TC4 powder, also known as titanium carbide powder, is an extremely hard ceramic material made from titanium and carbon. It is one of the hardest known carbides and has excellent wear resistance, high strength at high temperatures, and good thermal and electrical conductivity. TC4 powder is widely used in applications that require high hardness, wear resistance, thermal stability and strength.
Some key properties and uses of TC4 powder include:
TC4 Powder Properties and Applications
Property | Description |
---|---|
Hardness | Extremely high hardness of 3000 HV or more on the Vickers scale. One of the hardest carbide materials. |
Wear resistance | Excellent wear and abrasion resistance due to hardness. Low coefficient of friction. |
High temperature strength | Maintains high strength and hardness at temperatures up to 1000°C. Melting point around 3160°C. |
Thermal conductivity | Good thermal conductivity allows heat dissipation in high temperature applications. |
Electrical conductivity | Moderate electrical conductivity for a ceramic material. |
Chemical inertness | Resistant to chemical attack and corrosion at high temperatures. |
Applications | Cutting tools, dies, bearings, valves, abrasion resistant coatings, welding electrodes, armor plating, aerospace components. |
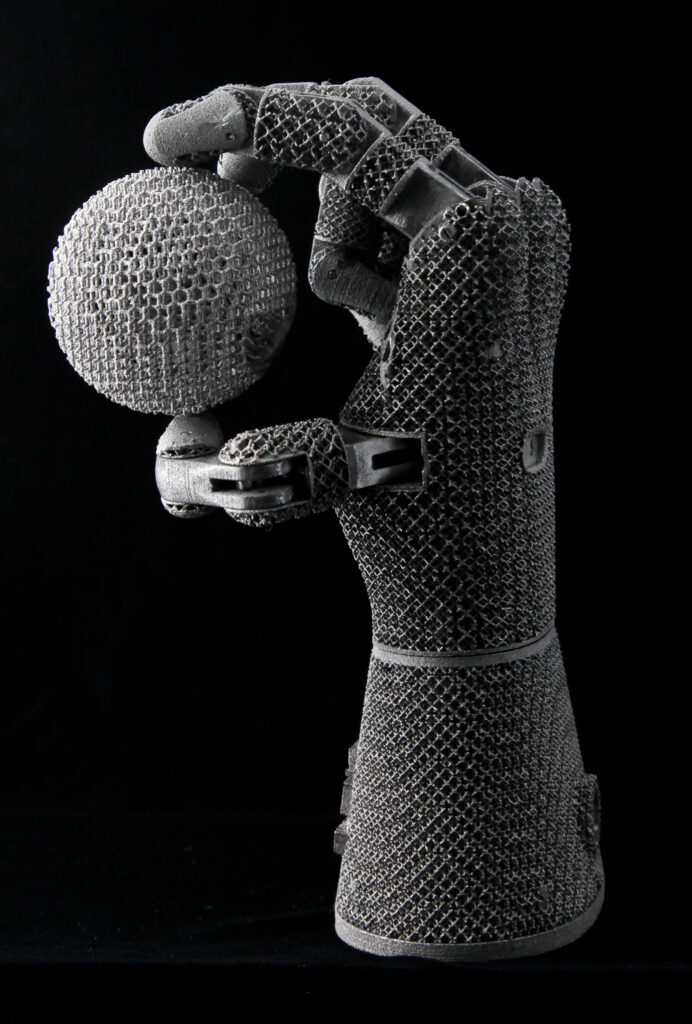
Types of TC4 Powder
There are a few different types and grades of TC4 powder that provide some variation in properties based on composition, particle size, and manufacturing process:
Type | Description |
---|---|
Micro grain | Very fine particle size of 0.5-3 microns allows sintering to full density. For consolidated parts and coatings. |
Macro grain | Larger particle size of 3-45 microns has lower sinterability but better wear resistance. For thermal spray coatings. |
Alloyed powder | Contains alloying elements like nickel, molybdenum, chromium to modify properties like toughness, strength, or corrosion resistance. |
Plasma densified | Shows improved sinterability due to densification during plasma synthesis. |
Characteristics of TC4 Powder
TC4 powder has unique characteristics that make it suitable for high performance applications requiring hardness, strength and wear resistance:
Characteristic | Description |
---|---|
Extreme hardness | Vickers hardness of 3000 HV or more provides excellent wear resistance. |
High elastic modulus | Around 500 GPa elastic modulus imparts resistance to deformation. |
Low density | Around 4.9 g/cm3 density compared to 7.9 g/cm3 for tungsten carbide. |
High melting point | Melting point of 3160°C allows use in high temperature environments. |
Good oxidation resistance | Forms protective oxide layer in oxidizing conditions up to 800°C. |
Thermal shock resistance | Withstands rapid heating and cooling cycles without cracking. |
Chemical stability | Inert to most acids, alkalis and molten metals. Slowly dissolves in hot HCl/H2SO4. |
