Overview of TA15 Titanium Alloy Powder
TA15 titanium alloy powder is an important material used across many industries due to its excellent combination of properties. Some key features of TA15 powder include:
- High strength-to-weight ratio
- Corrosion resistance
- Biocompatibility
- High temperature performance
- Good weldability
- Low modulus
TA15 belongs to the α+β titanium alloy class, meaning it consists of both α phase and β phase titanium. The α phase provides good ductility and formability, while the β phase imparts high strength.
The typical composition of TA15 alloy is:
- Titanium: Balance
- Aluminum: 5%
- Tin: 2.5%
- Zirconium: 5%
- Molybdenum: 5%
Small amounts of other elements like oxygen, nitrogen, carbon, and iron may also be present. The combination of aluminum, tin, zirconium, and molybdenum is important for achieving the desired properties in TA15.
Some of the key applications for TA15 titanium alloy powder include:
Table: Applications of TA15 Titanium Alloy Powder
Application | Details |
---|---|
Aerospace | Engine components, airframe parts, fasteners |
Chemical plants | Pipes, vessels, heat exchangers |
Biomedical | Implants, prostheses, surgical instruments |
Automotive | Valves, connecting rods, springs |
Marine | Propellers, shafts, pumps |
Oil & gas | Downhole tubing, wellhead components |
The high strength, corrosion resistance, and biocompatibility of TA15 make it suitable for critical applications across these industries. The alloy can be manufactured into various forms like sheet, plate, bar, wire, fasteners, and 3D printed components.
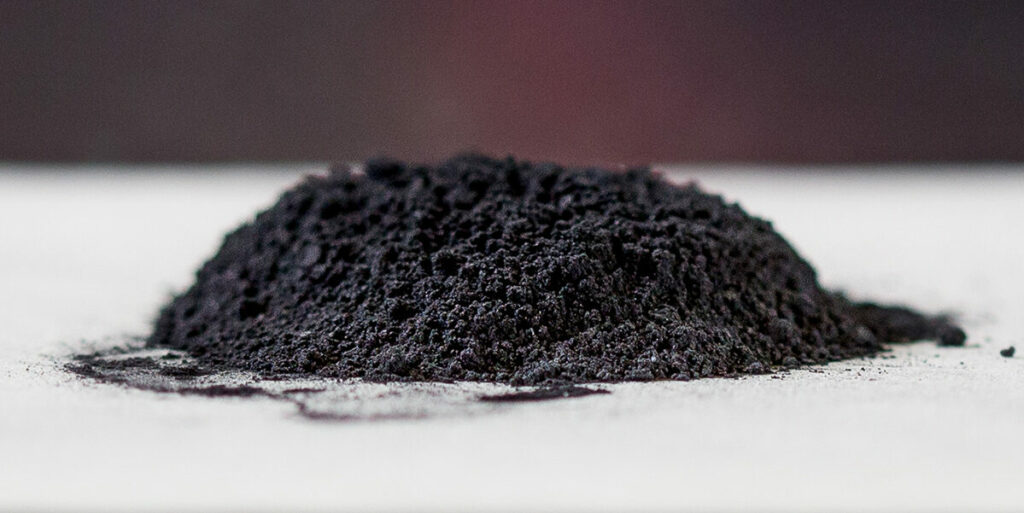
TA15 Titanium Alloy Powder Types
TA15 alloy powder can be categorized into different types based on particle size, morphology, manufacturing method, and microstructure. The main types of TA15 powder include:
Table: Types of TA15 Titanium Alloy Powder
Type | Details | Characteristics |
---|---|---|
Gas atomized | Made by inert gas atomization process | Spherical morphology, good flowability |
Plasma atomized | Made by plasma atomization method | Very spherical particles, high purity |
Hydride-dehydride (HDH) | Produced by HDH process | Irregular morphology, high oxygen content |
Alloyed elemental | Blended from pure Ti, Al, Sn etc. powders | Angular morphology, lower cost |
Pre-alloyed | Fully pre-alloyed powder | Homogeneous chemistry, high cost |
Gas atomized and plasma atomized powders have the most spherical particle shapes, providing good flow and packing properties. However, they can be more expensive.
