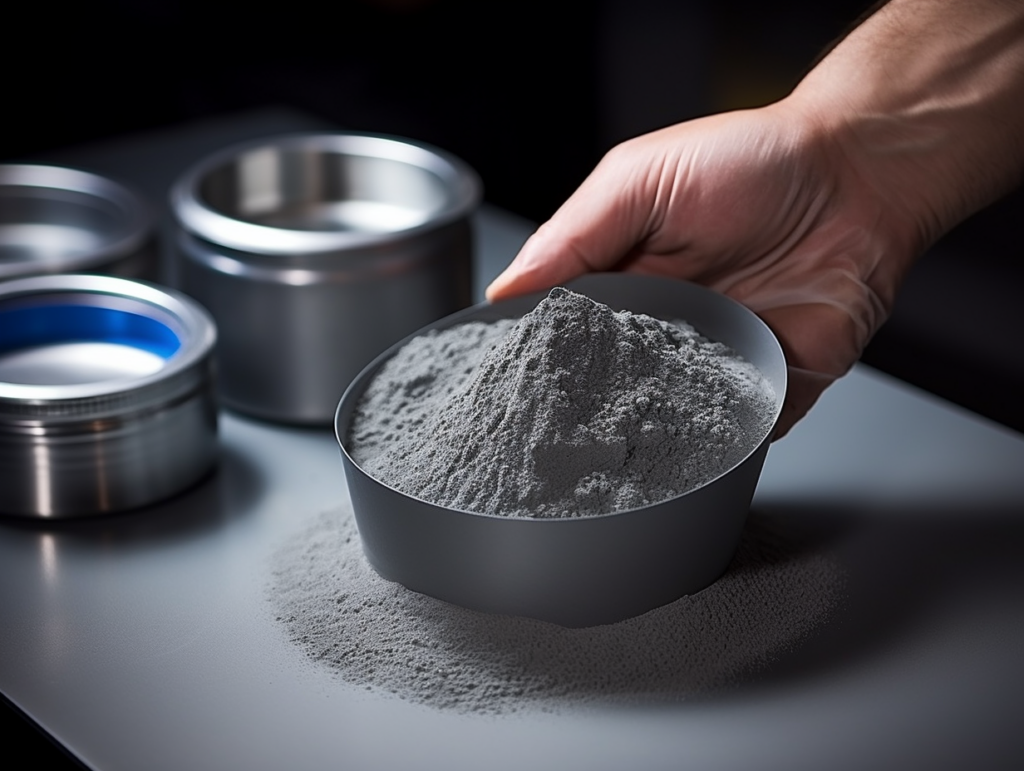
Composition of FeCoNiCrMo Powder
The exact chemical composition of the FeCoNiCrMo alloy powder can vary depending on the desired properties and applications. However, a typical formulation consists of the elements shown below:
Table 2: Typical Composition of FeCoNiCrMo Powder
Element | Weight % | Role |
---|---|---|
Iron (Fe) | Balance | Primary base material |
Cobalt (Co) | 15-25% | Solid solution strengthening |
Nickel (Ni) | 10-30% | Toughness, ductility |
Chromium (Cr) | 5-15% | Oxidation resistance, hardness |
Molybdenum (Mo) | 1-6% | Wear resistance, strength |
The high cobalt and nickel contents contribute to achieving very high strength levels in excess of 220 ksi (1520 MPa) after suitable heat treatment. Meanwhile, the chromium helps resist corrosion and oxidation at elevated temperatures. Finally, the addition of molybdenum further enhances overall wear performance.
By tweaking the proportions of these key elements, the properties of the FeCoNiCrMo powder can be customized to meet the needs of different applications.
Properties of FeCoNiCrMo Powder
FeCoNiCrMo powder distinguishes itself from other tool steel powders by exhibiting an exceptional balance of mechanical properties, hardness, corrosion resistance, and dimensional stability.
Table 3: Overview of FeCoNiCrMo Powder Properties
Property | Value | Importance |
---|---|---|
Density | 7.5 – 8.0 g/cm3 | Enables high strength in small sections |
Strength | 220 – 300 ksi (1520 – 2070 MPa) | Withstand high stresses and pressures |
Hardness | 50 – 65 HRC | Resist wear, indentation, scratching |
Toughness | 30 – 50 ft-lbs | Resilience against fracture and fatigue |
Corrosion Resistance | Excellent | Long component life in harsh conditions |
Heat Resistance | 1000°C | Retain strength in hot environments |
Dimensional Stability | Excellent | Predictable, precise finished dimensions |
By leveraging powder metallurgy techniques, parts made of FeCoNiCrMo powder can achieve mechanical performance comparable to or exceeding conventionally processed alloys.