Specifications for TC4 Powder
TC4 powder is available in standard specifications as well as custom formulations to meet specific requirements:
Parameter | Specification |
---|---|
Composition | Titanium content 88-92 wt%, carbon balance |
Particle size | 0.5 – 45 microns typical |
Apparent density | Up to 1.5 g/cm3 |
Tap density | Up to 2.5 g/cm3 |
Purity | >99.5% titanium carbide content |
Oxygen content | <1% |
Texture | Angular morphology |
Color | Grayish black |
The particle size distribution, purity levels, oxygen content and other parameters can be customized as per application needs. Finer particles offer better consolidation while coarser sizes give higher wear resistance.
Applications and Uses of TC4 Powder
Some major applications and uses of TC4 powder take advantage of its outstanding hardness, wear resistance and high temperature strength:
Application | Uses |
---|---|
Cutting tools | Indexable inserts, end mills, drills, reamers, burrs |
Metal forming | Punching and extrusion dies, rollers |
Wear parts | Seal faces, nozzles, bushings, ball valves |
Surface engineering | Thermal spray coatings, laser cladding |
Welding | Flux cored wires, submerged arc electrodes |
Armor | Vehicle armor plating, bulletproof vests |
Aerospace | Thermal barrier coatings on turbine blades |
Electronics | Resistive films, vacuum interrupters |
The unique properties of TC4 powder make it suitable for these demanding applications across automotive, oil & gas, mining, construction, defense, and other sectors.
Suppliers of TC4 Powder
Some of the major global suppliers that manufacture TC4 powder include:
Supplier | Location |
---|---|
H.C. Starck | Germany, USA |
Japan New Metals | Japan |
Beijing Youxinglian Nonferrous Metals | China |
Micron Metals | USA |
Nanochemazone | India |
Pricing varies from $50/kg for coarse macro grain powder to over $200/kg for ultrafine micro grain powder based on particle size, purity levels, production process and purchase volumes.
Installation of TC4 Powder
TC4 powder needs to be consolidated into a solid component using various techniques:
- For pressing and sintering, TC4 powder is loaded into a suitable die and compacted at high pressures of up to 300 MPa. The green compact is then sintered at 1400-1700°C in vacuum or inert atmosphere.
- Thermal spraying involves spraying the powder feedstock onto the substrate using a plasma or combustion flame. The sprayed particles consolidate into a hard coating.
- Laser cladding focuses a high power laser on the substrate to melt the powder and fuse it to the surface as a hardfacing layer.
- To make a cermet, TC4 powder can be sintered along with metallic binders like nickel, cobalt or steel to improve toughness.
Proper protective equipment for handling fine ceramic powders needs to be used during loading and processing. Dust collection systems are recommended to improve workplace safety.