HDH powders have lower cost but higher oxygen content. The particles are more irregular in shape.
Alloyed elemental powders are cheaper but have higher contamination risks. The angular powder morphology provides poorer flowability.
Pre-alloyed powders ensure uniform alloy chemistry but have the highest cost. The choice depends on the application requirements.
Characteristics of TA15 Titanium Alloy Powder
Some important characteristics of TA15 titanium alloy powder include:
Table: Characteristics of TA15 Titanium Alloy Powder
Characteristic | Details |
---|---|
Particle size distribution | Typically 10 – 45 μm for AM, up to 150 μm for pressing |
Apparent density | Around 2.7 – 3.5 g/cc |
Tap density | Approximately 4.0 – 4.5 g/cc |
Morphology | Spherical, irregular, or angular based on production method |
Flow rate | 25 – 35 s/50g for gas atomized powder |
Oxygen content | 0.15 – 0.25% for gas atomized, 0.3 – 0.6% for HDH |
Nitrogen content | <0.03% |
Carbon content | <0.08% |
Iron content | <0.25% |
The particle size distribution is an important parameter and is controlled based on the intended application. Finer 10-45 μm powder is used for additive manufacturing applications like laser powder bed fusion. Coarser powder up to 150 μm size can be used for press & sinter application.
The powder morphology also varies significantly depending on the manufacturing process. Spherical gas or plasma atomized powders have excellent flowability compared to irregular HDH powders.
Controlling the oxygen, nitrogen and carbon contents is crucial for achieving the desired mechanical properties in the finished TA15 part. Higher purity powders via gas/plasma atomization or pre-alloying helps to minimize impurity levels.
Applications and Uses of TA15 Titanium Alloy Powder
TA15 titanium alloy powder can be used to manufacture components through various processes:
Table: Processes for TA15 Titanium Alloy Powder
Process | Typical Applications | Benefits |
---|---|---|
Additive manufacturing | Aerospace components, implants | Design freedom, weight savings |
Metal injection molding | Small complex parts | High volume at lower cost |
Hot isostatic pressing | Jet engine components, pumps | Consolidates powder into net shape parts |
Pressing & sintering | Industrial valves, marine hardware | Simple shapes, lower cost |
Powder forging | Connecting rods, fasteners | Improved mechanical properties |
Additive manufacturing uses TA15 powder in processes like selective laser melting, electron beam melting, and direct metal laser sintering to 3D print intricate, lightweight components for aerospace and medical uses.
Metal injection molding combines the design flexibility of AM with the productivity of injection molding by first molding TA15 powder followed by debinding and sintering. Small, complex parts like gears can be mass produced at relatively low costs compared to machining.
Hot isostatic pressing (HIP) applies high temperature and isostatic gas pressure to consolidate TA15 powder into dense, net-shape parts with properties equivalent to wrought products. This improves consistency and reduces waste.
Pressing & sintering uses die-compacting and sintering to manufacture simple TA15 parts like valves and marine hardware at lower costs. Properties are reduced compared to wrought material.
Powder forging combines TA15 powder compaction with high temperature forging to refine the microstructure and enhance mechanical properties closer to those of wrought alloys. Connecting rods and fasteners are some examples.
Specifications of TA15 Titanium Alloy Powder
TA15 titanium alloy powder must meet certain specifications for chemistry, particle size distribution, flow rate, apparent density, and impurity levels based on international standards:
Table: Specifications for TA15 Titanium Alloy Powder
Parameter | Specification | Standard |
---|---|---|
Aluminum content | 4.5 – 6 wt% | ASTM B348, Grade 15 |
Tin content | 2 – 3.5 wt% | ASTM B348, Grade 15 |
Zirconium content | 3.5 – 5.5 wt% | ASTM B348, Grade 15 |
Molybdenum content | 4 – 6 wt% | ASTM B348, Grade 15 |
Titanium | Balance | ASTM B348, Grade 15 |
Particle size | 10 – 45 μm, max 150 μm | ASTM B348 |
Apparent density | ≥ 2.7 g/cc | ASTM B212 |
Tap density | ≥ 4 g/cc | ASTM B527 |
Flow rate | ≥ 25 s/50 g | ASTM B213 |
Oxygen content | ≤ 0.25 wt% | ASTM B348 |
Nitrogen content | ≤ 0.03 wt% | ASTM B348 |
Carbon content | ≤ 0.08 wt% | ASTM B348 |
Iron content | ≤ 0.25 wt% | ASTM B348 |
Meeting the chemistry requirements ensures that the desired α+β microstructure is formed in TA15 upon solidification. Controlling the particle size distribution and powder shape ensures high density and good flowability. Minimizing impurity levels like O, N, C is critical for achieving the required mechanical performance. Compliance with these specifications is validated through testing and certification.