Some of the notable characteristics of this multifunctional powder include:
- High strength and hardness: FeCoNiCrMo powder can be compacted and heat treated to strength levels surpassing 220 ksi (1520 MPa) and hardness over 60 HRC, approaching the properties of bearing steels and cobalt alloys. This is useful for components needing excellent wear, indentation, and scratch resistance.
- Well-balanced toughness: Unlike some tool steel powders sacrificing ductility for hardness, FeCoNiCrMo maintains respectable toughness between 30-50 ft-lbs in the heat treated condition. This allows better resilience against fracture, fatigue, or catastrophic failure in service.
- Excellent high-temperature properties: FeCoNiCrMo retains its strength and corrosion resistance up to temperatures nearing 1000°C making it suitable for hot working environments and friction applications.
- Outstanding dimensional stability: The low coefficient of thermal expansion minimizes concerns over growth or distortion issues during heat treatment or thermal cycling in service. This permits precise net shaping capabilities.
- Corrosion resistance: The chromium and nickel alloying additions enable FeCoNiCrMo powder to resist corrosion, oxidation, and chemical attack even at elevated temperatures and in acidic or salt-rich environments.
By optimizing parameters like composition, powder production method, green and sinter density, heat treatments, and secondary processing, the properties of FeCoNiCrMo powder can be tailored to meet application requirements.
-
SCM 415 Low Alloy Steel Powder
-
AISI 4340 Low Alloy Steel Powder
-
Invar 36 alloy powder
-
52100 Alloy Steel Powder
-
2.25Cr1Mo alloy steel
-
Stainless Steel OP431 Powder
-
Best Stainless Steel 316L Powder for 3D Printing
-
stainless steel 304 Powder for 3D Printing
-
Best 17-4PH powder stainless steel powder for 3D Printing
Applications of FeCoNiCrMo Powder
The unique combination of high strength, hardness, wear performance, heat resistance, and dimensional stability offered by FeCoNiCrMo powder makes it well suited to the following applications:
Table 4: Overview of FeCoNiCrMo Powder Applications
Application | Examples | Key Advantages |
---|---|---|
Aerospace | Turbine blades, landing gear, actuators | High strength, heat resistance |
Automotive | Valve lifters, connecting rods | Wear resistance, stability |
Industrial Tooling | Extrusion dies, forming tools | Hardness, toughness |
Biomedical | Joint replacements, dentures | Biocompatibility, corrosion resistance |
Oil & Gas | Seals, valves, well tools | High pressure capability, stability |
Some specific product examples taking advantage of the benefits of FeCoNiCrMo powder include:
- Aerospace components: Turbine blades, fuel system parts, landing gear, transmission gears, and structural brackets leverage the powder’s strength at elevated temperatures and in stressful dynamic environments. Lighter, smaller FeCoNiCrMo components enable better fuel efficiency.
- Cutting tools and dies: Punching/forming tools, shear blades, trim dies, and extrusion dies rely on the combination of hardness, toughness, and dimensional stability to achieve longer service life and improved productivity.
- Biomedical implants: Joint replacement substrates, dental implants, surgical tools, bone screws, and fixtures take advantage of biocompatibility, high strength, and corrosion resistance to better integrate in the human body environment.
- Seals, valves, pumps: Powder-based FeCoNiCrMo components resist wear, corrosion, erosion and deformation enabling reliable sealing and metering performance. The materials are often used in oil & gas, chemical/petrochemical, and other demanding fluid handling applications.
In many cases, the unique qualities of FeCoNiCrMo powder permit components with better performance or longer life compared to those produced via conventional methods.
Production Methods for FeCoNiCrMo Powder Parts
While FeCoNiCrMo powder can be consolidated into final parts via several methods, the most popular production routes include:
Table 5: Overview of FeCoNiCrMo Powder Production Methods
Method | Details | Part Size | Typical Uses |
---|---|---|---|
Metal Injection Molding (MIM) | Binder mixing, injection molding then sintering | 0.1-100g | Small, complex geometries |
Hot Isostatic Pressing (HIP) | Canned powder HIPed then machined | 100g – 50kg | Near-net shapes to finish machining |
Additive Manufacturing | Laser powder bed fusion (L-PBF) | 10-100g | Prototyping, custom geometries |
Press & Sinter | Compacted in a die then sintered | 1kg+ | Simple shapes, maximum economies of scale |
By leveraging various powder metallurgy techniques, very precise parts with complex shapes can be manufactured to near-net shape while minimizing expensive machining.
Below are more details on the popular processing routes:
Metal Injection Molding (MIM)
- Uses binder mixing, injection molding, debinding, and sintering to produce intricate FeCoNiCrMo components from 0.1-100 grams.