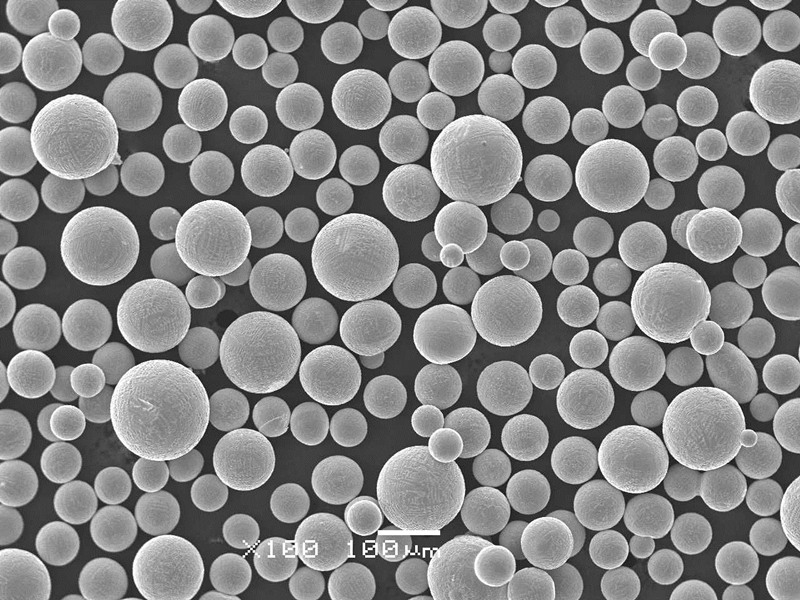
Operation and Maintenance of TC4 Parts
In operation, TC4 parts like cutting tools and wear resistant components require:
- Proper mounting, installation and machine setup to avoid cracking from excessive loads.
- Application within recommended parameters of load, speed, temperature, etc. Too high speeds generate heat which can cause thermal cracking.
- Use of coolants and lubricants to control temperature rise and lower friction during metal cutting or wear applications.
- Periodic inspection of parts for wear, cracks or damage. Early detection helps avoid catastrophic failures.
For maintenance, standard practices apply:
- Replacement of worn parts before dimensional tolerances are exceeded.
- Cleaning and recoating worn surfaces with fresh TC4 material to restore dimensions and function.
- Remanufacturing heavily worn parts by building up and re-machining to specifications.
Choosing a TC4 Powder Supplier
When selecting a TC4 powder supplier, some important criteria include:
- Technical expertise in production and quality control of titanium carbide powders
- Ability to customize powder characteristics like particle size distribution, purity levels, morphology, etc.
- Production capacity to meet demand volumes
- Range of powder types and compatible alloy grades
- Competitive pricing and stability of supply
- Responsiveness to technical requirements and sampling requests
- Quality certifications and compliance with international standards
- Record of consistently supplying quality powder to other customers
- Strong R&D capabilities for developing advanced products
Comparing TC4 Powder to Alternatives
TC4 powder compares to other hard materials like tungsten carbide and silicon carbide as follows:
Parameter | TC4 | Tungsten Carbide | Silicon Carbide |
---|---|---|---|
Hardness | Higher | Slightly lower | Lower |
Toughness | Lower | Higher | Higher |
Density | Lower | Higher | Slightly higher |
Temperature stability | Higher | Lower | Similar |
Corrosion resistance | Better | WC vulnerable to alkalis | Similar |
Cost | Moderate | Lower | Higher |
Advantages of TC4:
- Extreme hardness for wear resistance
- Maintains strength at higher temperatures than WC
- More thermally and chemically stable than WC
- Lighter than WC and SiC
Limitations of TC4:
- More brittle with lower fracture toughness than WC and SiC
- More expensive than tungsten carbide powders
- Requires high temperature sintering
So TC4 stands out for its exceptional hardness and thermal stability, though it suffers from poor toughness and higher cost than tungsten carbide. Proper application design and processing is needed to overcome its limitations.