Design Considerations for TA15 Titanium Alloy Powder Parts
Several important design factors must be considered when working with TA15 titanium alloy powder:
Table: Design Considerations for TA15 Titanium Alloy Powder Parts
Consideration | Details |
---|---|
Wall thickness | Minimum wall thickness 0.3 – 0.5 mm for AM processes |
Surface finish | Post-processing may be needed to improve surface finish |
Residual stress | Support structures help relieve residual stresses in AM |
Dimensional accuracy | ~0.1-0.3% linear dimensional change during sintering |
Part geometry | Simple, clean geometries recommended for press & sinter process |
Density optimization | Parameter optimization is key for maximizing density in AM |
Heat treatment | Solution treatment, aging can enhance mechanical properties |
Machining allowance | Add 0.5 – 1 mm allowance for post-AM machining |
For AM processed parts, a minimum wall thickness of 0.3 – 0.5 mm is required to prevent collapse or distortion. Generating the required surface finish may also need additional post-processing like surface milling, grinding, or polishing.
In processes like pressing & sintering, relatively simple part geometries with clean edges and corners are recommended to fill the die cavity effectively during compaction and avoid trapped powders. An ~0.1-0.3% linear dimensional change is expected during sintering due to shrinkage.
Proper heat treatments like solution treatment and aging can significantly enhance the mechanical properties of finished TA15 parts, regardless of production process.
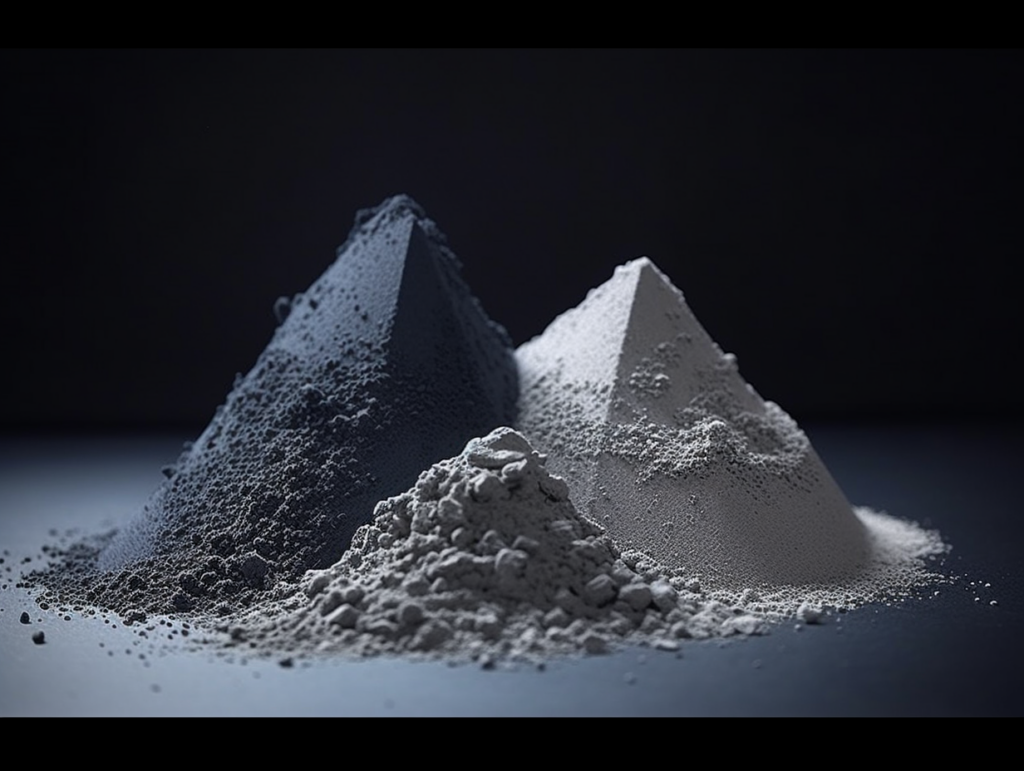
Effective Methods to Consolidate TA15 Titanium Alloy Powder
There are several effective methods used for consolidating TA15 titanium alloy powder into dense parts:
Table: Methods for Consolidating TA15 Titanium Alloy Powder
Method | Principle | Typical Density |
---|---|---|
Hot isostatic pressing (HIP) | High pressure inert gas | ≥ 99.5% theoretical |
Additive manufacturing | Laser/e-beam melting of layers | ≥ 99% theoretical |
Metal injection molding | Molding then sintering | ≥ 98% theoretical |
Press and sinter | Compaction followed by sintering | ~95% theoretical |
Powder forging | Pressing and forging at temperature | ≥ 98% theoretical |
Hot isostatic pressing (HIP) uses high pressures up to 200 MPa along with high temperatures around 1000°C in an inert atmosphere to consolidate TA15 powder into near theoretical density without melting. This achieves properties very close to wrought material.