- Capable of highly complex, tight tolerance geometries unattainable by other methods. Very minimal final machining is required.
- Ideal for making small precision components like biomedical implants and connectors in moderate volumes.
Hot Isostatic Pressing (HIP)
- Involves sealing FeCoNiCrMo powder in a container, encapsulating, then HIPing to consolidate into a densified compact.
- Subsequent finish machining produces 100% dense near-net shape components from 100 grams to 50+ kilograms.
- Typically used to make pre-HIPed billets for machining into aerospace and industrial components.
Additive Manufacturing (AM)
- Uses selective laser melting, laser powder bed fusion, or binder jetting to build complex 3D geometries from FeCoNiCrMo powder layer-by-layer.
- AM is capable of making one-off prototypes, custom tooling, or short run end-use parts weighing 10-100 grams without dies or tooling.
- Mostly used for design iteration and low volume production. Heat treatment is often required for better mechanical performance.
Press & Sinter Route
- FeCoNiCrMo powder is pressed inside dies up to several tons/inch2 then sintered to fuse powder particles together into a porous compact.
- Simple shapes over 1 kilogram are possible with maximum economies of scale by avoiding secondary processing.
- Suitable for some wear components like bushings needing looser dimensional tolerances. Secondary infiltration is sometimes used to increase densities.
Specifications of FeCoNiCrMo Powder
FeCoNiCrMo powder is produced by various commercial powder metallurgy suppliers to tight chemical compositions and particle size distributions tailored towards different consolidation methods.
Table 6: Overview of FeCoNiCrMo Powder Specifications
Parameter | Range | Typical | Importance |
---|---|---|---|
Particle size | 10-45 μm | 20 μm | Controls powder flow and packing |
Carbon content | < 0.1 wt% | 0.02 wt% | Avoids soot formation during laser melting |
Oxygen content | < 0.6 wt% | 0.4 wt% | Minimizes oxidation and porosity |
Tap density | 4.0-4.8 g/cc | 4.3 g/cc | Influences final part density |
Flow rate | 25-35 s/50g | 28 s/50g | Ensures smooth powder feeding |
Apparent density | 65-80% | 72% | Key for final part density |
Hausner ratio | < 1.25 | 1.15 | Determines powder flowability |
By controlling characteristics like particle shape, size distribution, chemistry, and flow rate, FeCoNiCrMo powder can be optimized for various AM, MIM, or pressing applications.
For example:
- Fine <20 μm powder spreads better during laser melting but has higher resistance to flow. More suited for AM.
- Coarser 35-45 μm powder presses to higher green density but doesn’t fuse as easily. Better for press & sinter use.
- Higher tap/apparent density and more spherical particles yield better densification and flow.
- Lower oxygen, moisture, and finer atomization yield superior mechanical performance.
Powder specifications are typically customized for the intended production method whether AM, MIM, or conventional press and sinter.
Grades and Standards of FeCoNiCrMo Powder
While proprietary grades of FeCoNiCrMo tool steel powder exist from various suppliers, the alloy system does not have an official standard composition or specification yet. However, development efforts are underway to introduce FeCoNiCrMo as a recognized alloy.
Table 7: Overview of FeCoNiCrMo Powder Standards
Status | Details |
---|---|
Existing standards | None (proprietary grades only) |
In development | UNS R30050, ASTM Specification |
Similar alloys | M300 Maraging steel (MIM, AM) |
The alloy shares similarities with powder grades used in metal injection molding and additive manufacturing such as:
- M300 Maraging steel: 18Ni-Co-Mo precipitation-hardening steel capable of 1300 MPa tensile strength after aging treatment. Lower alloy content versus FeCoNiCrMo.
- Nickel superalloys: Materials like Inconel 718 offer excellent heat resistance but lower hardness and weaker wear performance than FeCoNiCrMo.
Ongoing collaboration across industry, academia, professional societies, and standardization bodies like ASTM will be beneficial for establishing specifications guiding the composition, testing, inspection, and certification of FeCoNiCrMo powder. This will enable greater adoption across critical commercial and defense applications.
Pricing of FeCoNiCrMo Powder Products
As a newer alloy system, FeCoNiCrMo powder products currently demand pricing premiums compared to more established stainless or tool steel options. However, costs are projected to decrease with larger volume manufacturing.
Table 8: Indicative Pricing for FeCoNiCrMo Powder and Parts
Product | Cost |
---|---|
FeCoNiCrMo atomized powder | $80-150 per kg |
MIM parts | $2-5 per cubic cm |
HIPPED preforms | $15-25 per kg |
AM parts | $100-200 per kg |
In general, buyers can expect to pay a 30-50% cost premium for FeCoNiCrMo products compared to equivalent 416 or 17-4PH stainless steel parts. However, the enhanced mechanical performance often justifies higher prices for critical applications, especially where better corrosion resistance over less expensive alternatives like M2 tool steel is needed.