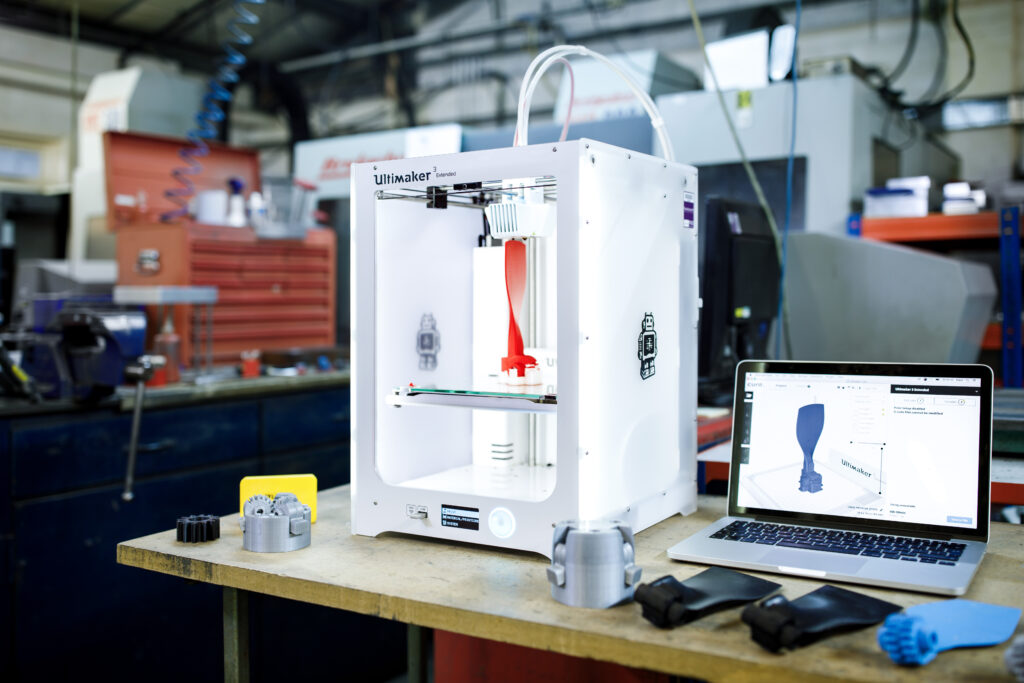
FAQs
Q: What is TC4 powder made of?
A: TC4 powder consists of 88-92% titanium carbide (TiC) with the balance being free carbon. It may also contain small amounts of oxides, nitrides and other transition metal carbides.
Q: What is the difference between TC4 and tungsten carbide?
A: The main difference is that TC4 is based on titanium carbide which provides higher hardness and strength at elevated temperatures compared to tungsten carbide. However, TC4 has lower fracture toughness than tungsten carbide.
Q: What are the advantages of TC4 powder?
A: Key advantages include extreme hardness resulting in excellent wear resistance, high strength at temperatures up to 1000°C, low density compared to WC, and good corrosion resistance.
Q: What is TC4 powder used for?
A: Typical uses include cutting tools, punching/coining dies, wear parts, thermal spray coatings, welding electrodes, armor, aerospace components, and electronics.
Q: How is TC4 powder made?
A: It is commercially produced by reacting titanium oxide and carbon black at very high temperatures above 3000°C using processes like plasma arc synthesis or chemical vapor deposition.
Q: Is TC4 powder toxic?
A: Like most fine powders, TC4 poses a health hazard if inhaled over long periods. Proper protective equipment should be used when handling the powder.
Q: How is TC4 powder consolidated into a part?
A: Main methods include sintering, thermal spraying, laser cladding, and hot pressing. Binder phases like Ni or Co can also be co-sintered with TC4 to produce cermets.
Q: Why is TC4 powder expensive?
A: The complex high temperature synthesis processes for producing high purity titanium carbide result in higher costs than simpler tungsten carbide production.
Q: What standards does TC4 powder comply with?
A: TC4 powder specifications align with standards like ASTM B381 for titanium carbide powders and ISO 18775 for cemented carbide powders.
In summary, TC4 powder provides an optimal combination of hardness, thermal stability and wear resistance making it suitable for demanding industrial applications, though it comes at a higher cost than alternatives like tungsten carbide. Proper processing and design is key to overcoming its brittleness limitations. Leading global suppliers can provide TC4 powders tailored to specific requirements.