Additive manufacturing (AM) utilizing selective laser melting, electron beam melting, or binder jetting melts or sinters TA15 powder layers sequentially to build near-full density parts with net shape geometry. Minimal machining is required after heat treatment.
Metal injection molding (MIM) is a powder metallurgy process combining molding of a TA15 powder-polymer feedstock, solvent debinding, and high temperature sintering to produce small, complex parts at high volumes. Final properties depend on sintering optimization.
Pressing & sintering uses uniaxial or cold isostatic pressing followed by vacuum sintering to produce simple TA15 parts like bushings or sprockets. While dimensional control and productivity are good, properties are slightly lower than wrought material.
Powder forging (PF) first presses TA15 powder preforms before densifying through forging and extrusion at high temperatures. This improves ductility and approaches mechanical properties closer to wrought alloys.
Suppliers of TA15 Titanium Alloy Powder
Some leading global suppliers of TA15 titanium alloy powder include:
Table: Suppliers of TA15 Titanium Alloy Powder
Supplier | Powder Types | Particle Size | Origin |
---|---|---|---|
AP&C | Plasma, HDH | 15-45 μm | Canada |
Tekna | Plasma | 15-45 μm | Canada |
Carpenter Technology | Gas atomized | 15-150 μm | USA |
Praxair | Gas atomized | 10-75 μm | USA |
ATI Powder Metals | Gas atomized | 10-63 μm | USA |
Sandvik | Gas atomized | 10-150 μm | Sweden |
LPW Technology | Plasma, HDH, blended | 15-45 μm | UK |
These companies offer TA15 titanium alloy powders made via different processes including gas atomization, plasma atomization, HDH, and blended elemental. Particle size ranges from 10 μm to 150 μm based on intended application – AM processes usually use finer 15-45 μm powder.
Both European and North American manufacturers are well represented. Working with an established industry name like AP&C, Carpenter, Sandvik or ATI ensures reliable quality and certification.
Cost Analysis of TA15 Titanium Alloy Powder
The typical price range for TA15 titanium alloy powder based on production method is:
Table: Price Range of TA15 Titanium Alloy Powder
Powder Type | Estimated Price Range |
---|---|
Gas atomized | $110 – $220 per kg |
Plasma atomized | $150 – $275 per kg |
HDH | $90 – $160 per kg |
Alloyed elemental | $80 – $140 per kg |
Gas and plasma atomized powders command the highest prices due to their high sphericity and low oxygen content. Irregular HDH and blended elemental powders are cheaper but have higher oxygen levels.