As manufacturing scales up, a 20-30% cost reduction is foreseeable over the next 5 years if customer demand accelerates from industries such as medical, aerospace, automotive, and industrial equipment. This outlook will be driven by optimization along the supply chain in areas like raw material sourcing, powder manufacturing yields, additive and MIM equipment productivity, as well as waste minimization.
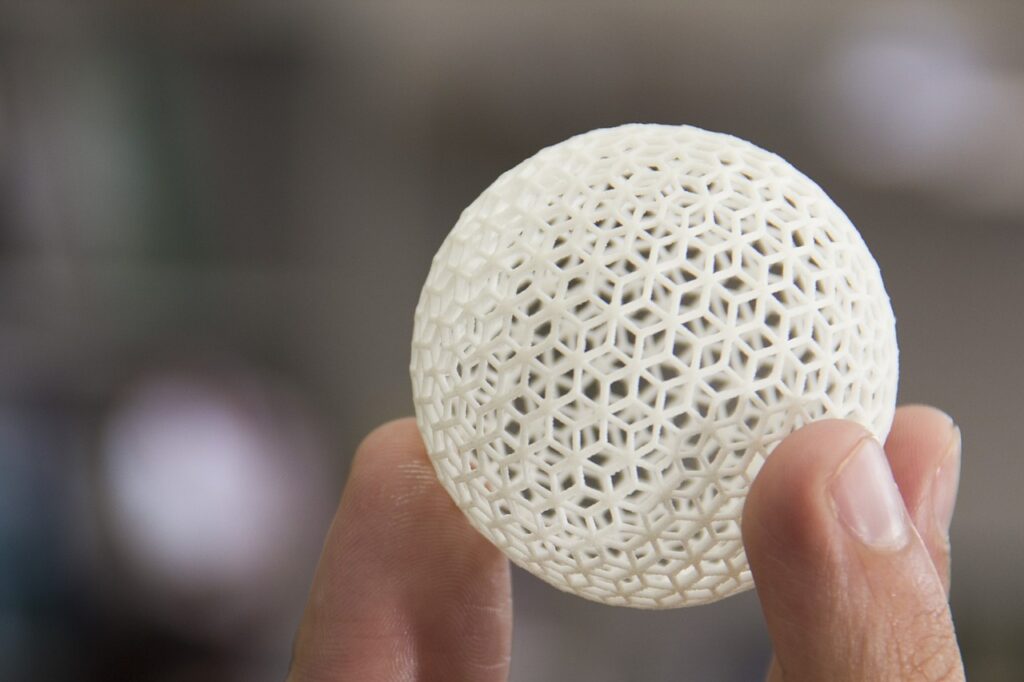
Pros vs Cons of FeCoNiCrMo Powder
While offering impressive all-around properties, FeCoNiCrMo powder also has limitations to consider before choosing it over competing alternatives.
Table 9: Comparison of FeCoNiCrMo Powder Pros and Cons
Advantages | Disadvantages |
---|---|
Exceptional strength and hardness | No existing industry standard yet |
Heat resistance up to 1000°C | Raw materials supply constraints |
Outstanding wear and corrosion resistance | Costs 30-50% higher than 17-4 and 420 powders |
Dimensional stability across operating envelope | Lower toughness than annealed austenitic stainless steels |
Net shape manufacturability minimizes machining | Requires controlled cooling rates during heat treatment |
Customizable properties by element tweaks | Susceptible to strain-age cracking without proper post-processing |
By trading off factors like cost against mechanical performance and corrosion resistance, buyers can determine if FeCoNiCrMo powder solutions justify the investment over alternatives for their specific application requirements.
Managing disadvantages related to developing broader supply infrastructure and industryfamiliarity with the alloy system are crucial for more widespread adoption. Qualification testing also remains vital for proving out FeCoNiCrMo performance in new applications, especially in risk-averse sectors like aerospace, medical, nuclear, and oil & gas where reliability and safety are paramount.
FAQs
Q: Does FeCoNiCrMo powder require special storage or handling precautions?
A: Like other reactive alloy powders, FeCoNiCrMo is best kept sealed in inert containers to avoid oxidation issues. Other typical precautions for powder handling and containment should be followed, especially during AM or other processing stages with open powder beds.
Q: What heat treatments maximize the properties of FeCoNiCrMo components?
A: Solutionizing at 1120-1180°C plus multiple temper cycles in the 550-650°C range for 1-2 hours duration can yield over 220 ksi tensile strength and 60 HRC hardness. Controlled rapid cooling after solution treatment is critical as well to avoid undesirable phases.