For small volumes, prices tend to be at the higher end of each range. Larger order quantities can access lower prices per kg. Significant cost reductions may be possible for very high volume orders above 5000 kg.
Besides composition and quality, pricing also depends on factors like order size, lead time, and supplier location. Getting quotes from multiple suppliers is advised.
Installing and Maintaining Equipment for TA15 Titanium Alloy Powder Processing
Key aspects for installation and maintenance of equipment used in TA15 titanium alloy powder processing:
Table: Installation and Maintenance of TA15 Titanium Powder Processing Equipment
Type | Installation | Maintenance |
---|---|---|
Laser melting machine | Stable foundation, leveling, utilities connections | Optics cleaning, beam calibration, inert gas purity checks |
Electron beam melting machine | Vacuum pumps, water cooling, controls wiring | Filament replacement, vacuum integrity checks |
Metal injection molding | Mold clamping, debinding furnaces | Mold cleaning, polymer drying and handling |
Powder presses | Tool mounting, hydraulics, controls | Punch & die lubrication, hydraulic checks |
Sintering furnaces | Insulation, atmosphere control | Atmosphere calibration, heaters condition |
Powder handling system | Ducting, cyclone, dust collection | Equipment sealing, spillage recovery, filters |
Proper installation of equipment like AM machines, powder presses, and sintering furnaces is critical for safety and performance. This includes ensuring stable, level foundations, securing inert gas supplies, wiring electrical connections, and integrating peripheral cooling or vacuum systems.
Periodic maintenance involves cleaning key components like AM optics, replacing consumables like electron beam filaments, checking hydraulic systems health, and recalibrating furnace atmospheres. Maintaining the inert integrity of powder handling ducts and cyclones is also essential.
Worker training for safe equipment operation, establishing preventative maintenance schedules, and proper lubrication and sealing against powder leakage/spills are key for maximizing uptime.
Powder Handling and Safety with TA15 Titanium Alloy
Effective powder handling and safety practices when working with TA15 titanium alloy powder:
Table: Powder Handling and Safety with TA15 Titanium Alloy
Issue | Mitigation Method |
---|---|
Powder exposure | Local exhaust ventilation, dust collection |
Skin contact | Personal protective equipment – gloves, clothing |
Fire hazards | Inert gas blanketing, spark detection and suppression |
Storage and transportation | Sealed containers, proper labeling |
Powder spills | Cleanup using vacuum, appropriate PPE |
Waste disposal | Follow local regulations, contract qualified disposal firms |
Worker training | Hazard communication, safe handling instruction |
As a fine reactive powder, TA15 titanium alloy poses several potential safety hazards if not properly managed. Robust engineering controls like exhaust ventilation and spark suppression along with administrative controls like worker training on safe handling procedures are essential.
Personal protective equipment including gloves, full-body clothing, goggles, and respirators minimize direct powder contact during handling. Careful inert storage/transport and proper labeling contain the risks.
Establishing emergency response protocols for spills and waste disposal procedures ensures minimal environmental impact. Ongoing emphasis on hazard communication keeps workers alert and vigilant when processing TA15 powder.
Selecting a Reliable TA15 Titanium Alloy Powder Supplier
Key factors in choosing a reliable TA15 titanium alloy powder supplier:
Table: Selecting a TA15 Titanium Powder Supplier
Consideration | Details |
---|---|
Experience | Years in business, number of customers served |
Production capacity | Ability to meet order quantities reliably |
Quality certifications | ISO 9001, AS9100, ISO 13485 |
Testing capabilities | In-house characterization facilities |
Inventory and lead times | On-hand stock for prompt delivery |
Technical expertise | Metallurgy and application knowledge support |
Sampling | Provision of test samples to customers |
References | Feedback from existing customers |
Pricing | Quoted price and payment terms |
TheCopy
go on
L
Here is the continuation of the article:
The supplier’s experience and production capacity ensure stable long-term availability of TA15 powder along with the flexibility to meet delivery timelines. Quality management system certification like ISO 9001 indicates standardized processes and quality control.
In-house powder testing capability allows reliable validation of powder characteristics like particle size, morphology, chemistry, density, and flowability per the application specification.
Reasonable inventory levels and lead times provide customers with responsive order fulfillment for production schedules. Knowledgable technical staff can recommend suitable TA15 powder types and sizes based on the manufacturing process needs.
Sampling allows customers to evaluate the powder properties firsthand through test builds. Getting customer references helps assess the supplier’s track record. Competitive fair pricing and payment terms are desired.
Overall, choosing a TA15 powder supplier with strong technical expertise, quality systems, product testing capability, inventory/delivery performance, and customer service ensures a consistent and positive experience.
Comparing TA15 Titanium Alloy Powder with Other Titanium Powders
Comparison between TA15 titanium alloy powder and other common titanium alloys:
Table: Comparison of TA15 Titanium Powder with Other Titanium Powders
Alloy | Strength | Ductility | Weldability | Corrosion Resistance | Cost |
---|---|---|---|---|---|
TA15 | High | Good | Good | Excellent | Moderate |
Ti6Al4V (Grade 5) | Very high | Low | Fair | Excellent | Low |
Ti6Al4V ELI (Grade 23) | High | Good | Very good | Excellent | Moderate |
Commercially Pure Titanium (Grade 2) | Medium | Excellent | Excellent | Good | High |
Ti13Nb13Zr (Grade 29) | Medium | Excellent | Good | Excellent | Very high |
TA15 offers a balanced combination of high strength, moderate ductility, good weldability, and excellent corrosion resistance at a moderate cost. It significantly outperforms workhorse titanium alloys like Ti6Al4V in weldability while also being stronger than commercially pure titanium.
Ti6Al4V is the strongest and least expensive titanium alloy but has poor welding characteristics. Ti6Al4V ELI gives up some strength for better ductility and weldability. Commercially pure titanium is easy to weld and shape but weaker. Exotic niobium-zirconium alloys like Ti13Nb13Zr are costlier despite modest strength.
For critical applications needing high performance at reasonable cost, TA15 titanium alloy powder provides an optimal set of mechanical properties, fabricability, and corrosion resistance.
Advantages and Limitations of TA15 Titanium Alloy Powder
Some key advantages and potential limitations of TA15 titanium alloy powder:
Table: Advantages and Limitations of TA15 Titanium Alloy Powder
Advantages | Limitations |
---|---|
High strength-to-weight ratio | Higher cost than steel or aluminum |
Excellent corrosion resistance | Lower strength than Ti6Al4V alloy |
Biocompatible for medical uses | Less readily available than standard alloys |
Good weldability and ductility | Limited high temperature capability |
Low modulus close to bone | High reactivity requires controlled processing |
TA15’s high strength despite low density makes it ideal for weight-critical applications in aerospace and medicine. It resists corrosion in harsh environments. The biocompatibility enables direct contact with human tissue for implants and prostheses.
The good weldability and ductility support manufacturability in the as-built condition. The elastic modulus close to human bone minimizes interfacial stresses.
However, TA15 alloy powder costs more than ferrous or aluminum alternatives. The strength is lower than Ti6Al4V, limiting high-stress uses. Availability is still catching up to widely used alloys like Ti6Al4V or commercially pure titanium. Use temperatures are constrained to under 350°C. The powder’s high reactivity necessitates careful handling to prevent contamination, fire, or explosions.
With thoughtful design and processing strategies, engineers can maximize the advantages of TA15 while accounting for its limitations.
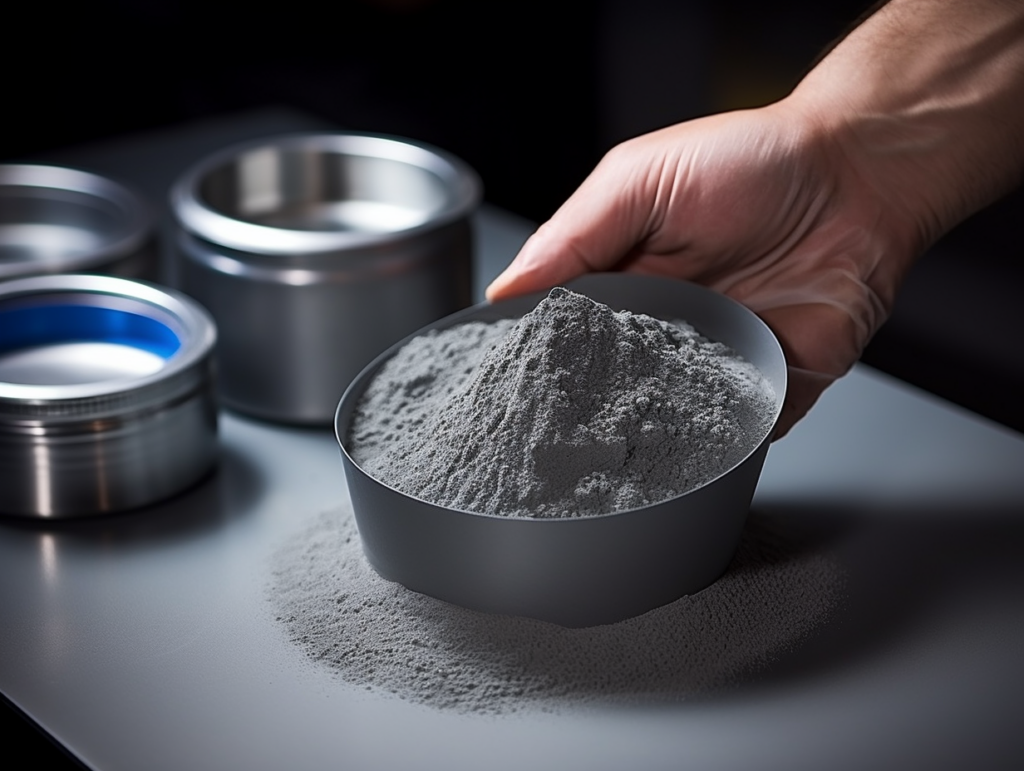
FAQ
Table: FAQs About TA15 Titanium Alloy Powder
Q: What are the main applications of TA15 titanium alloy powder?
A: TA15 is widely used in aerospace components like airframes and engines, oil & gas wellhead parts, chemical plant hardware, biomedical implants and prostheses, automotive parts, and marine propellers and shafts.
Q: What precautions are necessary when handling TA15 powder?
A: TA15 powder is flammable and reactive, requiring exhaust ventilation, inert gas blanketing, grounding/bonding, and spark detection & suppression along with protective equipment for workers. Proper storage and transportation in sealed containers is mandatory.
Q: What metal 3D printing process is used with TA15 alloy powder?
A: TA15 is most commonly processed via selective laser melting (SLM) and electron beam melting (EBM) additive manufacturing. Parameters must be optimized to achieve high density.
Q: What are the key benefits of TA15 versus traditional titanium alloys?
A: Compared to workhorse Ti6Al4V, TA15 offers much better weldability and ductility. It is stronger than commercially pure titanium. TA15 provides an optimized balance of properties.
Q: What kind of post-processing is required on TA15 titanium AM parts?
A: Heat treatment like hot isostatic pressing, solution treatment, and aging is usually required after AM to achieve optimum properties. Some machining, drilling, or surface finishing may also be needed.
Q: How should I select a reliable TA15 titanium powder supplier?
A: Look for years of experience, quality certifications like ISO 9001/13485, technical expertise in metallurgy, sampling, reasonable lead times & inventory, and strong customer references.
Conclusion
TA15 titanium alloy powder offers an exceptional combination of high strength, corrosion resistance, biocompatibility, weldability, and ductility for critical applications across aerospace, medical, chemical, and other demanding industries.
Careful characterization and selection of TA15 powder is crucial based on intended manufacturing process and part performance requirements. A variety of consolidation methods can be implemented to produce full-density components from TA15 powder.
By following good design practices and powder handling procedures, while leveraging capable suppliers, engineers can fully realize the benefits of this advanced titanium alloy in their projects and products.